Specifying performance instead of parts when purchasing machines and process skids cuts costs, reduces lead time and guarantees reliable operation.
Bill Dehner, Automation Specialist at AutomationDirect, authored an article for the June 2019 issue of Applied Automation titled Specifying performance instead of parts. Here is a summary of the article, click on the link above for the full text.
Many plants and facilities rely on pre-packaged machines and process skids purchased from original equipment manufacturer (OEM) suppliers. They want the components installed in this equipment to match what they currently use to the greatest extent possible to minimize spare parts stocking and improve their familiarity with the equipment.
However, Bill cautions that putting too much effort into specifying skids to a very detailed level comes at a cost.
Specifying preferred parts and vendors can make it difficult to create a bid specification because excessive detail is required, very little of which directly influences the most important attribute: performance of the machine or process skid. It may stop OEMs in their tracks, resulting in fewer bidders, or sometimes only one. Boxing in the brands that can be used will often push an OEM out of its comfort zone. For example, if the OEM can’t use its preferred controller or human-machine interface (HMI), the design and schematics will need to be changed, which will cause higher costs and delays in other areas.
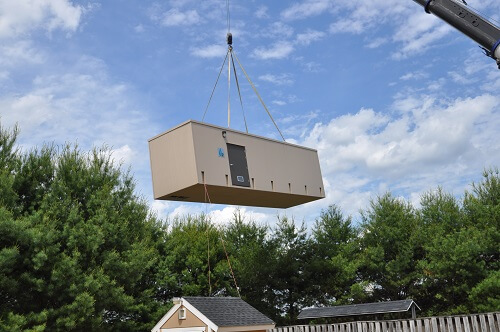
Innovative Treatment Products selected AutomationDirect products for the control system on this water treatment skid, allowing the company to provide performance guarantees to its customers.
A better approach in many instances is to specify the desired overall system performance, while giving the OEM as much leeway as possible in terms of parts and vendors. This keeps bid prices down by avoiding the cost of having OEM vendors reinvent the wheel.
Specifying Performance
It’s often much simpler and more effective to specify overall equipment performance as opposed to individual parts. For instance, a purchaser can call for a machine that produces a certain number of parts per hour with 98% uptime. If that same purchaser specified all of the subcomponents, the OEM might be reluctant to guarantee overall performance since they are not using their preferred and familiar products.
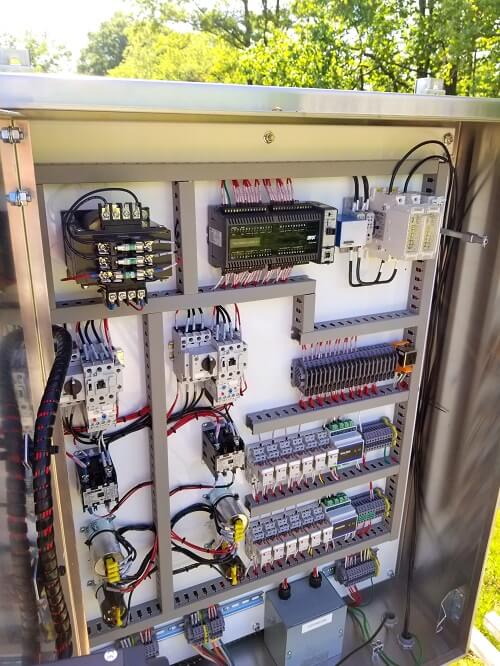
OEMs have invested time and effort to design, build and test their control system to meet the performance requirements of their machine or process.
Bill identifies some electrical and automation requirements that can be used to specify OEM equipment to support overall performance, while giving the OEM latitude. Consider specifying:
- Main power connection
- Control voltage at 24Vdc
- PLC I/O capabilities and types
- Sensors as PNP with M12 quick-disconnects
- NEMA 12 control enclosures
- HMI color touchscreens with minimum 6-inch diagonal displays
From an overall machine perspective, operational performance requirements may include things like:
- Cycle time
- Parts per hour
- Productivity availability
- Quality characteristics
An example could be requiring a machine to perform a press-to-depth crimp performance of 3-5 tons of force with +/-0.002-inch press stroke depth repeatability, with a production rate of 200 parts per hour and 98% uptime.
PLC and HMI programming specifications can be structured in a similar way, according to Bill:
HMI specifications also can be performance-based using operational parameters. For example, requiring an overview screen with mode, cycle, product and fault information. Product selection via recipes, teach robot points and help and fault message screens are other examples of operational performance requirements for an HMI. Basic requirements for data collection are another example of a performance-based specification. This might include storage of fault message data, display of the number of good and reject parts by part number, current cycle time, last 10 cycle times data, etc. These performance requirements lead the way to a quicker installation and startup. The end goal is a reliable and efficient machine or process skid that fits into ongoing operations.
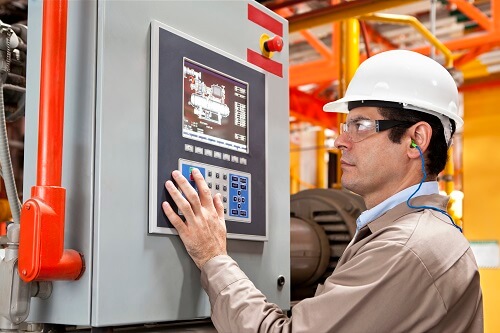
Specifying HMI operational parameters instead of a vendor and part number allows OEMs to select the components with the best price-performance ratio.
Supporting the System
OEMs are also far more willing to offer maintenance and after-warranty support at a reasonable cost if they can use their preferred vendors. This is an important point because many end users are lightly staffed and rely on outside support. Many purchasers include support in their requirements, and all should also require built-in provisions for remote access so OEMs can quickly troubleshoot problems.
Some new equipment contracts are actually leases, or are structured based on actual machine production. Bill points out that these arrangements strongly favor specifying performance instead of parts. Future procurement trends are likely to continue in this direction and may lead to more favorable outcomes for all parties.
Click to learn more about PLCs and HMIs.
Originally Published: June 2019