Industrial automation products are useful for much more than traditional applications, as PLCs and HMIs can be used in all sorts of unique commercial markets.
Byline: Mark McHenry, Systems & Controls
Other than being large and generally rectangular-shaped, a modern custom bus—the type frequented by touring music stars, mobile multi-millionaires, and campaigning politicians—bears little resemblance to the utilitarian school buses many remember. Sometimes called luxury coaches, motorcoaches, motorhomes, or recreational vehicles (RVs), these conveyances are bespoke creations built-to-order.
Their interiors are typically appointed with premium materials and carefully thought-out design features. This extends to the electrical and electronic systems, where LED lighting and digital controls and displays provide efficient and sophisticated functionality. But because they build far fewer units than a massive auto manufacturer, these custom coachbuilders have a problem. They have less of an opportunity to benefit from economies of scale, so many of the digital components they use must be specially developed for changing and unique applications.
The industrial automation sector already faces challenges like this, and designers and systems integrators (SIs) address these needs by applying commercial off-the-shelf (COTS) digital control products to make them suitable for the demanding applications. Mark McHenry founded Systems & Controls (S&C) in Lenoir City, TN in 1999 to service industrial customers, but over the years he has found success leveraging his company’s SI skillset to support the custom coachbuilder industry.
A Concrete Beginning
Working with scales, loadcells, flowmeters, and associated equipment was an early specialty of S&C. The company rapidly expanded their capabilities to include custom automated storage, transfer, filling, batching, and blending systems for dry and wet materials. A typical client would be a concrete batching plant, where various raw materials were scaled and metered according to a recipe to make the desired product.
One of the most effective ways to automate industrial systems like this is to use COTS digital devices, such as human-machine interfaces (HMIs) and programmable logic controllers (PLCs), to monitor and operate field-located sensors, along with other equipment, such as valves and motors. S&C refined the control logic and best visualization practices for automating systems using proven HMI and PLC devices (Figure 1).
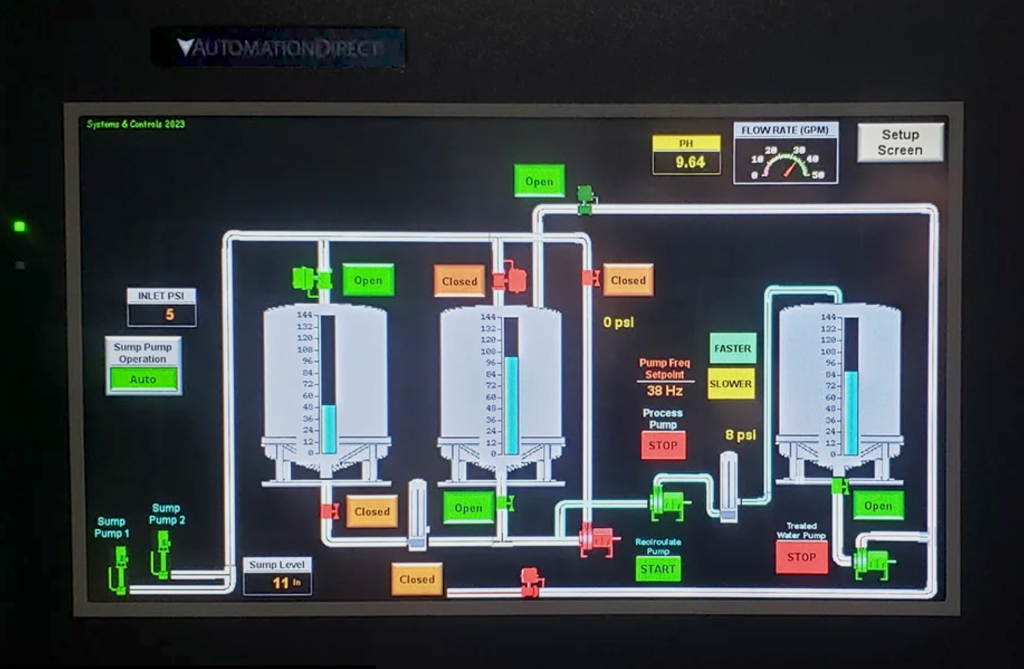
Of course, PLCs and HMIs can be used to automate almost anything. When S&C’s owner heard about an opportunity to work with a custom coachbuilder, he knew they had the right product knowledge and skillset to help.
