Here are some of the typical discrete level detection methods, with a summary of their strengths and weaknesses:
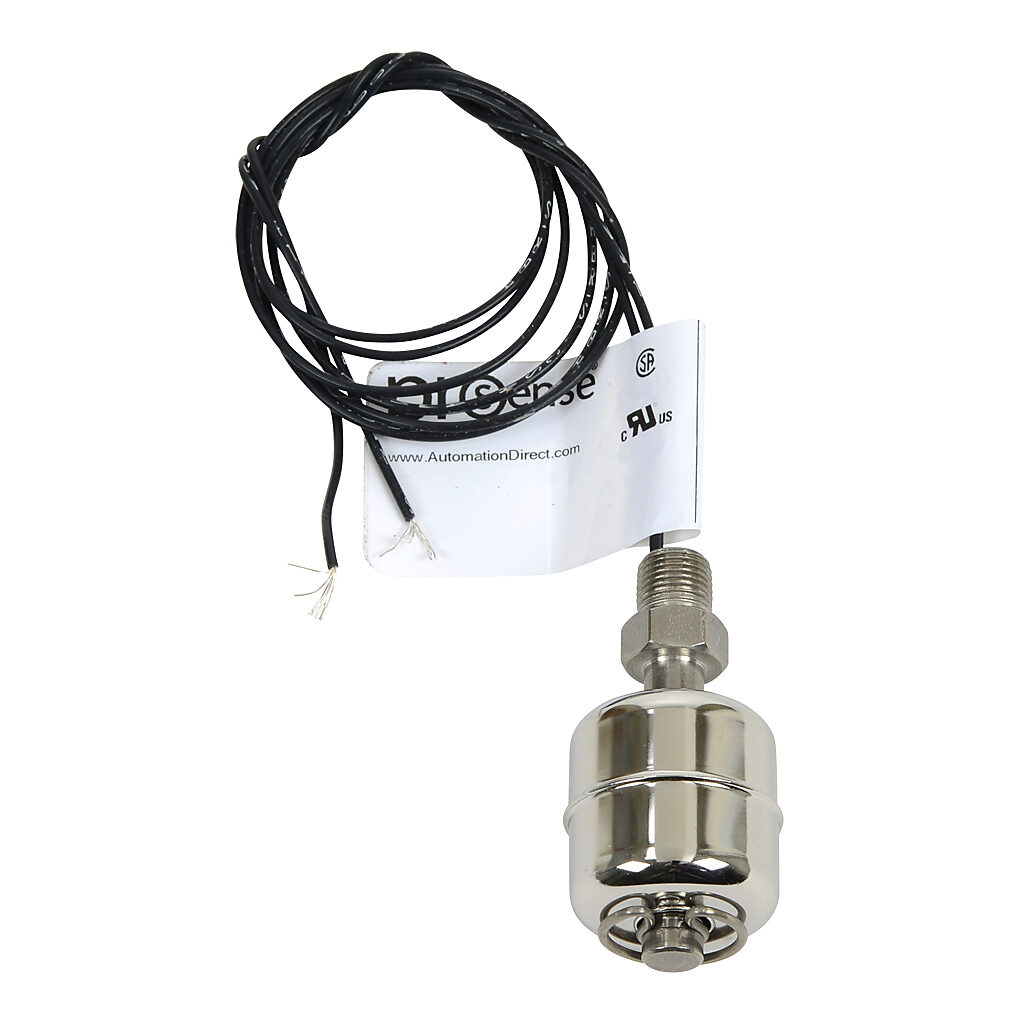
Float level switches : These simple devices provide an on or off signal as a liquid moves up or down. Some travel along a guide rod, while others just bob up or down on a cable, and either may use mechanical or electronic switching methods. They can be made with plastic or stainless-steel materials to resist various liquids, and they are inexpensive. However, they are susceptible to wear and damage.
