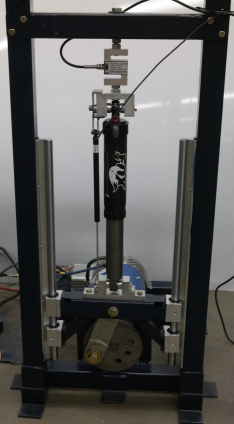
Eagle Motorsports and Georgia Southern University have been using AutomationDirect for two years to collect valuable data in order to improve our engineering decisions regarding suspension. It is important to know how fast the suspension on a vehicle moves in order to properly adjust the stiffness of the shocks and springs. These velocities can be categorized into various actions the car completes. For example, most low-velocity events involve things like braking and accelerating, while navigating ground obstacles involve higher velocities. A shock dynamometer is traditionally used to actuate the shock absorber at fixed velocities like those seen on track and to adjust valving either by means of an internal or external adjustment. Shock dynamometers typically carry a hefty price tag and, during the months of COVID, were impossible to get. For these reasons, Eagle Motorsports took on the challenge of building one.
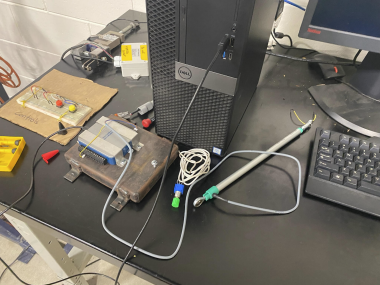
Shock dynamometers use a load cell to record force and a linear potentiometer in combination with time to record velocity. Shocks use a Force vs. Velocity graph to characterize the damping. A DC motor was previously used by the 2019 team on the dyno to cycle the shock absorber at a set speed. Later, when the team decided to upgrade the dyno to allow for a range of speeds, the team reached out to AutomationDirect for a Variable Frequency Drive (VFD). This used in combination with an AC motor allows a user to adjust the frequency of the motor and change its speed, which further allowed the team to gain insight into how their shocks performed at a range of compression and rebound speeds.
The 2019 team also used an old linear potentiometer which no longer reliably communicated data so, during development the team also leveraged their relationship with AutomationDirect for a new one. Linear potentiometers act as variable resistors. Applying a voltage to the potentiometer enables a varying voltage to be read from the middle pin based on the displacement of the shock as it oscillates up and down. This was then used in conjunction with a load cell, amplifier, National Instruments USB DAQ device, and a custom MATLAB script to record and plot the shock’s Force vs. Velocity curve to tune the Baja car. With these two items checked the team was able to run dyno tests on multiple shocks and adjust tuning to better compensate for the velocities and obstacles seen in Baja SAE competition.
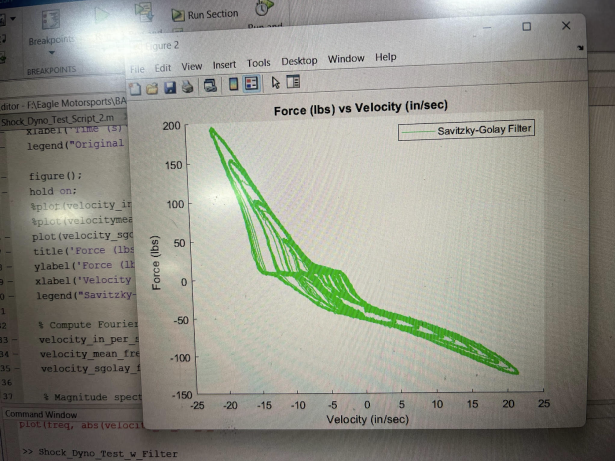
“AutomationDirect made getting this shock dyno ready possible, the whole team offered a wealth of knowledge and experience on recording and processing data that did not exist on the team. Having someone with resources in the industry willing to help gives everyone on the team a great feeling, it adds an extra layer of meaning to the work.” – Joshua Moore
Here is a video of the Eagles Motorports dynamometer in action