Opening the Door to New Markets
Custom coachbuilders are typically strongest at selecting a chassis, and then outfitting the rig with the hardware and components to create a personalized product for their clients. There are some integration technology suppliers offering smart switches and touchscreen devices suitable for use on board RVs, boats, and similar mobile transportation. However, these are mostly suitable for remotely viewing some status points, or for allowing users to remotely turn things on and off, with limited automation functions.
One coachbuilder engaged S&C to help with controlling an automatic motor-drive sliding pocket door. For the chosen mechanism, they needed a way to carefully control a small three-phase motor which transmitted motion using a cogged belt to open and close the door based on user button presses. The door would need to operate quietly, and smoothly run into each stop as it reached fully opened or closed. Most importantly, it would need to detect any blockage while moving, such as a person, pet, other obstacle. If obstructed while closing, the door needed to stop and then reverse; if somehow obstructed while opening, the door needed to stop until another command was received. In addition, it is possible to move the door by hand if a failure occurs.
Most vehicle systems operate at 12VDC. However, large custom coaches typically incorporate a full-time 120VAC distribution system—supporting multiple air conditioners, appliances, and other large loads—using an on-board generator or plug-in connection to “shore power,” depending on whether the vehicle is moving or parked. Three-phase power is typically not available, but S&C solved this issue by using an AutomationDirect DURApulse GS20 variable frequency drive (VFD), which has the capability to accept common single-phase 120VAC and output three-phase 240VAC. An AutomationDirect CLICK stackable micro brick PLC, and other compact components such as a Rhino power supply, ensured that S&C could create a design suitable for installation in the limited on-board space (Figure 2).
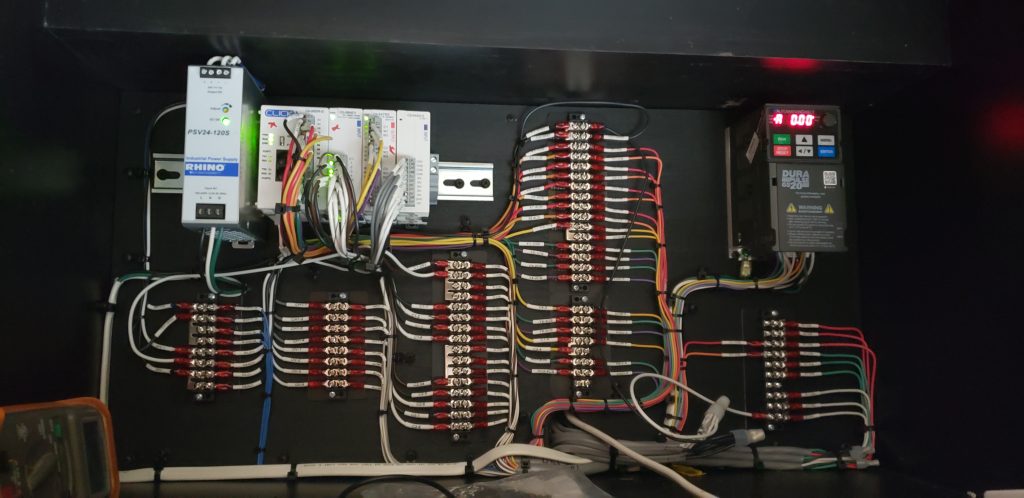
The design took a bit of iteration, and S&C along with one of the coach builders made a test jig so they could prove out the function in the convenience of their shop. The first idea was to run the VFD on a time basis, but this was not very accurate and resulted in the door bumping into each end-of-travel, and sometimes slipping the belt. However, by incorporating limit switches and monitoring the current draw, they could provide fine control of the door movement and stop it immediately as it snugged into each end point. Current monitoring was also essential as a safety function because any blockage due to a person, pet, or other item in the way of the door would be detected as the motor was forced to work a little harder, and movement would be commanded to stop.
Initially, the design was for operating just one pocket door. Since that time, adding additional I/O to the PLC has allowed it to control up to 4 pocket doors per installation. Just one PLC program was created to control up to 4 doors, and unused inputs are ignored if there are fewer. One issue discovered was that multiple switch activations or pressing open/close buttons while door was moving could cause unintended operation, so the PLC was programmed to ignore switch activations in a way to prevent this problem.
