Let’s say you have a system with some Variable Frequency Drives (VFDs) and you want to integrate those VFDs into your emergency stop circuit to ensure the VFDs will place the motors into a safe state upon an emergency stop condition. How do you do this? There were many ways this was done before advanced safety features were available and while some methods worked, some were unreliable. Some methods were not fail-safe and others could cause serious equipment damage. However, there is a safety feature available on newer, higher quality VFDs known as STO or Safe Torque Off.
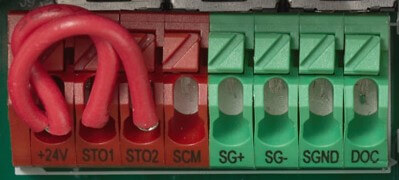
What is Safe Torque Off?
Safe Torque Off, known as STO for short is a safety feature on newer VFDs that turns off power on the VFD output to prevent the motor from producing torque. This is done through the VFD’s hardware to ensure fault tolerance. STO is considered an emergency stop method that will cause the motor controlled by the VFD to coast to a stop.
How Does STO Work?
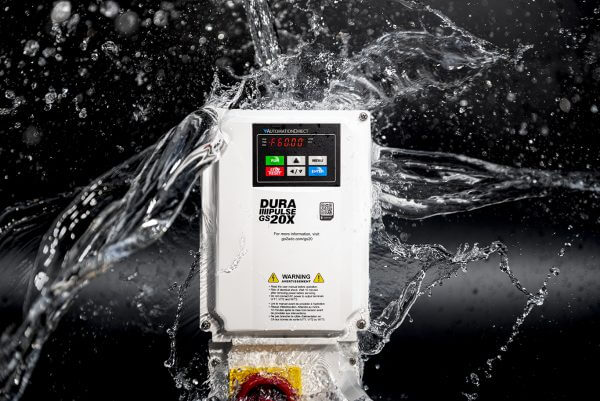
How STO works is by prohibiting the IGBT output circuits from sending current to the motor, by opening up the STO safety circuit, which is connected directly to the gate of the power device. Since the power device cannot turn on there is no current to the motor, so no torque is produced by the motor. However, it is important to note that the output circuit of a VFD is comprised of solid-state components and the circuit will not physically open, so voltage may still be present at the output terminals. Since the STO circuit is accomplished with and through the hardware design and software is not involved, it is also considered fail-safe.
Typically STO is triggered by a dual-channel, normally closed circuit, on the VFD. If one or both of these channels opens then STO is activated and the VFD will be prevented from sending current to the motor; the motor will not produce torque and the motor will coast-to-stop. After STO has been activated the VFD will be prohibited from restarting until the STO circuit has been reset (both channels closed) and a reset/restart sequence occurs such as a reset signal is applied, and the VFD restarted or the start signal to the VFD is removed and reapplied.
STO is a preferred choice as an emergency stop method for a VFD as opposed to what was done externally to the VFD before an STO feature became available. In the days before STO there were a few different options. Engineers and designers would use one or a combination of several to make their systems safer.
Other, Less Convenient Ways of Incorporating a VFD E-stop
One option was to wire in a contactor upstream of the input circuit to the VFD and have this contactor switched from the emergency stop circuit. This would remove power from the input side of the VFD and eventually the VFD would coast to a stop. However, the drawback here is that VFDs do not immediately power down when input power is removed. This can take several seconds or even longer depending upon how long it takes the DC bus capacitors to discharge completely; much could go wrong in the time it takes for this to happen, thus it is not fail-safe and considered ineffective.
Another option was to use the emergency stop circuit to remove the run signal or open the normally closed stop signal to the VFD. This would allow for a controlled stop of the VFD, but not fault-tolerant as the stopping relied on the software of the VFD to be operational and not corrupt.
A safer method for an E-stop in the days before STO was to wire a contactor on the output of a VFD so the circuit between the VFD and motor can be broken; this method also consequences. This method would indeed remove torque from the motor immediately, and allow a cost-to-stop action, but could damage the VFD circuitry in the event of an E-stop; opening the output circuit of a VFD while it is running with a load connected can cause permanent damage to the VFD. This method was effective and fail-safe to protect personnel but could require the VFD to be replaced at any time there is an E-stop.
