Using thermocouple sensors to measure temperatures in industrial applications.
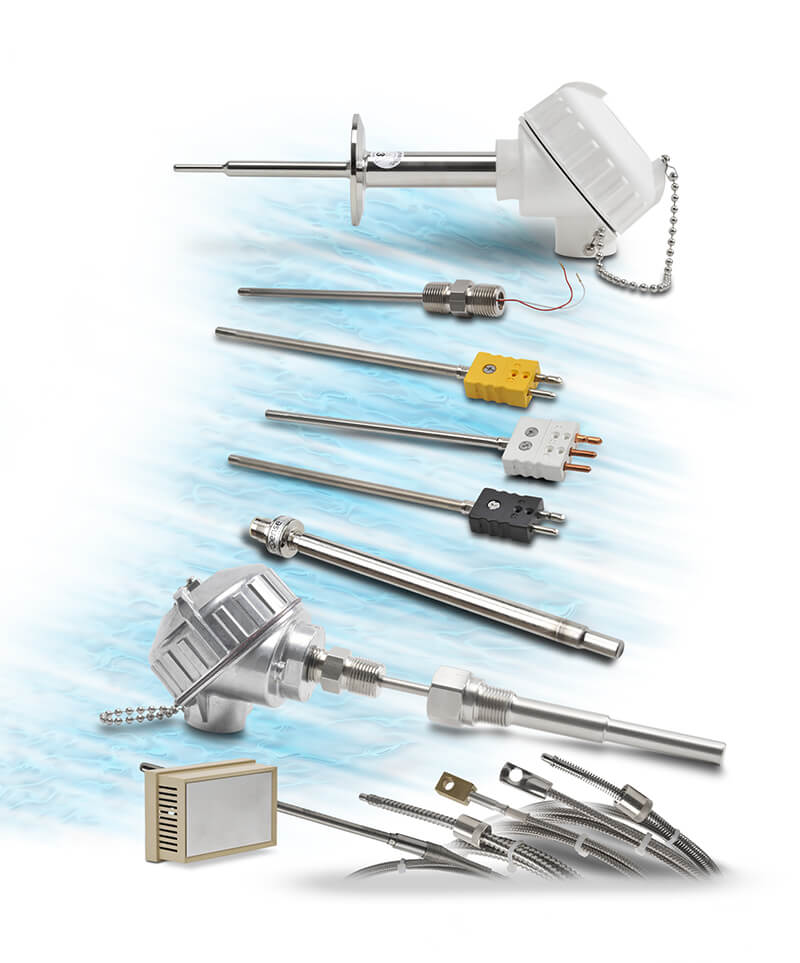
Thermocouple Definition
Temperature measurement is one of the most common requirements for any industrial automation or digitally-monitored system. It is often necessary to detect the temperature of gases, liquids, and physical equipment components.
The primary contact-based technologies for doing so are thermocouples (TCs), resistance temperature detectors (RTDs), and thermistors, and there are also more esoteric methods. Choosing a temperature measurement technology requires balancing the following considerations:
- Measuring and operating range
- Installation requirements
- Accuracy
- Responsiveness
- Drift over time
- Cost
Thermocouples are often the best choice due to their wide measurement range, ruggedness, acceptable accuracy of anywhere from ±0.2 to ±0.5°C, and low cost. For more limited temperature ranges, RTDs can offer better accuracy, although at a greater cost.
Designers need to understand the implementation details to pick the right sensor and associated transmitter or automation interface, as explained below.
Basic Thermocouple Operation
A TC consists of two different types of metal joined together, usually two dissimilar-metal wires. This connection point is where temperature detection occurs, and it’s referred to as the ‘hot junction’. It can simply be two bare wires twisted together, or it can be a welded connection.
The junction of two different metals experiences a small, induced voltage—on the order of millivolts—based on the local temperature and due to what is known as the Seebeck effect. The produced voltage can be directly correlated to the temperature, but the relationship is usually non- linear.
Bare TC sensors are most responsive, but typically some form of physical protection is needed. The TC junction is commonly fabricated within a metal sheath, probe, or jacket suitable for protecting the sensor from the physical conditions of the application. When the TC junction is not electrically connected to the protective sheath, it is called an ‘ungrounded thermocouple’. This style resists electrical noise the best and can provide better accuracy, at the expense of a slower response time. If the TC junction is electrically connected to the sheath, then it is a ‘grounded thermocouple’, which provides a faster response but may be susceptible to noise and degraded accuracy.
Because the TC conductors are wires, they can be conveniently run back to a transmitter or other device for measuring the voltage and relating it to temperature. TC extension cables must be the exact same type as the TC itself so no other voltages are induced. When these wires are transitioned to copper wires for any reason (such as in the transmitter itself), this point is called a ‘cold junction’, and a produced voltage compensation must be applied.
There are many types of TCs manufactured from various alloy combinations to achieve specific usable temperature ranges. They are assigned ANSI/IEC codes, and the most common for industrial applications are type J and type K.
