Automated industrial equipment often requires linear position sensing, and there are many choices ranging from economical to high precision.
Andrew Waugh, Product Manager for Sensor and Safety products at AutomationDirect, wrote an article for the August 2020 issue of Design World titled Lining Up the Right Linear Position Sensing Solution. This article discusses several options available to designers, with pointers to making the best choice for various applications. Here’s a summary, click on the link above for the full text.
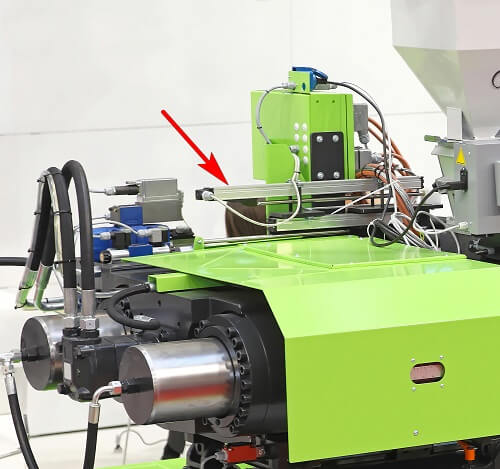
Sensing the presence or absence of automated industrial equipment mechanisms is relatively straightforward. More difficult, however, is detecting linear motion and position over longer operating distances with sufficient accuracy. Designers need to be aware of several options to address applications ranging from small machines up to large outdoor gantry cranes.
Let’s Get Something Straight
Linear position sensing is needed for a specific, but commonplace, subset of motion geometries. Mechanisms can be applied to translate linear motion into rotary motion and determine position, but this impacts accuracy and introduces a failure point. The best linear position sensing technologies provide a continuous analog or digital signal to responsively report position with sufficient resolution. Following are some options.
Linear potentiometer: This is a traditional configuration with a wiper that moves along a resistor. AutomationDirect offers Gefran sensors in this style. They are economical but must be large enough to accommodate the full equipment stroke, and they are subject to wear and problems from environmental conditions.
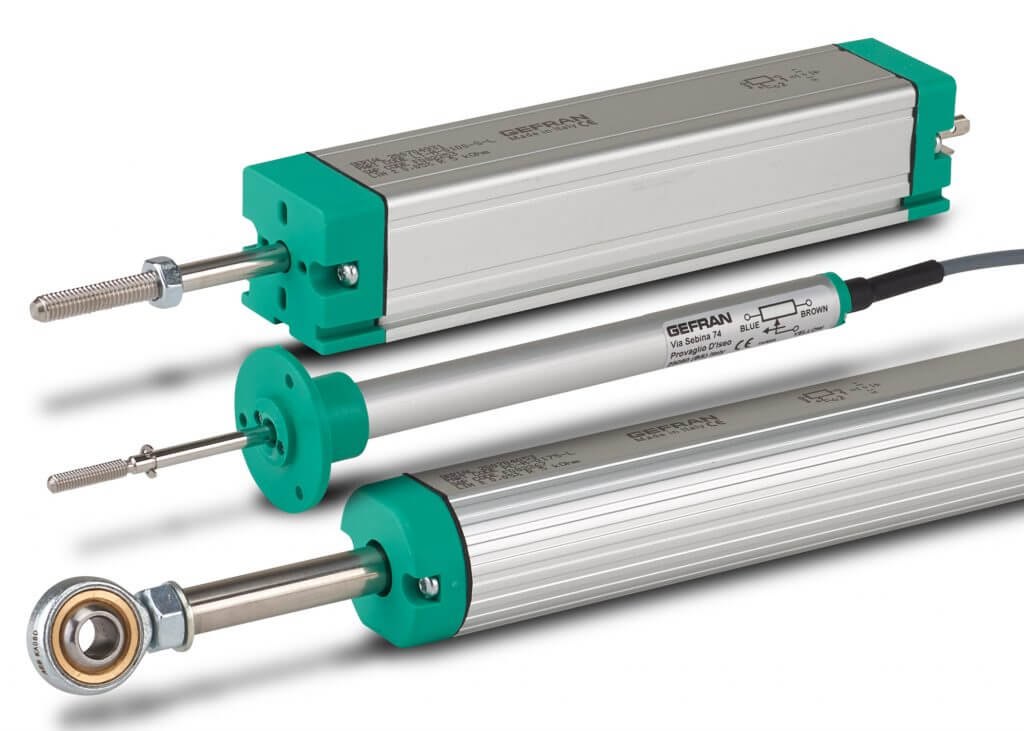
Magnetostrictive: These look similar to linear potentiometers but use magnetics to avoid mechanical wear issues. They cost more than linear potentiometers or linear inductive solutions, but the benefits can outweigh the costs for challenging applications.
