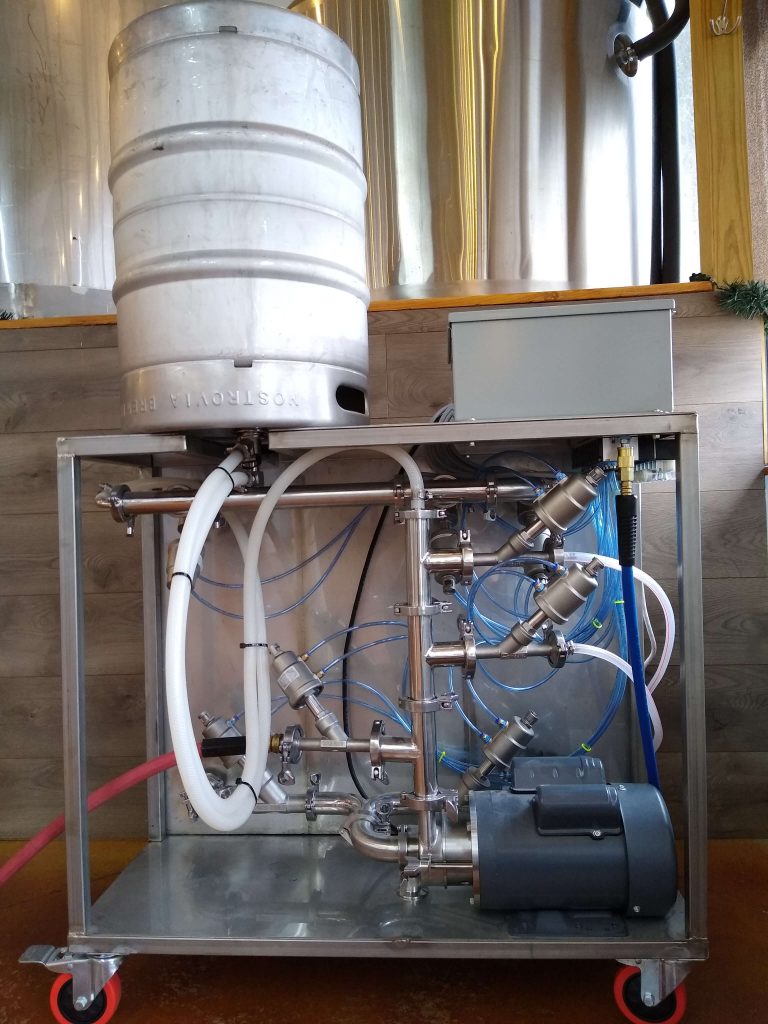
This microbrewery owner used AutomationDirect products to create a highly efficient keg cleaning system, which is used to improve in-house operations and support other similar small business owners.
Microbreweries and brewpubs have gained in popularity in recent years. Many of these are smaller operations owned by passionate craftspeople who perform many of the brewing functions manually. Good equipment sanitation is crucial to product safety and quality.
A June 2022 Control article titled Nostrovia Brewing Develops Automated Keg-Cleaning Kart bylined by Jeff Lukasik, owner of Nostrovia Brewing Co., describes how he used his hands-on knowledge and AutomationDirect products to create a keg cleaning cart, saving a lot of money and improving production.
Beer Budget Operation
Like many smaller microbrew and brewpub operations, Nostrovia uses a number of containers (barrels, half-barrels/kegs, sixth-barrels/sixtels) to produce, store, and distribute their product. Container cleaning is a labor-intensive and messy process with many steps using chemicals, high-pressure hot water, and CO2 purging. Basic systems cost a few thousand dollars, while fancier options range up to $20,000. Jeff knew he could improve upon these alternatives, and perhaps market the resulting system to other breweries.
Cleaning Chores Computerized
A typical keg cleaning sequence has hot water rinse, detergent wash, sanitize, and purge steps. Jeff was familiar with the mechanical and plumbing aspects, and he designed a cart to support a keg during these steps. A pump and solenoid valves orchestrated the actions.
