Modern PLCs and HMIs make it easy to implement extensive data connectivity and analytics.
By: Damon Purvis, AutomationDirect
Modern consumers are increasingly familiar with tailored experiences, abundant information, and generally getting things “their way.” Those working in the industrial manufacturing and automation sectors, on the other hand, have not always enjoyed such flexibility. Fortunately, hardware and software advancements mean that access to valuable industrial sourced data is easier, more secure, and available in many more ways than ever before.
The Explosion of Industrial Data
Manufacturing systems today generate vast amounts of data, a trend that shows no sign of slowing. According to estimates, global data creation was projected to reach 97 zettabytes in 2022, with manufacturing leading all sectors in data storage. Manufacturing data is digital gold, but only if it can be accessed, contextualized, and transported securely. The challenge lies in connecting distributed data sources, often located at the edge of production systems, to centralized computing resources or cloud platforms where the data can be processed and analyzed in support of efficient mass production (Figure 1).
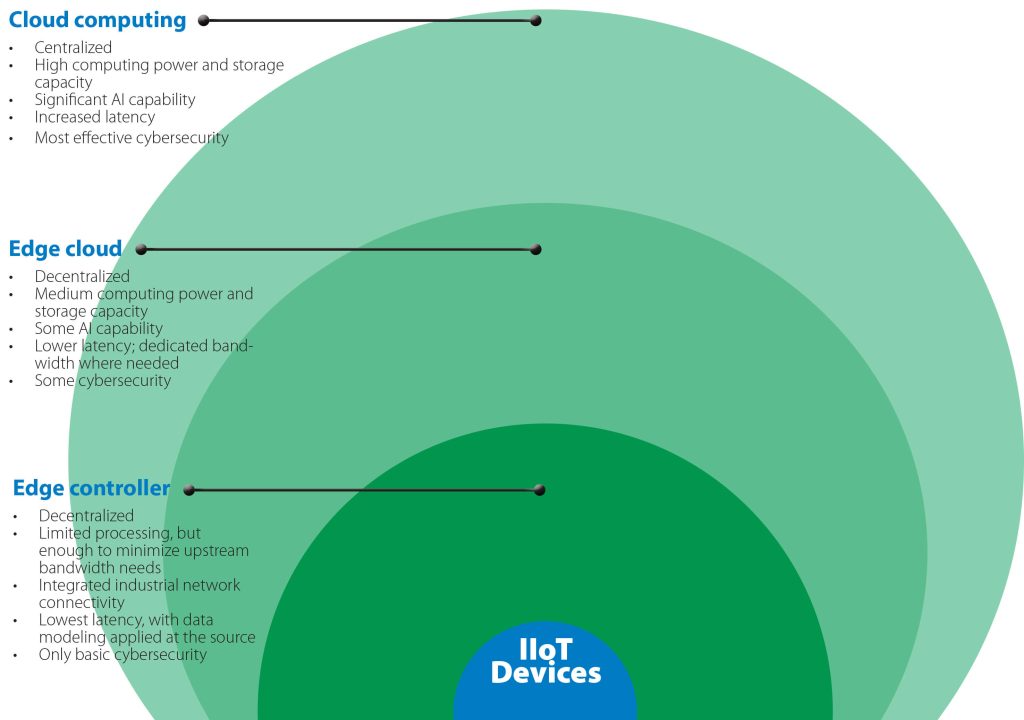
In today’s competitive market, manufacturers are adopting data-driven solutions to enhance equipment uptime, product quality, and operational responsiveness. This shift has led to greater integration of operational technology (OT) and information technology (IT) systems. Such integration allows manufacturers to leverage data for continuous improvement, quality control, predictive analytics, and more.
The increasing reliance on data has driven the adoption of new technologies, including the industrial internet of things (IIoT) and edge computing. Programmable logic controllers (PLCs) and human-machine interfaces (HMIs) used in the OT realm have long been staples in industrial automation, providing fundamental real-time control and monitoring functions. Industrial systems were commonly architected in accordance with the Purdue Model, a hierarchy with independent—but connectable—zones, including the manufacturing physical process, control center, enterprise, and others.
