It happens more often than we’d like in the material handling industry. During an accumulation conveyor start-up, the photoelectric sensors cannot detect the totes that the conveyor transports. Even worse is when a conveyor system that has worked fine for a long time is suddenly unable to detect new totes introduced into the system.
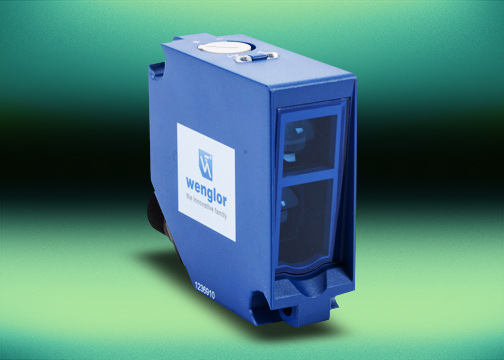
In the scenario mentioned above, the problem is usually a combination of two things. First, the conveyor’s photoelectric sensors are a diffuse type, meaning they operate without needing a reflector, and second, the new totes are black or some other dark color (dark gray, dark brown, dark navy blue, etc). If the problem only occurs with darker-colored totes, and other objects are properly detected, then this is most likely the problem. Fortunately, there is a solution.
Solving Problems with Photoelectric Sensors
Let’s discuss this problem by describing why we choose diffuse photoelectric sensors and how they operate. The biggest advantage of using a diffuse photoelectric sensor is that they don’t require a reflector mounted opposite the sensor. This makes them a logical choice on an accumulation conveyor, especially if the conveyor doesn’t have a guard rail installed on it. Many times a guard rail is impractical on a conveyor in places like pick modules or on conveyors where workers remove products from the conveyor. Diffuse photoelectric sensors don’t have as long of a sensing distance and aren’t as precise as the other styles of photoelectric sensors, but in most cases, they work well as “under-the-roller” sensors on an accumulation conveyor.
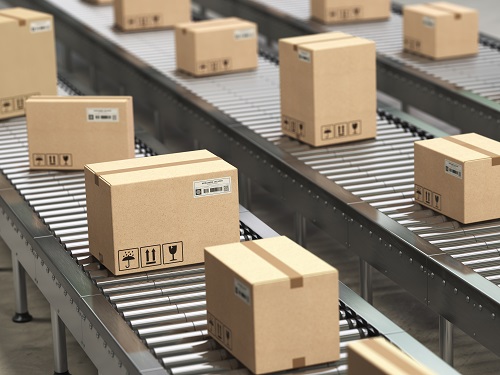
A diffuse photoelectric sensor has an emitter and receiver integrated into the same housing. The emitter sends out light, usually from a red LED, and if an object is present, it reflects much of the light to the sensor’s receiver. If enough light of a certain wavelength is received, the sensor determines that an object is present. If the color of the object we are trying to detect is dark, then too much of the light will be absorbed instead of reflected, and the object might not be reliably detected. The opposite can occur if the object is too shiny and reflective, such as chrome-painted products or clear packaging tape that isn’t secured properly onto a package. With overly reflective objects, the detection can be undetermined, resulting in no object being read or one object being read multiple times.
There are a few solutions to the problem of dark or shiny object detection. The more obvious solution to the problem is to use either a polarized retroreflective or a through-beam photoelectric sensor. However, in many cases, such as with an under-the-roller photoelectric sensor, this just isn’t possible. The other option is to use a dark and shiny object detection photoelectric sensor.
Dark and shiny object detection sensors work similarly to a standard diffuse photoelectric sensor, but they use blue light instead of red. Blue light is less likely to be absorbed by a dark object and is less likely to cause multiple reads or misdetections from shiny objects. Keep in mind that every diffuse photoelectric sensor that is required to detect dark or shiny objects will need to be replaced which can be costly and time-consuming. It is always best to know the color of the objects you are sensing ahead of time to avoid added time and cost or loss of production time.
Learn more about AutomationDirect’s offering of dark and shiny object detection photoelectric sensors.
To read more articles about sensors click here!