Here are some of the typical continuous/analog level measurement methods, with a summary of their strengths and weaknesses:
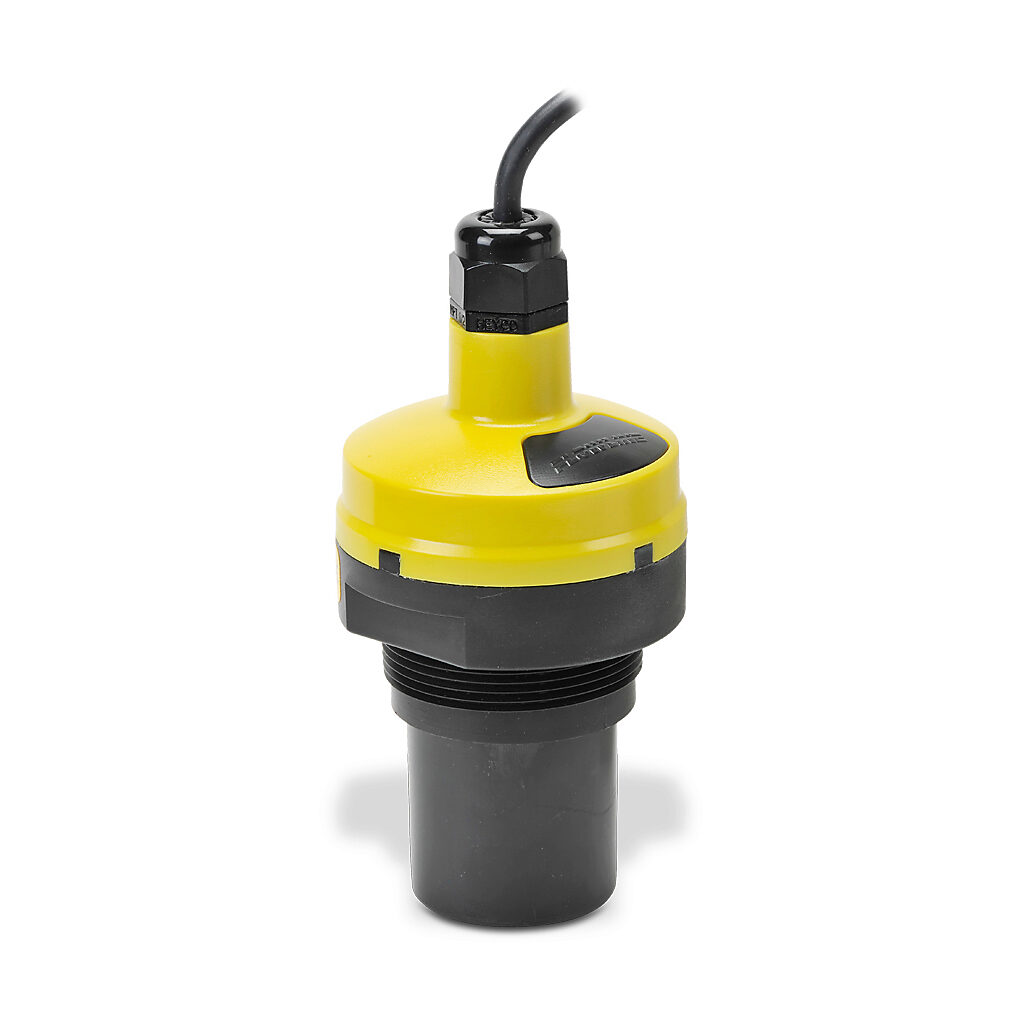
Ultrasonic level sensors: These are generally installed at the top of a vessel looking down into the product. They generate a periodic ultrasonic sound impulse and measure the echo’s return time to determine the distance to the material surface, with enough accuracy for many applications.
