Winn Paulk, automation controls group product manager at AutomationDirect, wrote an article for the January 2019 issue of Control Engineering magazine, titled Industrial controller selection: Look beyond the basics. See below for a summary, or click on the link above for the full text.
Industrial Controller Selection
Most industrial controllers, such as programmable logic controllers (PLCs) and programmable automation controllers (PACs), can handle basic functions like real-time monitoring and control of discrete and analog inputs and outputs. Paulk says when specifying industrial controllers, concerns often turn to other capabilities such as data handling, communications, and high-speed control. He starts with data handling and logging:
Modern controllers with advanced tag name-based programming have a variety of data handling capabilities including built-in data logging. Some advanced controllers also can also interact with standard databases in enterprise-level systems such as an enterprise resource planning (ERP) system.
Data logging is typically event-based or scheduled. Events are triggered by status changes. Scheduled data logging is configured to occur at regular intervals such as every minute, hour, day or month.
The number of tags that can be logged is often limited, but at least 50 tag values should be stored for every scheduled or triggered event. System errors should also be stored with the time and date of the error or event included.
Beyond local data logging, some controllers can communicate with IT enterprise systems. Several software tools on the market, including KepWare KEPServerEX, allow a user to set up a connection between an IT enterprise system and a PLC to allow data to be collected from the PLC and saved in a database.
Communications Capabilities
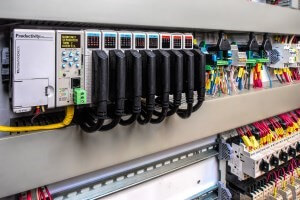
Paulk says the next important feature to consider when selecting an automation controller is communication capability:
Multiple Ethernet and serial communication ports should be available to provide easy integration with human-machine interfaces (HMIs), motor drives, and other devices. These high-speed Ethernet ports can also be used for peer-to-peer (P2P) or business system networking. This is where support for the EtherNet/IP (ODVA) and Modbus TCP/IP Ethernet protocols is important.
The communication and data handling capabilities of this AutomationDirect Productivity Series controller enables connection to many different devices.
Other communication ports should be provided for USB in/USB out, Mini USB, MicroSD, Remote I/O, RS-232, and RS-485 connectivity.
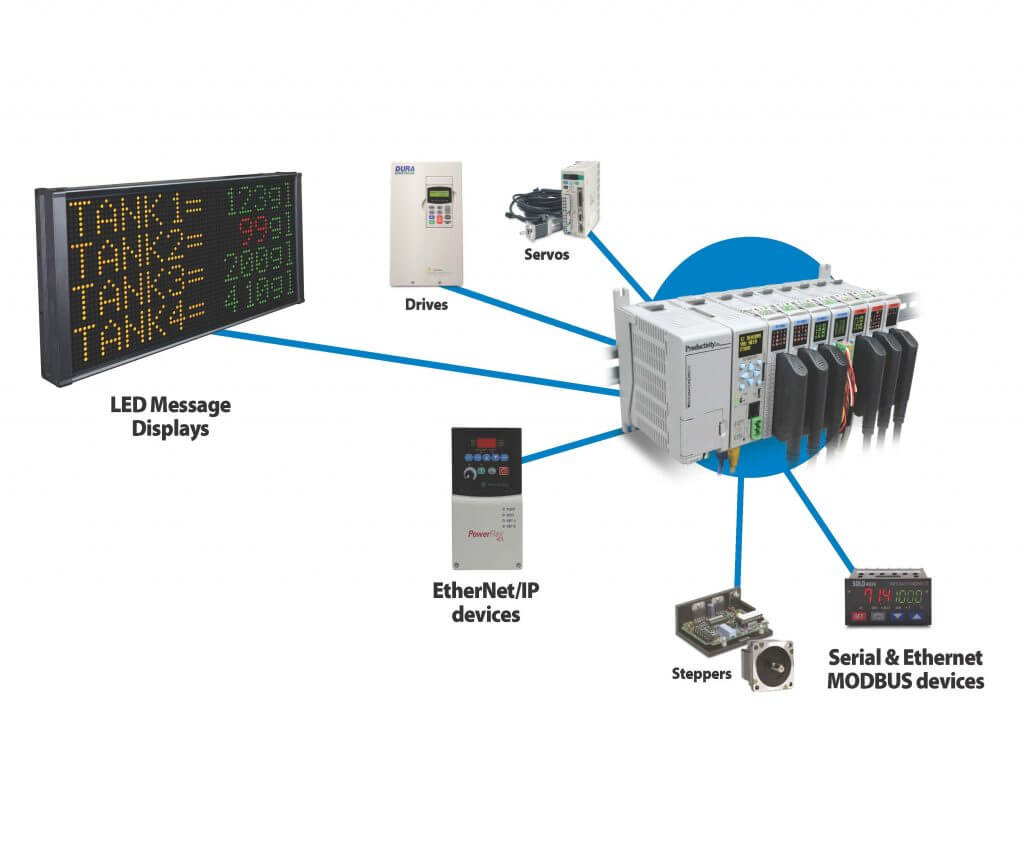
Some modern controllers, such as this Productivity3000 from AutomationDirect, include up to seven built-in communication ports, a critical capability for connection to both devices on the plant floor and to enterprise level business networks.
