Available in many combinations, filters and regulators are a must-have on any machine. Other devices to perform functions such as energy isolation, lockout tagout and lubrication should also be considered.
Chip McDaniel, technical marketer for AutomationDirect, wrote an article for the January 2019 issue of Design World magazine, titled Proper Air Preparation for Automated Machines. Here’s a summary, please click on the link above for the full text.
The process of filtering, regulating and lubricating compressed air is known as air preparation, or air prep, and McDaniel explains its importance.
Manufacturing plants include air prep at centralized compressors, and additional air prep is beneficial at each machine’s point- of-use. The air prep system—often referred to as the FRL after the filter, regulator and lubricator that is often included in the assembly—is the breathing mask on a machine, its personal protection equipment.
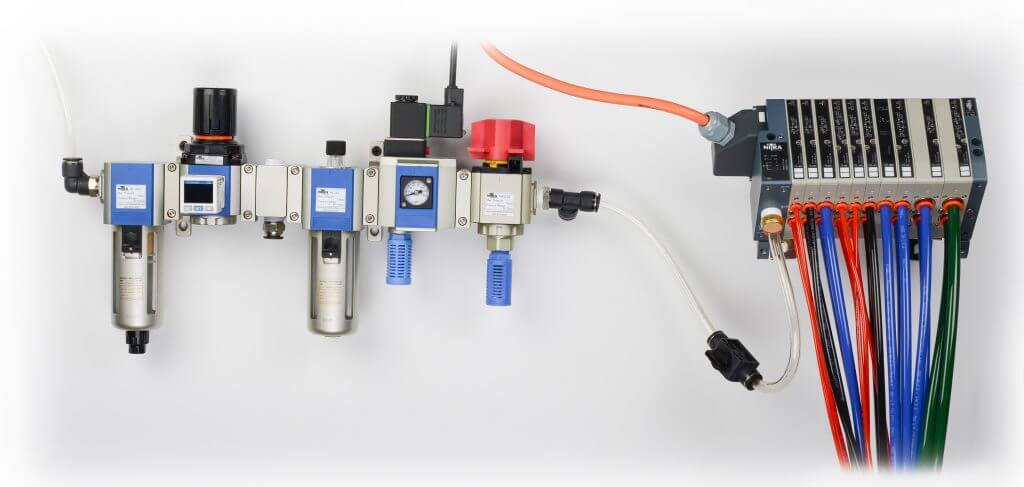
This air prep unit from AutomationDirect has many NITRA pneumatic components including filter, regulator with digital pressure switch, distribution block, lubricator, soft start/dump valve and manual shut off connected to a modular valve manifold.
Operating Pressures
Air prep systems are typically assembled inline and come in a variety of port or body sizes. Most air prep systems fall in the range of 1/8-inch to 1-inch NPT female port sizes, with some exceptions. These systems are often modular in design, so when specifying an air prep system, McDaniel says it’s important to match like-size devices for ease of assembly and use of accessories.
Generally, the pressure range of each pneumatic device is 20 to 130 psi to match up with the common supply air pressure in a manufacturing facility, which is between these values. While a lockout valve may have a pressure range of 0 to 150 psi, other air prep devices such as filters, regulators and soft-start/dump valves require a minimum operating pressure to activate internal pilot and drain valves. The minimum operating pressure may be as low as 15 psi and as high as 35 psi, depending on the device.
Manual Shut-Off Relief Valves
Crushing, pinching, cutting, amputation and other injuries due to unexpected or automated machine motion often occur due to an employee’s failure to safely disable and isolate energy sources, and lockout/tagout the machine before performing service or maintenance work. Because of the possibility of injury, OSHA and ANSI have important regulations regarding lockout/tagout control of hazardous energy and prevention of unexpected startup.
McDaniel says the manual shut-off relief valve or a pneumatic isolation lockout valve provides removal of motion-causing pneumatic energy, along with a means to lock the valve in the off position as part of a lockout/tagout procedure.
