Whether pumps are automated with hardwired controls or PLCs, designers can provide enhanced functional and protective features using control and monitoring relays.
Lenny Filipkowski, Product Manager at AutomationDirect, wrote an article for the August 2021 edition of Process Instrumentation magazine titled Exploring Options for Process Pump Automation. Pump control is a common application used in many processing and manufacturing industries, so it is important to understand options for providing the best functionality, protection, and visibility.
Process Pump Automation
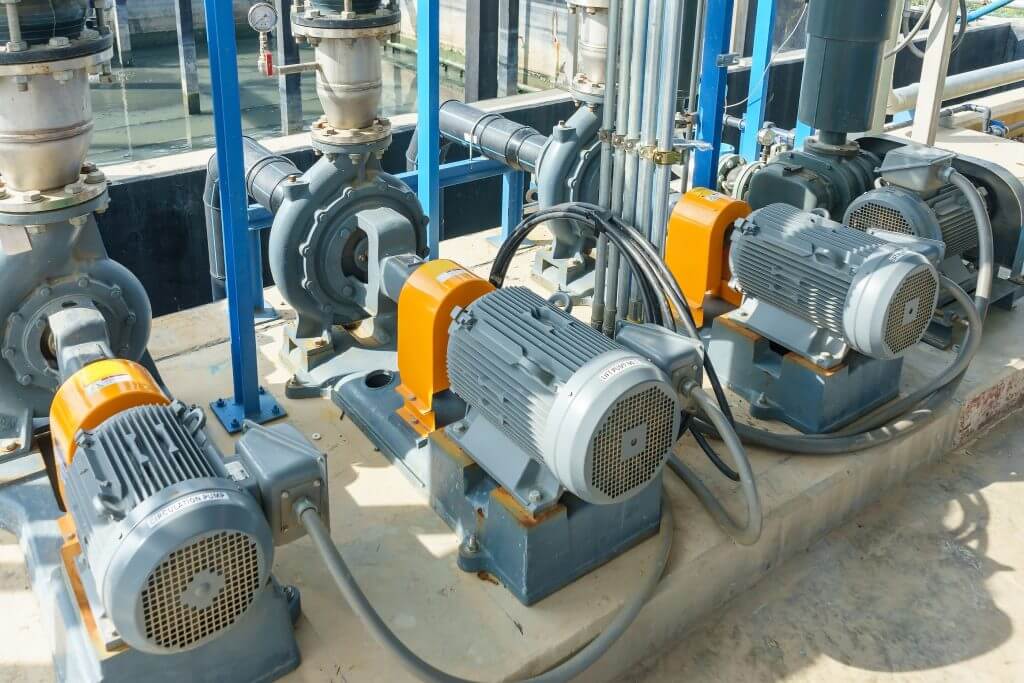
Pumps, whether they are used for basic drainage sumps or for advanced processing operations, are the workhorses of industry. While many applications are progressively relying on digital automation for advanced functionality, there are many good reasons for integrating just the right amount of local hardwired controls to achieve the best overall solution.
Here are some typical functional and protective features needed for industrial process pumps:
- Alternating operation
- Seal failure monitoring
- Electrical monitoring
- Intrinsically safe signaling
Smaller systems may only use hardwired operation, while larger systems are more likely to include PLCs. Regardless, there are many reasons to incorporate mission-specific relays for each of the functions listed above.
Alternating Relays
Many mechanical systems use two pumps. An alternating relay responds to the start signal and takes turns starting one pump or the other to equalize runtime.
Seal Failure Relays
Some types of pumps are submersible for convenient operation and cooling. However, the shaft seals can leak, which will lead to a failure unless a proper sensor and associated seal failure relay is used to alarm or interlock upon detection of this condition.
Phase-Monitoring Relays
Three-phase electrical motors are often used to drive pumps. These motors can be subject to electrical problems—like phase reversal, phase unbalance, undervoltage, overvoltage, and single phasing—which can lead larger issues if not addressed quickly. Phase-monitoring relays can detect some or all these conditions, and their outputs can be used to stop, or at least provide alarm indication, for the equipment.