Typical Thermocouple Details (refer to specific product data sheets for actual value)
Type Conductor + Conductor – Continuous Temp Range | ANSI color code | |||
J Fe (Iron) Cu-Ni ) Constantan 0 to +750 DegC (32 to 1382 DegF) | (+) White, (-)Red | |||
K Ni-Cr Ni-AI -200 to +1250 DegC (-328 to +2282 DegF) | (+) Yellow, (-)Red |
A TC can be wired directly into a PLC input module designed for this purpose. More commonly, a temperature transmitter is used to convert the millivolt TC signal to a more common—and linearized—industrial signal of 4-20mA, operating at anywhere from 8 to 35VDC.
4-20mA signals are more resistant to electromagnetic noise than TC millivolt signals. Also, the transmitter can be calibrated such that the output represents a smaller range than the TC is capable of, often preferred as most applications are focused on a relatively narrow band of temperature. For instance, many transmitters are calibrated to represent 0 to 100, 200, or up to 1000°F.
Over time, a TC signal output may change or ‘drift’, so the transmitter is a convenient device for recalibrating the TC against a known standard and delivering better accuracy. Some temperature transmitters are simple analog devices, while others are more capable digital programmable devices.
Form Factors
TC elements are available in several general-purpose and probe arrangements, for simple insertion in many types of applications.
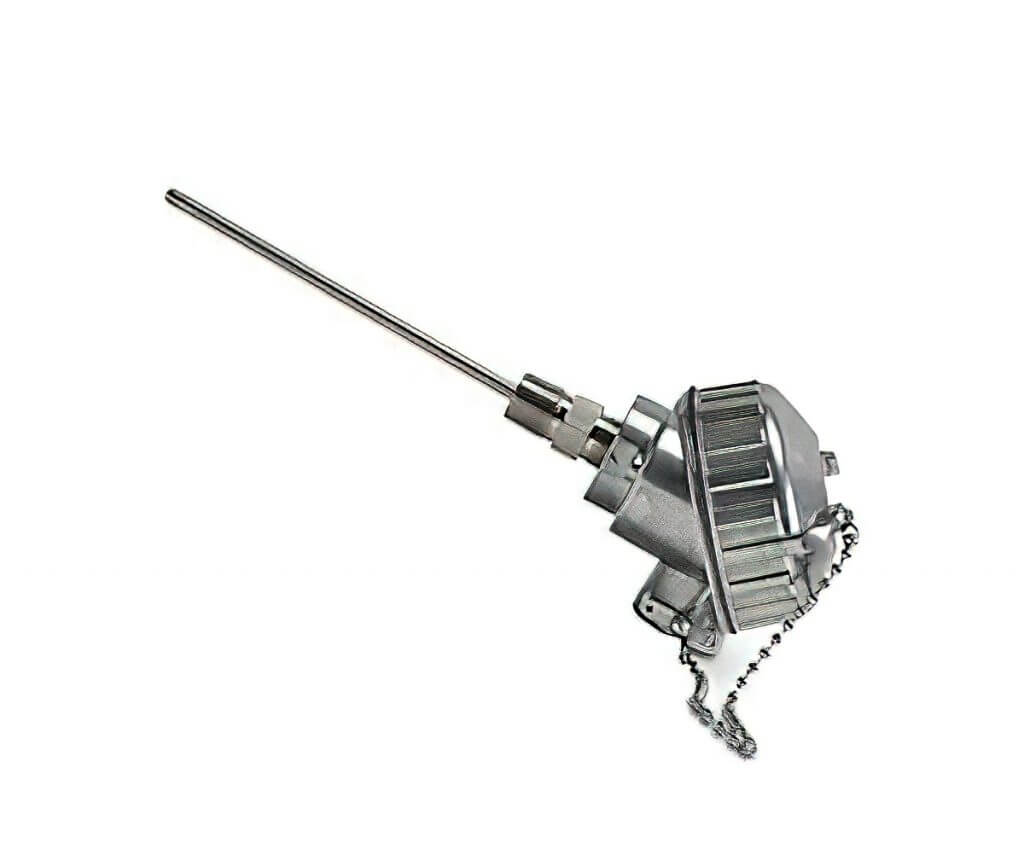
Many industrial projects require a more robust arrangement, and commonly use thermowells bolted into a pipeline or vessel, with a spring-loaded TC probe and connection head. The thermowell is essentially a small pipe, which physically maintains containment of the liquid or gas into the pipe or vessel where it’s inserted. This thermowell protects the TC probe from physical damage, and it allows the TC to be replaced without impacting the process fluid. The connection head allows the field wiring connection to be performed, and it can also accommodate a small hockey-puck style TC transmitter.
Selecting the Right Thermocouple and Accessories
The AutomationDirect website features an entire section devoted to the most popular styles and configurations of thermocouple sensors, thermowells, and temperature transmitters. Whether you need to measure the temperature of a room, of a desktop laboratory process, inside a pipe or vessel, or on industrial equipment, the AutomationDirect website, resources, and team can help you find the right solution.