Complex high-frequency signaling challenges, for both existing and new applications, can be solved using signal conditioners.
Frequency signal conditioners—designed to handle high-frequency pulse signals from sensors and convert them into other useful automation signals—are an important industrial automation design component for both new and retrofit applications. High-frequency pulses may be generated from a proximity sensor associated with a spinning sprocket, between digital motion control systems requiring synchronization, or from many other sources.
In a Process Instrumentation March 2025 article titled Frequency Signal Conditioner Applications by AutomationDirect’s Rick Canfield, the function of signal conditioners to interface high-speed sensing signals with supervisory automation systems is explained.
Frequency Signal Conditioning Basics
Most modern programmable logic controllers (PLCs) can handle high-frequency signals directly, but signal conditioners provide additional design options for flexibility and performance.
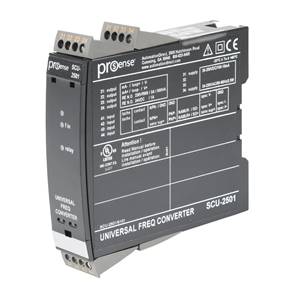
AutomationDirect provides a wide variety of signal conditioners. Within this offering, the AutomationDirect ProSense SCU Series (models SCU-2501, SCU-2502, and SCU-2503) is a versatile product family capable of converting, transmitting, scaling, and isolating frequency input signals from various sensors and controllers. These units are compatible with standard AC and DC voltages, are compact for easy installation, and can be mounted on DIN rails. They also feature a detachable LCD module for programming and display purposes.
The SCU Series signal conditioners support input frequencies up to 100 kHz from NPN, PNP, TTL, tachometers, and NAMUR sensors. Depending on the model, their output is a unipolar or bipolar current, voltage or frequency signal, or a contact from an internal programmable relay. They also provide three-way isolation between input, output, and power.
Typical Applications
Two real-world applications illustrate their utility:
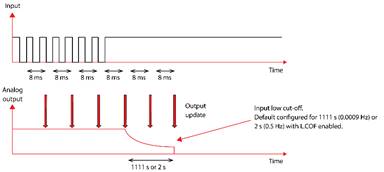
- Industrial Washing Machine Clutch Control: In a denim finishing factory, an industrial washing machine uses a pneumatic clutch to transition between low and high-speed operation. To prevent unsafe conditions if the clutch assembly fails to disengage, an SCU signal conditioner is used to monitor the clutch RPM using pulses from a proximity sensor detecting sheave spokes as they pass. The signal conditioner scales the data and triggers a relay to stop the machine if the RPM exceeds an acceptable threshold, providing an additional degree of safety.
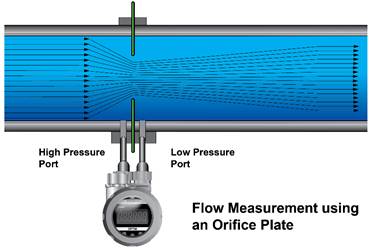
- Flow Meter Monitoring: Impeller-type flow meters spin a shaft as fluid flows through a pipe, and a sensor detects each revolution. The SCU-2503 conditioner converts these pulses into an analog output scaled by an appropriate K-factor to provide a flow measurement in engineering units, which can be used by a host monitoring and control or other system. The conditioner can also be configured to filter out any error due to low frequency signal pulses, making the resulting flow total more accurate.
Another common need—especially for differential flow meter applications—is conditioning input signals using a square root function and then transmitting the result as a linearized signal for use by the host system. Signal conditioners provide this capability, and can therefore simplify the configuration of a supervisory PLC.
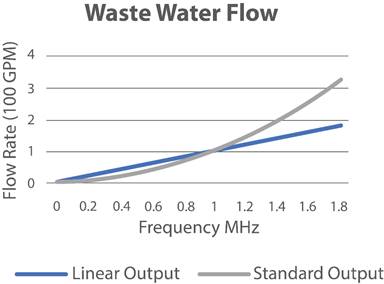
Universal Options
The AutomationDirect ProSense SCU Series provides capable solutions for enhancing the functionality and accuracy of sensors and systems.
These signal conditioners can solve complex problems presented by a variety of frequency signal applications, and the versatility of this family of signal conditioners is one of its main benefits for greatly enhancing existing sensors and applications.
Signal conditioners empower designers to create flexible solutions to complex signaling challenges for both existing and new industrial applications.
Check out the AutomationDirect signal conditioning web page to discover even more options for addressing your design requirements.