Stepper motors use specialized control methods to achieve better precision than standard variable speed motors, while avoiding the expense and complexity of servo systems.
For industrial automation, the term motion control usually means using an electric motor to positively drive the position, velocity, and acceleration of a physical system. Pneumatics are economical, and hydraulics can provide the greatest force. But electric motors often provide the right balance of accuracy, speed, power, durability, and operating cost.
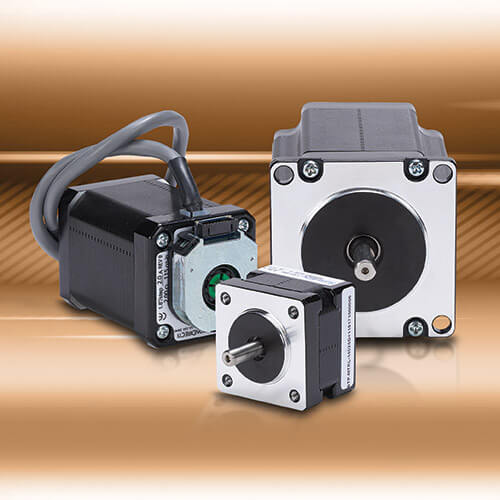
AC induction motors and DC motors are useful for basic on/off and less precise variable speed applications, while servo motors combine high speed, torque, and position/velocity/acceleration precision via positive feedback—with correspondingly high cost and complexity. Some users need better motion control than is possible with AC induction or DC motors but are looking for a more cost-effective option than servos.
For many applications, the answer can be stepper motor systems, consisting of a stepper motor, a drive, and a controller. Stepper systems provide some of the best features of the previously described motors, in an economical way. For lower speeds and smaller force requirements, stepper motors provide good motion resolution. This article describes how users can implement and control stepper motor systems.
Stepper Specifics
Stepper motors are named as such because they are commanded by pulses received from a drive to move in small discrete steps, and they can do so rapidly. They typically work best below 1,000 rotations per minute (rpm) because torque falls off rapidly as speed increases. Stepper motors lack any overload capability, therefore one industry rule of thumb is to size stepper motors and drives so that the expected load uses only 50% of the available torque to avoid potential stalling conditions.
Stepper motors are commanded by a pulse train from a controller. In full-step mode there are usually 200 steps (or 1.8 degrees) for each 360-degree revolution, and each pulse moves the motor one step, but this mode is not typical because it lacks precision. Instead, users typically select half-step, quarter-step, or other microstepping modes which operate at 400, 800, or up to 50,000 steps per revolution. The key is to balance tradeoffs between accuracy and the required control signal bandwidth.
Although stepper motors are considered a low-cost motion control alternative compared with servo motors, steppers have some other advantages. Stepper motors have no jitter/dither at zero speed. For applications without a constant load from gravity or some other force, some stepper drives may have an idle current reduction option, which saves energy and reduces motor heating when the shaft is at standstill.
For machinery or equipment with motor-driven moving parts, perhaps using gearboxes or rack-and-pinion mechanisms, stepper motors are a good way to positively position a load. Although most stepper motors do not incorporate motor feedback, it is possible to add an encoder to the motor. For most applications, it is at least necessary to add sensors to the equipment to provide position feedback.
Taking the First Step
A stepper controller is necessary to generate the specific pulse train to accomplish motion. In turn, the stepper controller is connected to a drive to send a pulse of the appropriate power level to the motor itself. The controller, drive, and motor are usually separate components, but in some cases two or three of these functions can be combined in a single housing.
The controller can be a standalone device, or certain programmable logic controllers (PLCs) can create the pulses, making it easier to tightly integrate motion control with other automation functions. Basic stepper drives are not intelligent as they simply receive the controller pulses and amplify them into voltage pulses to operate the motor.
Designers must choose controllers and drives with compatible pulse characteristics.
The electrical signals may be open collector, line driver, or push-pull. High-speed pulses encode both the frequency and motor direction, using one of three methods:
- Pulse/direction (this is the most common method)
- Clockwise (CW) / counterclockwise (CCW)
- (sometimes used for encoder following because this signal is often used by encoders)
A stepper system can create motion by commanding the motor with respect to how far and how fast it should rotate. Some common motion profile examples, in order of increasing complexity, are:
- Move at a fixed velocity.
