Human beings are visual creatures. It’s believed that our brains can process visual information 60,000 times faster than text, with 90 percent of information transmitted to the brain being visual and over half of the brain being devoted directly or indirectly to vision. Knowing that, it’s easy to see how a visual
representation of an automated system would allow for faster recognition of system variables. Which is exactly where the HMI comes into play.
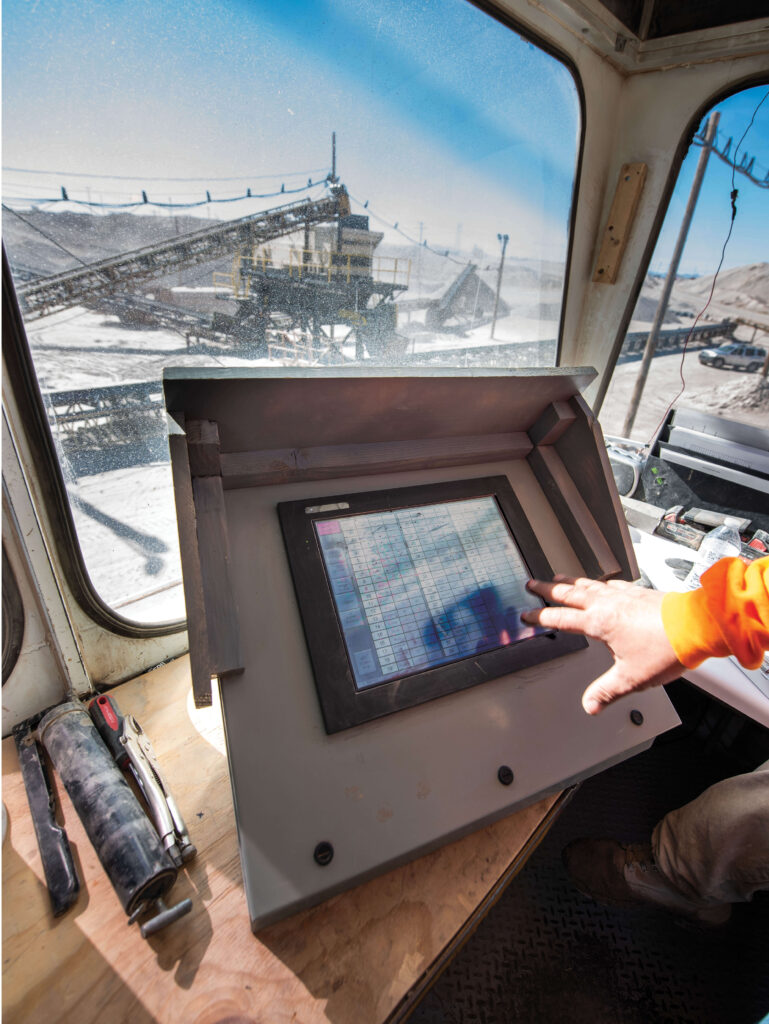
What is an HMI?
The HMI or Human Machine Interface allows operators to “interface” with the system(s) they oversee. It provides a visual overview of the automated system’s status and direct control of its operation. An HMI’s graphical screens can be programmed to display important performance and control information to the
operator. Pictures, icons, sounds, and colors can all be used by HMIs to visually represent different operating conditions, and many HMIs deploy touch screen technology for user interaction with elements displayed on the screen.
What Can an HMI Do For You?
Let’s say you need to decrease the temperature of a PLC-controlled industrial oven in your plant. You could connect to the PLC with the programming software and make the program changes online, you could install a potentiometer to adjust the temperature setpoint blindly, or you could enter the new value directly on an HMI screen. The HMI can also display the current temperature of the oven, a historical plot of temperature fluctuations over time, and will warn you if you set the temperature too low. In this case, the HMI’s convenience and functionality win hands down, and that’s just one scenario. Think about what it would take to install three new pushbuttons on a control panel. With an HMI, it’s all in the program. Adding or removing objects, like buttons, on the screen takes no time at all and doesn’t cost anything extra. In fact, most HMIs have object libraries that include numerous buttons, switches, dials, etc. that can be easily inserted into position on the HMI screen – usually with a simple drag and drop. With the many graphical objects in one small HMI, you could replace hundreds of mechanical control devices around your plant.
