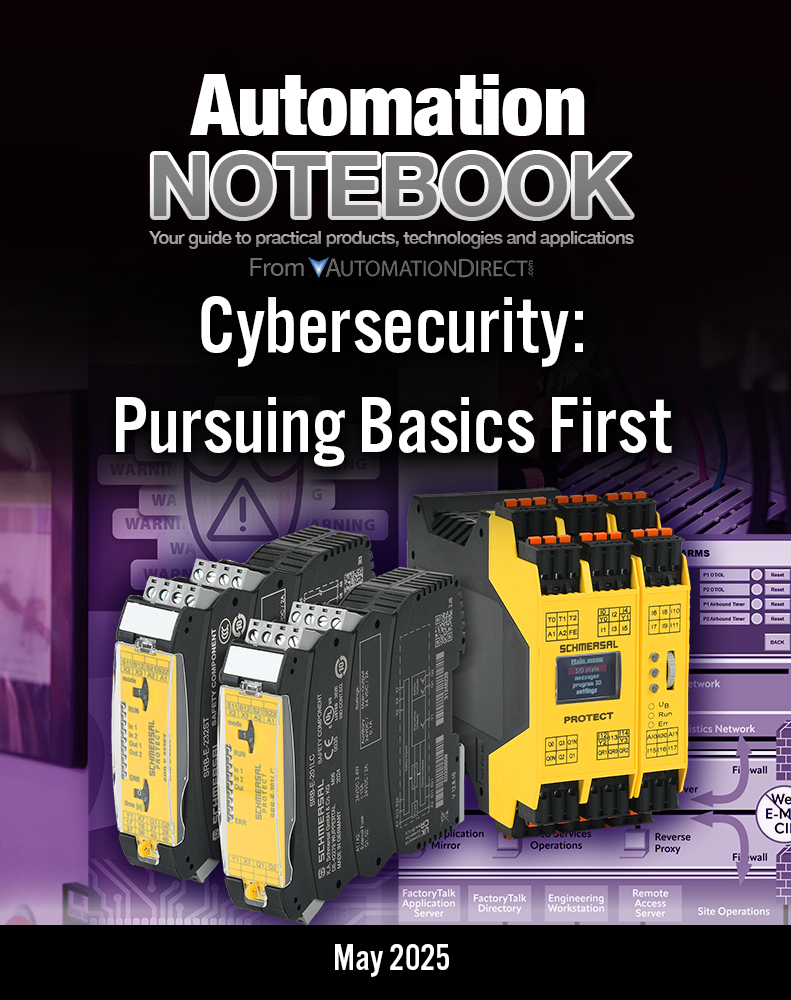
Highlights
- Cybersecurity Basics
- Celebrating Safety Month
- Explores the technology used to detect hazardous conditions
- Efficiently update your pump systems
In the world of manufacturing, efficiency and productivity often take center stage. However, there’s one element that must always be prioritized above all else: employee safety. Recognizing that June is National Safety Month, AutomationDirect is dedicating much of this issue of NOTEBOOK to addressing the issues that impact safety in the manufacturing workplace — from culture to the tools and techniques that ensure machine operators don’t get injured on the job.