Linear inductive: These provide a good middle ground option between potentiometer and magnetostrictive technologies. Linear inductive position transmitters look like the former but use inductive technology, so they are non-contact like the latter.
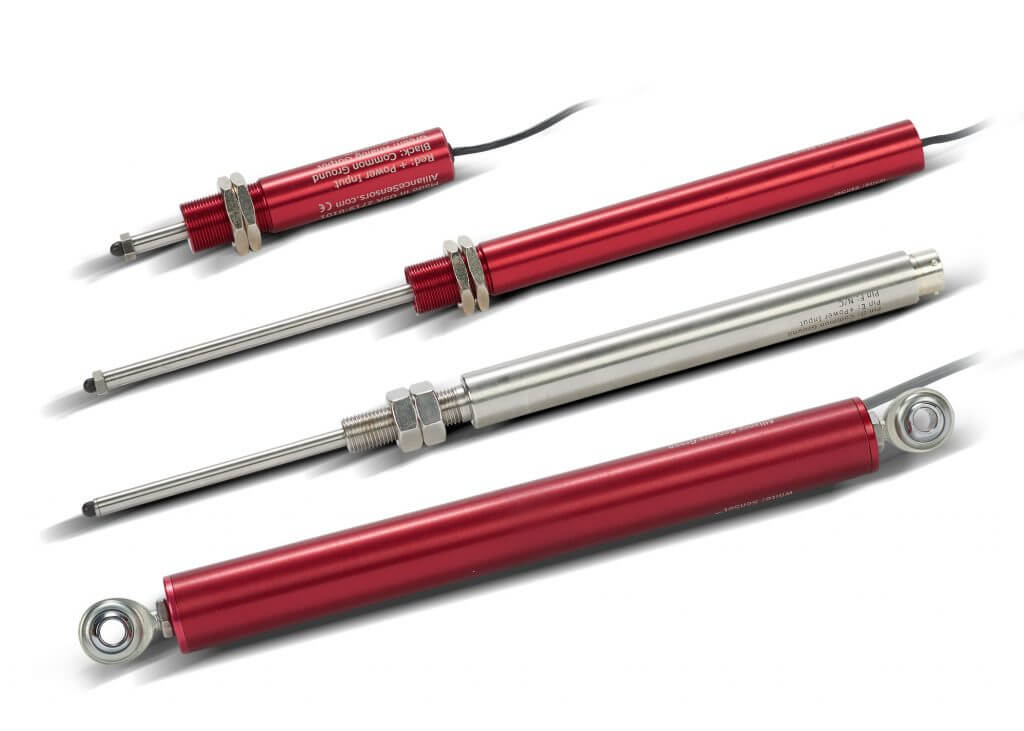
Linear variable differential transformer (LVDT): LVDT sensors use a free-floating armature kept in contact with the target. They are non-contact like linear inductive sensors and can be designed to work with AC voltage circuits for better design flexibility.
Linear encoder: These can be used if the physical arrangement allows for a tape or scale to be detected by an optical, magnetic, or capacitive sensor. They can be good choices for long distances in difficult environments.
Laser: Laser-based sensors provide excellent resolution and are a responsive non-contact technology. However, they rely on a clear line-of-site free from reflections and other environmental conditions.
Lining Up the Right Solution
Most of these sensor options mount to a fixed surface and have a physical portion which must connect with the moving object, or an optical sensor which must see the moving object.
The correct configurations will reliably detect the position of target hardware with sufficient precision for a given environment. Users can choose from many technologies, ranging from simple to advanced, to obtain the best solution for their applications.
Experienced suppliers with a wide range of solutions, like AutomationDirect, can help users select the right sensors for their applications.