HMI Hardware Choices
Many types of HMIs are available in today’s market from simple operator interface terminals (OITs) with two-line displays, to more capable embedded HMI graphics terminals (an embedded HMI is one where control and monitoring software are running on an embedded operating system (OS)), to powerful PC-based HMIs.
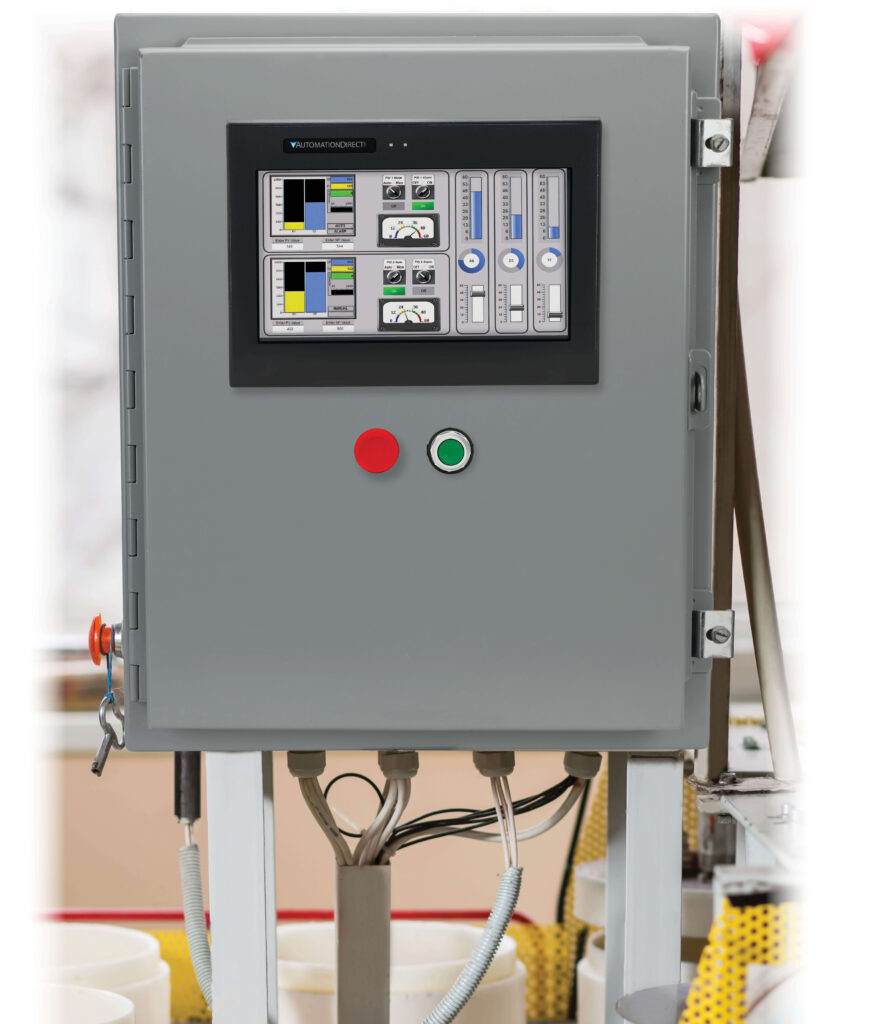
When selecting an HMI for a small machine, an OIT is typically acceptable—and certainly simple to configure, easy to use, and low in cost. An OIT will connect directly to the machine controller and provide suitable local operator interface functionality. It is also a good choice when adding operator displays to large assembly lines to give operators a better view of equipment status and line operation.
With larger machines or complex manufacturing lines, more extensive capabilities may be required, and this is where PC-based HMIs can be the best choice. With these types of HMIs, the PC can be industrially hardened for environmental reasons or be office-grade. PCs today are available with multiple processors, large hard drives, lots of memory, and include a wide range of built-in connectivity options. High-end functions such as a historian and the ability to simultaneously supervise multiple production processes can quickly justify the extra cost of this option.
The obvious choice for mid-size equipment and processes is an embedded HMI. However, in many cases, this HMI’s capabilities can also fit the bill for applications small to large. Embedded HMIs work well in a variety of configurations whether standalone or networked and even smaller machines can benefit from the remote access capabilities provided by these HMIs.
