Compact and distributed automation elements, and smarter fieldbus-capable instruments, are reducing the size of and need for control panels.
Chris Kregoski, product engineer for AutomationDirect, wrote an article for the July 2023 issue of Processing, titled Distributed Automation Enables Elimination or Shrinking of Control Panels. Here’s a summary, click on the link above for the full text.
Control panels have long been essential for protecting automation and electrical components associated with OEM machines and industrial manufacturing. While control panels will continue to be with us for the foreseeable future, several technologies are reducing the size of these panels, and sometimes obviating their use entirely due to:
- Smaller electronics
- Devices designed to withstand open mounting harsh environments
- Better field networking options, like IO-Link
- Wireless connectivity
- Mobile devices
Traditional automation architectures have relied on PLCs and HMIs located in main control panels. Motor controls and power distribution also needed to be protected by enclosures. Designers needed to evaluate many enclosure constraints such as:
- Size
- Protection
- Connectivity
- Thermal management
- Cleanliness
- Safety
Flexible Functionality
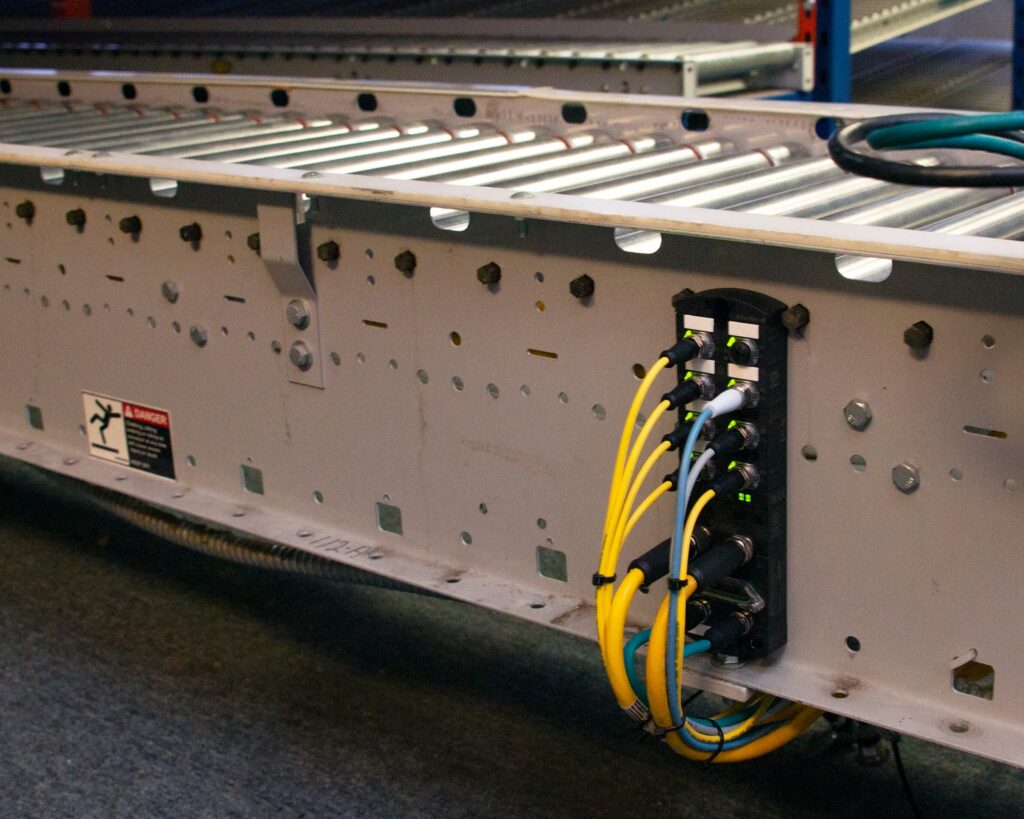
Here are just a few examples of newer technologies impacting how and where enclosures are needed:
- Wireless Ethernet and Bluetooth: Lets users work with their laptop or mobile device to wirelessly access automation devices and instruments, it works well for devices contained within non-metallic enclosures.
- Fieldbuses: Fieldbuses such as Modbus, PROFIBUS, and DeviceNet—or their newer Ethernet-based counterparts—let users minimize the amount of field wiring, and more easily distribute smaller control panels throughout a facility.
- IO-Link: IO-Link is a cost-effective standard providing practical digital connectivity for common OEM and factory needs. Benefits include bidirectional communications, transmission of up to 32 bytes of data, installation lengths of up to 20 meters of standard three-wire cables, supply of normal 24V DC power, and the ability for devices to act in traditional on/off or 4-20mA modes if desired.
IO-Link is particularly interesting because so many common field devices—like photoeyes, transmitters, and solenoids—are available with support for this protocol, allowing designers to push I/O closer to the field by creating a distributed architecture requiring minimal control panels.
