You’ve probably seen and read way too many articles telling you to use variable frequency drives on your AC motors to save energy, reduce maintenance and lengthen motor life. This is not one of those articles. Instead, we’re going to show you just how to calculate whether or not a VFD makes sense for your particular application.
It takes about $40k of electricity to run a 100 HP motor for a year at full speed, so it’s worth a look to see if these costs can be cut. Good candidates for VFD operation are motors that need to operate with their output throttled down to meet varying demand. Installing a VFD on these motors can result in big savings, with payback periods often measured in months, particularly when utility company rebates are considered.
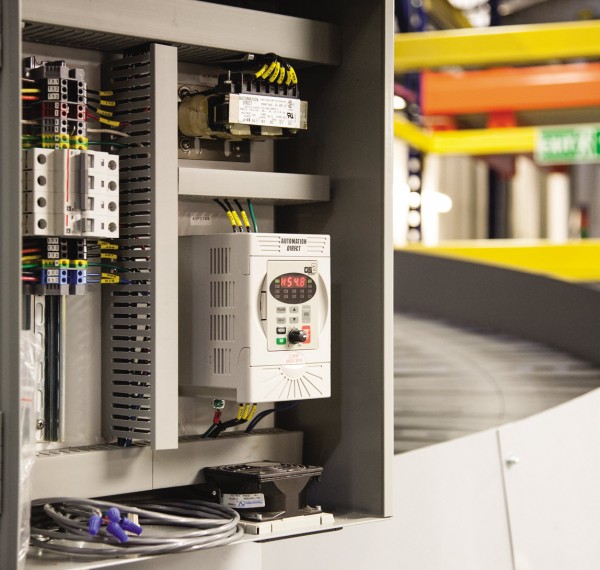
Extra VFD Benefits for Pump Motors
Many AC motors can benefit from adding a VFD, and the cost/benefit calculation procedures provided below apply to all AC motor installations. But centrifugal pump motors are particularly good candidates for VFDs because required pump motor power changes at a much faster rate than flow.
Per the table below, if pump speed decreases from 100% to 50%, then flow also decreases from 100% to 50%. But, pressure decreases from 100% to 25%, and power consumption drops from 100% to 12.5%. A VFD will therefore cut required pump power by a factor of 8 for a 50% reduction in pump flow, quite a bang for the buck.
Effects of the Affinity Law on Pump Applications
Pump Speed (% of Rated Speed) Pump Flow (% of Rated Volume) Pump Head (% of Rated Pressure Pump HP (% of Rated Horsepower | |||
150% 150% 125% 338% | |||
140% 140% 196% 274% | |||
130% 130% 169% 220% | |||
120% 120% 144% 173% | |||
110% 110% 121% 133% | |||
100% 100% 100% 100% | |||
90% 90% 81% 73% | |||
80% 80% 64% 51% | |||
70% 70% 49% 34% | |||
60% 60% 36% 22% | |||
50% 50% 25% 13% | |||
40% 40% 16% 6% | |||
30% 30% 9% 3% |
Determine the Need for Variable Frequency Drives
Unfortunately, it’s not a simple matter to figure out if a VFD is a good idea for a particular AC motor application. But it’s not incredibly complex either, just follow these steps:
Operating Conditions
- Specify the motor to meet both minimum and maximum requirements (only needed for new installations)
- Estimate the time the motor runs at different speeds
Costs
- Determine the installed cost of the VFD including required supplementary equipment for power factor correction, noise filtering, etc.
Savings
- Estimate cost of KWH at each of the selected motor speeds, include a 3% VFD loss, and translate these costs into yearly savings as compared to running the motor at full speed
- Add in savings from reduced maintenance, and from longer motor and other component life, all realized by running at lower speeds
- Add in any rebates from the utility for VFD installations
If savings exceed cost significantly, then a VFD is a good idea. If they don’t, it’s not, at least strictly from an energy savings point of view—although VFDs are often needed for other reasons related to process control.
Some suppliers suggest a VFD is a no-brainer for every AC motor over a few HP, but this is not the case. Instead, each application must be examined individually, as the devil is in the details.
This blog post is based on the article titled VFD Cost/Benefit Calculations, which includes an exciting application example with detailed calculations. The article was authored by Mark Berube, Drives/Motors Product Engineer at AutomationDirect, and ran in the July 2015 issue of Pumps & Systems magazine.
To read more articles about variable frequency drives, click here.