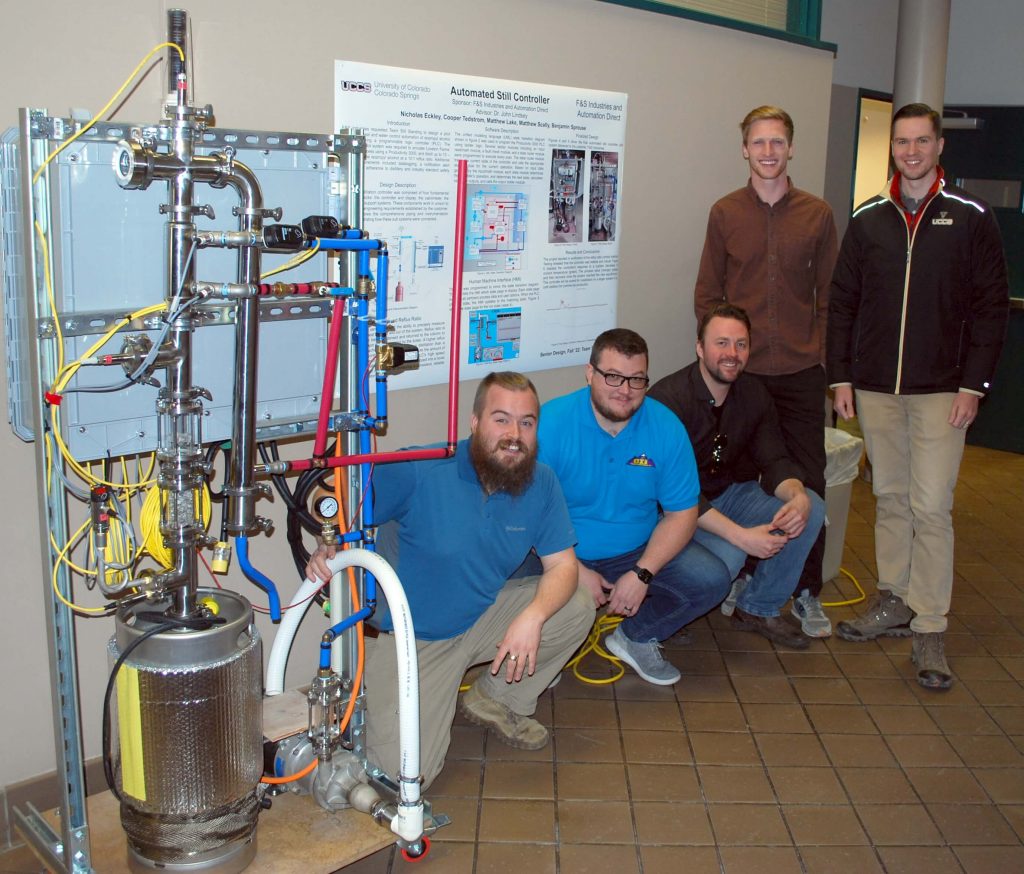
These University of Colorado—Colorado Springs students performed their capstone design project by using AutomationDirect products to optimize operations for a master distiller.
A team of electrical and computer engineering students at the University of Colorado—Colorado Springs (UCCS) got a flavor of industrial automation and the taste of success as they designed and tested an automated still controller. The team—named Still Standing—wrote about the project in a Control Design June 2023 article titled Distillery Control System Designed by University Team Reduces Manual Operation Time. By teaming with a local craft distillery, they gained valuable experience, while providing useful process improvements with reduced required operator effort.
A High-Proof Design
The team first developed an Engineering Specification Agreement to define detailed requirements for the craft distiller, including functional goals and safety matters associated with a pilot size system, which could later be scaled up. They created a piping & instrumentation diagram (P&ID), and then evaluated suitable controls and sensors. The prototype seven-gallon still included a column condenser and coolant pump hardware.
Based on the requirements, the team selected an AutomationDirect Productivity 3000 PLC, a C-more HMI, and state-of-the-art sensors from the ProSense line for measuring temperature, pressure, and flow. These sensors featured a user-programmable detection range, which allowed the designers to “zoom in” on the small temperature ranges of interest.
