Generators efficiently convert low-grade waste heat from diesel generators into power.
Joe Thibedeau, a control systems engineer with ElectraTherm, wrote an article for the November 2019 issue of Power titled Innovative Technology Captures Energy from Waste Heat. Here’s a summary, click on the link above for the full text.
Dutch Harbor power plant in the remote Aleutian Islands of Alaska operates several diesel gensets to generate electrical power. Electrical rates there are some of the highest in North America, about four times greater than the U.S. national average of $0.12/kWh.
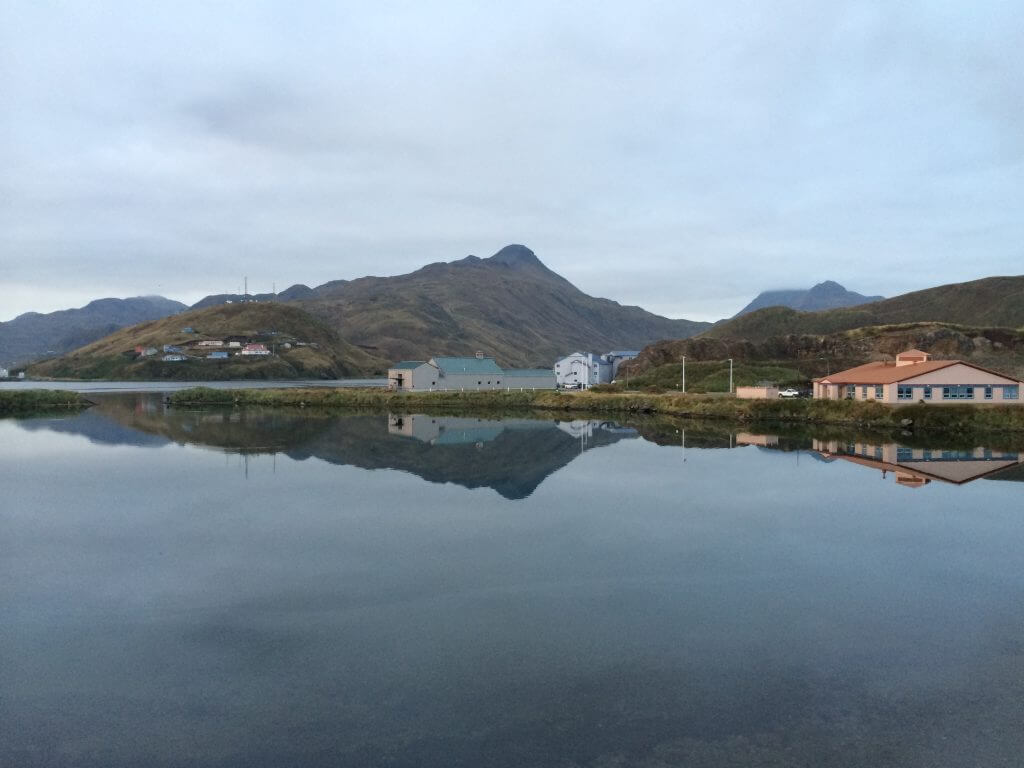
To take advantage of the previously untapped genset waste heat, the City of Unalaska and the Alaska Energy Authority purchased three organic Rankine cycle (ORC) generators in 2014. These generators capture waste heat at temperatures as low as 170F, and in conjunction with a 45F seawater cooling loop, the three units contribute approximately 75 kW of gross power.
The ElectraTherm POWER+ GENERATOR systems are controlled by an AutomationDirect programmable logic controller (PLC), and use an AutomationDirect human-machine interface (HMI) for operators to view and adjust operation.
A Warm, Green History
Typical stationary generators using diesel or natural gas reciprocating engines only convert about 33% of the fuel energy to electrical power, with the remaining energy lost as waste heat. Recovering and converting the waste heat into electricity increases overall plant efficiency. In the past, there were few options to do this commercially.
Today, ElectraTherm has deployed more than 70 POWER+ GENERATOR systems worldwide. Their design and associated proprietary technologies reliably turn waste heat into power.
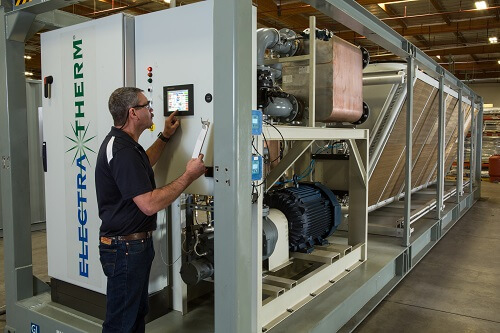
The ORC Process
Because engine waste heat is too low to drive a steam engine, ElectraTherm uses ORC technology, a process similar to that used in a steam engine.
The primary difference with ORC technology is that the water used in a steam engine is replaced by a fluid with a much lower boiling point. The ORC process is like a refrigerator running in reverse, where heat flow is used to generate power.
Replacing water and steam with alternative low-boiling-point fluids allows a modified version of the traditional Rankine cycle to efficiently convert the waste heat to power.
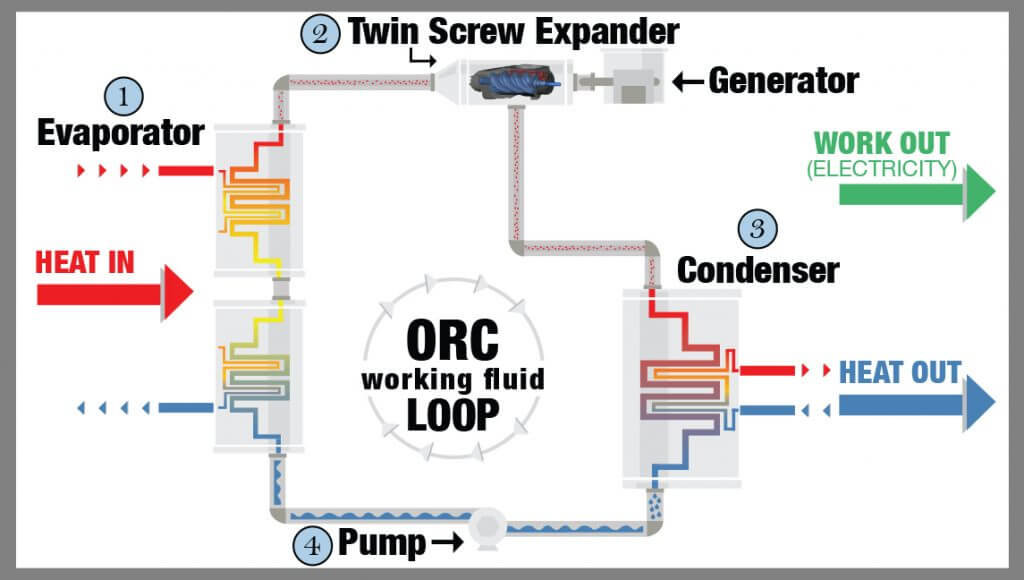
Twin Screws Provide Multiple Benefits
Instead of radial or axial turbine technologies, ElectraTherm uses a twin-screw expander in its heat-to-power generating system. The advantages include lower working speeds, and a simple and compact design not requiring a gear box or oil pump. Besides the mechanical advantages, these features simplify the required automation.
Automating the System
The POWER+ GENERATOR is designed to run automatically with minimal end user oversight or supervision required. Once started, the proportional-integral-derivative (PID) function in the PLC maintains system power output at the setpoint.
The PLC was selected for its expandability, PID control functions, and ease of use. Another reason for selecting AutomationDirect components was the support of its value-added reseller Quantum Automation. The company provided assistance with the initial design and support throughout the process of integrating a new automation system into the Power+ Generators.
The PLC controls the working-fluid feed pump, safety valves, and various other subsystems and field-connected devices. Temperature, pressure, and power transmitters are monitored by the PLC and used for control, and the PLC’s PID loop control features auto-tuning to quickly provide near-optimum loop settings.
The HMI was selected based on ease of use, availability of data logging, upload features, and low cost. In addition to graphical display functions, it provides alarming, remote accessibility, logic, math, and support of numerous communication protocols. Machine status can be viewed locally or remotely.
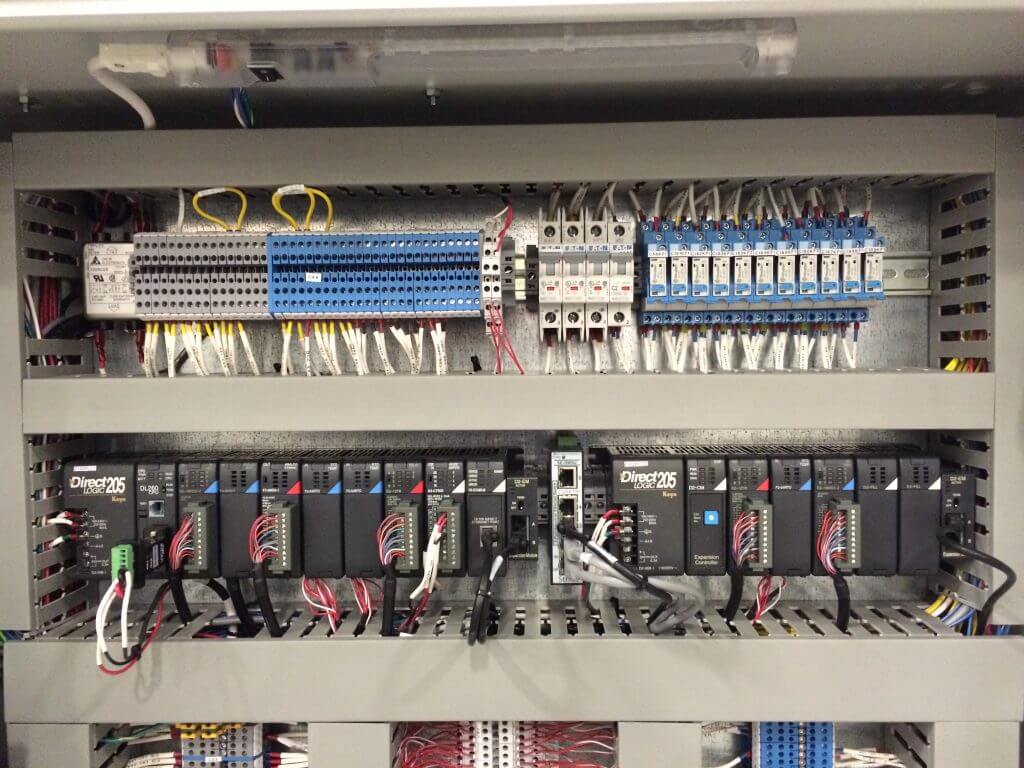
Improved Efficiency
By using POWER+ GENERATOR systems to convert waste heat to power, the Alaska Energy Authority estimates it is realizing about $100,000 in annual energy savings. In addition to the benefit of generated electricity, the systems reduce generator engine cooling loads and increase efficiency. AutomationDirect PLC and HMI controls are critical for reliable system operation.
Check out the AutomationDirect.com website today to explore products that can help your company control its own automation destiny.
Read more articles related to programmable logic controllers.