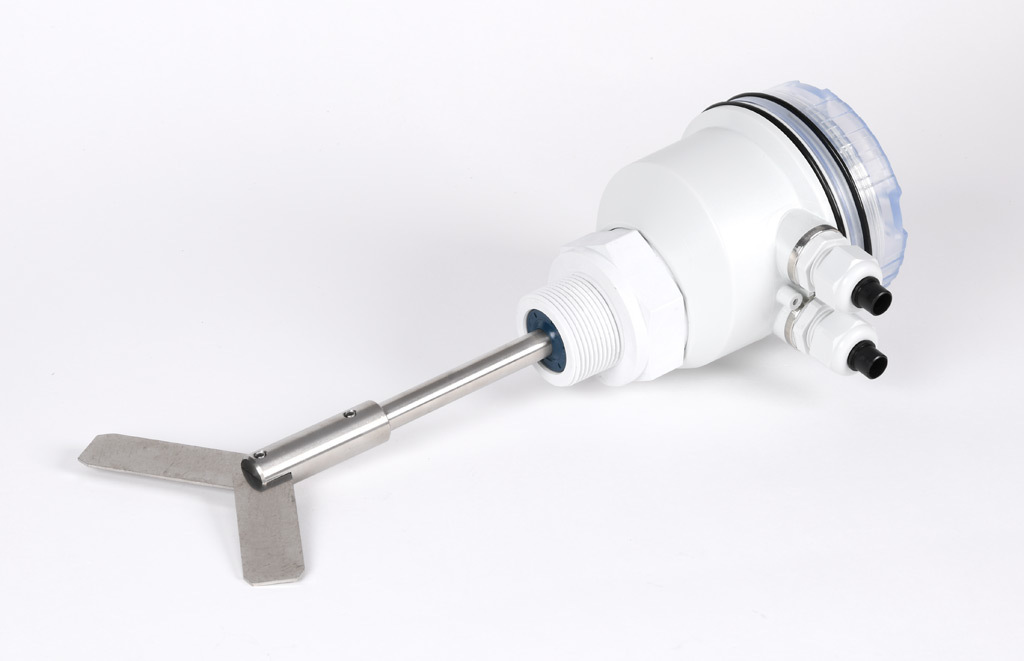
Rotating paddle level switches: These function similarly to floats, but are designed for immersion in solid pellet, granular, or powder materials for providing an on or off signal for material presence, depending on if the motorized paddle is free or stopped. They are rugged and some models can be used in hazardous locations common with dusty environments.
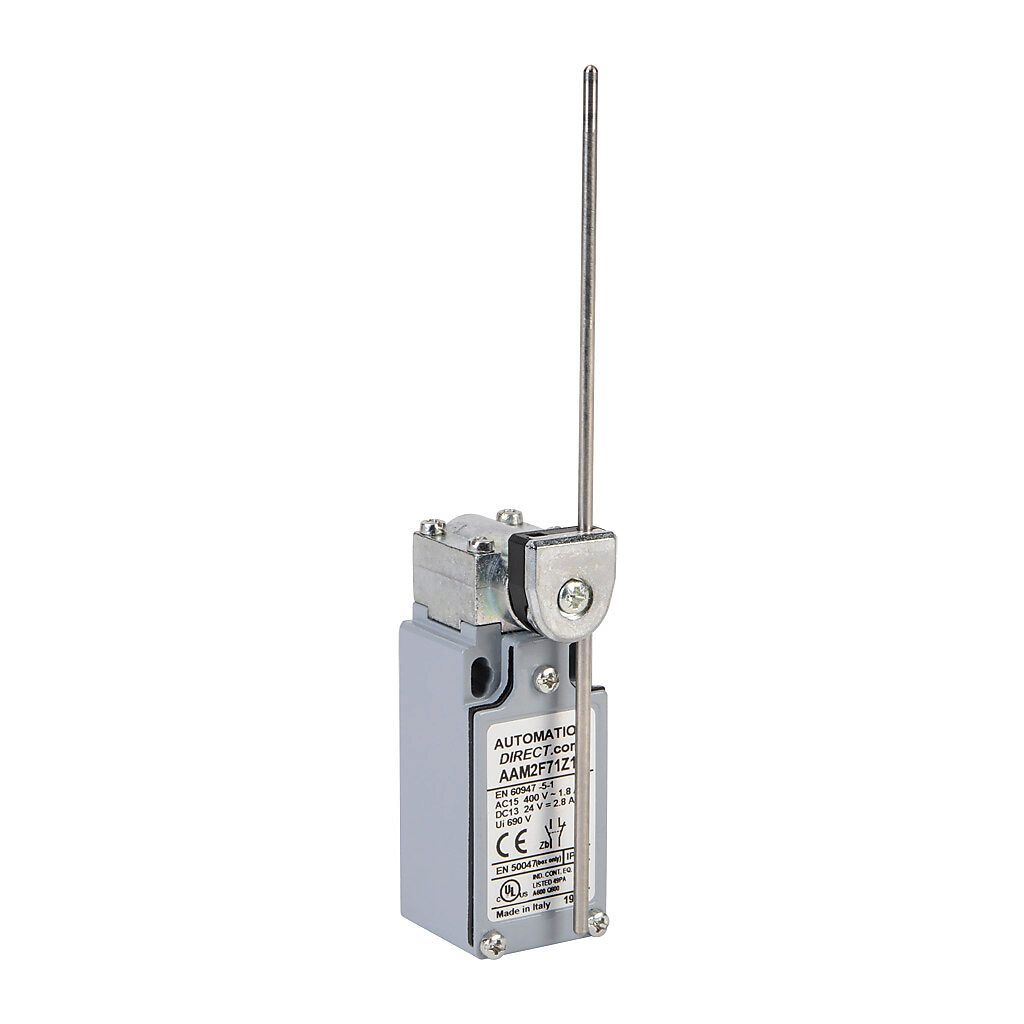
Mechanical limit switches: In some cases, such as for small metal parts in a hopper, it may be possible to detect a high level using a mechanical rotary-type limit switch with a rod or whisker on the actuator. While simple, this arrangement is susceptible to damage and can indicate improperly if buried by product.
