Proximity sensors allow non-contact detection of objects. Therefore, they are used in many industries, including manufacturing, robotics, semiconductor, and many more. Inductive sensors detect metallic objects while capacitive sensors detect all other materials. Ultrasonic sensors detect all materials by using sound wave reflections to determine presence.
All applications have certain specific needs, but, in general, the following steps will help you choose the correct sensor for your application:
Step 1:
What is the sensing distance required?
The sensing distance is the distance between the tip of the sensor and the object to be sensed. The selection guide and the specifications table for each sensor family lists the sensing distances.
Some things to keep in mind are:
A. In many applications, it is beneficial to place the sensor as far as possible from the sensing object due to temperature concerns. If a sensor is placed too close to a hot temperature source, the sensor will fail quicker and require more maintenance.
Greater distance may be achieved with extended and triple range sensors. In many applications, a sensor may not be mountable close to the sensed object. In this case, longer sensing distances are needed. Extended sensing distance sensors are offered in 8mm to 30mm dimeters, and triple sensing distance sensors in 8mm and 12mm formats.
In many cases, using an extended distance sensor to get the sensor farther away from the detected object can be beneficial to the life of the sensor. For example, without an extended distance sensor you may not be able to place the sensor close enough to the detectable object, or you may need to buy more expensive high temperature sensors.
Another example would be a mechanical overshoot situation, where mounting the sensor farther from the detection object may eliminate unneeded contact with the sensor, thereby extending the life of the sensor.
These are just a few examples, but the benefits of using extended distance sensors are obvious in many applications. Think of how extended distance sensors could save you time and money in your application.
B. The material being sensed (i.e. brass, copper, aluminum, steel, etc.) makes a difference in the type of sensor needed.
Note: If you are sensing a non-metallic object, you must use a capacitive sensor.
The sensing distances we specified in our catalog were calculated using FE360 material. Many materials are more difficult to sense and require a shorter distance from the sensor tip to the object sensed.
If sensing a material that is difficult to sense, you may consider using our unique stainless steel sensing technology. This will measure virtually all materials at the specified distances.
Step 2:
How much space is available for mounting the sensor?
Have you ever tried using a round sensor or short body version, and not been able to make it fit? Our rectangular sensors can meet your needs. The same technology used in a standard round proximity sensor is enclosed in a rectangular housing. This technology includes sensing distances, electrical protection and switching frequencies similar to round sensors.
Step 3:
Is a shielded or unshielded sensor needed?
Shielded and unshielded sensors are also referred to as embeddable and non- embeddable. Unshielded sensors allow longer sensing distances but shielded sensors allow flush mounting.
Step 4:
Consider environmental placement concerns.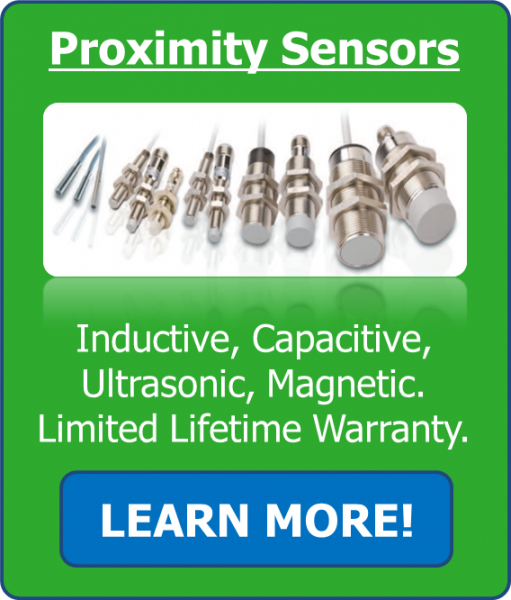
Will the sensor be placed underwater, in a high-temperature environment, continually splashed with oil, etc.? This will determine the type of sensor you may use. In the selection table and in the specification tables for each sensor family, we list the environmental protection degree ratings. Most of our sensors are rated IEC-IP67 and others are rated IP65 or IP68.
These ratings are defined as:
- IP65: Protection from live or moving parts, dust, and protection from water jets from any direction.
- IP67: Protection from live or moving parts, dust, and protection from immersion in water.
- IP68: Protection from live or moving parts, dust, and protection from submersion in water under pressure.
- IP69K: Protection against high-pressure/steam-jet cleaning.
Step 5:
What is the sensor output connected to?
Note: If using AC sensors, please skip this step.
The type of output required must be determined (i.e., NPN, PNP or analog). Most PLC products will accept any output. If connecting to a solid state relay, a PNP output is needed.
Step 6a:
Do I need 2, 3, or 4-wire discrete outputs?
This is somewhat determined by what the sensor will be connected to. Some simple guidelines to use are:
Step 6b:
Do I need analog outputs?
This is determined by the sensor application and what the sensor will be connected to. Sensors with analog outputs produce an output signal approximately proportional to the target’s distance from sensor.
If you only need to sense presence of an object, you do not need an analog output. Note that many discrete-output proximity sensors come with “adjustable” ranges, i.e. “adjustable from 20-80 mm”. This means only that you can set the target distance for presence detection within that range; it does not mean you are getting a variable outpu
Step 7:
Determine output connection type.
Do you want an axial cable factory attached to the sensor (pigtail) or a quick-disconnect cable?
There are many advantages to using a quick-disconnect cable, such as easier maintenance and replacement. All proximity sensors will fail in time and using a Q/D (quick-disconnect) cable allows for simple replacement. Factory attached axial cables come in a 2 meter length. CD08/CD12 Q/D cables come in 2 meter, 5 meter , and 7 meter lengths. Extension cables are available in 1 meter and 3 meter lengths to extend the length of the standard Q/D cables.
Q/D cables are offered in PVC and PUR jackets for meeting the requirements of all applications. Axial cables typically come with a PVC jacket. PVC is a general purpose insulation while PUR provides excellent oxidation, oil and ozone resistance. PUR is beneficial if the cable is exposed to oils or placed in direct sunlight.
There are also advantages to a factory attached axial cable:
- Cost: The cable is integrated into the sensor and included in the price. Q/D cables must be purchased separately.
- Environmental Impact: Since the cable is sealed into the sensor, there is less chance of oil, water or dust penetration into the sensor, which could cause failure.