AutomationDirect products and services enabled an industrial calibration provider to deliver more services to help their clients save time and money.
Industrial calibration firm Gulf State Instruments (GSI) has a 20-year track record of helping their customers optimize operations. In this success story published in the July edition of Control magazine, titled Gulf States Instruments expands business with automation solutions , GSI owner Robert Boudreaux describes how his team used their deep understanding of instruments and equipment to integrate automation products from AutomationDirect to help their clients improve safety and minimize waste.
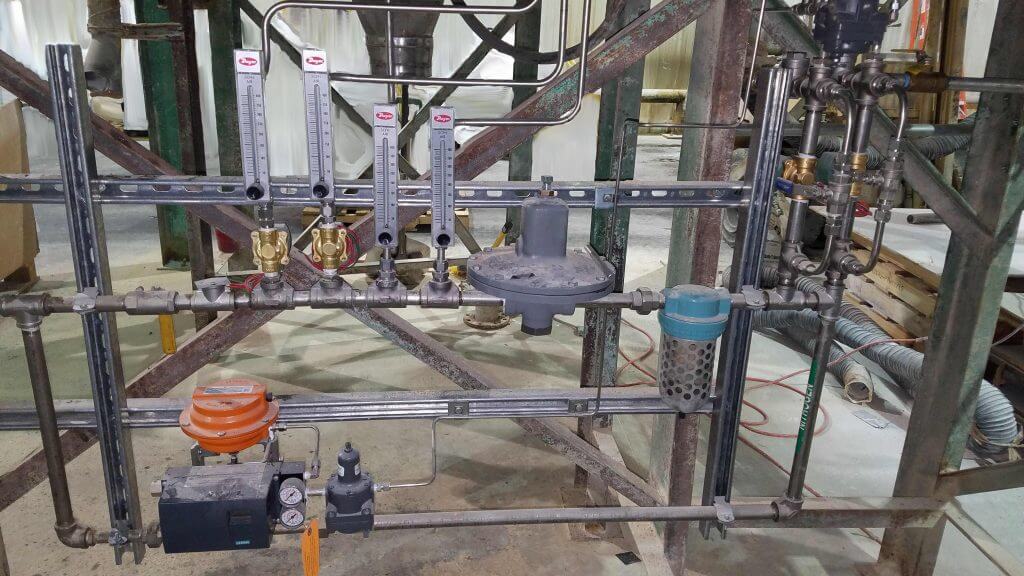
The Right Mix
Toll manufacturing processors provide a service to blend, mix, or compound multiple raw chemicals and materials into a finished good used by other companies. Because these activities may create combustible vapors or dust, it is necessary to inert vessel headspaces with a blanket of nitrogen to avoid ignition. Bulk nitrogen, valves, and instruments are needed to achieve this. Traditionally, this is a manual activity, which is time-consuming and subject to operator errors or excessive nitrogen waste.
Improved Inerting
As GSI technicians calibrated instruments and maintained devices at their clients, they observed the problems with manual inerting, and initially created some basic hardwired interlocks to help the operators. Positive results soon led GSI to develop a more comprehensive programmable logic controller (PLC) and human-machine interface (HMI) system to automatically inert the vessel and monitor the status.
