IO-Link modules, sensors, and other automation field devices help designers architect intelligent and cost-effective digital solutions so they can easily connect with industrial edge data for monitoring and controlling equipment.
Byline: Kevin Kakascik and Chris Kregoski, AutomationDirect
Traditional hardwired input/output (I/O) works well for monitoring and controlling sensors, actuators, and other field-installed devices associated with industrial automation. However, newer machines and systems are designed with far more instruments and automated components—some of them with intelligence providing significant additional data—which drives up the cost of classic single-signal I/O design and installation.
To address this issue, a variety of fieldbuses, including several industrial protocols suitable for use in the factory, have achieved success over the years for connecting with advanced field devices used in manufacturing and process applications. Unfortunately, most fieldbuses used on machinery are not made for direct connection to these sensors and actuators. To bridge this gap, a newer right-sized technology called IO-Link is making it easy and economical to efficiently network with all kinds of modern instruments and automation devices.
What is IO-Link?
IO-Link is specified in IEC 61131-9 as an open standard supporting responsive bi-directional communication between a programmable logic controller (PLC) or other host system and a field device (Figure 1). Basic IO-Link characteristics include:
- The ability to operate with standard I/O (SIO) hardwired devices, or with smarter devices supporting digital communications via IO-Link.
- Use of standard unshielded three-wire cables to provide 24VDC power and signaling for each field device, at distances up to 20 meters.
- Components and standard key-coded M12 connectors are available in IP65- and IP67-rated versions, making them suitable for surface machine-mounting without enclosures.
- An IO-Link master module transmits hardwired I/O or IO-Link communications to a host using an industrial Ethernet protocol, such as EtherNet/IP. An IO-Link hub can consolidate up to 16 discrete hardwired I/O points, and it can communicate the information with a master using IO-Link.
- Deterministic communication of 32 bytes of cyclic data to and from each IO-Link device attached to a master, which can include multiple process values, configuration settings, and diagnostics.
- Some master modules can also communicate directly to the cloud using the industry-standard MQTT protocol, even as they interact with a local controller.
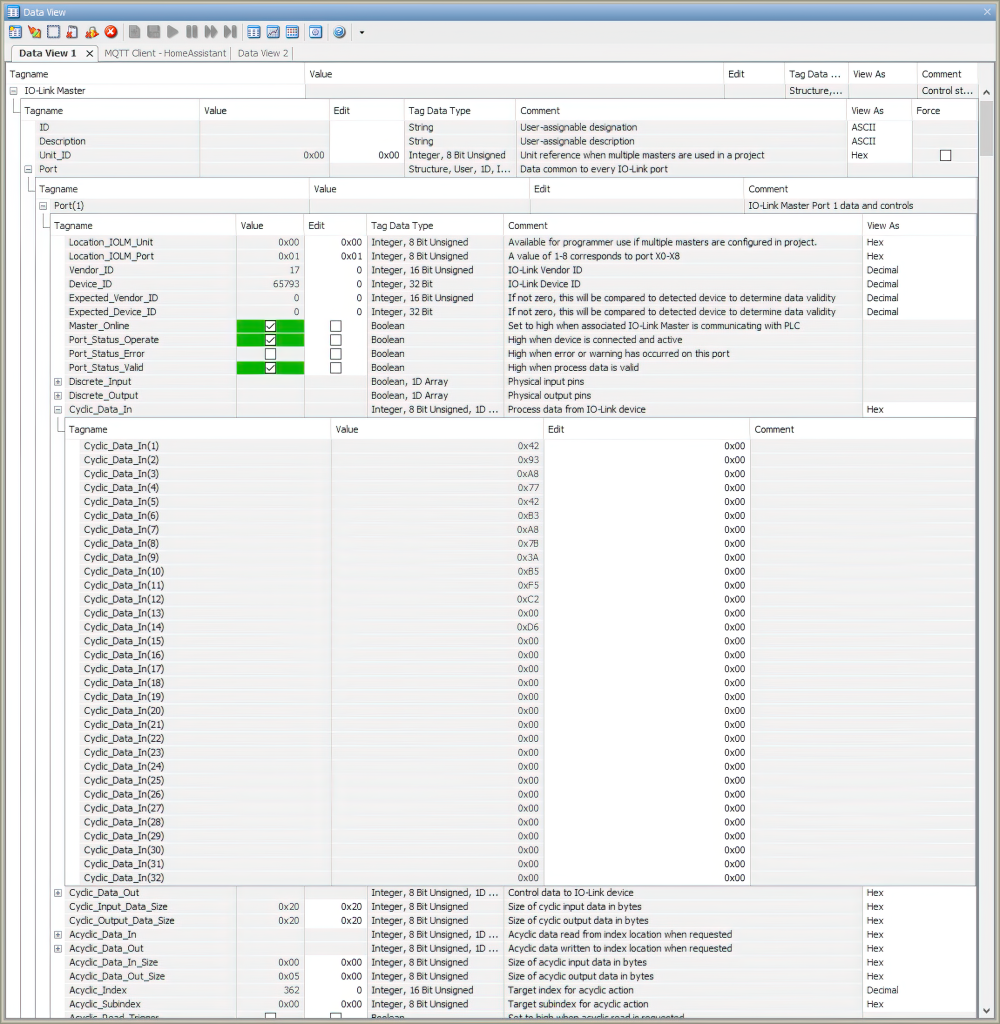
The IO-Link architecture provides a flexible way for efficiently installing and interconnecting master/hub modules, sensors, actuators, and other field devices.
Why IO-Link?
Some examples of basic IO-Link devices are absence/presence sensors (photoelectric, proximity), pushbuttons, and stacklights. More advanced devices are also available, such as flow/level/pressure/temperature instruments, light grids, and RFID readers. These devices are nearly as affordable as their traditional counterparts, and they are easily installed in the field with connectorized cables (Figure 2).
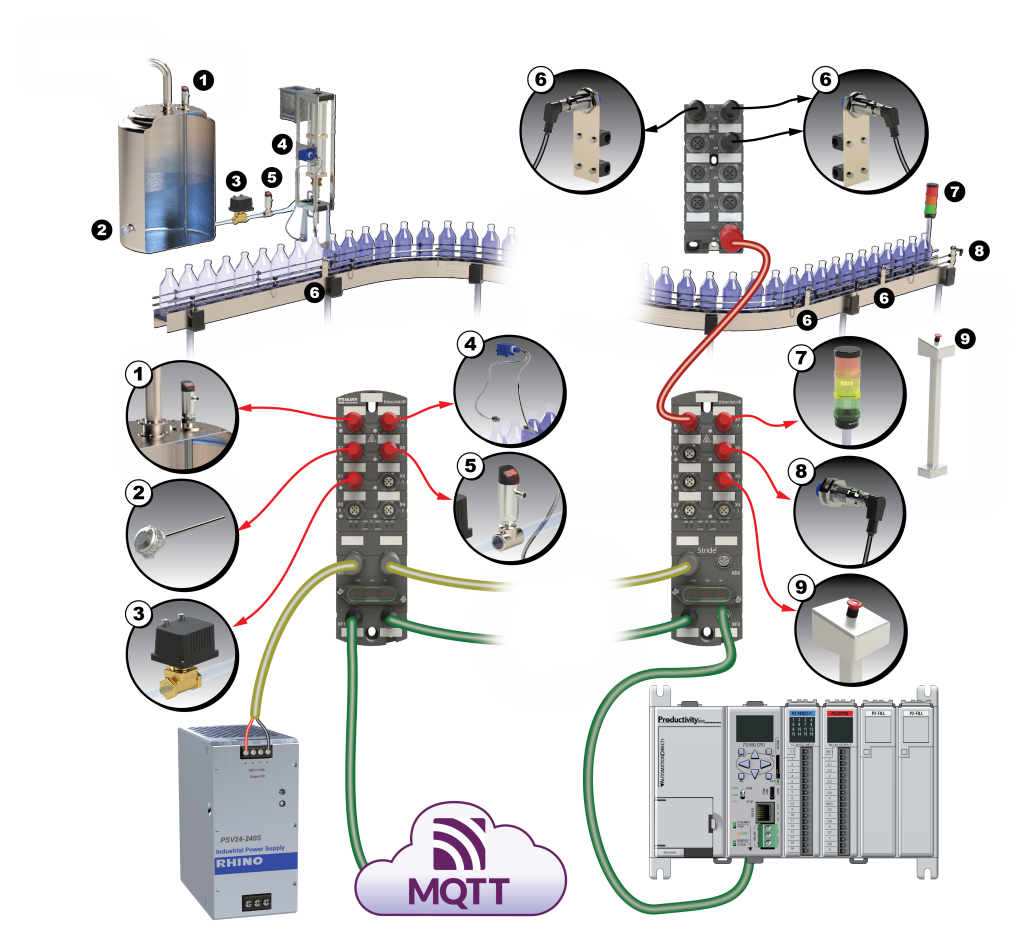
IO-Link installations perform the same general functionality as traditional hardwired devices, but provide additional user benefits such as:
- Remote configuration: IO-Link devices are easy to set up upon initial installation, and parameters can also be reconfigured dynamically in operation to support changeovers.
