Modern VFDs can now perform torque control for winding/unwinding and other applications, expanding options for equipment designers.
Variable frequency drives (VFDs) are commonly used by automation systems to vary the speed of an AC electric motor, but there is another class of applications where torque control, regardless of speed, is the primary goal. Kevin Kakascik at AutomationDirect wrote an article for the May 2023 edition of Processing Magazine, titled Torque Control: The Other VFD Operating Mode, describing when this mode is needed and how users can implement it.
Speed versus Torque
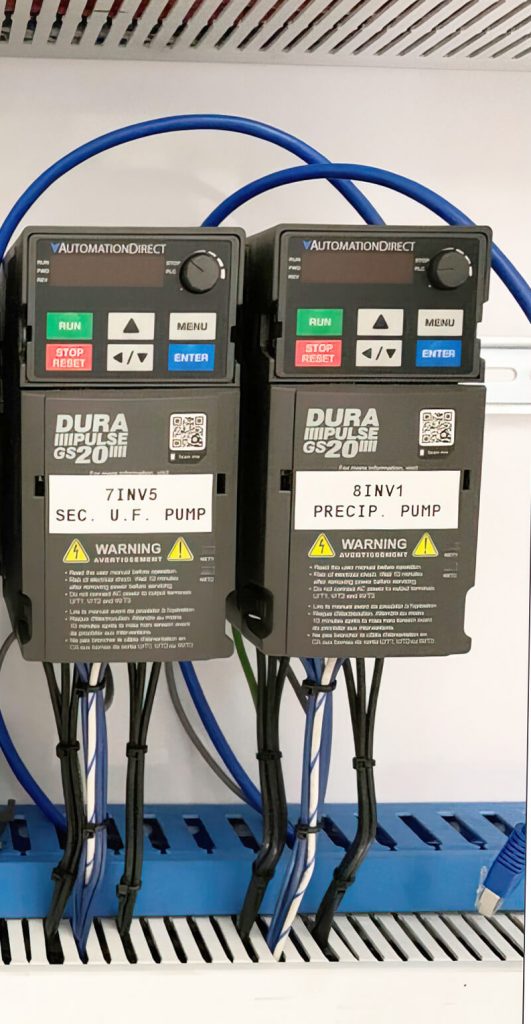
Bicyclists are familiar with the fact that when they are in a specific gear, the speed at which they pedal, and the effort they expend, are related but different. They may need to pedal harder or softer depending on the grade to maintain a given speed, or they can pedal with consistent effort and the resultant speed will vary with the grade.
VFDs are commonly operated in speed mode, where the power and torque are modulated as needed to maintain a speed. But there are many winding/unwinding applications—specifically when the diameter of a rolled product varies but tension must be consistently regulated—where torque control is the proper solution. Torque control was formerly available mostly with high-end VFDs but is now available on mid-level VFDs.
AutomationDirect VFDs, like the DURApulse GS20 and WEG CFW500 families, support torque control and many other advanced features.
For applications in the textiles, paper, and metal sheet industries—when handling products ranging from delicate to robust—maintaining tension on a constantly changing roll size is critical. There are other applications for material handling, and even holding a load in a fixed position, where carefully controlled torque is needed.