High-speed Control
Another feature driving the selection of a modern controller is the ability to control motion and other high-speed applications. High-speed I/O is needed to perform these functions, along with a powerful processor and the ability to prioritize high-speed tasks.
While some controllers offer coordination among many motion axes, Paulk says even coordinated motion between two axes typically requires special hardware and built-in controller functionality:
To start, a high-speed output (HSO) module and high-speed input (HSI) module are required. The HSO module generates pulse and direction commands to command servo drives operating two or more servo motors. These pulse and direction commands can control a variety of applications such as cut-to-length, stitching and coordinated x-y axis moves.
A programmable drum switch (PDS) and programmable limit switch offer additional high-speed control capabilities. The PDS enables monitoring of several devices, such as encoders, at rates up to 1 MHz. These input signals are used to coordinate and control outputs at rates of up tens of thousands of times a second. This type of hardware configuration provides precise and accurate motion control independent of controller scan time, which can vary depending on processor load.
Summary
When selecting PLCs, PACs, and other industrial controllers, users need to think beyond basic control and I/O requirements. For many applications, controllers also need extensive data logging and communication capabilities, along with control of high-speed applications such as coordinated motion.
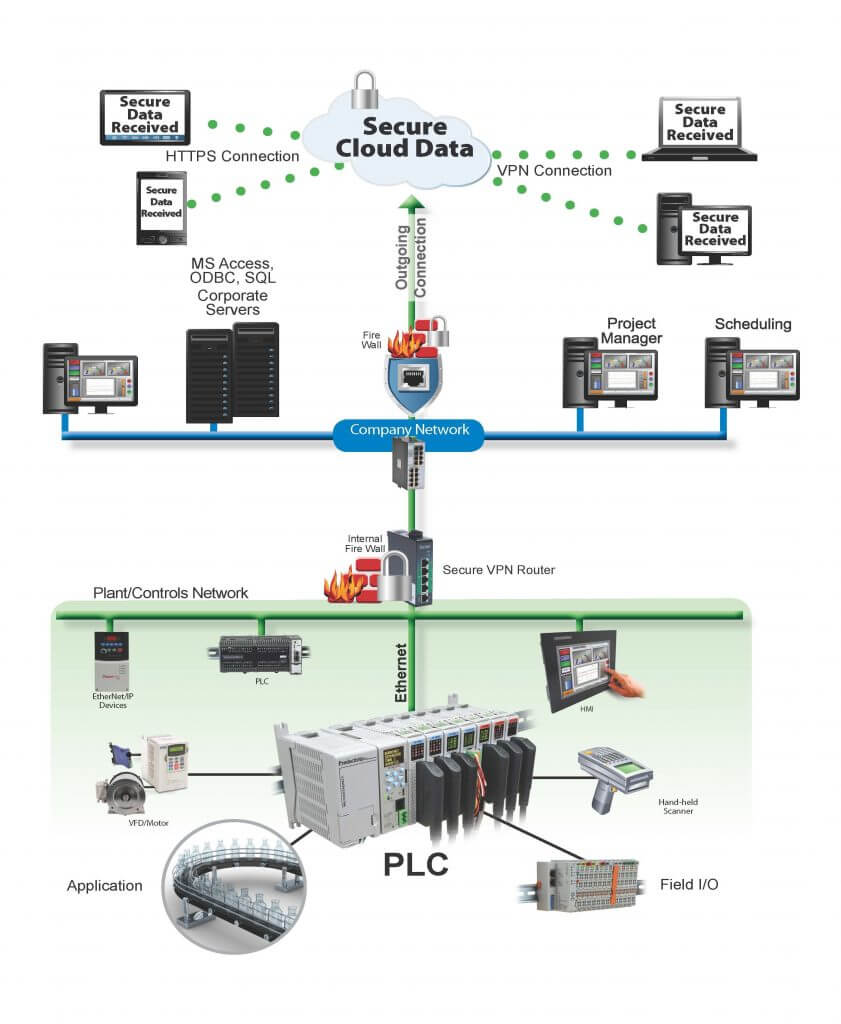
The capabilities of modern industrial controllers, such as this Productivity2000 from AutomationDirect, are expanding. Features such as data handling, communication, and high-speed control should be considered during the selection process to improve designs.
Read more about industrial controllers here!
Originally Published: January 2019