The EtherCAT protocol is a high-performance and cost-effective Ethernet networking technology, providing a versatile solution when EtherNet/IP and PROFINET simply aren’t fast enough.
By Joe Kimbrell, AutomationDirect
Ethernet rapidly expanded into and throughout commercial information technology (IT) networking connectivity environments beginning in the 1980s, and it has experienced rapid performance advancements and adoption since then in the IT realm. Once the speed and responsiveness improved sufficiently, and robust form factors were developed to withstand operational technology (OT) environments, Ethernet was ready for industrial applications.
However, Ethernet as a media must also be applied in conjunction with one or more industrial communications protocols suitable for the application. There are several protocol options, some of them general-purpose, and others specialized for certain applications. A top choice for high-speed input/output (I/O) signaling and motion control applications is Ethernet for Control Automation Technology (EtherCAT®).
The Right Ethernet Protocol for the Right Job
Some estimates (Reference 1) indicate that for the industrial network market, Ethernet protocols as a group hold almost 70% of the share and growing, with traditional fieldbuses at around 25% and shrinking, and wireless making up the remainder and growing. The two most deployed general-purpose protocols are EtherNet/IP and PROFINET, and there are several other protocols holding much smaller market shares, including Modbus TCP. But a solid third place is occupied by the EtherCAT protocol.
The EtherCAT protocol was originally developed by Beckhoff Automation in the early 2000s, and they then donated the rights so the protocol could be standardized under IEC 61158. The EtherCAT protocol works over normal Ethernet media much more efficiently than other general-purpose industrial protocols. A key feature of EtherCAT is the ability for communication among devices to maintain very rapid data transfer with accurate synchronization and deterministic cycle times.
EtherCAT Details
This high level of performance is possible because specific master and slave devices are used. A single master device initiates a data telegram (potentially containing multiple datagrams), which is then sequentially passed through slave devices (network nodes). This avoids the type of data collisions which may occur with other protocols. Each device rapidly receives and then sends the telegram to the next node in a cyclical fashion. Data can be inserted in the telegram as it passes through a node, but processing data received at the node only happens “on the fly” when possible after the frame is read, so there are no delays in transmitting the frame (Figure 1).
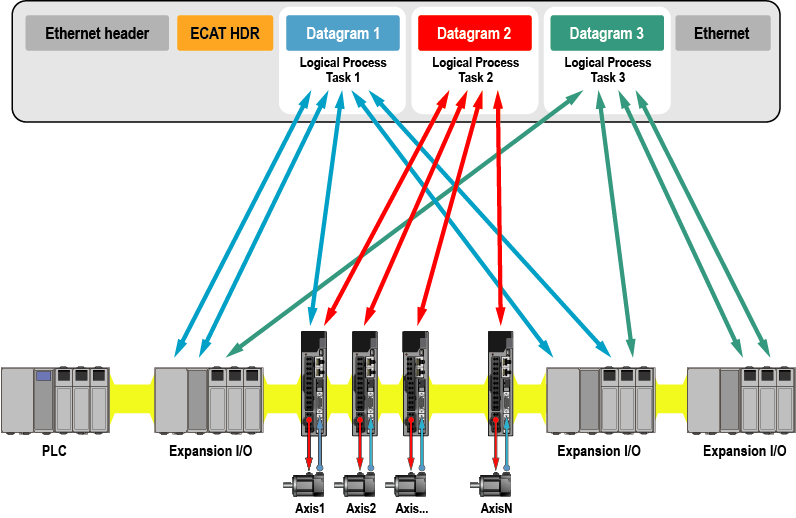
Therefore, the EtherCAT protocol is:
- Deterministic: Provides short deterministic cycle times of less than 100 µs, with a minimal communication jitter of less than 1 µs.
- Scalable: As an open standard that works with many makes and models of controllers and devices, it can handle a large number of devices on a single cable, making it a convenient architecture for complex multi-axis motion control systems.
- Cost-effective: Although master and slave devices are specialized hardware, the architecture uses standard Ethernet installation media and the reduced installation complexity of a linear topology (although other topologies are possible), which is very economical and provides favorable overall hardware costs compared with older technologies.
EtherCAT in Motion
Many applications are well-served with general-purpose industrial protocols and network architectures, but motion control is a notable exception which benefits from the performance possible with the EtherCAT protocol (Figure 2).
