Motion-optimized PLC platforms combine traditional controls functionality with advanced multi-axis motion control, providing a streamlined automation solution.
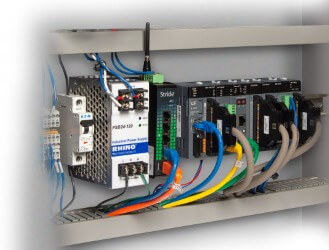
Industrial motion control applications range from simple to complex and are generally considered a design specialty. Currently, there are some entry-level solutions, and designers are also aware of high-performance motion control platforms. However, there are many cases where designers would like to coordinate traditional automation with medium-complexity motion control, without incurring the expense and difficulty of integrating multiple platforms, or learning a highly sophisticated motion system.
A Design World August 2024 article titled Next-Level PLC Motion Control, by Kevin McClelion and Joe Scoccimaro of AutomationDirect, discusses how there is now a happy medium suitable for a wide range of applications. A PLC with significant built-in motion-specific features can perform extensive multi-axis motion control, and directly monitor and control related field equipment.
Next-Level Motion Control
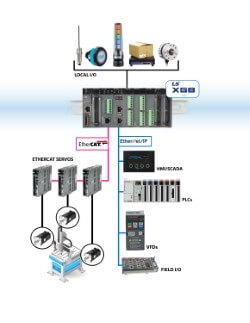
Designers have several choices for implementing a few basic motion control axes. They can choose a servo drive with an on-board motion controller, and even use hardwired signals to connect some of these together. Alternatively, certain PLCs can command a few servo drives using hardwired connections. However, hardwired signals can only support limited interconnectivity.
A better choice for many applications is to select a motion-optimized PLC. This type of PLC is based on industrial-grade hardware, and it can connect to field devices and supervisory systems using industrial Ethernet protocols to perform monitoring, control, and data communications. It also includes significant motion-specific instructions, and it can connect to many servo drives using standard IEC 61158 Ethernet for Control Automation Technology (EtherCAT) motion control fieldbus.
When to Select a Motion-Optimized PLC
The following requirements would prompt the selection of a motion-optimized PLC able to operate servo drives using EtherCAT:
- Command and coordinate more than two or three axes, up to four or eight
- Support for enhanced data connectivity
- Ability to execute advanced motion operations, including speed-limited torque control, registration for printing and bagging operations, specialized moves such as helical, and virtual axes coordination
- A preference for coordinating additional equipment automation, with the ability to use IEC 61131-3 compliant programming languages
A motion-optimized PLC, connected to servo drives using EtherCAT, consolidates traditional control and motion via hardwired devices, industrial fieldbuses, and EtherCAT connectivity. The resulting architecture provides high-performance servo motor control, along with a convenient way to aggregate data and communicate it to higher-level visualization and computing systems.
Typical applications include fillers, assembly machines, and multi-stage production line equipment. Extensive data connectivity is demanded by modern automated systems, and a motion-optimized PLC is well suited for this task. Also, this type of PLC provides native diagnostics and trending, essential for developing and commissioning complex motion applications.

More Capable Motion Control
While some motion control applications are simple, there are plenty of cases where motion control has developed a reputation for being costly and complex to implement. Yet there are plenty of applications between these two extremes.
For mid-tier motion control—with several coordinated axes, other sensing and automation devices, and a need for data handling—designers will find that a motion-optimized PLC is likely to meet or exceed all their technical needs, while providing high performance-to-cost ratio.
Check out the AutomationDirect LS Electric XGB PLCs (Stackable Micro) webpage to discover motion-enabled PLC, EtherCAT, and servo drive products available to support your automation and motion control project needs.