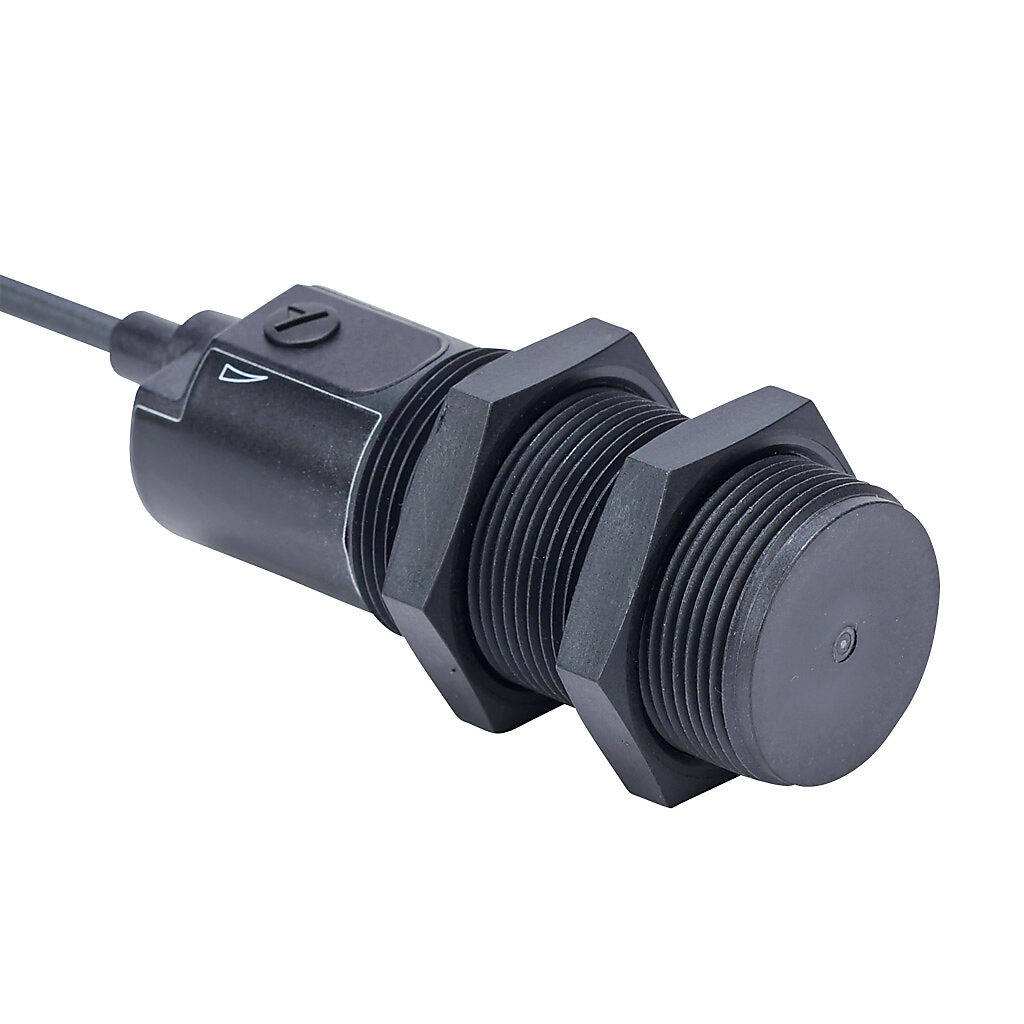
Proximity and photoelectric sensors: Proximity sensors can be installed directly in the sidewall of a vessel, or they can be arranged to look through a clear viewport. Inductive proxes can detect metal parts, capacitive sensors can detect other materials, and photoelectric sensors can be arranged to look across an area and detect if material blocks their signals. These installations can be robust and serviceable, and they provide a cost-effective point level measurement option.
