Most plant floor workers already carry mobile devices, so using them to access, control and monitor equipment is a natural next step.
The September 2018 issue of Control Design magazine featured a cover story spotlighting new and better ways for delivering a mobile industrial operator interface experience. Titled A Better Interface, the article presented input from hardware and software suppliers, and from system integrators, describing how they are moving to mobile for industrial automation applications, and that story is adapted in the following sections.
Office workers commonly have one or more mobile devices close at hand, and the trend of companies endorsing a bring-your-own-device (BYOD) policy is growing. As mobile becomes blended for personal and business purposes, it is inevitable that industrial plant floor workers will continue to follow suit and use the technology for human-machine interface (HMI) control and monitoring of machines (Figure 1).
As a result, mobile technology is making industrial systems more usable and even social, enabling productive worker collaboration.
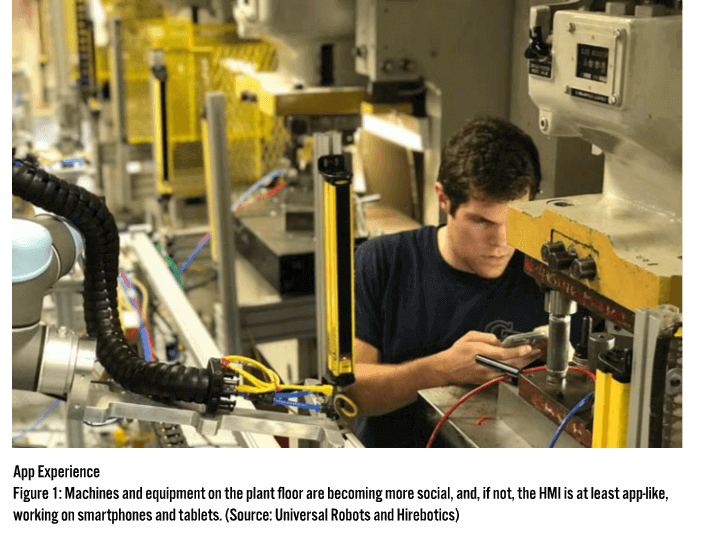
Fingertip Control
Systems integrators tasked with applying the right technology to deliver results are right where the action is. “Think about the computing power readily at hand when using smart phones or other mobile devices loaded with apps,” says Hayden Serio, senior engineer at Maverick Technologies, headquartered in Columbia, Illinois, and a member of the Control System Integrators Association (CSIA). “In addition to phone calls, email, text messages and pictures, these devices can be used for taking notes, downloading documents or even digitally entering and storing round sheets, among other capabilities. Why not take it a step further and use mobile-app technology for real-time data analysis and reporting, system monitoring, diagnosing and troubleshooting potential problems?”
Serio goes on to describe how mobile applications can influence reliability programs. “As automation professionals make the rounds using mobile technology, they can make informed data-driven decisions in real time about manufacturing systems and processes, improving overall operational efficiency,” he notes.
Today’s operators already comfortably consume information using personal mobile devices, so using those as HMIs is a natural step, points out Rob Goldiez, co-founder of Hirebotics in Nashville, Tennessee, a certified system integrator (CSI) of Universal Robots. “Our users consume machine status, production data, quality data and much more,” says Goldiez. “We have the ability to convert machine status into human readable messages that are delivered in real time via push notifications”
(Figure 2).
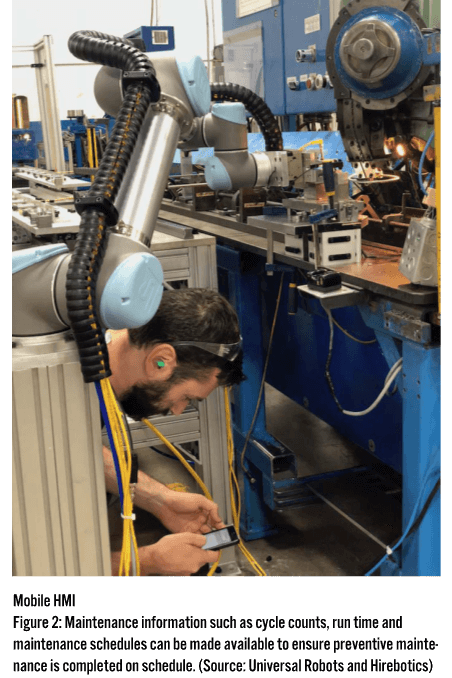
No Time Like the Real-Time
“With mobile apps, real-time data can be delivered to associates in real time, wherever they are,” according to Nate Kay, project manager at Martin Control Systems in Plain City, Ohio, a CSIA member. “They no longer have to be standing in front of the machine to access this data. If there is an issue with a machine, it is often possible to troubleshoot that issue before setting foot on the plant floor. This can speed up recovery and minimize downtime.”
