AutomationDirect PLCs and products help a hobbyist automate his homebrew equipment, taking quality to the next level.
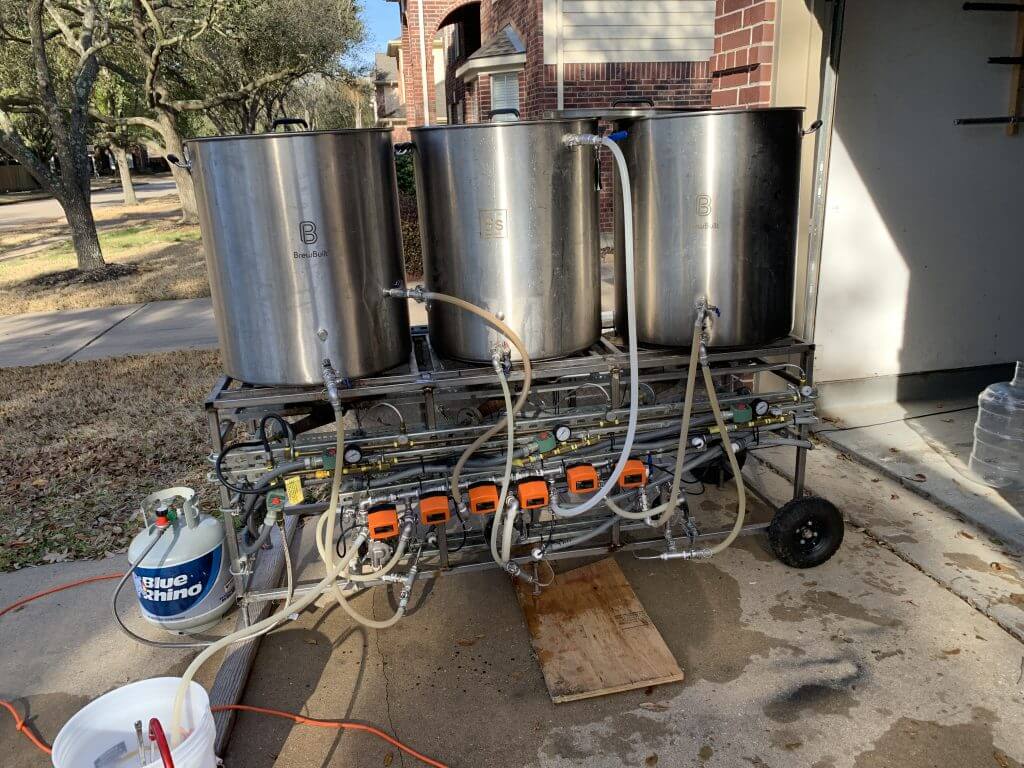
Back in 2012, Jason Wilson toured a local brewery, and soon thereafter became a homebrew enthusiast. He was fascinated by the detailed science and math underlying the production process, and quickly realized automation would be key to precisely controlling the brewing process.
Jason wrote a success story article published by Automation.com in June 2021 titled Hopped-Up Homebrew Automation, describing his journey of learning and implementing industrial automation products for his homebrew system, and how he relied on AutomationDirect PLCs and products to do just that. Here’s a summary.
Brewing 101
The basic beer recipe has been around for a very long time. Barley grain is germinated, dried, and crushed—then introduced to hot water, creating a mash where grain starches are converted into sugars. Mash is boiled with hops to create wort, which is then cooled, and yeast is added to convert the sugars into alcohol.
Temperature control is important at every step because various enzymes are activated and then denatured as temperature rises. The flavor and quality of the final product is impacted by the temperature profile as it controls these enzymes. Most homebrewers start with manual thermometers and burners, but it is very difficult to closely monitor and control the temperatures in this manner.
Automation Upgrade
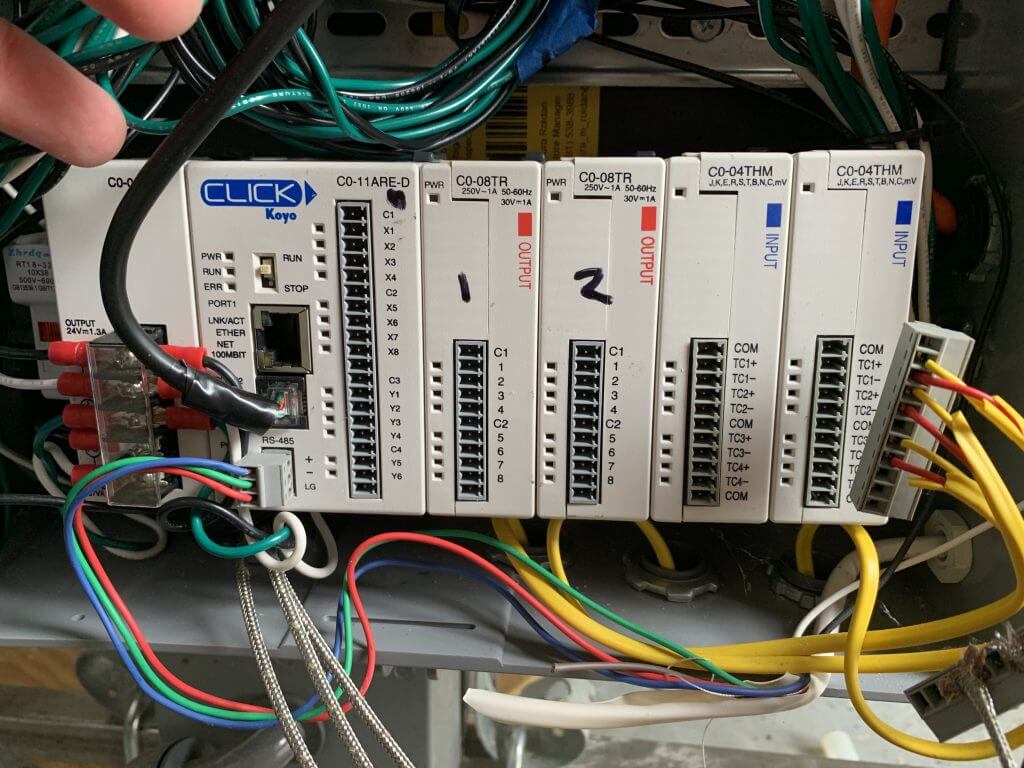
Jason assembled some small-batch kettles and burners, but he had no specific training in electrical, instrumentation, or controls programming. Fortunately, an acquaintance introduced him to the AutomationDirect website, where he discovered a variety of solenoid valves, sensors, industrial controllers, and other components he could quickly and economically obtain to build out his system.