Embedded HMIs can go it alone, but they also play well with others. In a dedicated, standalone setup, an embedded HMI connected to small or mid-sized automated equipment is a cost effective and simple solution. Simply ensure the correct protocol is available to talk to the machine controller, hardwire it to the controller with its included cables, and you’re ready to configure the software. Unlike OITs, these embedded HMIs have many features including the capability to interface with mobile devices such as smartphones and tablets.
Networking Options
If you’re working in a networked setup, there are two main network architecture options: one with multiple HMIs connected to one controller and the other with one HMI connected to multiple controllers. Some applications work best with both options employed simultaneously so multiple HMIs are connected to multiple controllers.
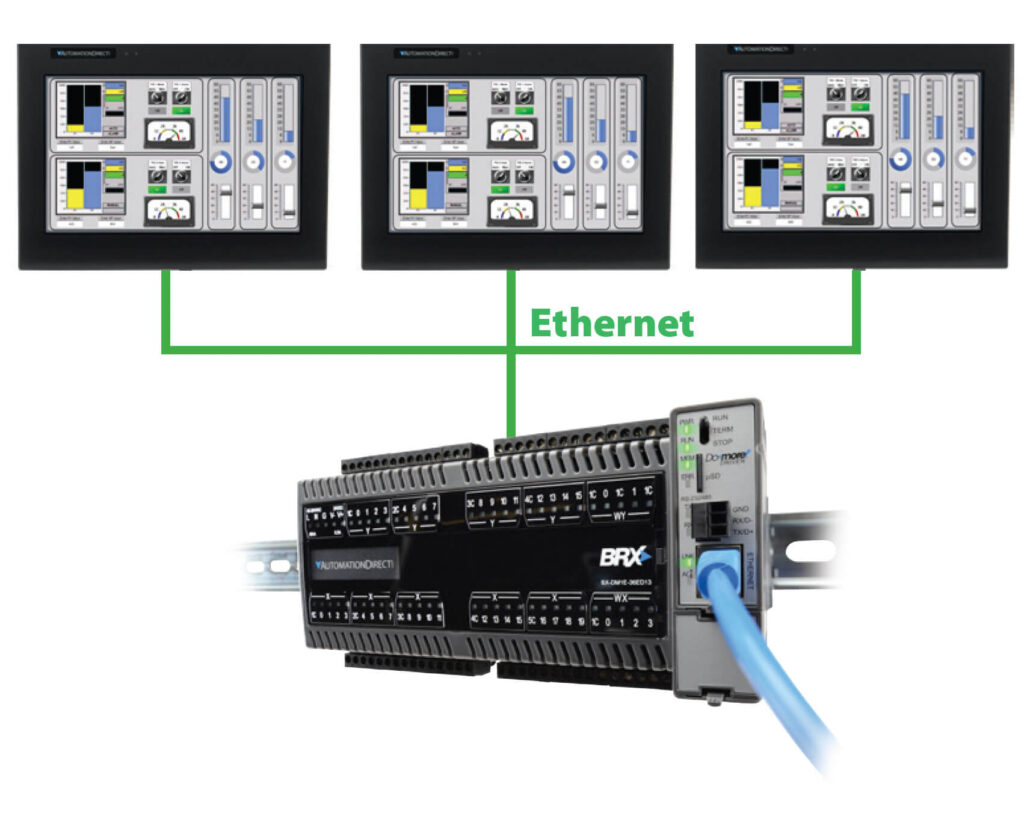
OITs and embedded HMIs fit well into the first scenario, where multiple HMIs are connected to one controller on a single large piece of equipment like a printing press, or an assembly line with multiple manual and automated work cells. In either configuration, this networked solution will support many HMIs. If one HMI fails, other HMIs can provide redundant operator interface to minimize downtime. The fallback HMI may be in a less than optimal location, but it can provide needed functionality until repairs are made.
In the second scenario, where one HMI is connected to multiple controllers, a PC-based HMI is typically the focal point as it can connect to many controllers simultaneously, even using different protocols if necessary. A PC-based HMI can contain many screens, limited only by the designer’s imagination and available memory, so each controller can have its own set of displays. With this option, OITs and/or embedded HMIs are often used to provide local operator interface, with the PC providing an overall view of operation.
