What makes the ‘swoosh’ noise happen when a soda can opens? What powers the gates, brakes, and passenger restraint systems on a roller coaster? What makes animatronics work at an amusement park? Compressed air is the magic that makes all these things happen – and much more.
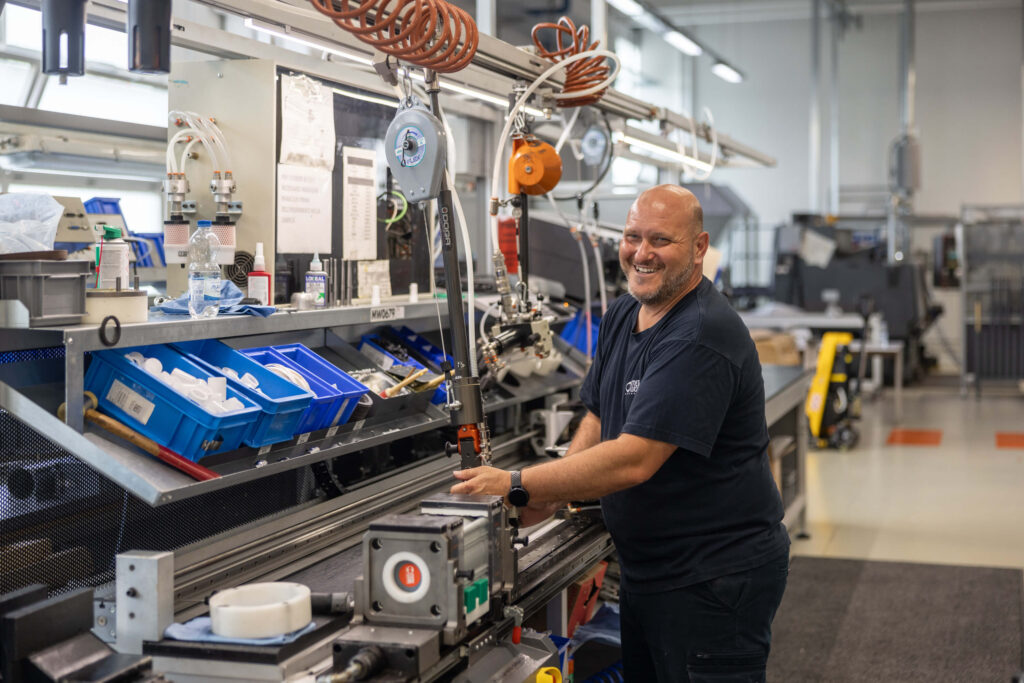
Compressed air consists of the same mix of gases as the air we breathe, but it has been forced into a smaller space and kept under pressure, bringing its molecules closer together. When the pressure is released, the result is an energy source that is safer and easier to use than other power sources such as steam or batteries.
Manufacturing facilities around the world use compressed air to power their industrial and commercial applications, including pneumatic systems. These systems use manual, air-pilot, or solenoid valve actuators for control, and offer a lower cost, more flexible, or safer alternative to electric actuators for industrial and commercial applications.
Basic pneumatic components such as valves, cylinders, hoses, and fittings can be combined in many ways to provide simple and reliable machine control. Pneumatic power transmission is often the best way to grip, lift, press, shift, or stack products.
Many companies use pneumatic components and systems made by Metal Work, headquartered in Concesio, Italy. The company offers a product range across five lines: actuators, valves, air treatment units, fittings, and handling components, which are ISO 9001, ISO 1401, and OHSAS 18001 certified.
“We strive to provide innovative, reliable, and efficient solutions that improve our customers’ productivity and profitability,” said Paul Saunders, President of Metal Work Pneumatic USA, Inc. “We constantly seek solutions and products to meet their needs as well as new market demands.”
