The Grand Garnisher has been turning heads as it tours the United States and Europe. AutomationDirect hardware and software automation underpins the attractive, steampunk contraption.
By Stuart Ostroff, Salmon Studios
Picture this: you are in the back garden of the grand duke’s estate, enjoying social hour with great company, a botanical cocktail in your hand. You think, “the only element that could make this better would be a garnish for my drink.” As if reading your mind, a retro-futuristic truck and crew—seemingly out of a sci-fi magazine—come to life from a billow of steam, drawing gin-enthusiasts with their promise of the perfect cucumber garnish.
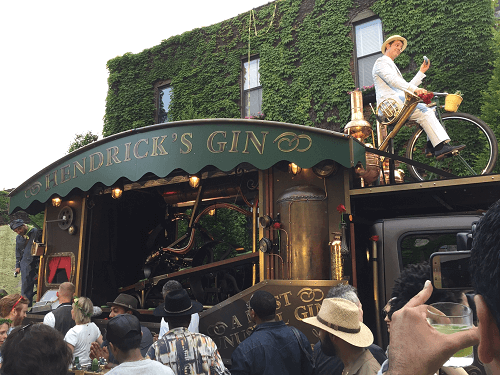
Hendrick’s christened this machine the “Grand Garnisher”. It has toured the U.S. coast-to-coast twice and more recently completed a circuit in Europe, delivering wondrous cucumber garnishes and leaving awestruck patrons in its wake. Although at first glance it may appear the contraption is driven by a steam generator, the sensation is made possible by a lineup of AutomationDirect automation equipment in the back.
A Most Unusual Garnisher
Hendrick’s Gin—distilled in Scotland—is known for its rose, cucumber, floral, and botanical flavor notes. The marketing group contracted Salmon Studios in Florence, MA to develop a functional and aesthetically-pleasing garnishing apparatus to set on a 20-foot, flatbed truck. Keeping with the steampunk theme reminiscent of Hendrick’s marketing, all visible wiring and electrical devices would be hidden away behind the retro aesthetic of steam-powered machinery.
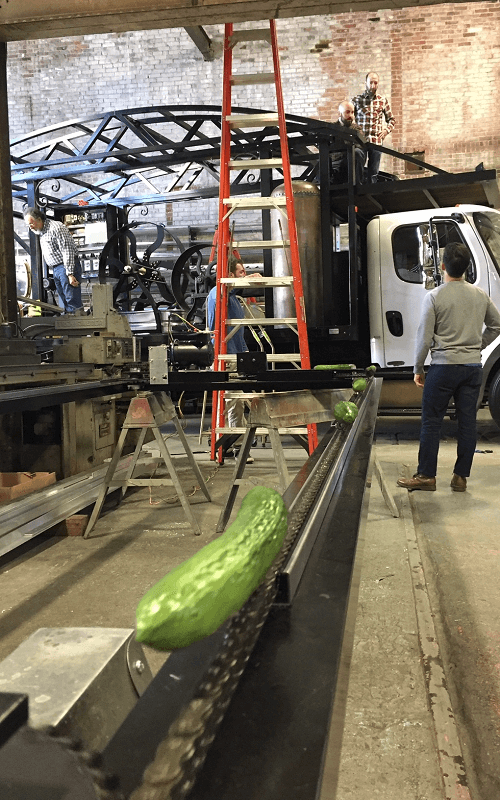
The flatbed-mounted visuals include six motorized parts:
- a steam engine with dual flywheels, driven by a hidden gearmotor
- two separate chain conveyors whisking artificial cucumbers around the bed
- a rotating cucumber slicer
- a reciprocating mechanical arm to control the slice frequency
- a product discharge conveyor to where patrons can hold out their drinks to receive the garnish
Atop the truck cab on a whimsical penny-farthing bicycle, a cyclist in period attire controls the system operating speed based on the rate of pedaling.