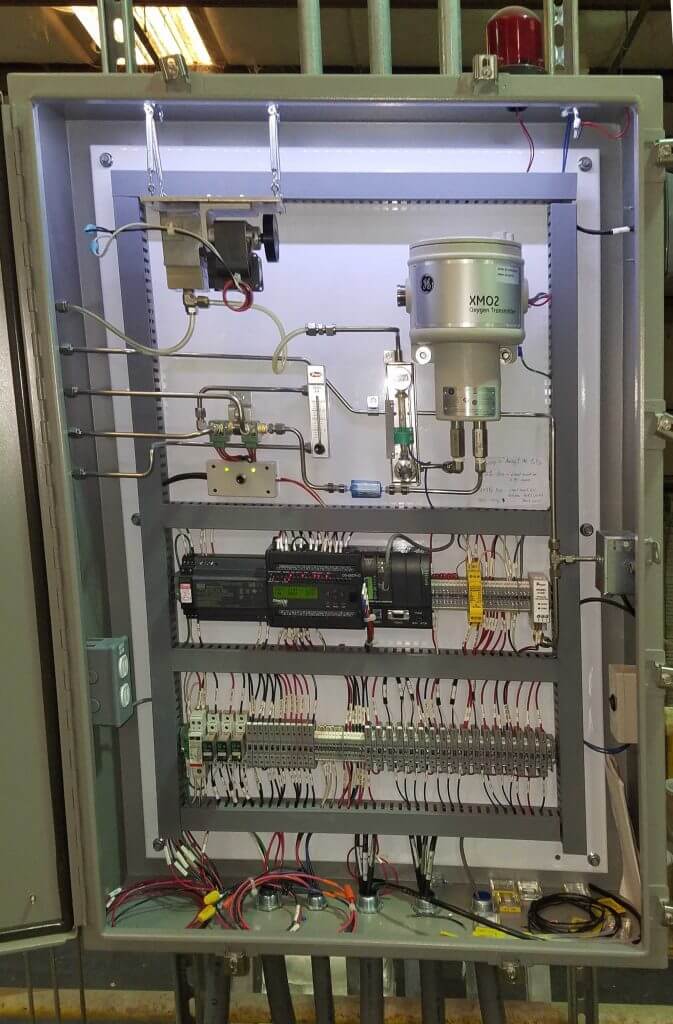
Picking the Platform
The GSI team worked with their client to clearly define the automation tasks and select associated valves and instruments. Based on GSI’s previous positive experiences with AutomationDirect PLCs, HMIs, and other industrial automation components, the control panel was designed around a DirectLogix PLC and a C-more HMI. The AutomationDirect website offered all the necessary technical specifications and guidelines, simplifying specification and procurement of devices. Technical support was just a phone call away and helped the team complete design quickly.
HMI Look and Feel
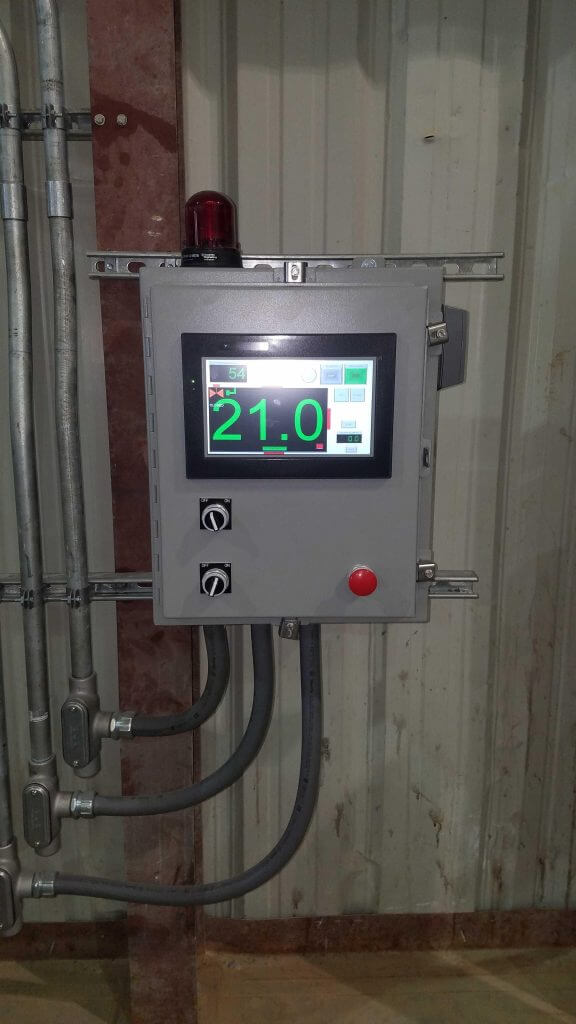
The PLC automation needed to be bulletproof, but equally important was ensuring the remotely located HMI clearly communicated the most important values and provided easy access to control functions. GSI collaborated with the owner to detail the displays. They created one display for blending, another for clean-out, and a third for more detailed information. A large visual indicator shows oxygen level, easily viewable from a distance, and audible/visual alerts notify operators of any warning conditions.
Future Flexibility
Because the first automated inerting system solution was such a success, GSI has subsequently produced four more. AutomationDirect’s family of PLC and HMI platforms and automation products have provided the flexibility needed for GSI to offer improvements and enhancements with each iteration. Future upgrades may include networking these standalone systems, adding mobile connectivity, and expanded data gathering.
Working with AutomationDirect products and technical support enabled the GSI to extend their capabilities beyond normal day-to-day activities.
GSI and their clients appreciate how the systems accurately inert vessels, reduce nitrogen waste, improve safety, and increase personnel productivity.
Figures, all courtesy of AutomationDirect and Gulf States Instruments
Originally Published: July 2020