VFDs, RS485, PLCs — these terms may seem like names of droids or faraway galaxies and planets in a “Star Wars” movie. However, they really refer to earthly based components that Vermont Technical College engineering student Dan Rapoza learned about when he set out to help a dairy farmer save time and money by automating a routine process critical to milking cows.
The Challenge
Rapoza’s main project challenge was to figure out how to automate the opening and closing of four heavy vinyl curtains. These curtains serve as a barrier to keep heat in a farm’s milking parlor during the winter and also to keep bacteria out, therefore ensuring compliance with the milk inspector. Before automation, the curtains were being operated manually 30 – 40 times a day, 365 days of the year, to let 80 cows enter and exit a milking parlor six at a time. In addition, Rapoza wanted to address how the curtains were suspended to reduce maintenance needs and increase energy efficiency.
“I am passionate about improving agriculture as well as the control systems,” said Rapoza. “I believe that all agricultural facilities can benefit from implementing automated systems in one form or another.”
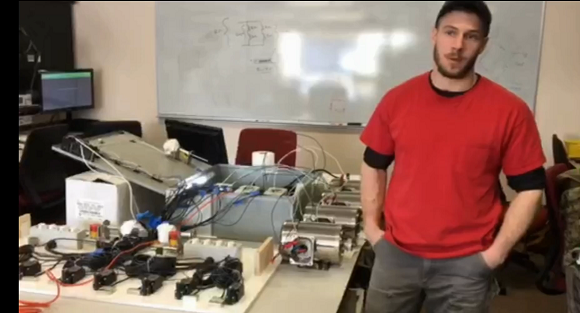
Dan Rapoza and the AutomationDirect parts used in his project!
For his project, Rapoza considered several different methods of building a system to move the curtains back and forth, but discarded them due to high costs or ongoing maintenance needs. He designed, fabricated, and tested a PVC pneumatic cylinder which tested well and seemed to be cost-efficient to create and maintain. He then turned to the AutomationDirect website to look for the components he needed to turn his project into reality. “The website provided me with more options to consider,” said Rapoza. “I now had options to achieve the linear motion needed to push and pull the curtains, a way for them to slide, and the system needed to control their movement.”
“At the beginning of the project, I knew next to nothing about Variable Frequency Drives (VFDs) and AC motors working together or how they would communicate with the programmable logic controller (PLC), but I was excited to learn,” explained Rapoza. “I learned about control systems and instruments, including three-phase motors, VFDs, communication protocols such as RS485 and how to program PLCs.”
From his research, Rapoza opted to use an AC motor and VFD to push and pull a timing belt for the linear motion needed to open and close the curtains. To create the curtain sliding system, he built a new header to move the curtain suspension cable away from the wall, installed a new cable to suspend the curtains, and designed custom pulleys to minimize friction. For the control system, he used a CLICK PLC equipped with Ethernet, RS-485, and RS-232 communication ports. The RS-485 was used to communicate to the VFDs and SOLO temperature controllers. Finally, he used diffuse photoelectric sensors with limit switches to sense the position of the curtains, polarized photoelectric sensors to detect the location of the cows, and inductive proximity gate sensors which ultimately determine when the curtains should open or close.
The Solution
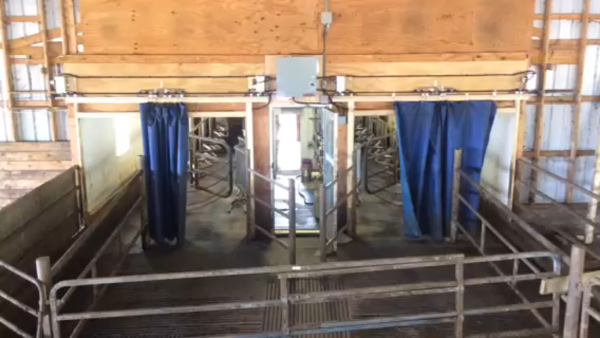
See above for Dan’s finished project.
Rapoza’s planning, research, and hard work proved to be successful. After the project was installed, the temperature in the milking parlor increased 12.4 degrees, and the curtains open and close automatically. Ultimately, the project achieved its goals of improving energy retention, boosting operational efficiency, and reducing maintenance costs. He recently reflected on his project “I learned that even the smallest projects require extensive and careful planning from coming up with a functional design to fabricating and implementing the final product,” he shared. “I also learned how to manage projects and deliver my product on time.”
Rapoza’s education about strange-sounding components and how they can work together, paid off. He recently graduated from college and now works for Freeport McMoRan Copper and Gold in the Process Control and Automation group. In the future, he looks forward to continuing to automate processes in the field of agriculture.
*Originally published: April 17, 2018