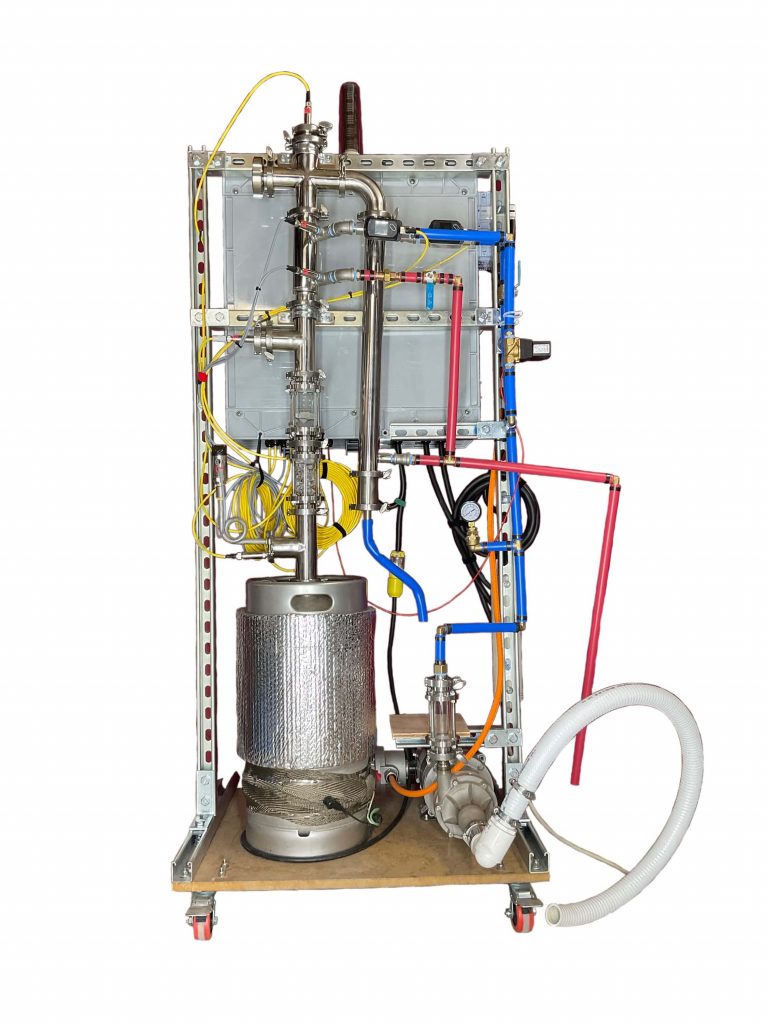
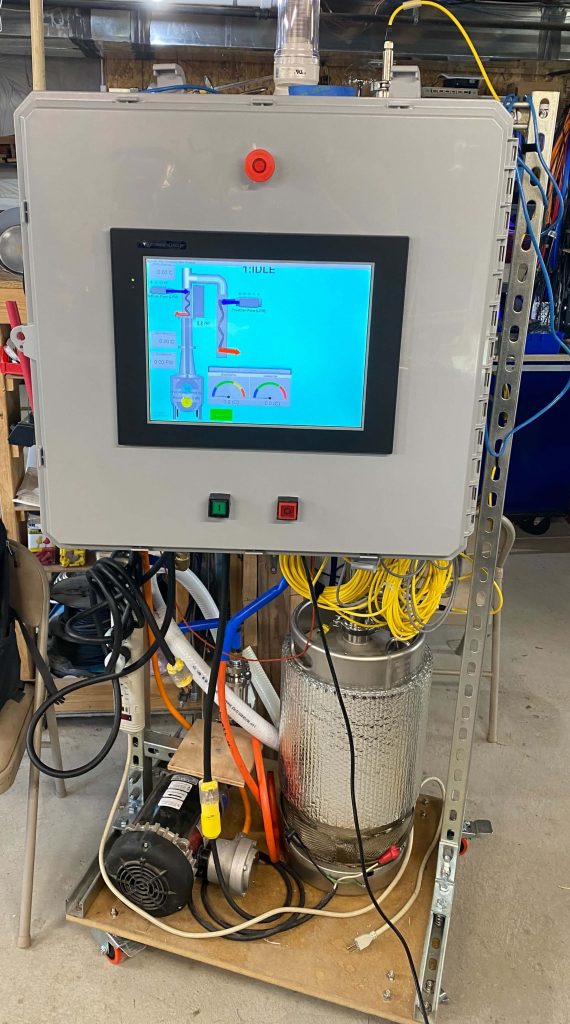
Team members found the Productivity PLC development environment was quick and easy to learn, and it allowed them to create a finite state machine for controlling the process through warmup, production, and cooldown. They also programmed logic to handle faults and perform PID loop control.