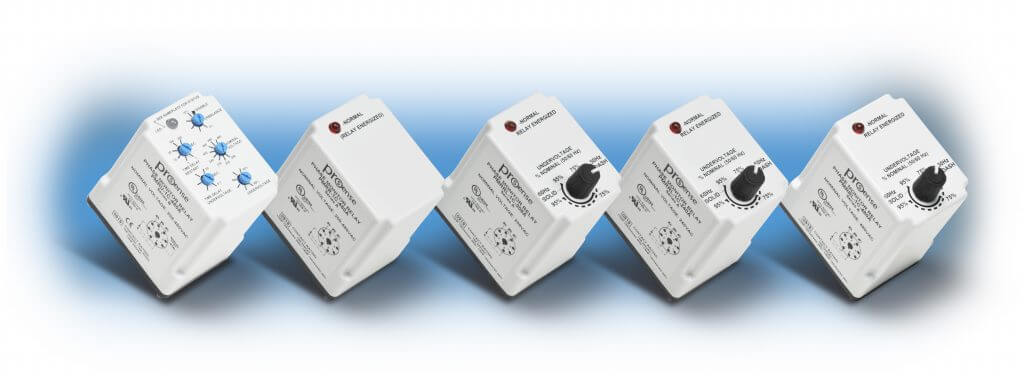
Intrinsically Safe Signaling
If pumps are located in hazardous locations where explosive vapors may be present, designers need to follow the National Electrical Code and any other standards for the signal wiring. Intrinsically safe relays act as an energy barrier by permitting signaling while protecting against ignition.
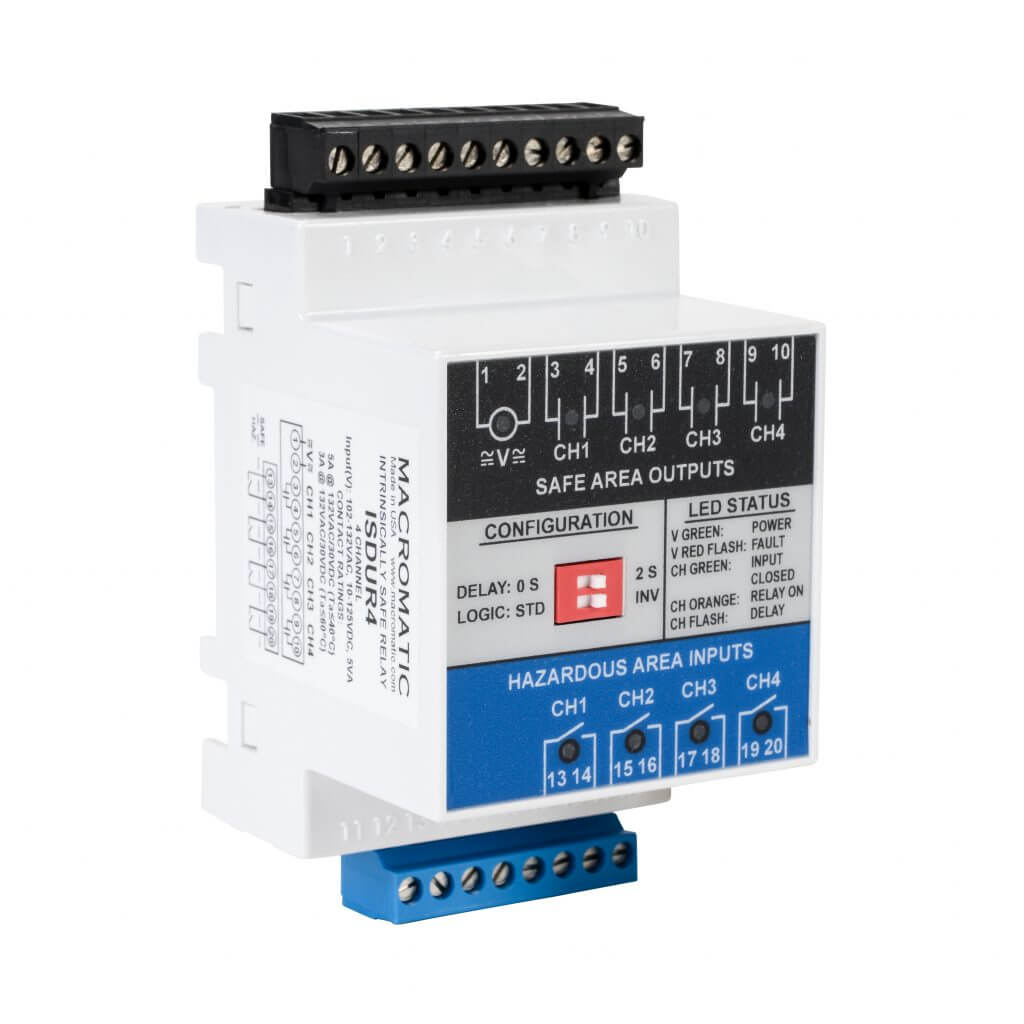
Enhanced Pump Protection
Pump control and monitoring relays are convenient for many reasons:
- Provide a local and simple method of control for maintenance personnel inspection and troubleshooting.
- Minimize downtime by equalizing equipment runtime and providing early trouble indication.
- Perform intelligent operating decisions to keep processes running.
- Allow OEMs to standardize on equipment protection methods.
Relays are an economical way to provide a consistent interface with electrically driven pumps, which in turn can be operated by any type of hardwired or digital controls.
Providing the right combination of relays for pump control applications improves designs, leading to simpler operations and maintenance.