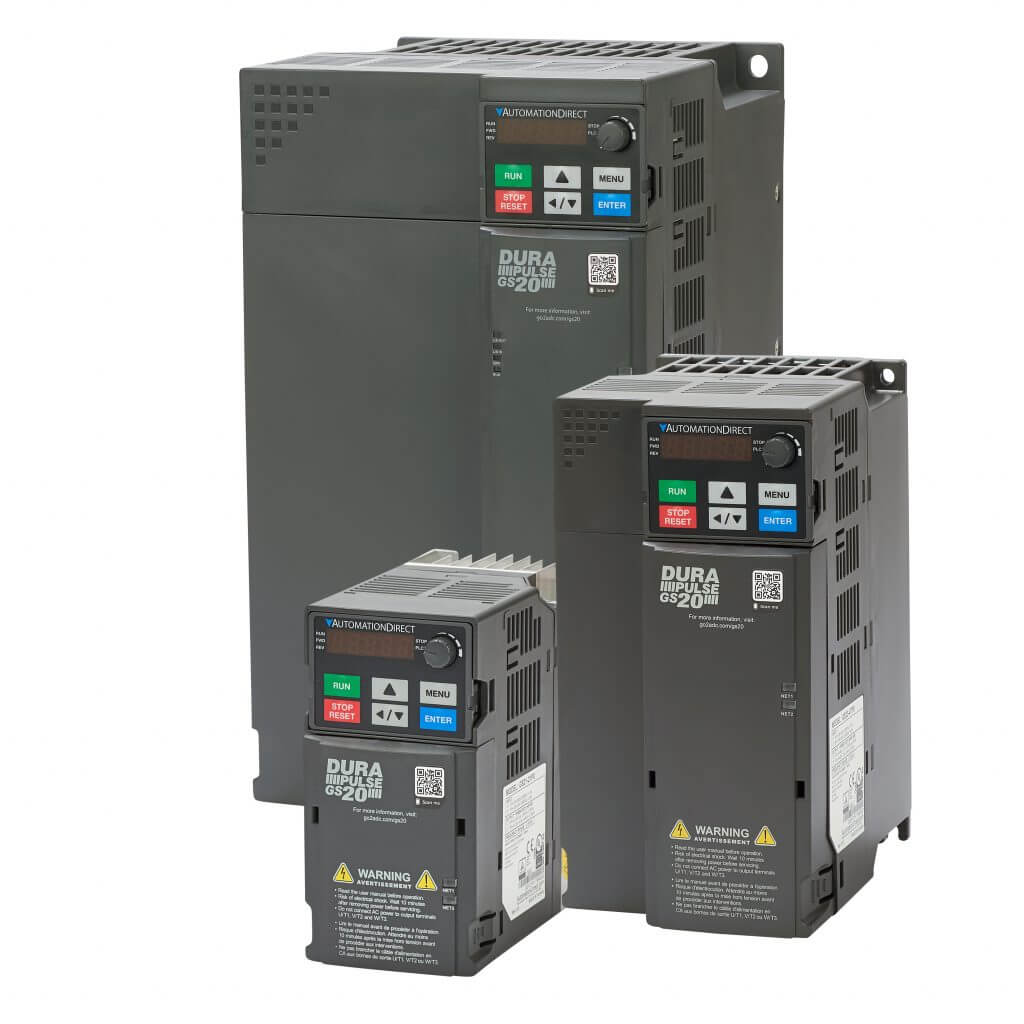
STO is a great choice to be used as an emergency stop for motors controlled by a VFD when a coast-to-stop condition will not endanger personnel. Be mindful that STO just disables current from being sent out of the VFD output which prevents the motor from generating torque, which causes a coast-to-stop condition. Sometimes a coast-to-stop method is not safe for personnel in some installations and a controlled stop will be required.