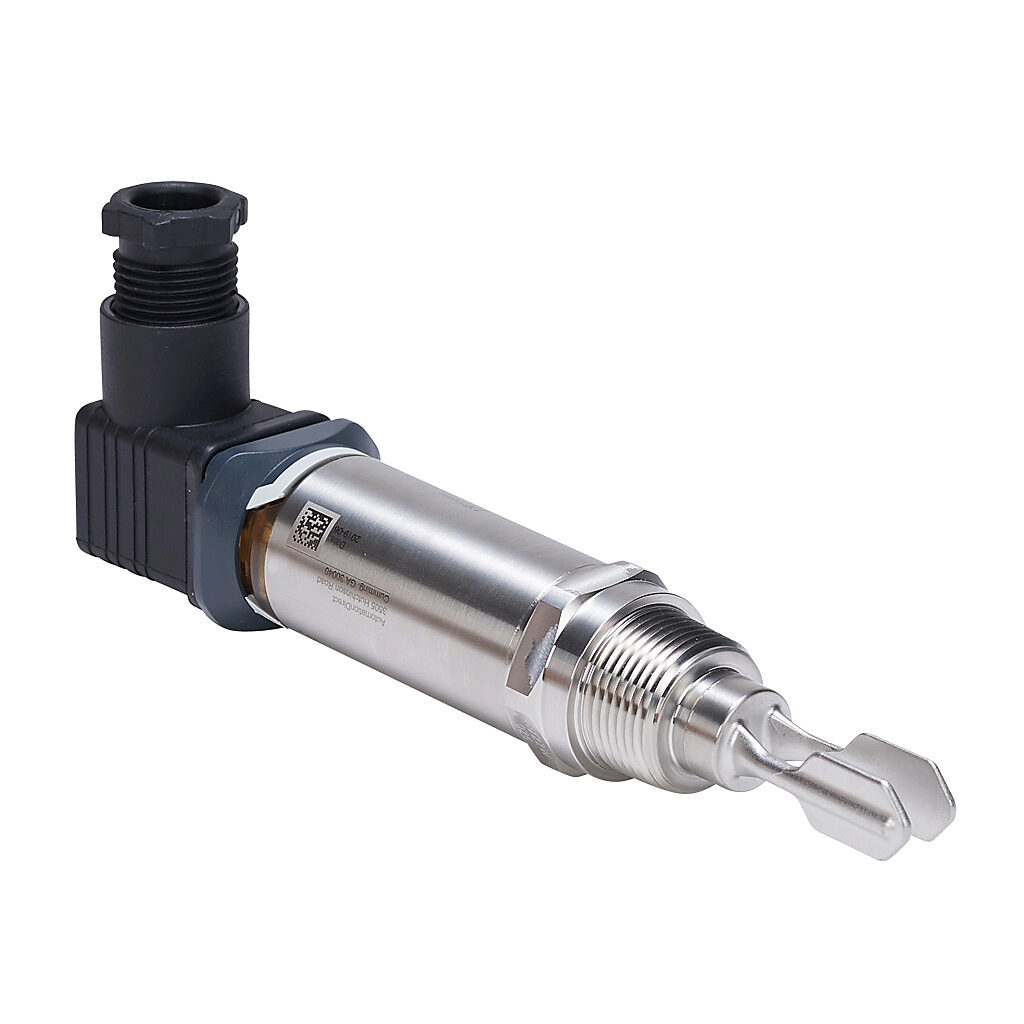
Vibration fork level switch: These sensors use a pair of vibrating prongs or paddles which insert into the product through the sidewall or lid of a vessel. They provide a good option where liquid characteristics are problematic for other technologies.