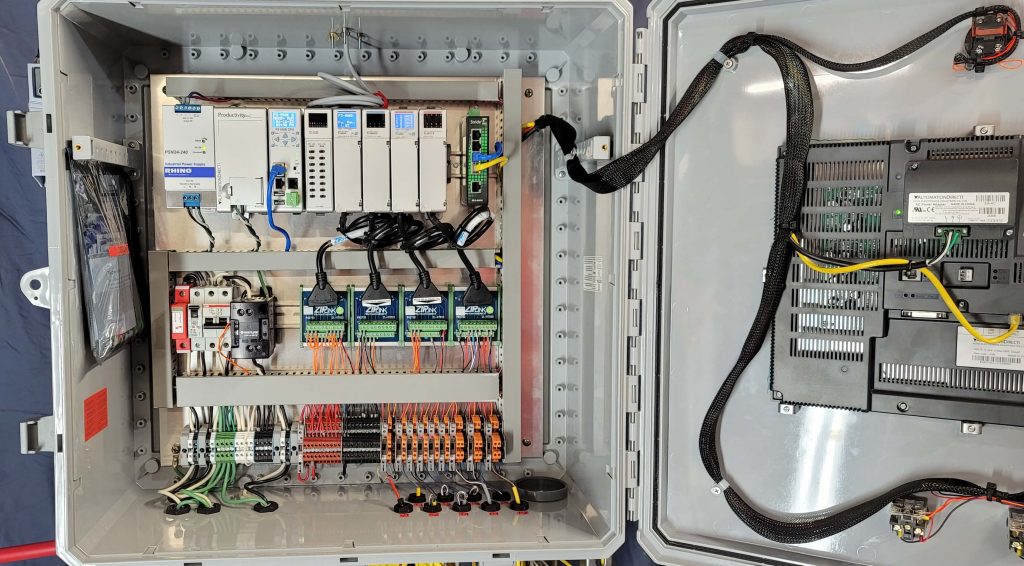
Delivering Visual Clarity
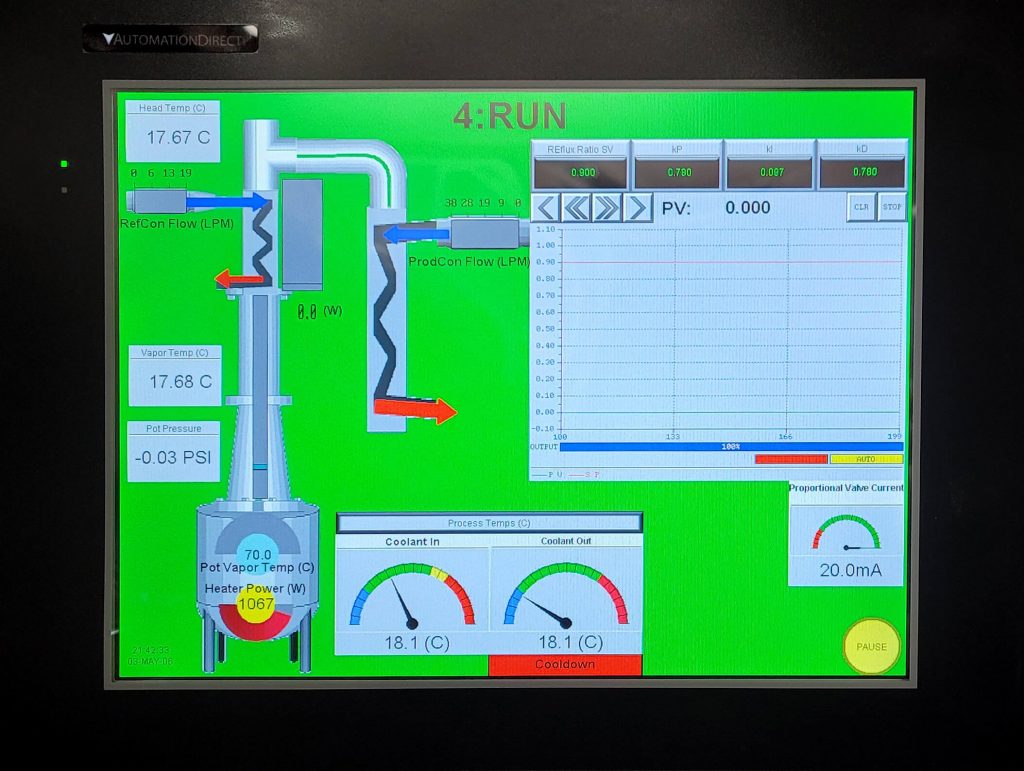
The HMI provided real-time data display for operation and tuning, and data logging was implemented for valuable post-process analysis. A notification alert system warned operators of any detected errors. Users found that the large and vivid display made it easy to observe process conditions, initiate command and setpoint changes, and trend performance.
Last Round
Typical small batch distillation is often performed by operating a boiler open-loop without any feedback. To improve performance with this reflux still design—which can have notoriously non-linear reflux response to temperature changes—the system resolves temperatures to a fraction of a degree, resulting in far more responsive and accurate control than is possible manually. During testing and validation, a fully automated run (using isopropyl rubbing alcohol instead of ethanol) performed error-free to distill 12% alcohol to the target 91% concentration.
For pilot projects like this, the PLC and HMI automation platform is important, but the primary focus is on developing and optimizing the process. The team appreciated how easy the selected automation platform was for them to learn and develop and how capable it was in operation.
While the PLC, HMI, and other AutomationDirect components were selected for their performance and cost-effectiveness for the prototype system, they are equally applicable to the distillery’s full-scale production. AutomationDirect helped team Still Standing satisfy all customer requirements and complete their senior design project successfully.
Visit the AutomationDirect.com website today to explore products that can help your company keep essential systems in service.