VFD Details
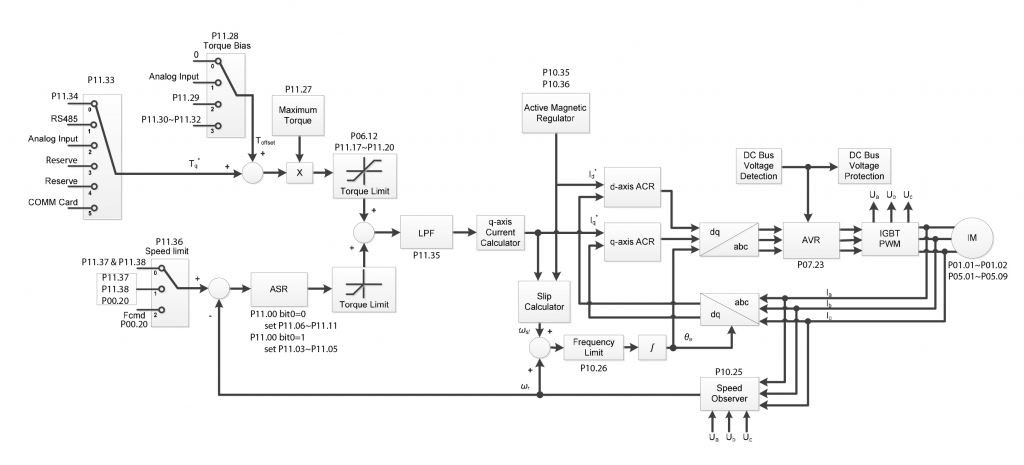
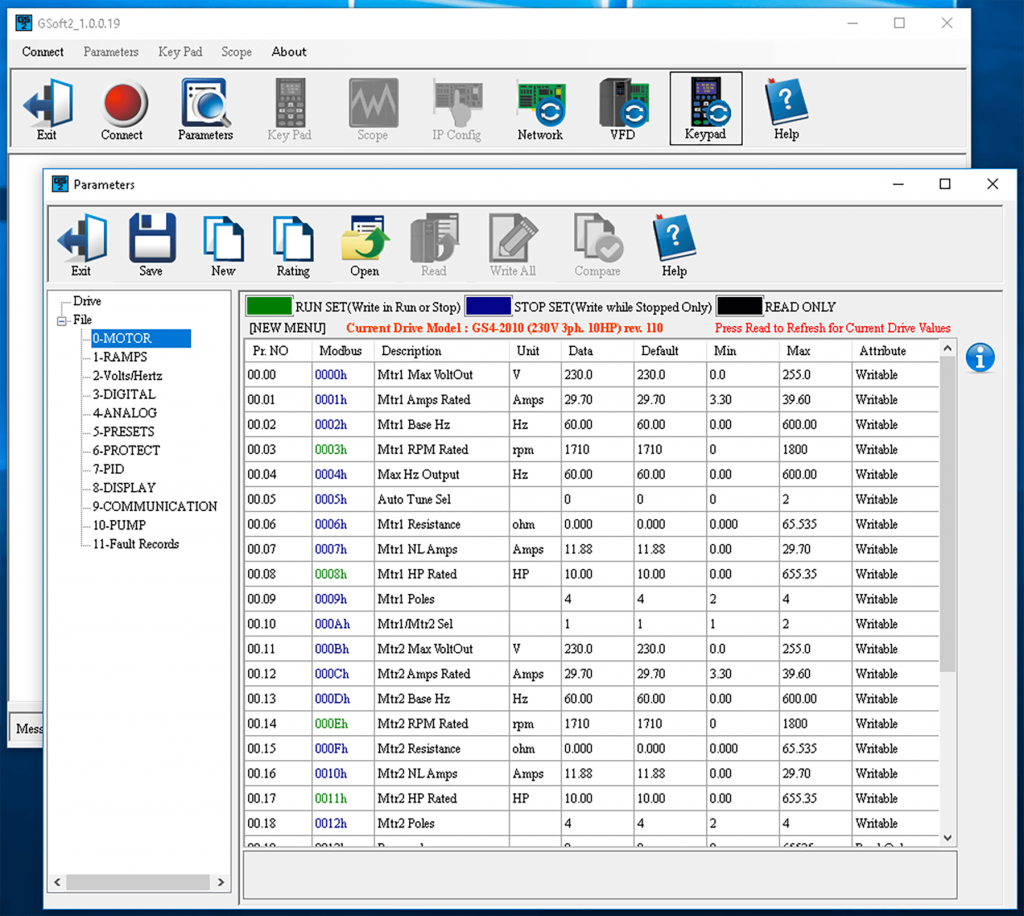
Speed control of 3-phase motors is achieved when the VFD varies the voltage and frequency it supplies to the motor. An external speed sensor can be used, but most mid-range VFDs can use sensorless vector technology—after the VFD “learns” the motor characteristics via a tuning process—to provide adequate speed detection. Sensorless vector drives can also estimate the scalar value of current, which is proportional to torque, with enough accuracy to perform torque control, eliminating the need to measure current with a dedicated instrument.