- Reduced downtime: If a replacement is needed, then all parameters can be automatically copied over to the newly installed device.
- Extended diagnostics: Smart IO-Link devices can report errors and other health parameters, streamlining maintenance efforts.
- Native IIoT support: IO-Link devices provide connectivity to a wide variety of field data sources, which can be transmitted directly to the cloud or via the host PLC, supporting industrial internet of things (IIoT) applications.
IO-Link Multiplies Performance
End users, OEMs, and systems integrators will continue to rely on some amount of traditional I/O connectivity, especially for real-time control. However, IO-Link has evolved as a right-sized approach for bringing more advanced digital connectivity to machine automation and other applications which have traditionally relied only on hardwired I/O.
Check out the AutomationDirect website to discover the wide variety of IO-Link master/hub modules, sensors, and automation devices available to help designers create more intelligent solutions, while reducing overall costs.
All figures courtesy of AutomationDirect
About the Author
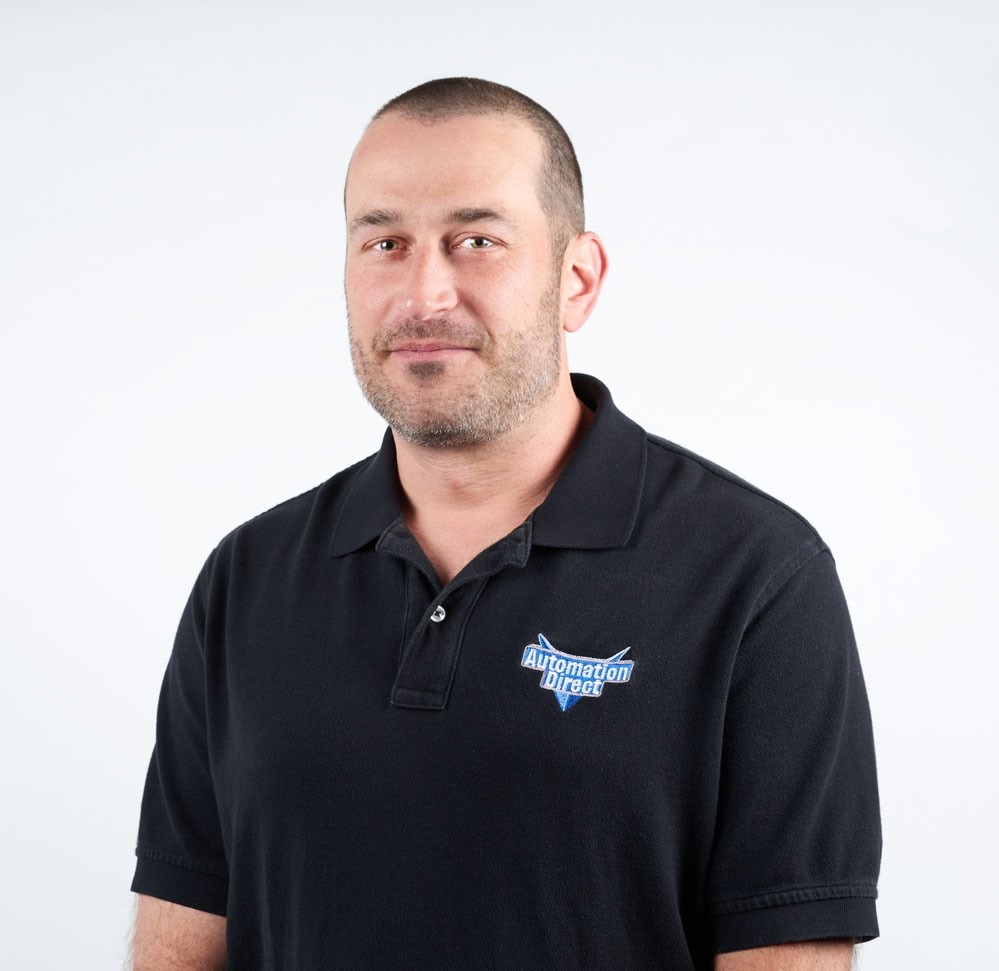
Kevin Kakascik is a Technical Marketing Engineer at AutomationDirect. Over his 20+ year career he has held controls engineering positions for machine OEM’s, entertainment industry systems integrators, and material handling systems integrators where he estimated, designed, commissioned, and started up systems. Kevin has worked at AutomationDirect since 2013 in technical and marketing roles. He holds a bachelor’s degree in Computer Science and Engineering Technology and an associate’s degree in Electrical Engineering Technology.
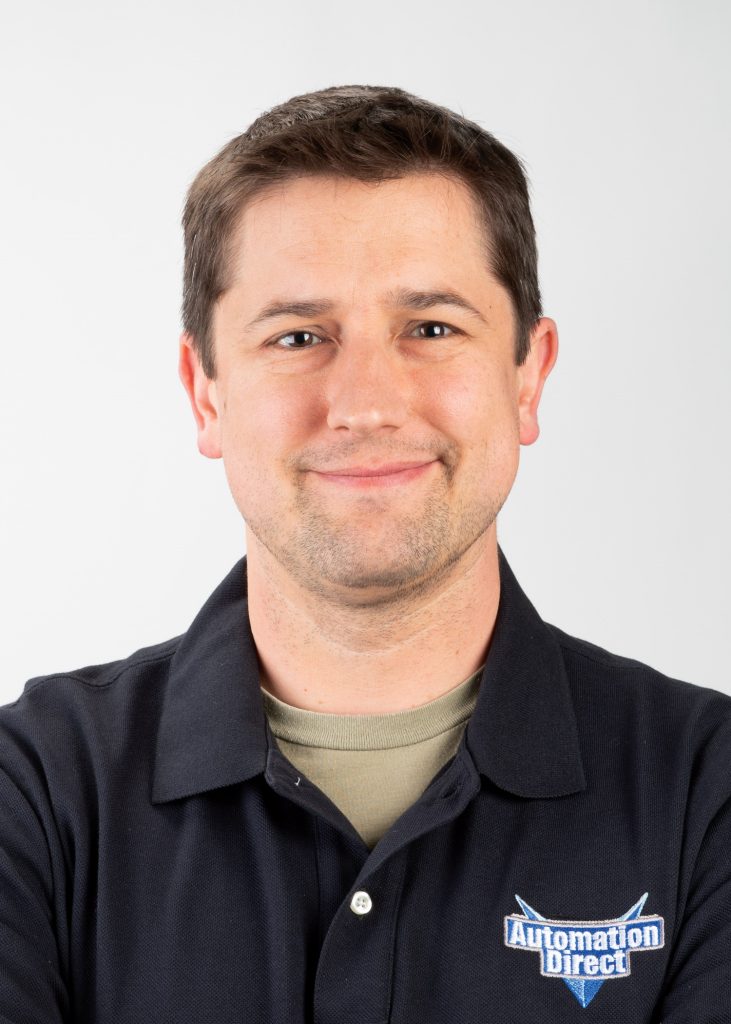
Chris Kregoski is a product engineer at AutomationDirect in Cumming, GA., on the Productivity PLC development and support team. He spent nearly a decade as the owner of Woodwest Controls, a small system integrator, servicing start-ups in malting, brewing, distilling, and water treatment industries.