HMI Location
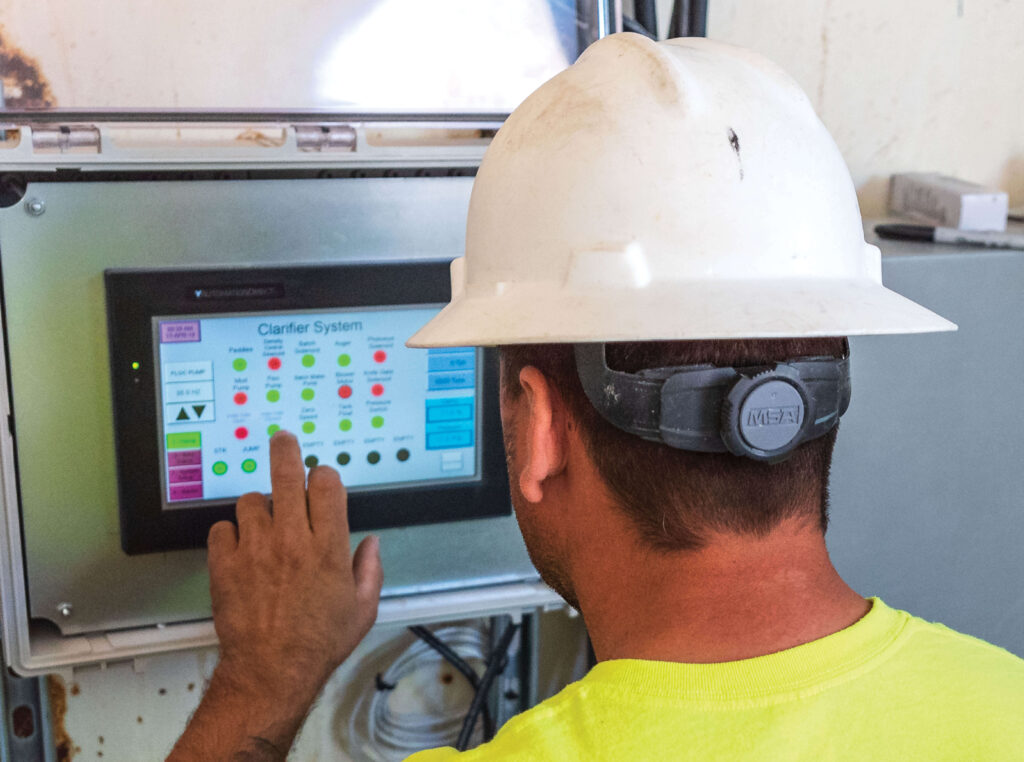
A big consideration is where and how to position the HMIs. It’s very important to consider ergonomic and normal operator position. If the operator has a kink in his neck from looking at an awkwardly positioned HMI screen, he or she may start to ignore the screens and follow gut instinct. In general, each HMI should be positioned so the operator doesn’t need to look up much, and down just a little.
It’s also important to consider where the operator is going to spend most of his or her time. How far will the operator have to walk to view the HMI? HMIs are often mounted in the main control enclosure, many times located at the front end of the production line. But if there are locations where there tend to be line disruptions or stoppages, how much time would be saved if the HMI were mounted close to where these problems typically occur? To maximize efficiency, it’s good practice to mount the main HMI in a centralized and easily accessible location to keep the operator’s steps to a minimum. Fewer steps combined with additional OITs and/or embedded HMIs at strategic problem points can quickly pay for themselves in terms of improved operations and safety.
Another location consideration is how far the HMI will be from the actual equipment area of interest. Being 20 feet away from the tooling station you are trying to operate manually from the HMI is never an
enjoyable experience. Also, consider mounting the HMI on a swing arm if the machine footprint allows, as this will make the viewing experience up close and personal.
There are many considerations when designing and integrating a control system’s OITs and HMIs. Once the type of HMI is selected and communication features and functionality are confirmed, consider how the operator and manufacturing engineer will use the OITs and HMIs. Make sure they are readily accessible, and remember that with OITs and HMIs, more is often better especially if it leads to improved efficiency.