- In these cases, additional circuitry would need to be designed to put the VFD in a controlled stop mode before triggering the STO function.
- Additional care would need to be taken into account as to what happens if this circuitry fails, and/or consideration could be made as to the addition of motor braking to stop motor rotation.
- STO only prevents current from being sent to the motor and voltage may still be available at the output terminals.
Because the risk of shock or electrocution still exists when STO is active, STO should not be used when performing maintenance on a motor connected to a VFD. A proper local disconnect and/or powering down the VFD completely is recommended. Please check your local code when designing for safe maintenance practices. The STO input circuit is a dual-channel circuit and has tight tolerances for when these two individual circuits close. A safety relay with a dual-channel output, as opposed to a general purpose relay is recommended for this purpose.
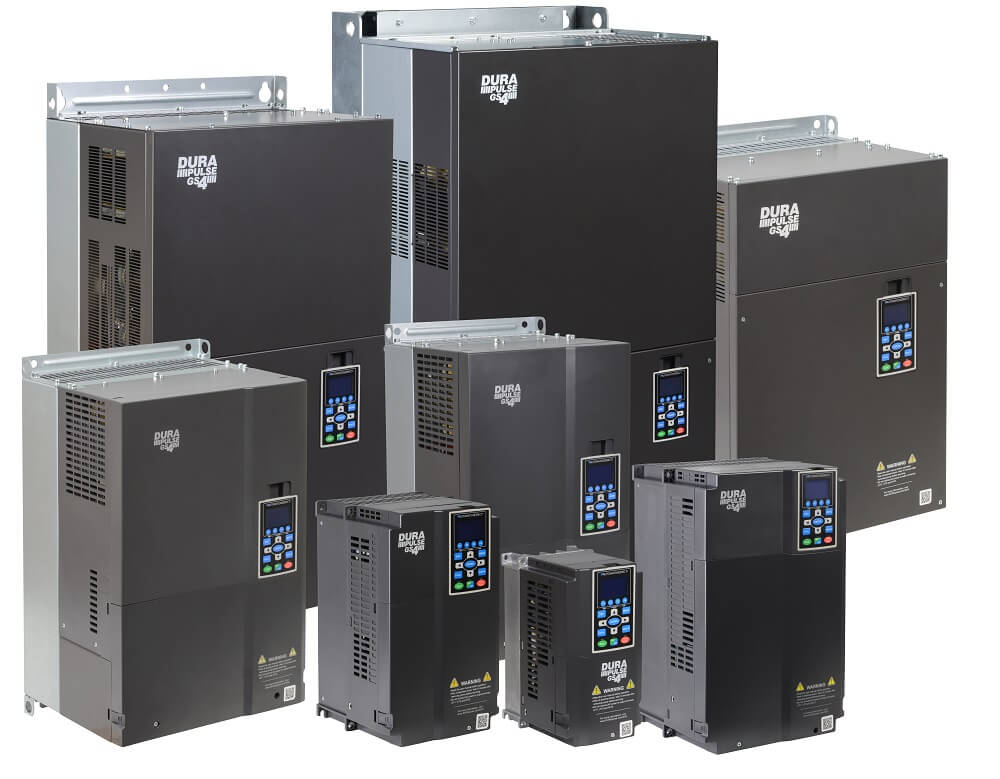
By selecting a VFD that has an STO function that has been tested and certified by a nationally recognized test lab (NRTL), such as TÜV Rheinland, it will be easier to design your safety system. Once a risk assessment of your facility is performed it will determine what SIL, PL ratings and Category are required to minimize risk to your personnel. Then you will know the minimum ratings needed for the VFD you select.
Safe Torque, STO, is a great safety feature found on new variable frequency drives such as the general purpose DURApulse GS20 or the high performance DURApulse GS4 available from AutomationDirect. AutomationDirect has been selling VFDs, PLCs and other industrial automation products since 1994. We offer FREE shipping on every order from us. FREE technical support is included for all products that we sell and offer a 30-day return policy on most products. You can TRUST AutomationDirect to be a reliable supplier for your VFD needs.