Mobile apps enable operators and maintenance personnel to work almost anywhere and access the information they need. “The operators can control equipment while being near it,” points out David J. Stock, president at Innovative Control in Algonquin, Illinois. “It also reduces foot traffic needed when constantly returning to a control room and provides the capability of monitoring the process from any location within a facility.”
Mobile devices also enable other extended options. “The device can have additional functionality by leveraging barcode scanning and RFID technology,” adds Stock. “We leverage this to confirm operator presence, even to issue commands to the system. For process control, users can stay with the process and be connected to the same information and functionality that a control room would have.”
Built for Users
“Small, handheld mobile devices can show users, such as operators or managers, what they and the engineering and technical teams need to know,” continues Stock. “But this should be handled completely differently compared to control room SCADA/HMI displays. The displays should be designed/architected for their size and purpose—primarily focusing on text-based views instead of equipment graphics or P&ID-based views. Focusing on a more text-based design enables the maximum usage of the small footprint, allowing several pieces of information to be displayed, and interfaced with, rather than just equipment status.”
In most cases, typical HMI/SCADA navigation styles should not be applied directly to mobile apps, which instead should be designed to improve focus on important information, according to Stock. “Mobile-app navigation should flow intuitively to minimize training and button clicks. Typing on the mobile devices should be minimized, as well. Barcodes and QR codes reduce errors and operator frustration,”
he concludes.
Using contemporary high-performance HMI methods to minimize distracting objects and colors is key for displaying critical equipment information, explains Serio at Maverick Technologies. “Using these HMI techniques helps users to view the important information they need on small, handheld mobile devices.”
Useful information is not the same as raw data. “It takes analysis and interpretation to make data valuable,” explains Serio. “Trending is one way to visualize data over time and allows you to analyze recurring patterns and go beyond the current machine status. Being able to see multiple measured parameters over time will allow users to use their experience to make informed decisions
about equipment.”
Far greater value can be realized by analyzing many similar systems networked from different plants, processes and machines, claims Kay at Martin Control Systems. “For example if I only analyze the data on one machine, that tells me a lot about that individual machine,” he points out. “However, if I correlate the data from many machines and compare that data with data from across the company, then I can start asking and answering questions such as: How can I improve my overall process? What are areas where efficiency can be improved? How can I improve efficiency? What are the causes of downtime? Why does Machine A seem to run better than Machine B?”
Collaboration is the Next Step
“Machine-specific information related to geospatial location, technical information and current and historical alarm status of the connected machines can all be weaved together via a configurable dashboard application and can be customized as needed for specific user roles and scenarios,” asserts Mike Malone, principal of Technotects
(www.technotects.com) in Harleysville, Pennsylvania (Figure 3).
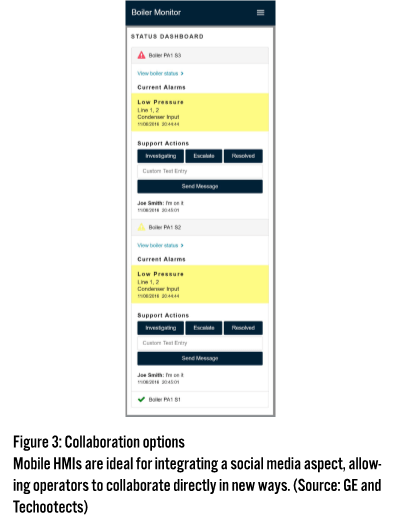
“These applications automatically scale to the size and shape of the mobile device, allowing the user the freedom of using BYOD. Mobile machine apps typically have a social media aspect to them, as well. The various team members that are tasked with supporting the machinery can interact and collaborate directly through the apps using simple text-messaging or through videoconferencing technologies such as with Facetime and Skype. These interactions are then logged into the case that gets created for the downtime condition. When confronted with a similar case in the future, technicians can quickly review the case and determine how the issue was resolved previously. It’s all about improving the productivity on the plant floor”.
Any Time, Any Place
“Mobile applications are well suited for communication with many different devices,” points out Serio at Maverick Technologies. “Wireless protocols, such as Wi-Fi and Bluetooth, make connectivity quicker and cheaper to obtain than older hardwired methods. Couple this with the Industrial Internet of Things (IIoT) technology, and you can create connections to machines, processes and plant systems very quickly. With the IIoT, the sensors and controllers that monitor and control industrial equipment have connectivity built-in; therefore, end users can connect to them via the manufacturer’s mobile applications. Sometimes, they can even connect via a simple Web browser. It is critical to keep cybersecurity in mind as increased connectivity comes with a greater responsibility to protect these connections from cyber-attack.”
Information technology (IT) workers commonly make use of virtual private networks (VPNs), virtual local area networks (VLANs), industrial demilitarized zones (DMZs) and firewalls. These same IT technologies are now regularly applied on the back end for operations technology (OT) use, according to Kay at Martin Control Systems. “On the front end, many HMI and SCADA software packages have a mobile app plug-in for quick access,” he explains. “These apps make it possible for end users to quickly select the machine, process or plant they want to access using their mobile device.”
Security Requires Careful Attention
“All devices on networks, including control systems, have some inherent security risk, whether or not mobile apps are used,” cautions Kay at Martin Control Systems. “However, if designed properly security risks can be minimized. Anytime we shop or do banking online, there is some security risk. Yet many people still shop on Amazon and check their bank accounts using their mobile devices as the risk is small compared with the benefits. Additionally being able to monitor and access your data in real time through things like mobile apps can increase security in the same way that a credit-card company can alert you to fraud by monitoring your data.”
One crucial consideration is that many industrial automation systems, even if mobile connectivity has not been implemented, may already have unexpected risks for cyber-attacks, explains Scott Cunningham, product and application manager, controls and automation, at KEB America. “Many machines reach the Internet, either intended or unintended. ‘Was that old machine just connected to a production PC, which happens to have internet access?’” he asks. “It is important that the production floor also has security infrastructure in place as a baseline.”
One approach to incorporating mobile connectivity is to use dedicated devices configured to be isolated from the internet and business networks, according to Stock at Innovative Control. “Or don’t allow equipment control and sensitive material to be available on the mobile app,” he says. “If outside network/Internet is required on the mobile device, this would require a DMZ bridge between the automation system and the business/Internet to further prevent possible intrusion and viruses.”
Cybersecurity should always be a prime consideration, maintains Serio at Maverick Technologies. “Any connected system should have it built into its design,” he instructs. “Hoping for ‘security by obscurity’ is no longer a valid approach to cybersecurity. IT managers should start with a robust network-security architecture that incorporates defense-in-depth strategies, as well as smart-domain policies. Over the past several years, however, mobile technology has matured so that more security options are available. The arrival of the Internet of Things and the Industrial Internet of Things has pushed manufacturers to integrate security down to the device level, rather than relying solely on secure infrastructure.”
Making an HMI Mobile
Mobile HMIs should maintain consistency with typical apps for best operator acceptance. “We use mobile apps, as well as desktop access to Web servers embedded in the equipment,” explains Rick Lamb, president at Midwest Technology Ventures, a technology-focused system integrator in Indianapolis. “In fact, I’m setting up a client project right now with mobile-app access. It’s a material call application in an engine-assembly plant. Wireless pushbuttons are located in the assembly cells, wherever it’s ergonomically convenient for the operators. They push a button, and it sends a material call signal for the specific part they need.”
“There’s an iPad in the assembly area, allowing operators to view the material call status,” adds Lamb. “Material handlers have iPads on their forklifts, as well. They see a queue of the materials needed. When they go to the storage area, somebody has already picked those materials for them based on the assembly line calls, so the handlers can quickly deliver needed material to the workstations.”
In this case there is no dedicated mobile app, because web server code generates the user’s iPad view. “The material call system is pretty much custom-coded; data is kept in an Oracle database; and the material requisitions are interfaced to the warehouse/inventory management system,” Lamb explains. “The server is a virtual server in the IT department; it serves up the Web pages to the iPads.”
Apps Provide HMI Advantages
The traditional plant floor filled with a variety of purpose-built HMI devices already raises concerns, points out Malone at Technotects. “The security risk and support headache associated with patching and maintaining all of these HMI devices is becoming troublesome,” he notes. “A well-designed mobile application, which connects and collects all of the plant-floor machinery data into a single, simple-to-use user interface, will undoubtedly improve manufacturing productivity and unshackle the operators from their installed HMI screens and associated logins. The use of mobile-device apps has drastically improved consumer and commercial productivity, and it is just common sense that the industrial space will benefit just as well. Just as a driver can navigate around trouble spots on the highway using GPS-guided and crowd-sourced apps such as Waze, thereby improving his personal productivity, a process technician can avoid upstream issues and save a batch by rerouting the process. Having access to critical machine and process data and getting immediate alerts on your mobile device regardless of your location is key to reducing downtime and improving overall productivity.”
Check out the rest of Automation Notebook Issue 42, 2019