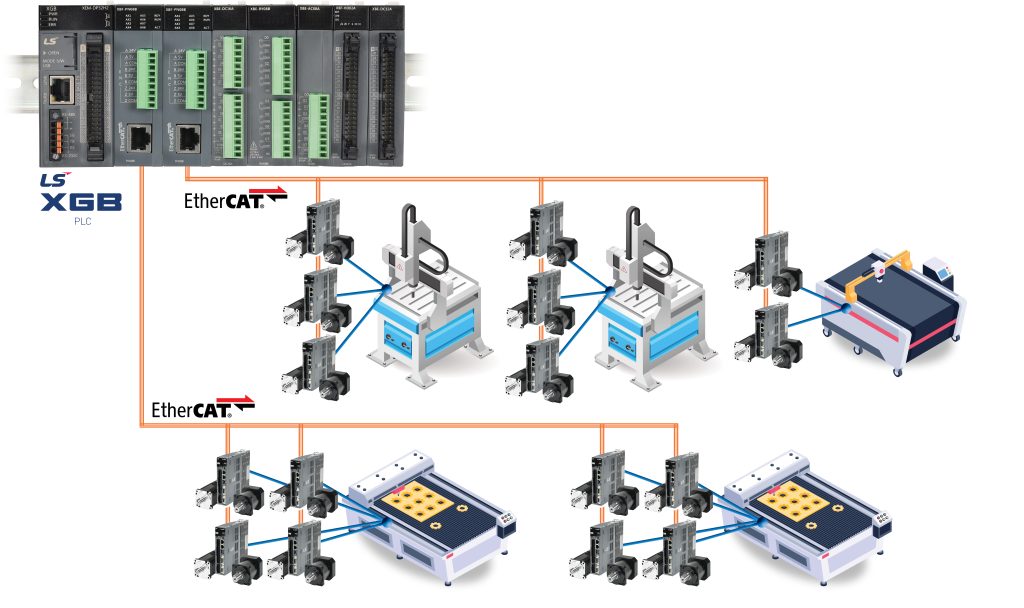
The EtherCAT protocol, when implemented between a programmable logic controller (PLC) or dedicated motion controller, and one or more associated servo drive/controller slaves, simplifies installation and enables functionality to be fully orchestrated in the PLC (Figure 3). It also permits extensive data communication between the controller and drives, which is not possible using traditional hardwired control.
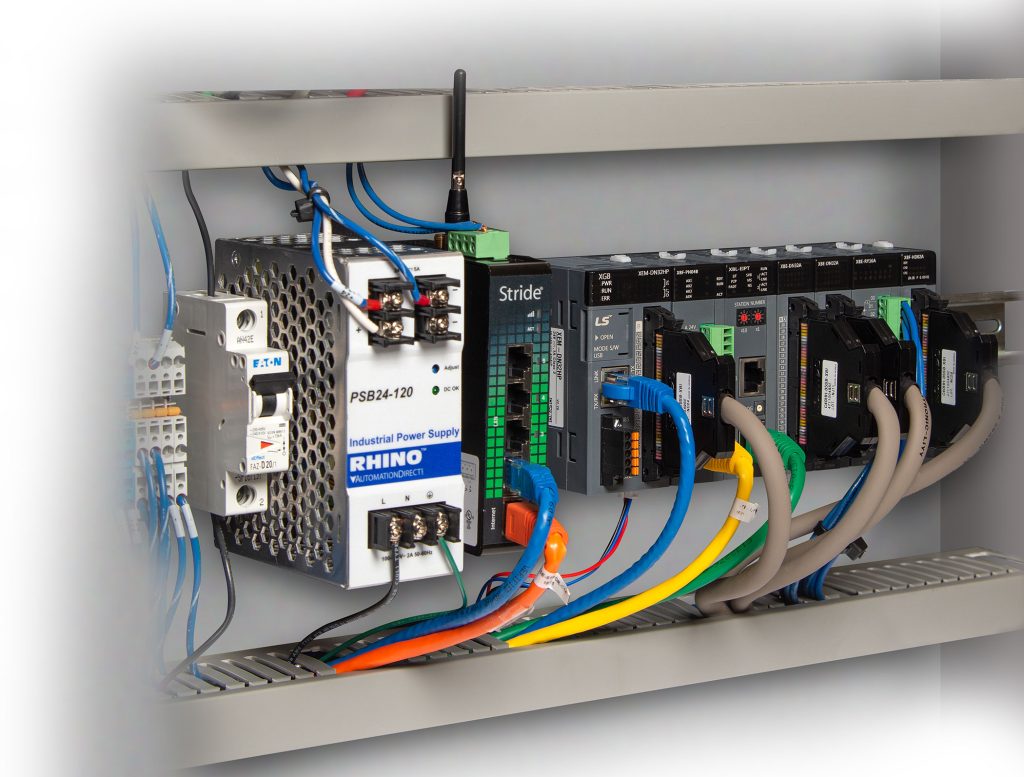
For high-performance industrial I/O and motion control applications, the EtherCAT protocol offers a powerful and versatile solution. Its combination of features supports the speed, accuracy, scalability, and cost-effectiveness needed to make it a preferred choice for these applications.
References
Reference 1: https://www.hms-networks.com/news/news-details/21-05-2023-industrial-network-market-shares-2023
All figures courtesy of AutomationDirect
About the Author
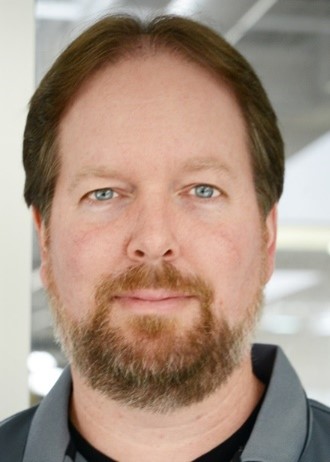
Joe Kimbrell is the Product Manager for Motion Control Products at AutomationDirect. He has over 25 years’ experience with automation, motors, drives, motion control, and servos, and has worked as engineering manager at a packaging OEM and at a multi-axis motion control integration firm. Joe holds a BSEE degree from Georgia Tech.