Users must perform a degree of basic setup by entering key motor parameters, and they must then perform “dynamic tuning” where the VFD operates the bare motor in various ways to determine various electrical characteristics under differing conditions. At this point, the VFD can command the motor in torque control mode.
The PC-based AutomationDirect GSoft2 application software provides users with a complete management and configuration experience—and it offers other advanced capabilities like oscilloscope functionality—to simplify setup, commissioning, and troubleshooting efforts.
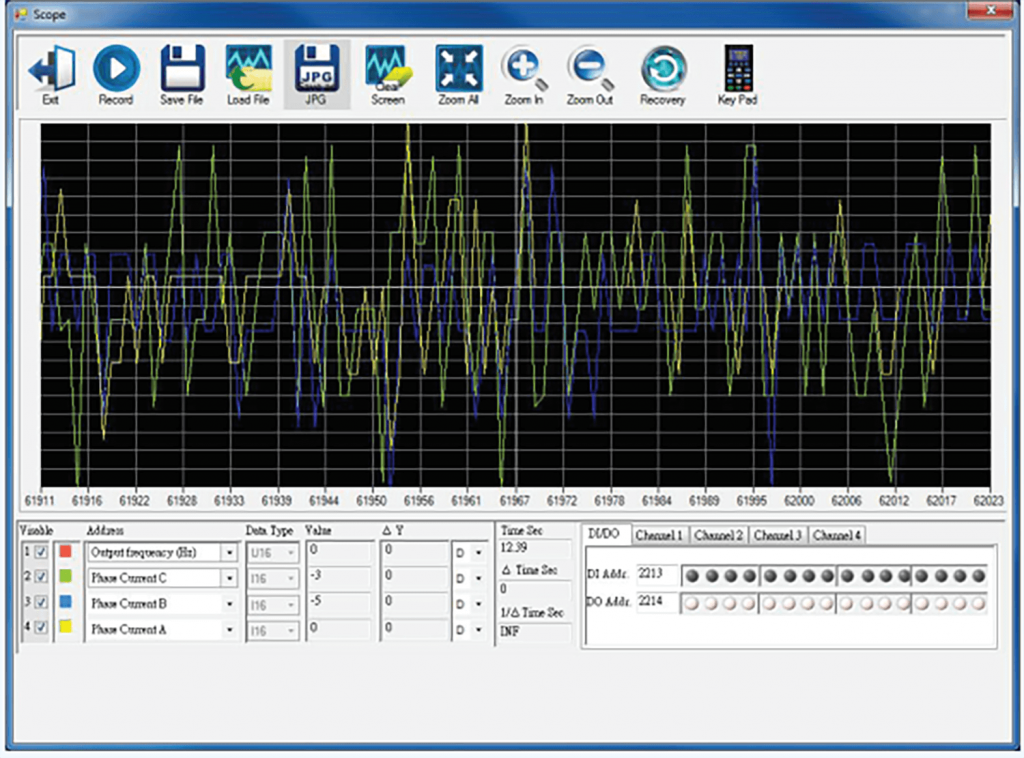
Trouble-Free Torque Control
Torque control is necessary for many industry applications.
Until recently, torque control has been a more sophisticated mode of operation requiring high-performance VFDs. However, this has changed as some of today’s more economical general-purpose VFDs now offer sensorless vector technology and built-in torque control modes.
Visit the AutomationDirect website to explore the complete portfolio of VFDs, motors, and other products supporting motor speed and torque control.