Applying commercial off-the-shelf automation products can provide the most capable and supportable solution for end users trapped with underperforming automation systems, as with this application.
By: Aaron Stahl and Edward Stahl, Spring Valley Electric
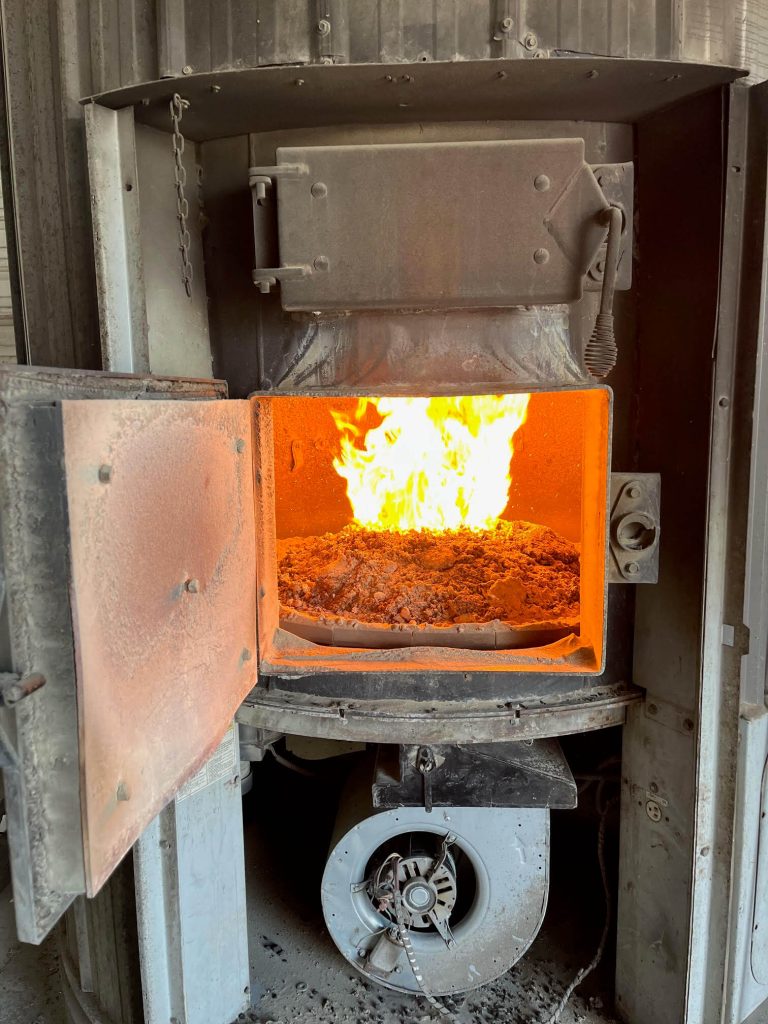
Worldwide, there are countless examples of businesses forced to work inefficiently because they are using equipment which is automated by systems that are underperforming or downright broken. Industrial automation is a bit of a specialty, and many companies simply are not staffed to troubleshoot control problems, much less to perform upgrades. Unless the original equipment manufacturer or other service technicians are available, the equipment owner may find themselves stuck because removing and replacing either the entire machine, or even just the control system, is usually cost-prohibitive.
To address these types of issues, Spring Valley Electric (SVE) provides general electrical, and now control system, installation and repair services for a number of end users in rural South Dakota, and more than a few of their customers have run into problems keeping automated equipment running. This prompted the team to be creative in how they could support their customers, and part of this process was learning how they could incorporate programmable logic controllers (PLCs) and human-machine interfaces (HMIs) to keep their clients running.
Winter is Coming
One of the SVE clients runs a livestock operation where the facilities need a constant supply of hot water, especially during the winter months. An existing coal-fired boiler had served for many years, but the automation system was progressively degrading, and the equipment became very unreliable (Figure 1). The facility did not have the programming tools, source code, or expertise to support the system.
In addition, even when the boiler ran normally there were several nuisance tasks that required manual in-person attention, and if the system had problems, there was no remote alarming capability. This client certainly couldn’t afford a new boiler, and they were worried about how much work it would take to limp the system through the next winter. They thought they were stuck.