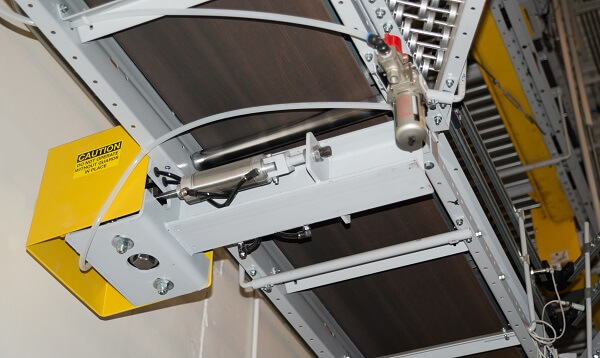
It shuts off upstream air pressure and relieves downstream air pressure to an entire machine or zone. Its oversized exhaust ports provide a quick pressure release, which can be very loud, so suitable silencers (mufflers) should be used, especially if ear protection is not required in the area.
It’s important to note that, even though the shut-off valve relieves air pressure, trapped air (energy) may still be present downstream from the air prep unit.
Pneumatic Air Filters
Filters are a critical part of an air prep system for removing both particulates and moisture. These filters use either a centrifugal or a coalescing design. The centrifugal types remove particulates and some moisture, while the coalescing types remove more water and also oil vapor. A dryer/refrigerator unit may be required to remove larger amounts of moisture, and it should be installed just downstream of a plant air compressor.
Regulators for Air Preparation
A regulator is often “set and forget” when used to supply compressed air at a consistent pressure to a machine, with a typical adjustable pressure range from 20 – 130 psi.
McDaniel cautions that because supply of air at constant pressure is critical to machine operation, a regulator with a locking pressure adjustment knob is required, along with other key components.
An integral pressure gauge should also be included to help quickly identify actual air pressure. Another useful device is an adjustable pressure switch mounted downstream of the pressure adjustment device and monitored by the machine controller.
A combination filter/regulator includes all the features of a standalone filter and regulator in a single, space-saving device.
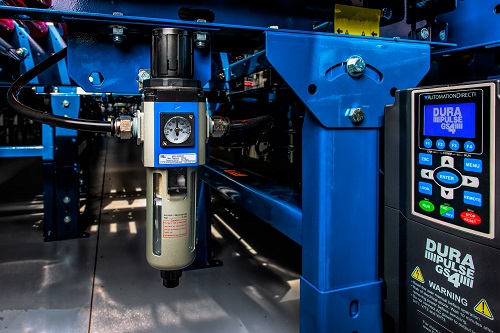
Total air prep (TAP) systems are available as an alternative to specifying each air prep component separately, and then assembling these components on site. These all-in-one systems include the filter, regulator, shut off/dump valve, soft start, electric shut off, pressure switch and indicator. A TAP is about half the size, weight and cost of an air prep system assembled from separately purchased components.
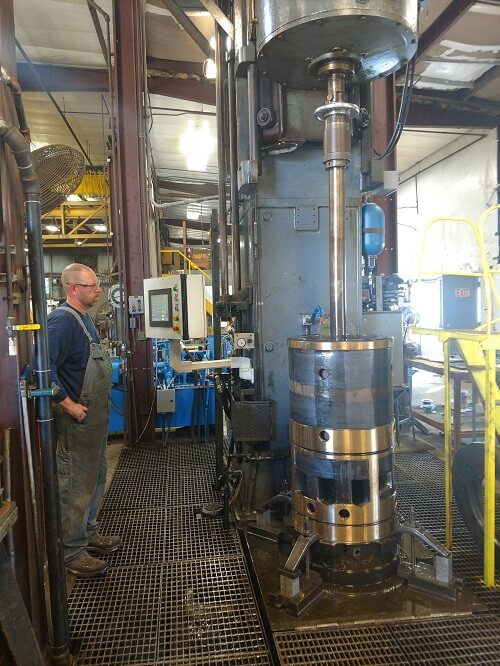
Total air prep systems are available from AutomationDirect and other suppliers, are about half the size, weight and cost of systems assembled from separately purchased components
With a better understanding of pneumatic air prep components and their use, both machines and operators can be protected, McDaniel says.
To summarize, a manual shut-off relieve valve and soft start/dump valve is required to control, isolate and remove compressed air from the machine or system. As the air flows to the system, a filter, regulator and lubricator are used to prep it for use.
To read more pneumatic articles, click here.