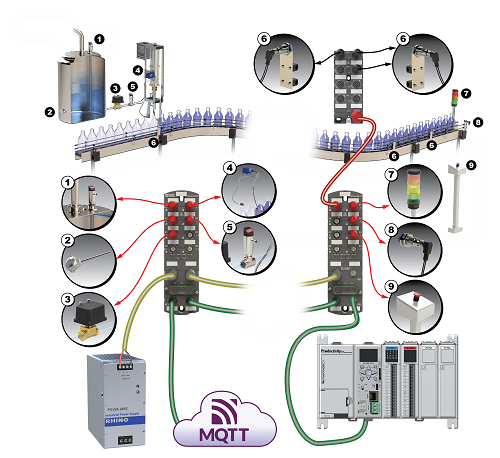
There are still cases where traditional panel-mounted HMIs make sense, but many designers are now taking advantage of mobile HMI technologies. A typical HMI display, or a newer “headless” HMI design, works with mobile devices like smartphones and tablets so users can interact with their systems wherever they are located.
Similarly, washdown-rated VFDs rated at NEMA 4X enable designers to install intelligent motor control directly on equipment or near the motor, saving on installation and disconnect switch costs. Some AutomationDirect VFDs include on-board PLC controllers to push even more functionality closer to the field.
Automation technologies of all types are becoming smarter and smaller, and some products are now made specifically for on-machine and field mounting. Many OEMs and systems integrators are moving outside the box to capture total overall installed savings due to minimized field wiring.
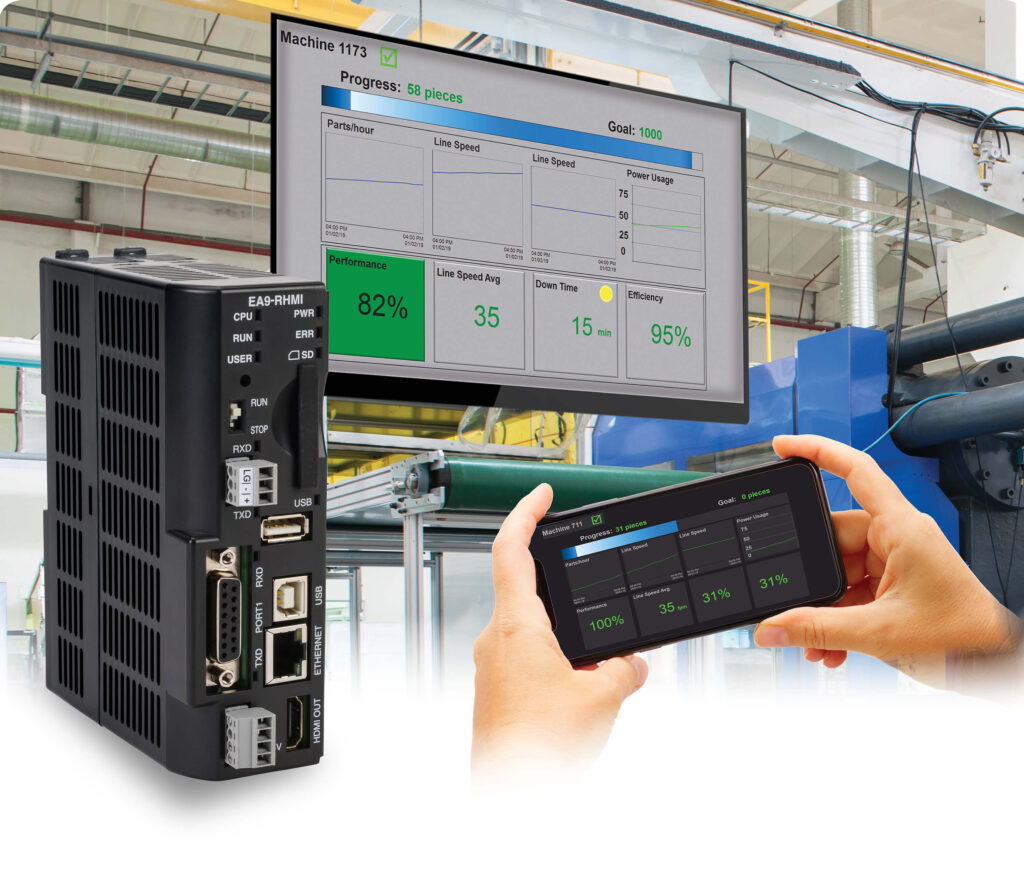
The AutomationDirect website offers an wide portfolio of enclosures, electrical components, PLCs, HMIs, VFDs, accessories, and much more, along with design tools and helpful online/phone support. Many OEMs and systems integrators are using these products to increase the effectiveness of their designs, and to realize total overall installed cost savings.