Fortunately, the team at SVE had been called in for other work at the site, and they let the owner know they could take on the project to upgrade the system before the onset of winter.
A Practical Upgrade Path
There exists a multitude of automated machinery throughout the world, much of it using dedicated microcontrollers or programmed PLC/HMI systems. As these systems age, sometimes the original equipment suppliers are not accessible, and/or the automation components become obsolete. Often these systems are locked-down, so the users have no access to modify or even view the code. When the SVE team can perform an electrical/controls repair on a problematic piece of equipment, that is usually the most cost-effective way to get their clients up and running, but in some cases this just isn’t practical.
Fortunately for the boiler project, while the facility staff did not understand the inner workings of the existing legacy controller, they did know how the equipment was supposed to work, how it was typically working (or not working), and how they wanted it to work.
Over the years, SVE had built up their capabilities to serve customers in this situation. The SVE team gravitated to using AutomationDirect components for many reasons. The programming and configuration software is free, and there is ample online technical information, video examples, and phone/internet support in place to help them succeed. SVE also knew that all the parts they needed would be readily available at a fair price. After progressively gaining experience from applying AutomationDirect components for these types of projects, the team suggested they could quickly and economically perform a retrofit of the existing control system, and the owner authorized them to proceed (Figure 2).
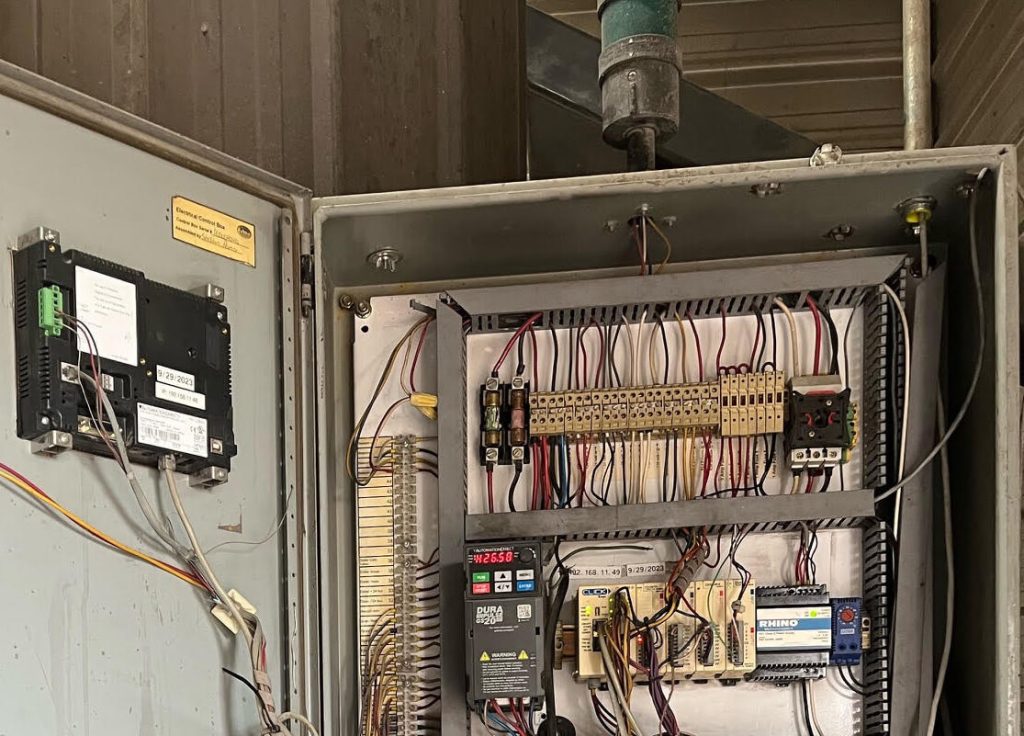
To minimize the amount of fieldwork, the existing panel would need to be retained, as well as the wiring to the field devices. It would be a challenge to re-use this existing wiring, some of which was quite short. However, the compact footprint of the AutomationDirect CLICK stackable micro brick PLC, DURApulse GS20 variable frequency drive (VFD), and other related components eased the retrofit task. Furthermore, the C-more touchscreen HMI fit nicely into the door and provided the proper degree of environmental resistance.
