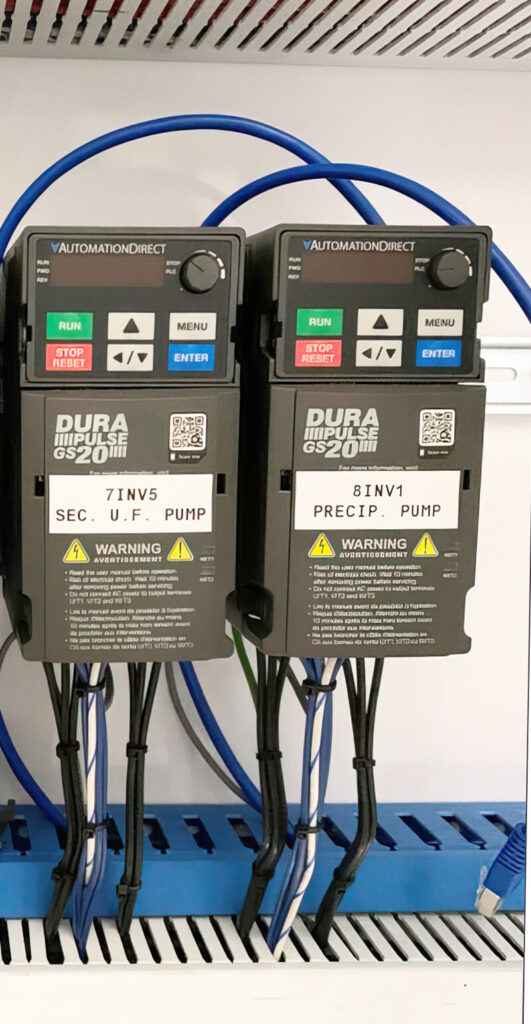
Speed control is the most common VFD control mode, but many of today’s VFDs can also perform in torque control mode, which is needed for certain applications.
Variable frequency drives (VFDs) let designers optimize equipment operating speeds, save energy, and even minimize mechanical wear—but VFDs can play another important role other than standard speed control. Kevin Kakascik at AutomationDirect wrote about the applications and details of VFD torque control, in an Industrial Equipment News July/August 2023 article titled VFD Control: Speed Versus Torque.
Tension Control
The most common VFD torque control application is for motors controlling the winding or unwinding of materials, such as paper, textiles, or even metal sheets and strands. As a product is rolled/unrolled, the effective diameter changes. If the driving motor remains at a constant speed, the winding tension progressively changes, which has a negative impact on the material handling. Torque control enables the driving motor to always apply the desired force, regardless of the winding position, for consistent material tension.
Monitoring Operation
Speed control and torque control are two different but related ways of operating a motor:
- Speed control: The VFD must modulate frequency and voltage as needed to produce a commanded speed.
- Torque control: The VFD must modulate current and frequency as needed to produce a commanded torque.
Torque control was once considered a high-end feature. However, today even mid-range general-purpose VFDs, like the AutomationDirect DURApulse GS20 series, use sensorless vector technology to determine the motor speed and operating current so they can perform either speed or torque control.
Software Configuration
Most VFDs can be set up via their faceplate, but the AutomationDirect GSoft2 PC-based software provides a complete and easy-to-use VFD configuration and management interface for users. This makes it simple to enter basic motor nameplate information, and to initiate the “dynamic tuning” of the motor needed for the VFD to determine the motor electrical characteristics.
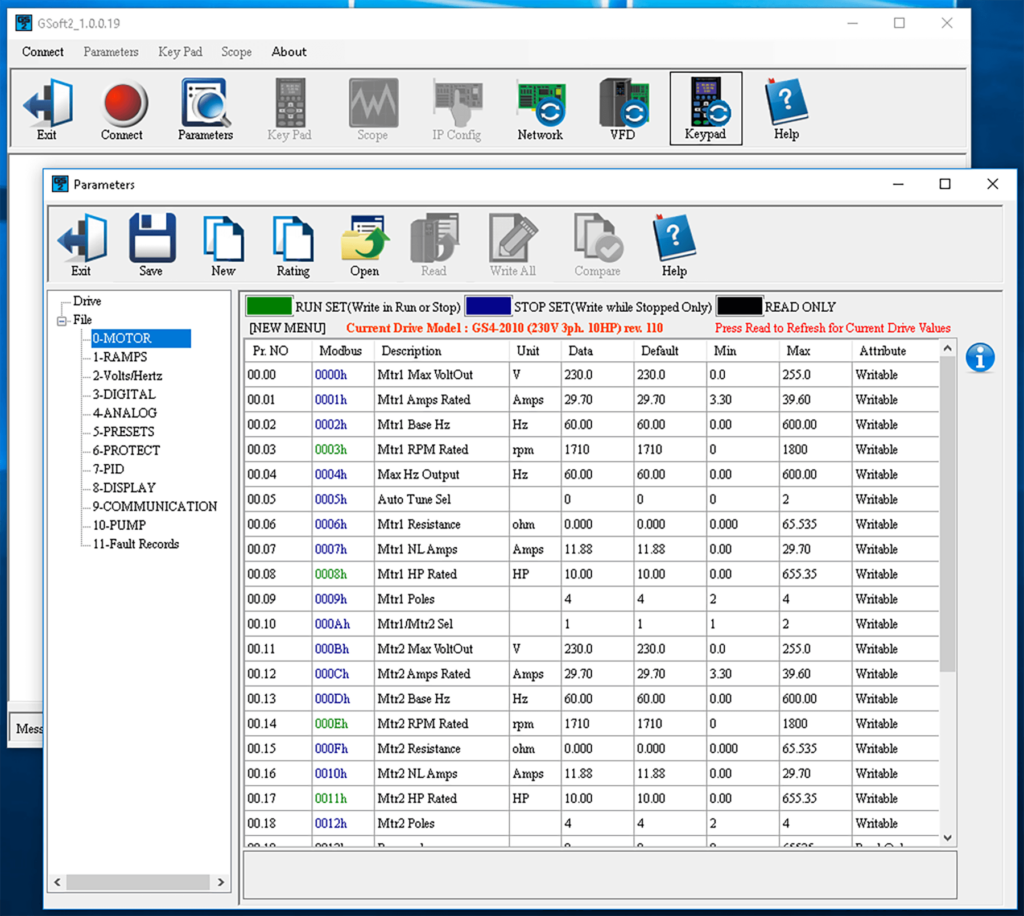
The software even includes built-in oscilloscope functionality to help users visualize electrical characteristics and motor commanded operation, especially useful during commissioning and troubleshooting.
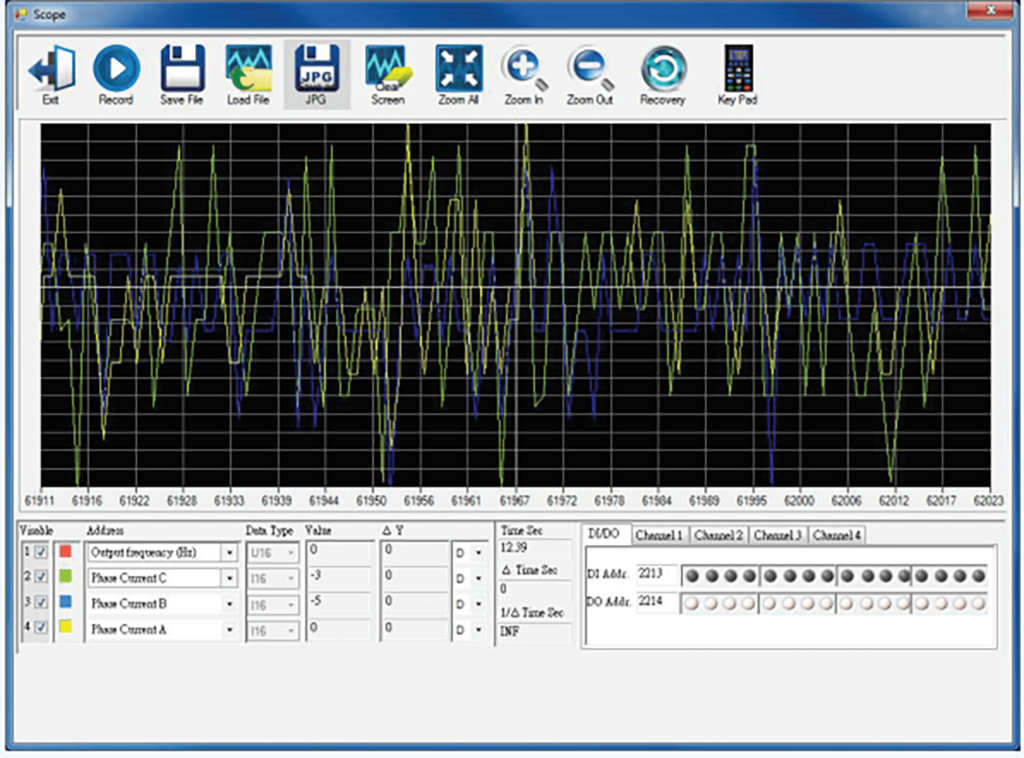
Operating AC electric motors at a commanded torque instead of a commanded speed is important for any kind of winding/unwinding application and for other machinery and material handling tasks. While torque control was formerly a relatively specialized function, this capability has been made more accessible today, even on mid-range VFD products.
Go to the AutomationDirect website to see the complete portfolio of VFDs, motors, and other products supporting motor speed and torque control.