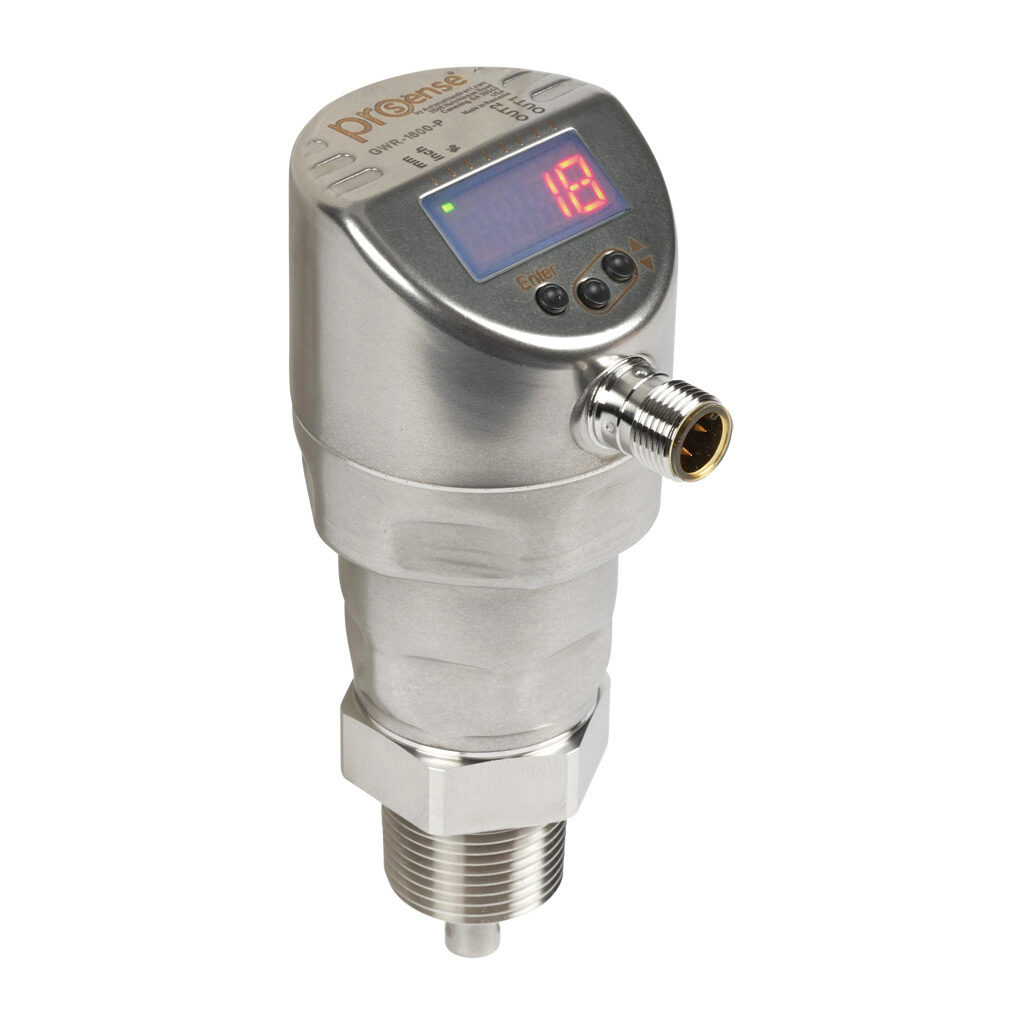
Radar level sensors: These work similarly to ultrasonics but use radar pulses for higher accuracy and reliability. Guided wave sensors transmit pulses down a metal probe or wire which extends into the material, while pulsed radar is non-contact and relies on open-air pulses. Frequency modulated continuous wave (FMCW) uses continuous transmission of varying frequencies, so it is unaffected by most media, process, or environmental factors.