Turning Up the Performance
Basic boiler operation was fairly straightforward. Two draft fans ensured proper air flow, and a screw auger would run at a variable speed selected by the operator to meter coal into the burner and achieve a desired water temperature. There was also a cleanout sequence where the burner turned off and a mechanism was activated to clean out the flue, then the boiler would restart and continue. The boiler would start and stop as needed to maintain the desired temperature range, and there were some alarms.
However, besides the fact that the legacy system was unreliable, the facility staff had a few pain points with the existing system:
- Many settings simply could not be adjusted.
- Of those settings that could be adjusted, such as the feed rate, an in-person operator was required at the equipment to perform this task. Feed rate adjustment was necessary to account for changing coal and environmental conditions.
- There were no load cells to measure weight in the system and no other way to track throughput, so it was difficult to know when the coal storage silo needed to be replenished.
Armed with this knowledge, the SVE team developed a PLC program and HMI configuration that superseded the basic operation of the previous system, while adding significant functionality. Operators can now adjust all pertinent settings, including not just water temperature limit and differential, but also cleaning cycles (Figure 3). In fact, all HMI displays can be securely accessed by the facility staff using a mobile device, like a smart phone or tablet, via an internet connection.
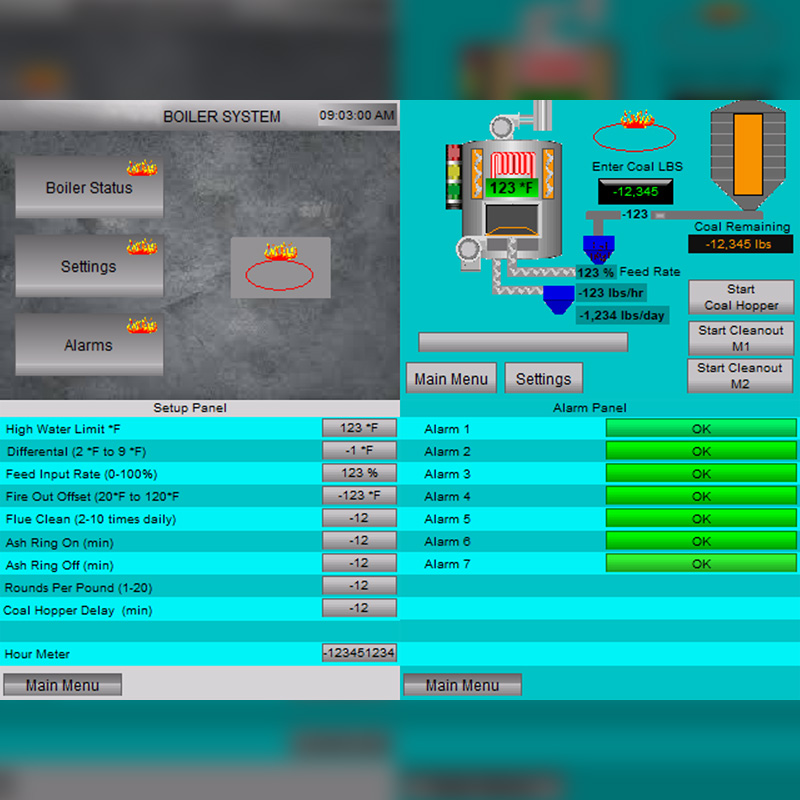
There is now a way to calibrate how many turns of the VFD-driven feed screw are needed to discharge a pound of coal—a variable that changes based on coal conditions and screw wear—so a simple throughput calculation was possible. The HMI also allows the operator to enter how many pounds of coal are added to the silo when it is refilled, and the system then tracks how much is depleted, so the operators have early indication of when a refill is needed. Multiple alarms are configured to send warning calls/voicemails to the users via a remote auto dialer, so they are notified of any impending or existing issues.