He had no programming background, but as a first-time hobbyist he found it easy to learn how to use the software by using technical support documents and videos. On a few occasions where he ran into a snag, knowledgeable experts at AutomationDirect helped him via phone support.
An AutomationDirect CLICK PLC was wired to thermocouples to monitor temperatures, solenoids to control gas and liquid flows, and level switches to monitor kettle levels. Jason created multi-event recipes to allow detailed configuration of time and temperature setpoints, along with on/off burner control logic, and he also automated filling and emptying of the kettles.
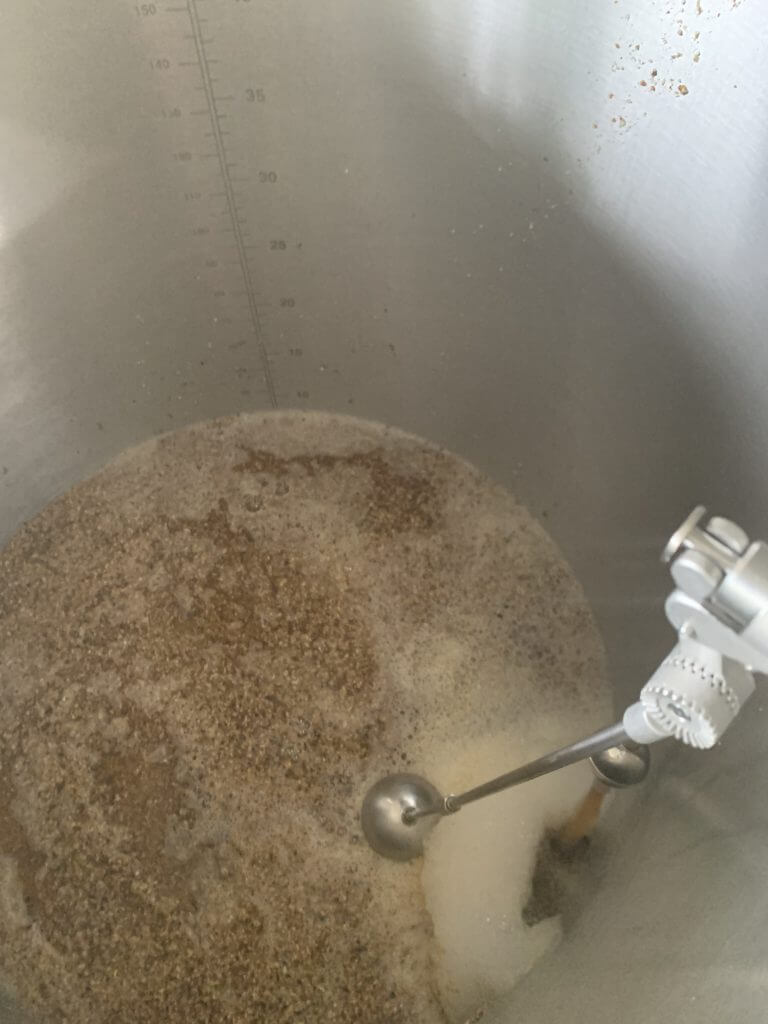
With the basics in place, Jason soon added other advanced capabilities, like using his smartphone as an HMI, with displays for monitoring brewing status and adjusting setpoints. This lets him confidently monitor and control the brewing operation from anywhere.
He configured the PLC to log data so he could create a record of the batch, which helps him decide how and where to improve future recipes.
Bill Owens, who founded America’s first brew pub in 1983, once said “Give a man a beer and waste an hour. Teach a man to brew and waste a lifetime.” Many would say the word “waste” is a bit strong when describing a beverage which is among the most-consumed worldwide and is found in almost every culture, but one can see how it is easy to get excited about this hobby.
Using AutomationDirect products has been a fun and productive way for Jason to take his homebrew system to the next level. He now enjoys virtually endless flexibility to experiment, and one day he may even scale up to a commercial level.
Check out the AutomationDirect.com website today to explore products that can help your company control its own automation destiny.
Read more application stories here!
All figures courtesy of Jason Wilson