- Move a number of steps and then stop.
- Accelerate from one velocity to another
- Move a number of steps from one stopped position to another, first accelerating to a target velocity then decelerating back to zero speed at the target position, known as a trapezoidal move.
- Accelerate from one velocity to another; known as an S-curve move.
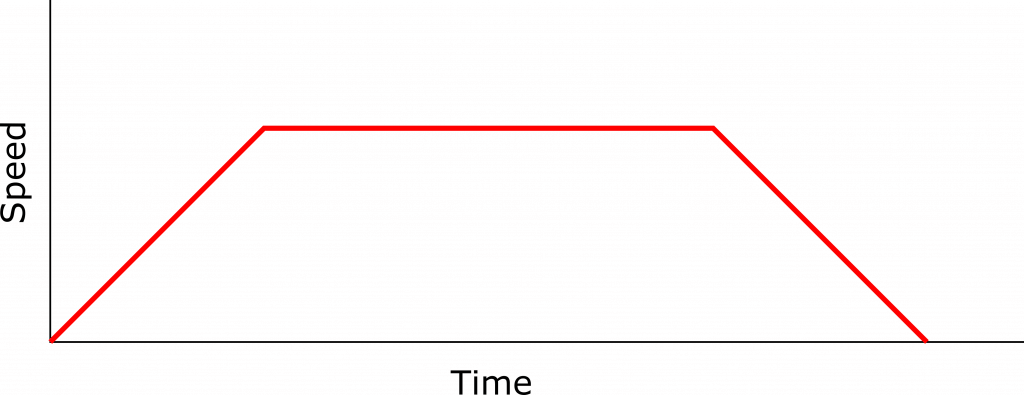
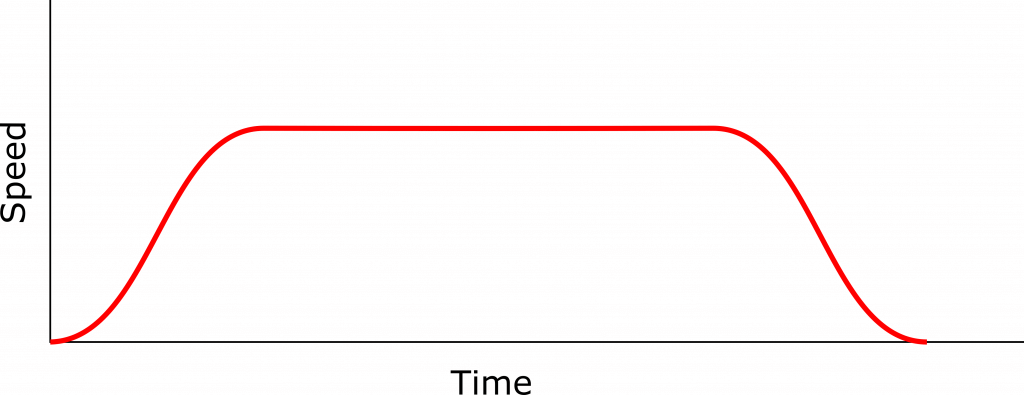
Homing and Position Verification
Stepper systems can only perform accurate, relative movements after the controller has learned the home position through a homing procedure. Because there is usually no motor feedback, a periodic position verification may also be used to confirm accurate movements for ongoing operation.
One way to accomplish homing is by installing a position switch at a known equipment location. To learn the home position, the controller/drive travels the motor to the expected position and establishes the home once the position switch is triggered. Position verification is similar, but it is generally a quick check performed during normal operation.
Exploring the Options
Stepper motors can be an advantageous choice for many applications, and when they are suitable, they will be a lower cost option than servos. For applications where accurate single-axis or limited multi-axis motion control is needed, stepper motors, drives, and controllers (especially PLCs) used in conjunction with position switches and/or an encoder will reliably operate machinery at about 25% the cost of servo motor systems.
AutomationDirect offers an online stepper selection tool, customer assistance (phone & online), and a wide variety of associated parts and technologies to help users implement the best solution for their application.