Escaping a Proprietary Trap
Many businesses may feel trapped because they are forced to get by with poorly performing or completely broken automation systems, but replacing the controlled equipment is rarely financially feasible. Fortunately, AutomationDirect offers a complete portfolio of PLCs, HMIs, VFDs, power supplies, and many other automation components, which are ideal for retrofit projects due to their space efficiency and attractive price/performance ratio. These easy-to-use products empower end users, and the contractors supporting them, to keep their facilities running smoothly.
For every industry, systems integrators and electrical contractors specialize in using these proven products to solve their customers’ automation problems. At the end of the day, their end user customers will enjoy a reliable system, based on readily available and supportable parts, with better functionality than they had previously, and much improved long-term support.
All figures courtesy of Spring Valley Electric
Author Bio
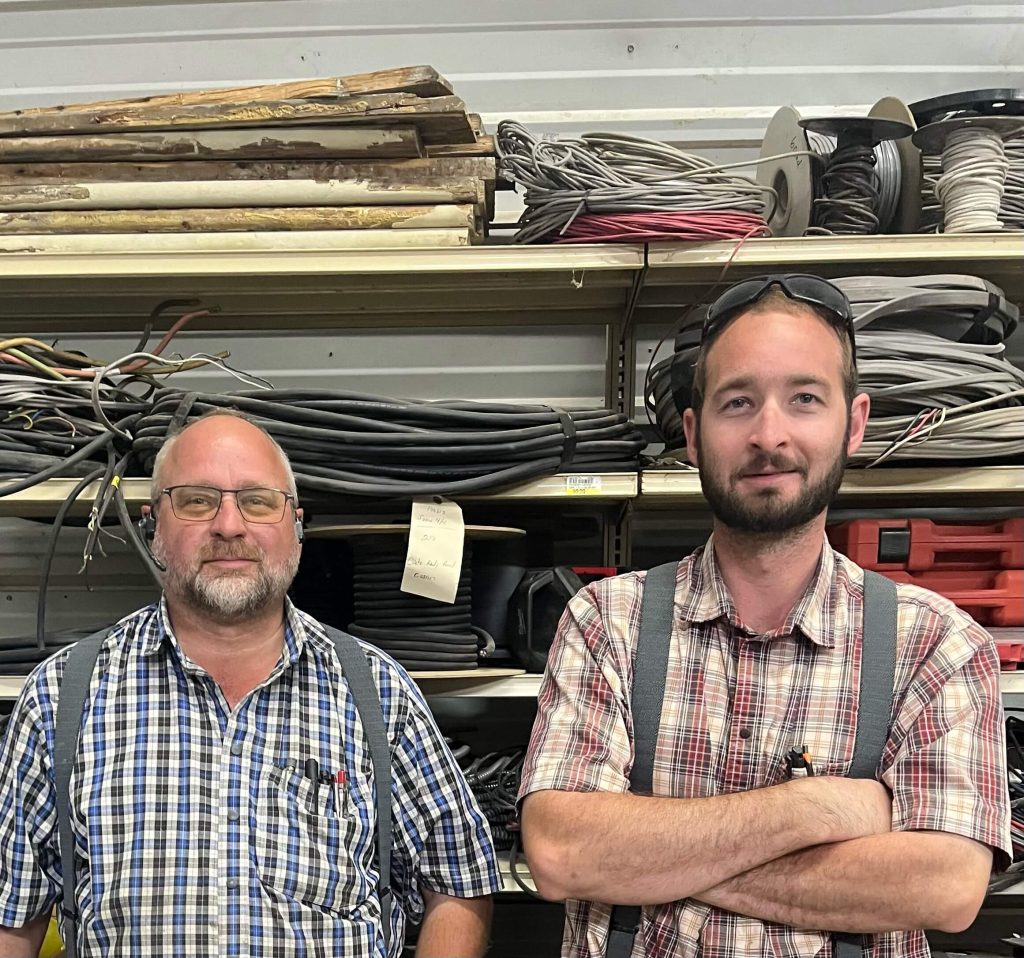
Edward Stahl founded Spring Valley Electric over 20 years ago, and Aaron Stahl joined him almost 10 years ago. They have grown the business serving local residential and commercial customers.