Automation Direct sells Metal Work air prep assemblies, pushbuttons, switches, indicators, and pneumatic components. Its newest Metal Work offering is the Syntesi combination air prep assemblies. They are pre-assembled with the most popular component configurations. Available models include
manual shut-off with filter/regulator and lubricator, filter/regulator with lubricator, filter with lubricator, and filter with coalescing filter assemblies.
Fifty-Six Years of Growth and Innovation
Metal Work began in 1967 as a small workshop manufacturing push-in fittings for compressed air systems. Today, the company has grown to 59 subsidiaries in Asia, the Americas, Africa, and Europe and employs 1,350 people. In recent years, it has expanded its offerings to include the production of electrical components and vacuum technology.
Metal Work Pneumatic USA, Inc. is the company’s U.S. subsidiary and is headquartered in Arlington, Texas. It is a leading manufacturer and supplier of high-quality pneumatic components, systems, and solutions for the automation, food processing, packaging, medical, and automotive industries.
One of the company’s core product lines is solenoid valves, which are essential components in pneumatic systems, controlling the flow of air, gas, or liquid in various applications. Metal Work Pneumatic USA offers a wide range of solenoid valves to suit the needs of their diverse customer base. The valves are known for their high quality, durability, and reliability. They are engineered to withstand demanding operating conditions and are rigorously tested to ensure their performance meets or exceeds industry standards.
The company is also known for exceptional customer service. The company’s team of expert technicians and engineers provide comprehensive support to customers from design and installation to maintenance and repair. Metal Work Pneumatic USA also offers training programs and technical support to ensure that their customers can get the most out of their products.
Focus on Quality and Sustainability
From its start, Metal Work has focused on producing quality products as well as doing so through sustainable economic, social, and environmental practices. Metal Work has been ISO 9001 certified since 1992, gained ISO 14001 certification in 2000, OHSAS 1800 certification in 2007, then moved to ISO 45001 in 2019.
“These awards confirm a total quality philosophy for our entire company,” said Daniele Marconi, Managing Director. “We pay attention to how to save energy from the initial design phase of a product and application. As a result, the electric power needed to operate Metal Work valves has decreased in recent years by 75 percent.”
In addition, the company is proud to present the first edition of its Sustainability Report related to 2022. This document testifies to the company’s current and future commitments in relation to social and environmental issues, in order to promote and divulge the organization’s idea of a sustainable future.
Looking Forward to Geographic and Product Growth
Metal Work is continuing to grow its footprint around the world as well as its product offerings. It recently opened a new headquarters in Malaysia and looks forward to expanding further throughout the world to serve customers.
The company is also focused on helping customers manage operational data, lifetime, and diagnostics for processing machinery through pneumatic automation for Industry 4.0, the shift to intelligent manufacturing systems.
“Every processing machine has hundreds of components to be managed – actuators, pneumatic cylinders, electric motors, limit switches, pressure regulators, or temperature gauges,” said Saunders. “The most common, but least efficient, approach to managing this data is to entrust it to the machine PLC. However, the PLC, and the person programming it, already has numerous things to consider, without having to focus on the intelligent management of statistical, diagnostic, and preventative maintenance data for individual actuators or sensors. As a result, this information which is essential for the satisfactory operation of the entire system is ignored and not managed.”
To address this issue and help manufacturing facilities operate efficiently, Metal Work created the EB80 Electro-Pneumatic System. It lets the PLC handle work cycles, sequencing, and machine checks, while it transmits its decisions to the actuators/sensors, checks everything is operating satisfactorily, and flags a warning when a component malfunctions or has reached its expected lifetime. Ultimately, the system can help manufacturers’ systems become increasingly reliable, high-performing, efficient, and sustainable.
“It’s invigorating to be part of this Industry 4.0 transformation and help our customers around the world with these changes,” said Saunders. “It is also exciting to look at how our company has grown from producing fittings for compressed air systems to adding electrical components, vacuum technology, and more to serve customers’ evolving needs. We look forward to more growth and innovation as we do that.”