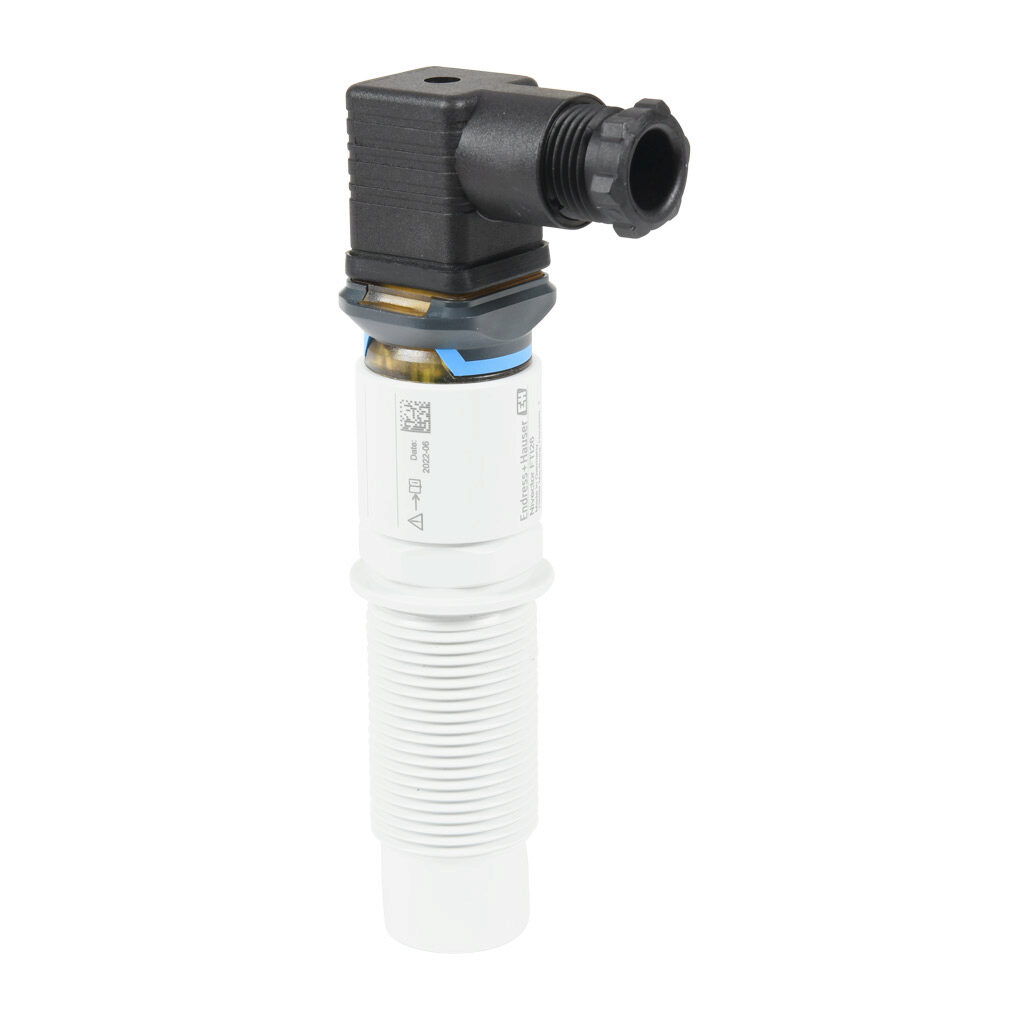
Capacitance level sensors: These sensors can be compact single-point units, or they can be configured with one or more longer probes to detect multiple level points. They work by detecting a change in capacitance when covered by a material, and versions are available for various build solids and liquids.
Note that the preceding devices are used for dedicated discrete point level measurement. Many other more advanced technologies are available which can provide not only continuous/analog level measurement, but also can return discrete point level signals as well. See the next section for a summary of these technologies.
Of course, there are other ways to measure discrete levels, sometimes by creating custom mechanisms that interact with the product, and are themselves provided with a detection device. Designers need to consider the vessel geometry, product characteristics, measurement accuracy, detection reliability, serviceability, and total cost of ownership when selecting discrete point level devices. Many of these devices will require some initial setup, and perhaps periodic calibration, to work correctly.
Some technologies are favored by certain industries and applications for discrete point level measurement. Water/wastewater sumps often use floats or capacitance probes. Bulk dry material applications work well with rotating paddles or proximity techniques. More challenging liquids or enclosed/pressurized vessels are good candidates for vibration fork technology.
Check out the other two blogs in this series: