Solar thermal installations need advanced control systems to optimize energy harvesting, storage, and distribution at remote mining operations.
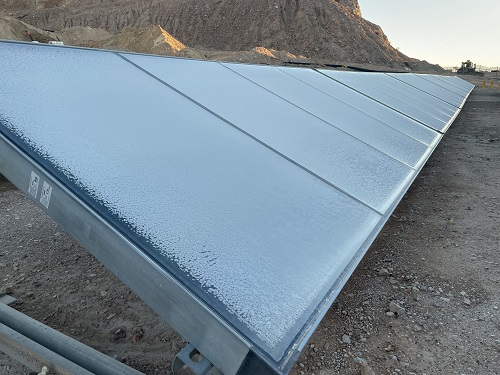
For certain applications in the right geographic areas, solar thermal can be a cost effective and low carbon way to supply large-scale heat energy. Flemming Jørgensen, of Jorgensen Thermal solutions, supplies these systems, and he needed to develop a control system capable of maximizing heat production, while efficiently managing the distribution of heat to a variety of processes.
Jørgensen recently wrote a Control Design March 2024 article titled PLC-Based System Controls Solar Thermal Installation in Mexican Mining Operation, describing how he used AutomationDirect PLCs to implement this type of project at a remote mining facility in northern Mexico.
Gathering Heat From the Sun
The mining facility uses electrowinning to extract metals from ore, and this process requires a tremendous amount of heat energy. Because the mine has plenty of land and nearly 3,000 sunshine hours available per year, solar thermal generation is a great fit.
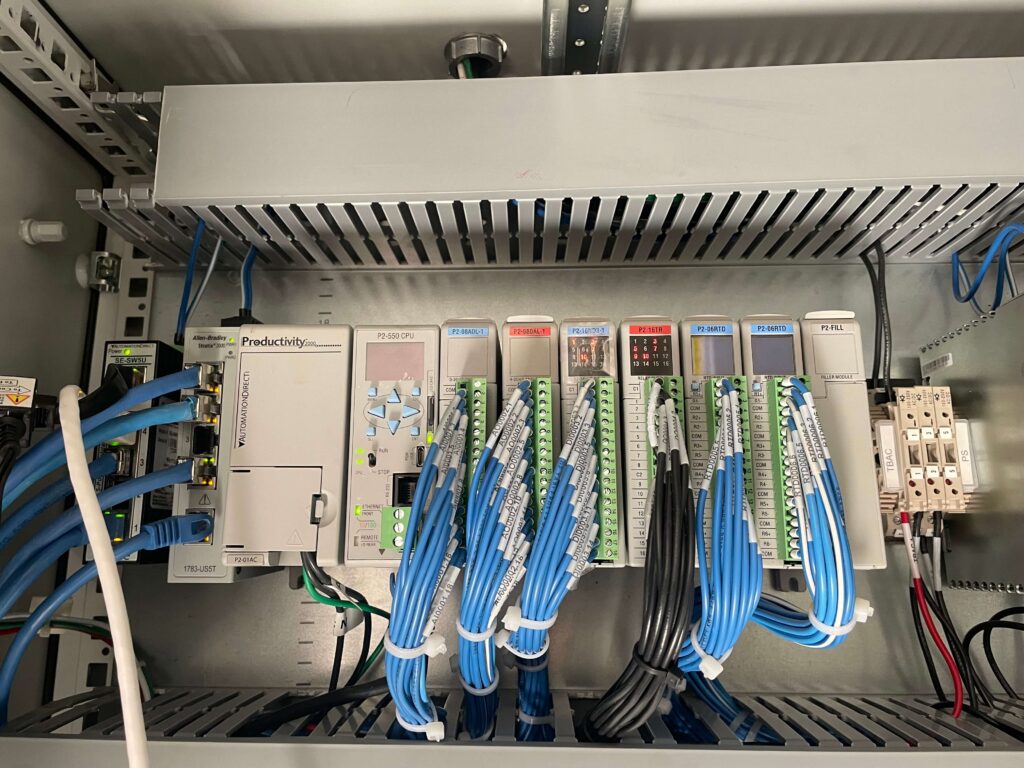
Unlike photovoltaic (PV) systems, which generate electric energy, a solar thermal system circulates a fluid through flat plate collectors, and then pumps this fluid through a heat exchanger to transfer the energy for storage and usage elsewhere.
Jorgensen developed the S200 automation system based on an AutomationDirect Productivity2000 micro-modular PLC and a C-more 15” HMI. While automation of consumption/distribution systems and electric backup were straightforward using traditional logic and closed loop feedback control, the solar thermal system was more complicated.
Automation of the solar thermal system needs to be reactive to the dynamic needs of the facility, and flexible to handle off-peak conditions, changing weather, and nighttime hours. Feedforward control principles are used to anticipate system needs by optimizing the output, and this requires simulating conditions based on solar radiation, ambient temperature, and other variables. Without using these advanced calculations, the system would not be able react quickly enough to meet heat energy demands.
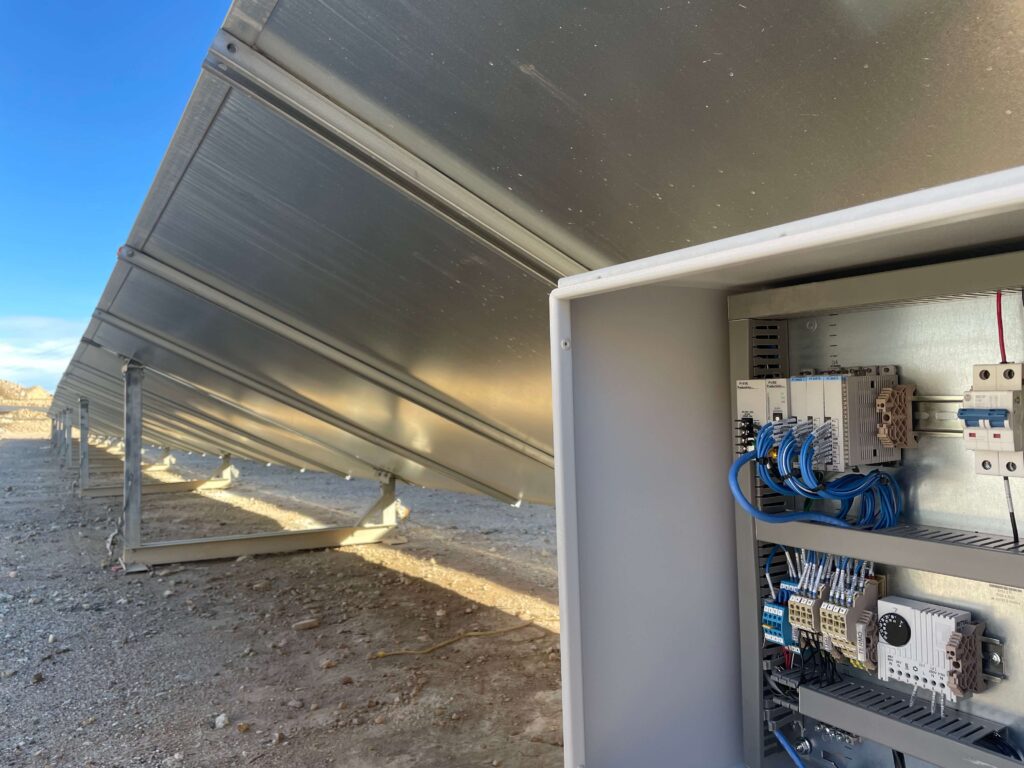
To guarantee uninterrupted operations, an insulated water tank stores hot water so it can be distributed throughout the facility as needed. Temperature, pressure, level, and flow sensors distributed throughout the distributed facility are monitored by the PLC via remote I/O, minimizing the amount of required local field wiring. A PLC-based PID loop controls the water distribution system, and the logic operates VFDs as needed to maintain pressure.
The touchscreen HMI provides clean and streamlined graphics, developed with an emphasis on intuitive and easy use by the many operators throughout the facility.
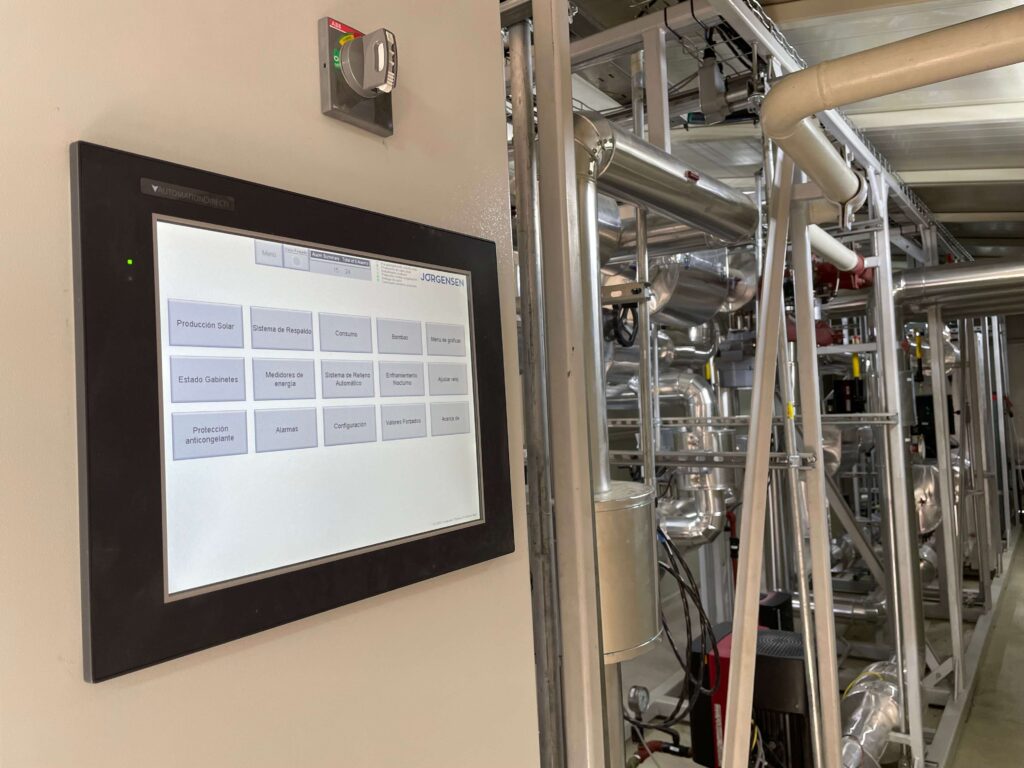
During the design phase, there were some challenges obtaining parts from various vendors due to the global supply chain crisis. One unique attribute of AutomationDirect is their consumer-facing website with transparent stocking level information, which Jorgensen used to ensure needed parts were available.
They were able to view real-time inventory levels on the AutomationDirect website and select components that had the best availability for their project timeline.
Like many other manufacturers, OEMs, and systems integrators, Jorgensen relies on AutomationDirect to deliver high-performance automation hardware and software so they can implement successful projects for their clients. Visit the AutomationDirect.com website today to discover a massive portfolio of products available to support your projects.
All figures courtesy of Jorgensen Thermal Solutions ApS and Flemming Jorgensen SA de CV, www.jorgensen.com.mx