In this issue of the Automation Notebook…
Because industrial automation systems often remain in service for decades, it is important to select a hardware/software supplier and integration specialist familiar with performing incremental updates as needed. By: Randy Ames, Ames Electrical Consulting, Inc. Repair or replace: a conundrum familiar to owners of appliances, consumer electronics, cars, homes, and also industrial processing facilities. For…
Many industrial automation end users are not staffed to deploy cutting-edge cybersecurity provisions, but they all will benefit from performing attainable and practical basic steps. By Tim Wheeler, AutomationDirect Albert Einstein said, “Genius is making complex ideas simple, not making simple ideas complex.” Modern cybersecurity is an example of an extremely complex subject, where a…
+Tech TopicsHand Tools &Test EquipmentIssue 55, 2025Learning ResourcesNotebook IssueProductTech Thread
Outfitting Your Panel Shop to be Safe and Efficient
AutomationDirect has created an extensive portfolio of professional-grade control panel products, tools, and test equipment, all readily available at reasonable cost so that shops can equip their technicians to deliver high-quality results. By Zach Ganster, AutomationDirect The “good/better/best” concept is familiar to most people. When it comes to obtaining anything we use in our daily…
This student team gained valuable STEM experience by developing an underwater remote operated vehicle, and they accelerated their efforts by using commercially available industrial-grade components. By: Geoff Gardener, North Paulding High School Exploration of both the deep sea and of outer space share a lot in common. Both are extremely unforgiving environments where it is…
By Travis Morris, Safety Administrator, AutomationDirect As we recognize National Safety Month this June 2025, it’s the perfect time to reflect on how industrial safety has evolved alongside technological advancement. At AutomationDirect, we’ve seen firsthand how the safety landscape in manufacturing and logistics continues to advance rapidly, creating both new challenges and unprecedented opportunities for…
By: Larry Reynolds, AutomationDirect Safety systems play a crucial role in industrial equipment, protecting personnel, guarding against machine damage, and minimizing unscheduled downtime. To make a machine totally safe, we could build a wall around it, cut the power, send staff home, and lock the doors after them. That approach isn’t particularly practical, however. Instead,…
Polka Dot Remainder Find the area of the blue shaded portion in each figure below: Area Sensors Speaking of Area – did you know that AutomationDirect offers multiple types of Area Sensors? Also known as Measuring Light Grids, these sensors can detect the presence of an object within the grid, AND measure that object’s height….
February 26, 2025 – AutomationDirect has added new specialty modules for the CLICK PLC family. CLICK PLUS CPUs offer the utmost versatility with up to two option slots for custom I/O configurations. These option slots also allow for specialty modules, including the C2-DCM serial communication module and the new C2-NRED and C2-OPCUA modules. The C2-NRED…
February 26, 2025 – AutomationDirect has added the new Titanio series of stepper drives from Ever Motion Solutions®. These drives offer peak performance, a rich feature set, and work seamlessly with AutomationDirect SureStep® stepper motors. Three new drives are available with two open-loop (no encoder feedback) models and one open/closed-loop version (a motor-mounted encoder provides…
February 12, 2025 – AutomationDirect has added BLOCK CT and USTE series open core control transformers to provide a flexible solution for stepping down a wide range of voltages from 208 to 600 VAC. The BLOCK CT series is made in the USA and offers a rugged design specifically engineered for isolation, lighting, or signaling…
February 5, 2025 – AutomationDirect has added general-purpose WEG CFW320 AC drives and full-featured SSW900 soft starters. The CFW320 series VFDs offer all the features of the existing CFW300, including a compact size, a built-in operator interface (HMI), and an embedded SoftPLC, but provide support for 460 VAC and Ethernet communications. These drives support 230 VAC 3-phase…
January 29, 2025 – AutomationDirect has added Gladiator GPB1 and GPB2 series enclosed-style terminal blocks to provide a safe and reliable way to connect multiple electrical circuits to a single power source. The GPB1 series terminal blocks are ultra-compact, offering time-saving multiple wire connection options for a variety of control panel applications. Push-in spring connections…
January 22, 2025 – AutomationDirect has added configurable and programmable safety relays from Schmersal. Many safety systems require more than one specialty safety relay but do not justify the need for a safety controller. Schmersal PROTECT SRB-E configurable relays are easy to set up and reduce the number of safety relays required for a machine…
January 22, 2025 – AutomationDirect has added Dold VARIMETER series voltage and phase monitoring relays to safeguard electrical equipment and prevent costly downtime by evaluating voltage levels and phase sequences. These relays provide early detection and response to abnormalities such as undervoltage, overvoltage, phase loss, phase reversal, and phase imbalance. The VARIMETER series monitoring relays…
December 18, 2024 – AutomationDirect has added more Captron capacitive pushbuttons that utilize touch control and are activated without pressure when a hand or body part nears the device’s surface. They feature a robust IP69K design, wear-free operation, resistance to water, oil, and harsh environments, and are available in various mounting/operator sizes. Caneo Series10 additions…
December 18, 2024 – AutomationDirect has added four new series of Lika Electronic rotary encoders each with unique features or applications. Linear measuring wheel encoders are also now available. The new A41 series are compact (41mm diameter body) medium duty encoders with hollow or solid shafts and resolutions from 100 to 3600 PPR. A50 series…