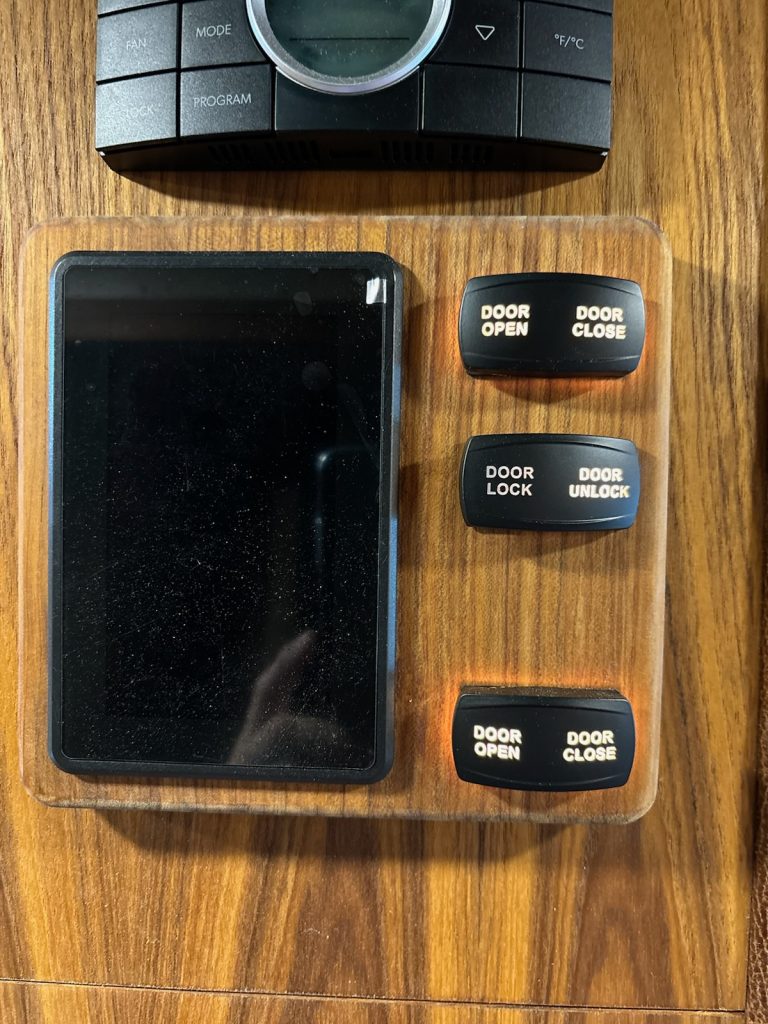
Interfacing with On-Board Systems
The PLC was easily interfaced with the coach’s smart switch system or discrete switches so users could interact with the door using the interface available to them for all other on-board functions (Figure 3).
Using a PLC in this type of application is also beneficial because the input/output (I/O) module count is easily expandable, and there is plenty of programming memory available, so that one PLC can control multiple things. Another custom coach application is coordinating air conditioners. Some coaches have up to five 120VAC air conditioners. If more than one happens to start at the same moment, there is the potential of tripping a circuit breaker. To avoid this, S&C has configured a PLC to monitor the air conditioner run command from each thermostat, and it then performs logic to stagger the starting of each unit and prevent an overcurrent trip.
Automation is for More Than Just Industry
Industrial automation products are widely used for all types of machinery, equipment, and manufacturing processes, but they also provide an ideal way to monitor and operate almost any type of system. S&C has recognized this, and it has expanded their client base over the years to perform many types of projects over and above their typical core work.
Part of the S&C success story is attributable to the selection of the right automation supplier. Key characteristics needed to facilitate the work of an SI are an extremely wide range of products, a favorable price performance ratio, and support by a comprehensive ordering and documentation website. Free software, online/phone support, and training/example videos make it easy for users to learn and work with the products. S&C is sticking with their preferred supplier based on all these reasons, and because they have a large installed base of reliable installations.
All figures courtesy of Systems & Controls
Author Bio
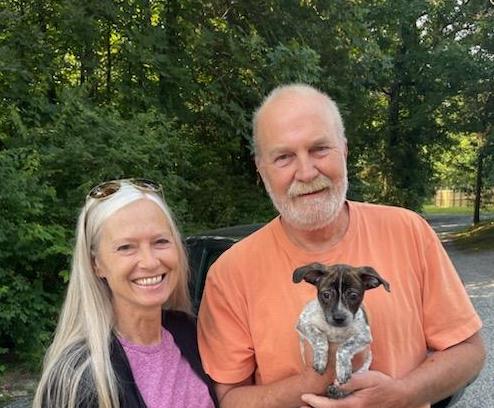
Mark McHenry graduated Tennessee Institute of Electronics with an Associate degree in electronic technology in 1980. After working for almost 19 years in the electronics industry as a technician, he started Systems & Controls in 1999 and he will be celebrating 25 years in business this fall. With almost 70 years combined experience, Mark and his team at Systems & Controls enjoys the challenges of one off and custom system integration.