HMI Software Considerations
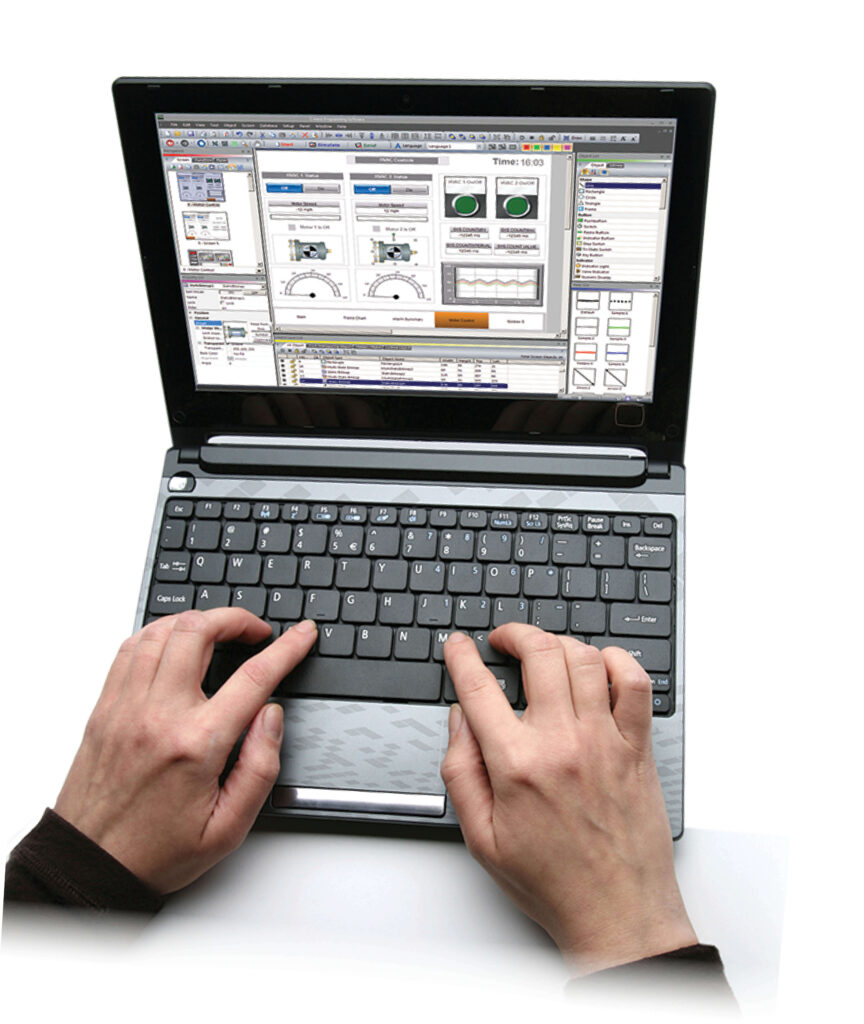
When searching for an embedded HMI, there is a wide variety of options. Hardware capabilities are important but so are the capabilities of the HMI software. Choosing an HMI that offers powerful easy-to-use programming software, can make a huge difference for your project and your development timeline. The following is a list of features any good HMI software package should have.
- Built-in Simulator – an easy-to-use simulator will result in a better-looking, more effective project AND reduce your development time. You should be able to fully simulate your entire project on your PC (every object, every screen) while it is being developed, without being connected to a touch panel or PLC.
- Recipe Functions – recipes should make it easy to make large numbers of tag (data value) changes with the push of a single button. Recipes are incredibly useful, not just for the traditional process industries (i.e. mixing of ingredients), but also for machine setup values and other data groups. For example, a recipe can enable a packaging machine to “change over” from jumbo size candy bars to “fun” size in just a few seconds.
- Helpful Event Manager – an Event Manager should provide much more than simple alarm and message functions and should enable an HMI to act based on random events like changing tag values, or periodic events like day-of-week, time-of-day, or even based on a particular screen change. A good Event Manager can simplify your PLC code because of all the functionality that the HMI can provide.
- User Libraries – once you’ve created an object, a group of objects, or a screen, you should be able to give it a name and save it within the HMI software for fast and easy reuse later. You should be able to store objects, graphics, sounds, and even entire screens in this manner. You should have the option to save objects/screens with or without the PLC tag info, and to easily share objects/screens from your library with other developers that you may work with. Reusing common objects and screens not only saves time but also creates a common look or theme that your operators will benefit from.