However, the evolving landscape of manufacturing now requires more than just basic control and rigidly segmented zones. As industries move toward more data-driven operations, the role of modern PLCs and HMIs is becoming integral not only for automation, but also for facilitating the collection, processing, and sharing of valuable operational data with IT-based enterprise resources. Combined, these technologies enable data collection and analysis, which are critical for optimizing operations, reducing energy consumption, and enhancing overall production agility.
Advanced Data Access
Although data collected from PLCs, HMIs, and other OT systems was historically isolated from enterprise IT networks to a great degree, over time the convergence of OT and IT has made it easier to collect and securely share data, enabling real-time visibility and decision-making. A critical development in this convergence is the introduction of controllers with enhanced connectivity and computing resources to process and communicate data directly at the edge.
For many small to mid-sized operations, the advanced capabilities of modern PLCs and HMIs are ideal for accessing, processing, and transmitting data (Figure 2).
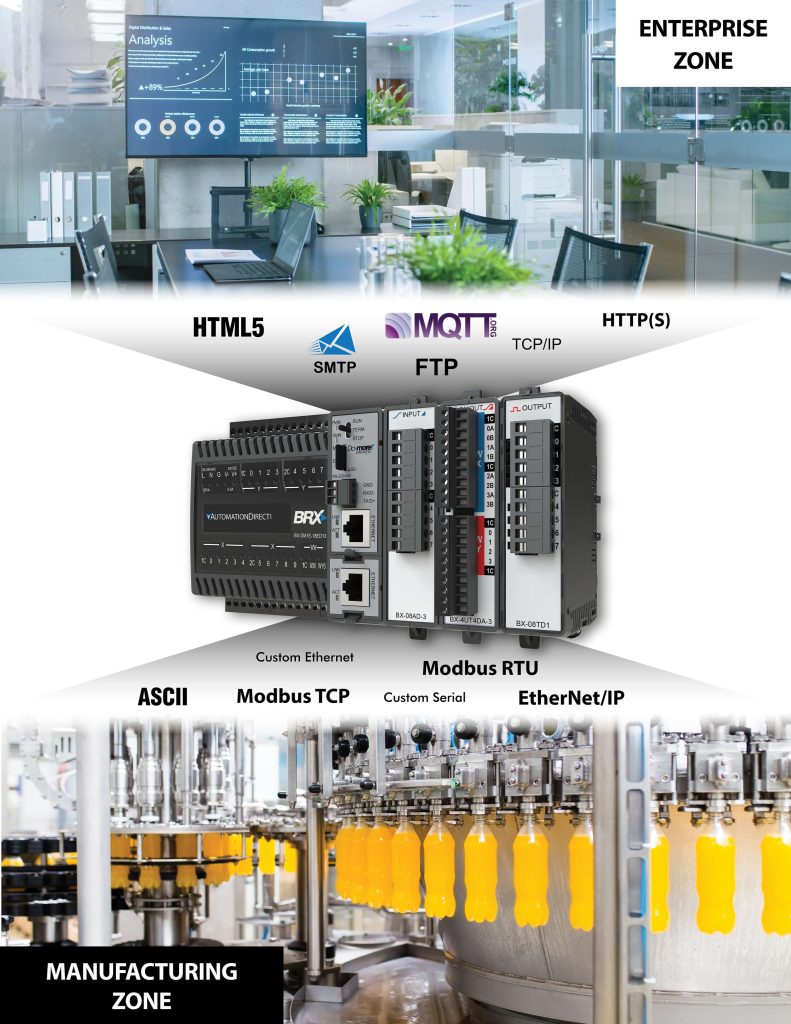
Today’s PLCs are far more advanced than their predecessors. They come equipped with enhanced networking, data handling, and processing capabilities, making them well-suited for tasks beyond basic control. These devices now support secure remote connectivity and integration with higher-level IT systems, facilitating seamless data exchange and enabling advanced analytics.
Modern PLCs offer several key capabilities that enhance their utility in data-driven environments:
- Advanced Networking and Communication: PLCs today support traditional OT protocols—such as Modbus, EtherNet/IP, and PROFINET—for communication with field devices. They also incorporate a broad array of communication protocols and methods—including OPC UA, secure REST APIs, MQTT, and Microsoft Azure integration—which allow them to integrate directly with enterprise IT systems. These capabilities provide an efficient means of data exchange, while addressing cybersecurity concerns with native encryption and secure communication protocols.
- Data Contextualization: Earlier PLCs often stored unstructured data that required significant effort to prepare it for enterprise system consumption. Modern PLCs, however, allow automation designers to define and structure data at the source, ensuring consistency and reducing the need for complex data rework. This capability results in a “single source of truth,” which improves data accuracy and accessibility across systems.
- Low-Latency Data Processing: Modern PLCs have improved memory and processing power, enabling them to collect and process data locally at the edge. This local aggregation reduces the amount of upstream data traffic and lowers the strain on centralized computing resources, which is particularly useful for applications requiring real-time decision-making.
These features make modern PLCs highly versatile, capable of supporting both real-time control and advanced data handling. As a result, they serve as a cost-effective and scalable solution for a variety of industrial automation needs, from basic control tasks to more complex, data-driven applications.
Practical Connectivity
For original equipment manufacturers (OEMs) and automation designers, the primary goal is primarily to develop reliable, standardized systems that can be easily deployed and maintained. However, these users may worry that standard solutions could limit innovation as their needs evolve. Modern PLCs and HMIs address this issue by providing a balance between standardized control and flexibility for future needs.
By leveraging the advanced features of modern PLCs, designers can create right-sized systems that are ready to integrate with enterprise IT systems now, and to support more sophisticated applications in the future. These devices provide a robust platform for current automation needs, while also enabling easy upgrades to incorporate more advanced technologies, such as cloud computing, machine learning, and IIoT analytics.
Figures, all courtesy of Automation Direct
About the Author
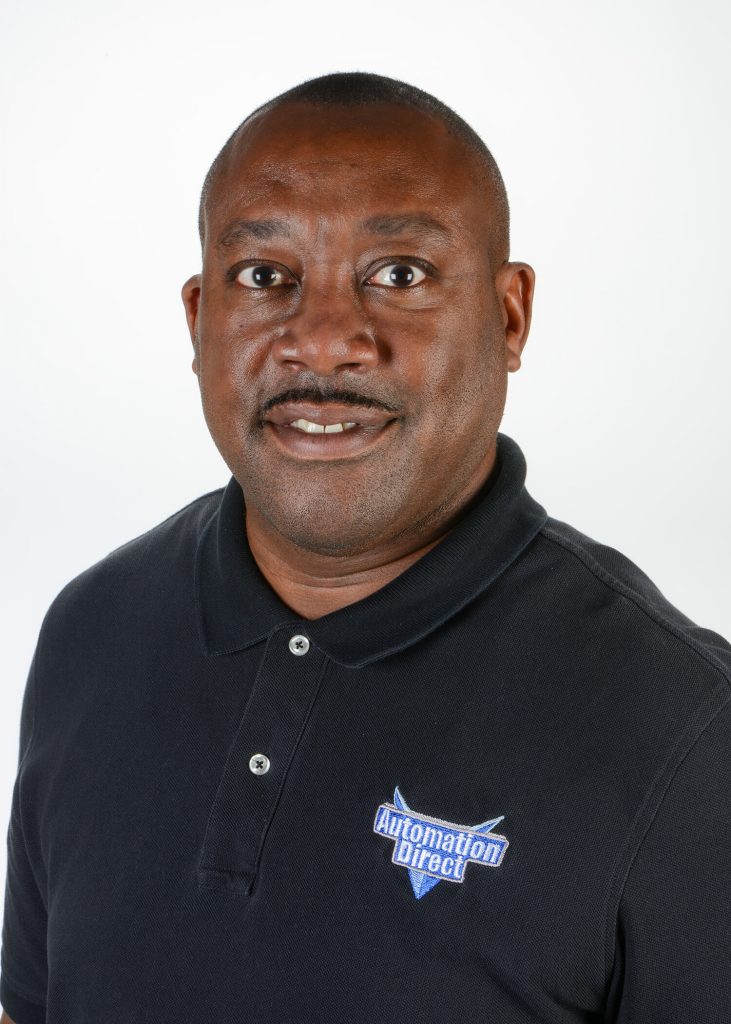
Damon Purvis is the PLC Product Manager at AutomationDirect.com. He has over 22 years of industrial automation experience. Previous roles have included designing and deploying automated solutions in a variety of industries, and managing product development of manufacturing data management and business intelligence applications.