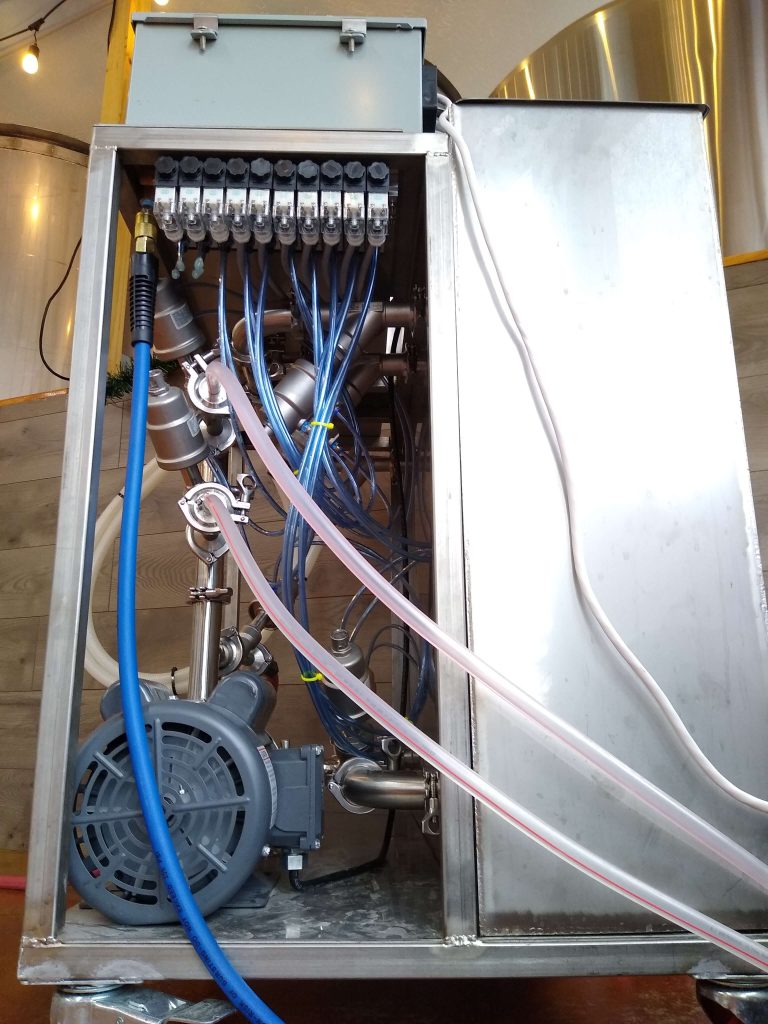
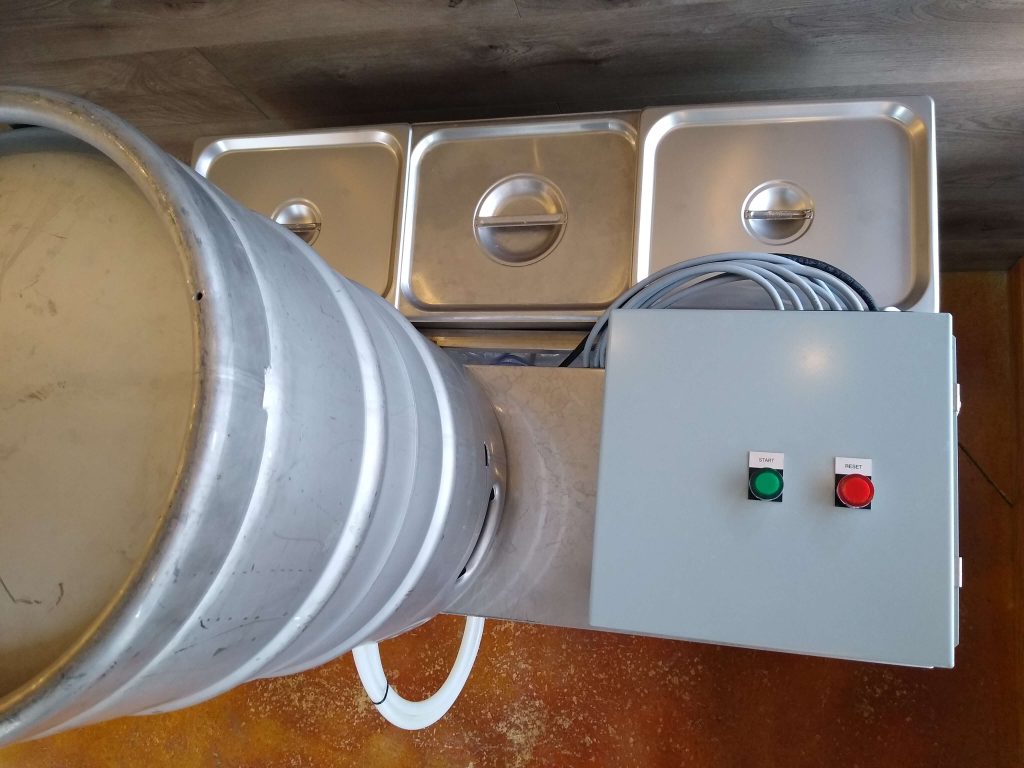
After some initial research, Jeff determined that an AutomationDirect CLICK PLC would be just right for this task. He designed a compact, serviceable, and water-resistant on-cart control panel using this PLC, along with many buttons, circuit breakers, power supplies and more, all sourced from AutomationDirect.
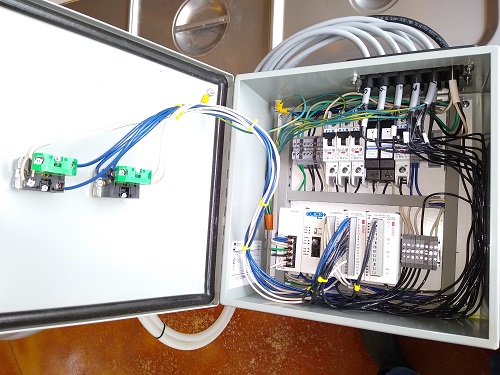
Jeff had no formal programming training, but he found the CLICK PLC and free software easy to learn and apply. He took advantage of online training and information materials, as well as web and phone support where needed. Programming and startup were accomplished within days, and the system has the flexibility to grow and be modified if sequences and timing need to be updated.
Since commissioning, Nostrovia has benefited from better cleaning effectiveness and simplified operation, along with cost savings due to less energy and chemical usage.
The ease with which I created this automated keg cleaning system has opened up new possibilities for our brewery. The excellent experience with this project is also leading us to look at what other aspects of our brewery we can automate, such as canning, to provide better beer for our patrons.
Jeff is already thinking about adding an HMI and more sensors, a feasible plan because the PLC provides endless options for continuous improvement.
All figures courtesy of Nostrovia Brewing Co.