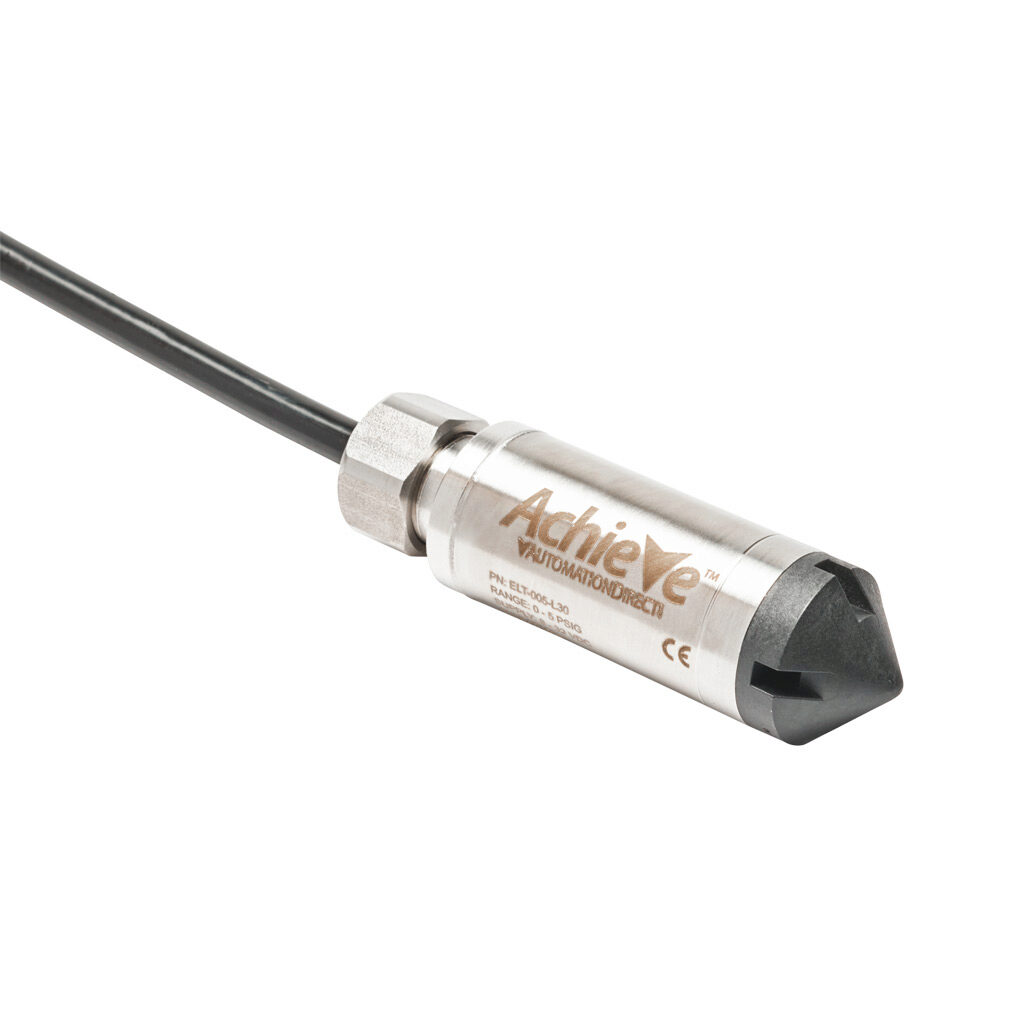
Submersible level sensors: These are inserted into a vessel or well, down to the lowest point of measurement, and work by detecting the pressure exerted on them by gravity acting on the liquid above them. They are simple and low cost, and work well in certain applications.