- Object Layer List – an Object Layer List should be incorporated. This list provides a rundown of all the objects on the active screen and allows you to quickly select an object from the list to edit. With this list you can expand or collapse grouped objects and access individual objects in a group without having to separate the group or move objects on the screen.
- Convenient Project Transfers – good HMI software should allow you to transfer a project to an HMI using a flash media card or a USB memory stick. This is ultra-convenient, whether the panel is installed in your local factory, across town, or on the other side of the planet. Project transfer using Ethernet or USB communications should also be supported.
- Database Tools – database tools such as search (with filtering) should be offered as well as the ability to import and export all the various databases for large projects. HMI databases can include tag-names, messages, recipe values, address book, Event Manager, object and screen libraries, and even screen images. These tools alone can save countless hours of development time.
- Versatile Text – good HMI software should allow wide ‑flexibility in the use of typefaces, fonts, and text size and should allow all text to be displayed in multiple languages. Language selection should also be selectable with the touch of a button.
- Ease of Use – the programming environment should offer a flexible, dock-able window layout and offer drag and drop functionality for all screen objects. It should allow easy access to all components on the development screen for quick and easy modifications.
- Data Logging – you should be able to preserve both tag data, with easy-to-use data logging capabilities, and project data, with auto save and backup functionality.
- Remote Access – remote access is becoming a must-have for HMIs and with it you can access and control your HMI from anywhere, just like you are standing in front of it.
NEW! CM5 Series High-performance HMIs
Starting at only $340.00
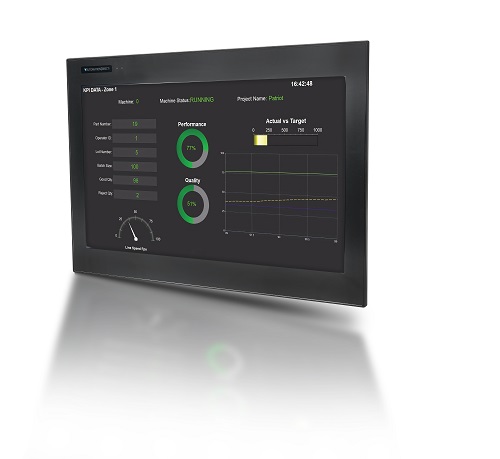
The next generation of AutomationDirect’s popular C-more HMI product line has been released. The CM5 HMI series offers lower cost, high-performance HMIs in sizes from 4 inches to an impressive 22 inches. With an amazing 1.6 GHz processor in the larger units (10” and above) and 43 Mbytes of memory, these HMIs provide much better trending, extra data storage, faster communication, and improved file types.
With each panel comes a host of communication ports for plug-and-play connections with industrial networks. All CM5 panels have serial and Ethernet ports that support many of the most popular industry protocols, including EtherNet/IP, MQTT, and Modbus. The included USB ports provide in-an-instant connections for programming and peripherals like keyboards, USB-to-audio converters, barcode scanners, memory storage, etc. And the embedded SD card slot provides easy project transfers or up to an additional 2TB of data storage (depending on model) for important log files.
With the CM5 series HMIs, you also get:
- 16.7M colors and LED backlights
- 800MHz or 1.6GHz CPU
- Built in real-time clock with 30-day backup (no battery required)
- NEMA 4/4X (indoor use only), IP65 ratings
- Dual Ethernet ports on 10” or larger models
- State-of-the-art communication protocols
- A host of supported drivers for numerous brands of PLCs
- FREE programming software
- FREE remote HMI mobile app
- FREE technical support
The FREE C-more HMI programming software has many tools built in to help make screen development quick and easy. Continuous refinements and improvements, using customer insight, have made this HMI software a favorite for many automation professionals.
- Fill-in-the-blank Event Manager makes programming a cinch
- Built-in project simulator pays for the HMI in time savings
- User libraries allow you to re-use your work again and again
- Convenient recipe and alarm functions
- Helpful database tools
- Huge array of objects and customized parts
- Trend graphs, PID faceplates, true historical data logging
- Wide assortment of fonts
- Numerous software security features to keep your system safe
- Remote access and control
- Plus, so much more