The Magic Behind the Curtain
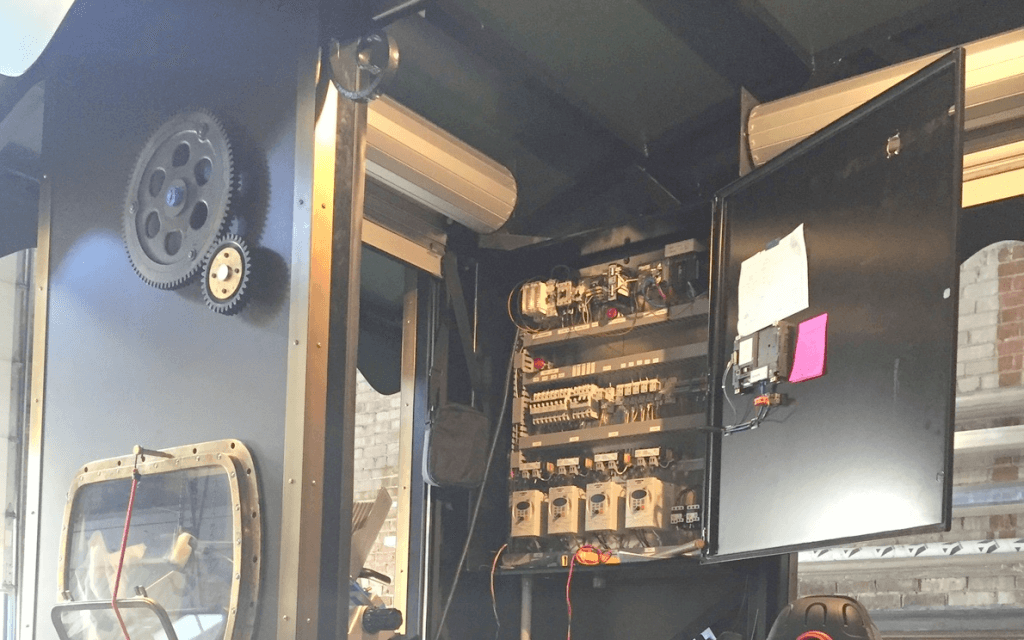
Though it is conceivable to create a purely mechanical steam-powered machine such as this, it would be incredibly impractical—the year is 2020, not 1820. If we pull back the literal curtain concealing the equipment making this spectacle possible, we find a complete electrical automation system driven and controlled by AutomationDirect components.
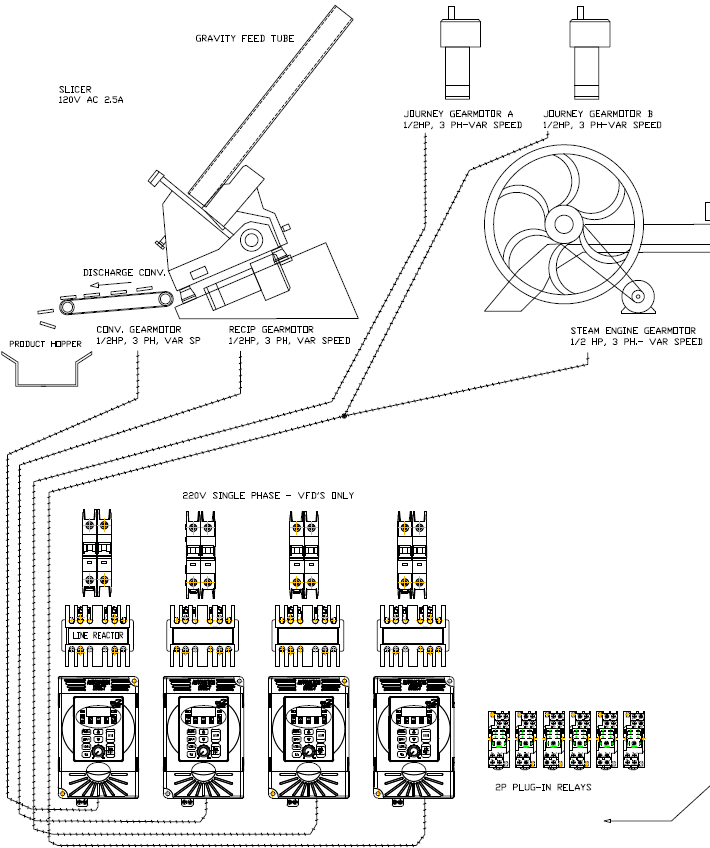
The conveyors, steam generator, and reciprocator half-horsepower gearmotors are driven by four AutomationDirect GS2 230VAC VFDs with single-phase input and three-phase output. The VFD frequency is controlled by 0-10 volt analog outputs (AOs) from the AutomationDirect Do-more PLC rack. Each VFD’s speed can be independently set in “manual mode” by entry on the AutomationDirect C-More 8-inch touchscreen HMI, or the system can be placed in “pedal mode”, in which the AOs are synchronized to a speed determined by the bicycle pedal rate.
A proximity sensor is mounted on the front wheel of the penny-farthing, which sends a digital input signal to the PLC with each wheel revolution. Pedal rate is calculated by a PLC-programmed timing circuit, which is scaled and transmitted to the VFDs via the AO voltages.
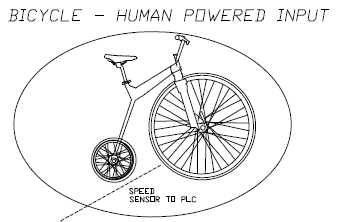
For cucumber slicing, technicians removed the meat tray from a commercial meat slicer, replacing it with two vertical, plexiglass tubes through which cucumbers are manually loaded by an operator for gravity feed. As the 120-volt continuously-rotating slicer operates, the VFD-driven reciprocator mechanical arm drives the slicing carriage back-and-forth. Each stroke produces two, thin cucumber slices, dropping onto the product conveyor for delivery to the eager consumer. Unused slices fall into a stainless-steel bar container to later be used for garnishing if desired.
To power the system, a 230VAC feed is supplied by an onboard diesel generator or by external “shore” connection—the engineering team created provisions for using both U.S. and European utility industrial standards. Initially concerned with generator-induced current or voltage fluctuations causing VFD damage, the team worked with support staff at AutomationDirect to specify line reactors installed on the incoming side of the VFDs for protection.
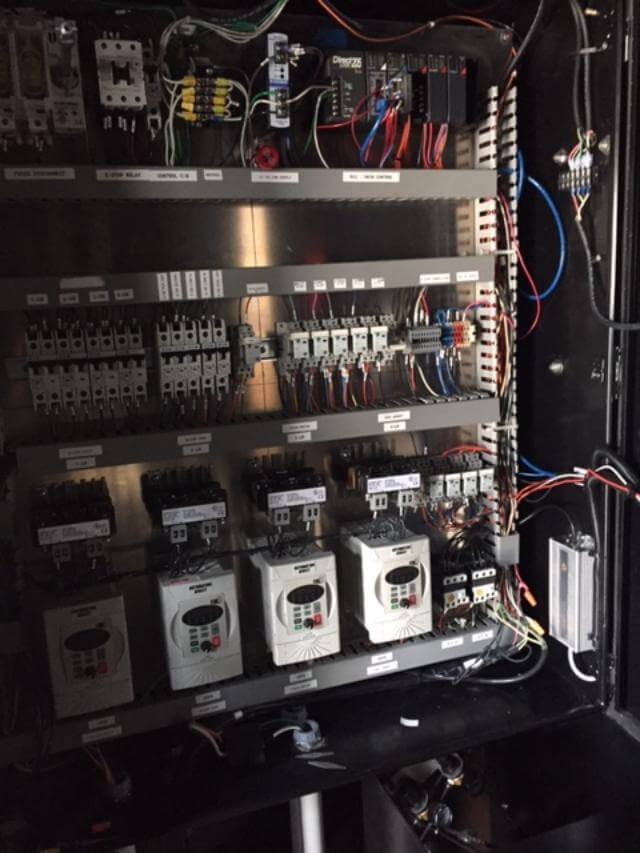
With further assistance from AutomationDirect, the engineering team generated an automation system bill of materials calling for parts exclusively sourced by AutomationDirect: PLC, HMI, VFDs, motors, transformer, power supply, line reactors, relays, circuit breakers, terminal blocks, wiring and cables, and other panel components. During the Garnisher’s three seasonal tours, there has not been a single automated equipment incident or failure.
Retro Garnisher, Modern Automation
Back in the grand duke’s garden, you line up with your friends to receive the perfect, fresh garnish for your cocktail, marveling at the creativity that automation makes possible. Using AutomationDirect hardware and software, the engineering team at Salmon Studios creatively animated what has become a staple image of Hendrick’s Gin.
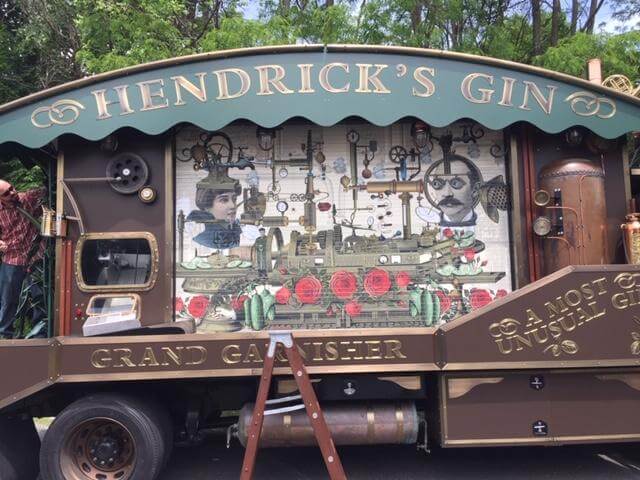
From the project outset, the engineering group has been pleased with the simplicity of selecting, acquiring, installing, and programming the automation system components. Following three successful tours, the question is now, “what will we build next?” The Grand Garnisher is an inspiring piece, showcasing excellence in practical function and an extravagant aesthetic.
Figures, all courtesy of AutomationDirect, Salmon Studios, and Hendrick’s Gin.
Want to Learn More?
If you’re interested in learning more about The Grand Garnisher check out this feature from Food & Wine Magazine titled, A Giant Cucumber Slicer is Crossing the U.S. to Help Improve Your Cocktails or check out this YouTube video!
Author Bio
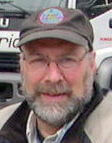
Stuart Ostroff is a machine designer, builder, and installer. With nearly 50 years of industrial application experience, he has successfully completed projects in mechanized machining, automated assembly, paper converting, industrial baking, and cryogenic tank fabrication. He has employed PLC automation technology since its advent in the early 1980s. Once AutomationDirect products became available, he has depended on these almost exclusively due to their excellent quality, remarkable technical and sales support, and unbeatable prices.