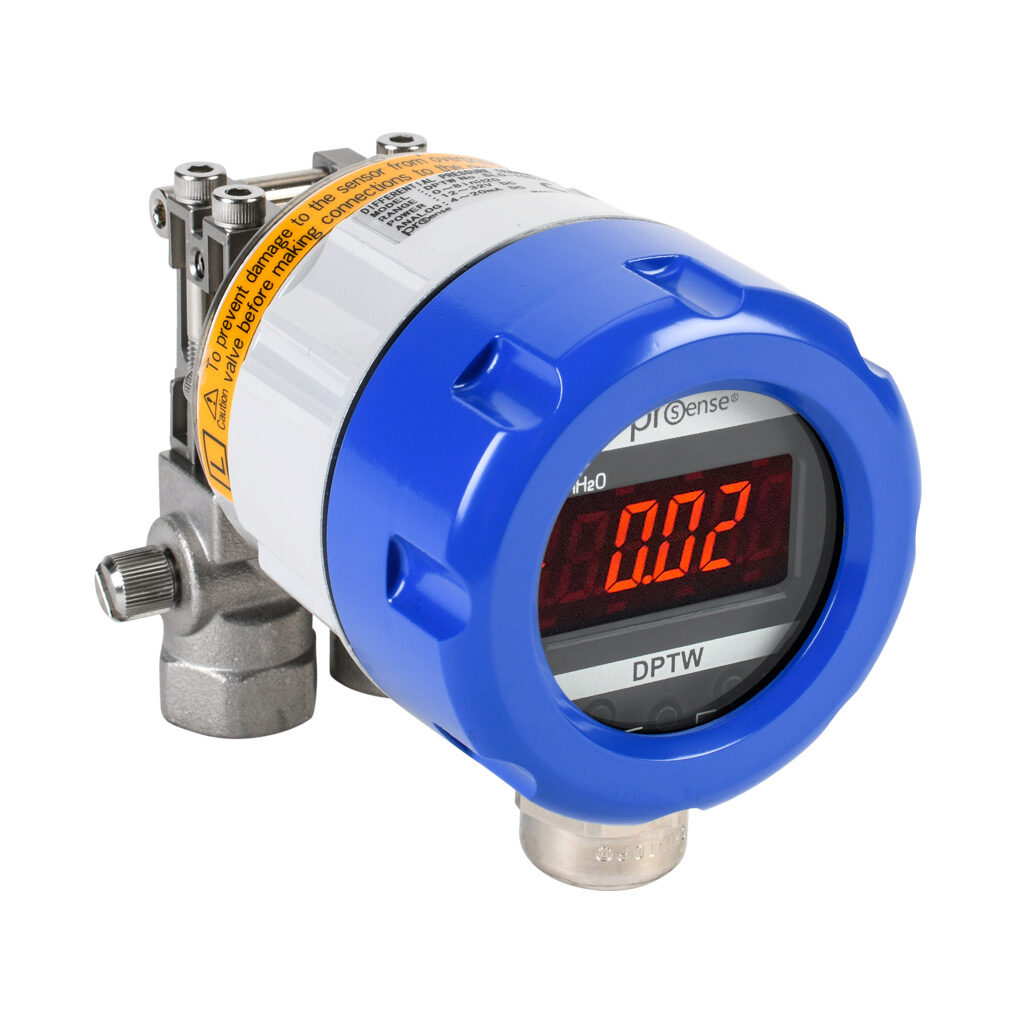
Differential pressure level transmitters: These also measure level using pressure, but they are installed outside a vessel and connected at just the bottom (for atmospheric applications), or the bottom and top (for pressure/vacuum applications) using tubing taps. Alternatively, a small amount of air can be “bubbled” in the bottom of the vessel and the transmitter can measure the backpressure change as the liquid level varies.
Again, there are other possible level measurement technologies, such as putting a tank on load cells to detect its varying weight, using a laser distance device to detect the moving product or a target, and others. However, the preceding technologies cover a large majority of typical industrial applications, and all are commonly used.
Level measurement technologies require loop power or a maybe a separate power source—usually in the 10 to 30VDC range—and a degree of configuration. Some of them can be configured using buttons right on the instrument, while others require a configuration tool, PC software, or a mobile app for adjusting various settings and calibration. The latest version of these devices may use HART over 4-20mA, EtherNet/IP, IO-Link, Bluetooth wireless, or other digital communications or fieldbus technologies to enable easy remote configuration, along with transmission of a multitude of process data and diagnostics information. These devices are therefore more complex and require more attention, but this is a consequence of using better technologies to deliver more performance.
Some technologies are favored by certain industries and applications for continuous/analog level measurement. Ultrasonic sensors are cost-effective for many types of atmospheric applications. Submersible level sensors work well in water/wastewater applications and wells. Radar level sensors provide better performance and accuracy than other technologies, and differential pressure level transmitters are common for enclosed/pressurized applications.
Check out the other two blogs in this series: