Modular gripper system kits provide a versatile way for designers and OEMs to quickly create material handling and robot end-of-arm tooling solutions.
Many types of industrial equipment must reliably pick-and-place products, materials, containers, and other objects to perform their functions. Designers now have new options to accelerate creation of these gripping solutions, as explained by Pat Phillips in his Fluid Power World April 2023 article titled Get a Grip With Modular Vacuum Kits.
OEMs and designers put a lot of work into gripping systems because dropping a payload can lead to waste and downtime. Custom-engineered systems are often the norm, but these can be costly and inflexible. By starting with a modular system, designers can rapidly build a solution using proven components.
Using Pressure and Vacuum
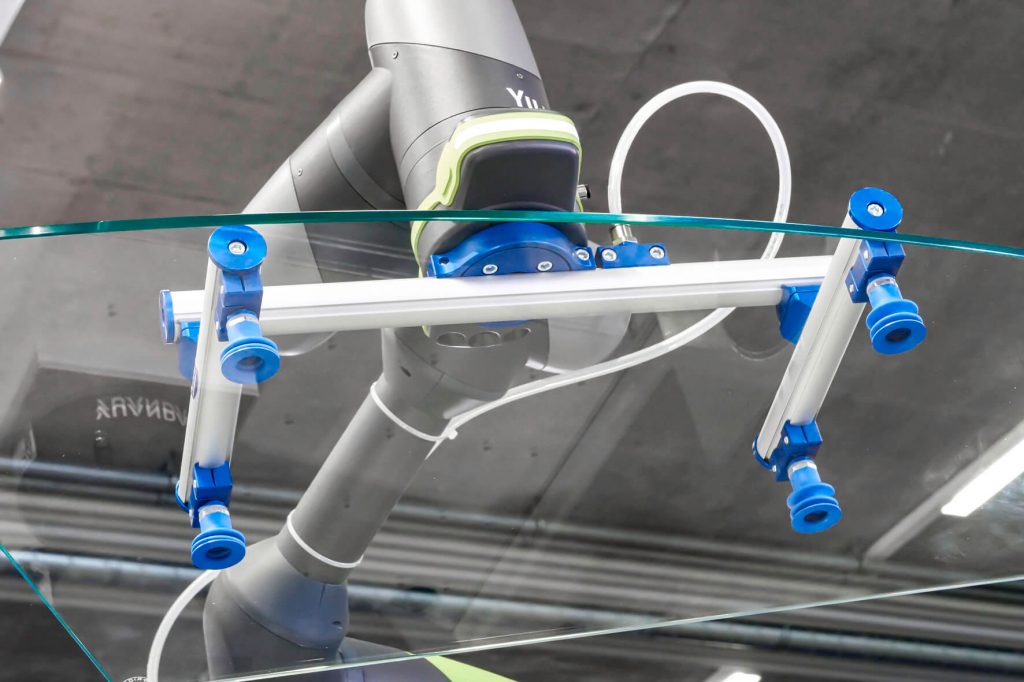
Pneumatic compressed air systems are a straightforward and economical way to drive mechanical hardware and provide significant gripping force. Air pressure can also be used to create vacuum using a vacuum generator, also known as a vacuum ejector.
Vacuum suction cups provide many advantages when implementing gripping functions as compared to pneumatically-driven mechanical grippers:
- Provides a strong grip, with little chance of marring the payload
- Useful for cartons, cardboard, and parts with flat surfaces
- Multiple suction cups can be arranged to provide more grip and redundancy
AutomationDirect offers suction cups in many different materials, such as Elastodur, nitrile rubber, and silicone. The cups are available in both flat and bellowed configurations, and they can be fixed-mounted or installed using a spring plunger. Cup material and mounting is dependent on the payload, and sometimes position sensors are installed on the overall tool so the automation system can detect when the suction cups are in gripping range.
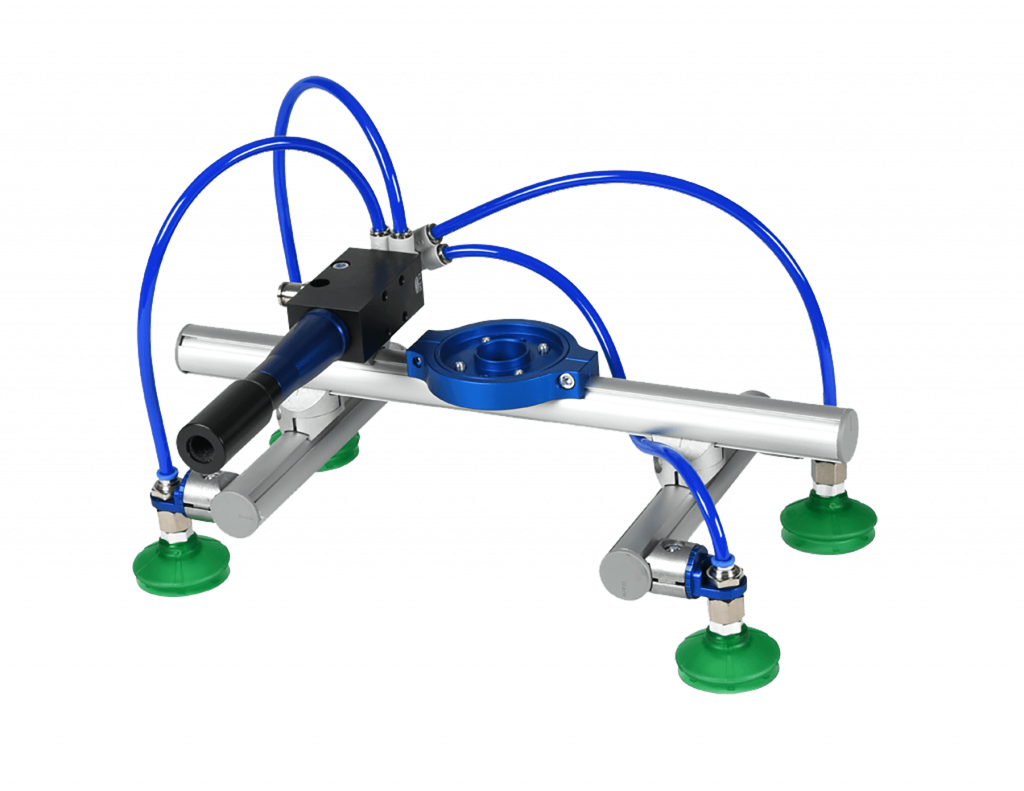
Creating the Gripping Tool Framework
A mechanical framework is needed to arrange the suction cups on the machine or robot end-of-arm. This framework must be strong enough to support the payload while not flexing, yet light enough to not burden the machine or robot mechanisms. A compact form factor is needed to avoid interference with any objects during operation.
Custom designs requiring metal fabrication, but these can be complex to design and build, and inflexible to change in the future. Sometimes T-slot aluminum framing systems are used as the mechanical support.
A better hybrid solution incorporating the best of these traditional approaches has emerged in the form of standardized modular kits with specific vacuum distribution features. AutomationDirect offers Schmalz PXT modular gripper system kits, each including dozens of basic components, and users can add or expand as needed.
One important innovation is that vacuum can be distributed internally through the hollow framing profiles. A variety of sealing end caps and other connectors or adapters are available so users can create exceptionally compact vacuum gripping tools, each of which can be easily modified as needed in the future.
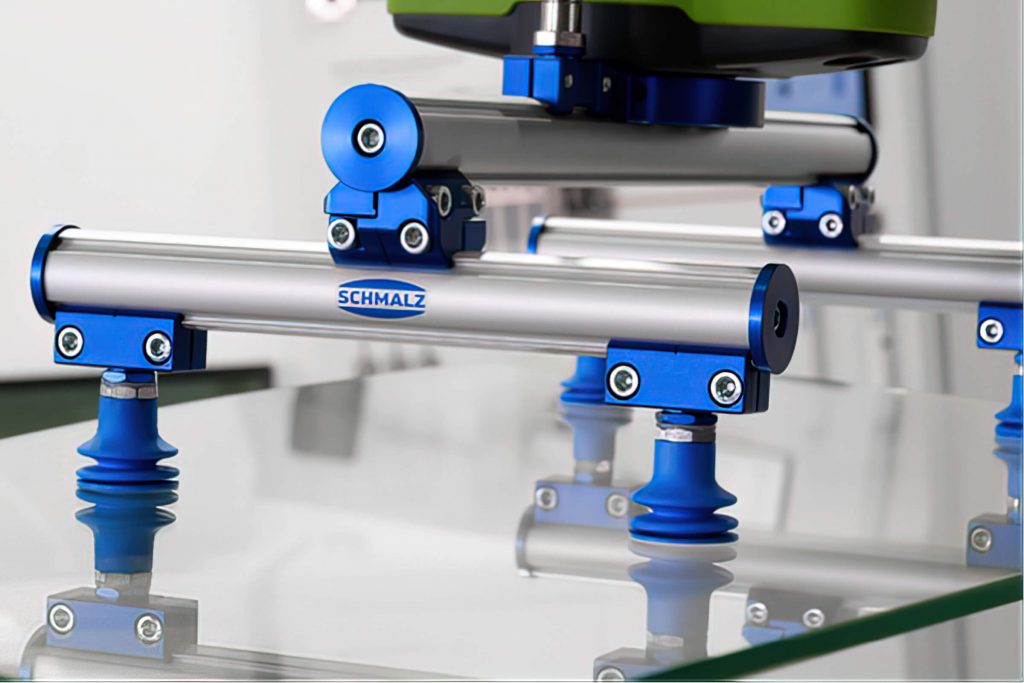
To avoid the costly and risky pitfalls of “reinventing the wheel,” engineers and designers usually prefer to build solutions based on standardized offerings to the greatest extent possible. By beginning their designs with modern modular gripping system kits, end users can create versatile gripping tool configurations more economically and rapidly than with a completely custom approach.
Designers will find the complete portfolio of vacuum end-of-arm tooling kits and components at the AutomationDirect.com website.