Efficient use of motors is always important, but there are many other things to consider when specifying an electric motor. Mechanical and environmental considerations are on the list, as is the application and operation. All of these factors are important, but the application is where the selection process should start.
How to Select a Motor
The application defines the motor load, speed, acceleration, deceleration and duty cycle of the motor. This all feeds into the horsepower and torque requirements. Control of motor speed and position also determines the type motor used, and defines whether the motor load is constant or variable horsepower and torque.
Applications Drive Motor Loads
Applications drive the type of motor load, and there are four main types in industrial automation:
- variable horsepower and constant torque
- variable torque and constant horsepower
- variable horsepower and variable torque
- positional control or torque control
Gear pumps, cranes and conveyors are examples of variable horsepower and constant torque applications. Constant speed AC and DC motors work well in these applications where the horsepower requirements may vary, but the load remains constant.
A web unwind or rewind machine is an example of a variable torque and constant horsepower application because the load increases with the diameter of the roll and vice versa. DC motors and servo motors work well here, and AC motors with closed loop drives are another option. Consider regenerative power in this case to increase efficiency.
Centrifugal pumps, fans and mixers/agitators require variable horsepower and variable torque. When speed increases, so does the motor load. Variable frequency drives (VFDs) are often used in these situations.
Motion control applications with linear motion slides and actuators often require accurate positional control, and some presses and tension control systems use torque control. Feedback is usually required, and servo and stepper motors are often a good choice.
Pick a Motor
You only need to choose between two classifications of motors, AC and DC, but there are over three dozen motor types used in industrial applications. Fortunately, looking through the AutomationDirect’s Motion Control and Motors online catalogs, you’ll find solutions for most motor applications using servo systems, stepper systems, general purpose and inverter duty AC motors—or general purpose DC motors and gearmotors.
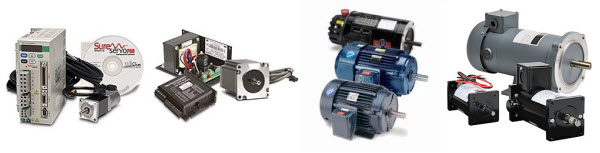
The selection of motors and drives listed and pictured about should cover most industrial automation motor applications.
Some applications need a gearbox to increase torque. To help with motor, drive and gearbox sizing, AutomationDirect has online product selectors and configuration utilities for Sure Servo Complete Systems, AC Motors, SureGear Gearboxes and more. With application and environmental information in hand—it’s possible to calculate load inertia, torque and speed—along with mass and size of the load.
Application Types
Three common motor speed/torque control applications include constant speed, variable speed and torque (or position) control.
Constant Speed Applications
Many applications only require the motor to run at constant speed with no need for acceleration and deceleration ramps. Simple on-off control using branch circuit protection fusing, contactor and overloads are all that is needed to turn the motor on an off. Motor starters, manual motor control or soft starter are also often used.
Common AC and DC motors are suitable in these applications. Both are simple and efficient designs and require minimal maintenance.
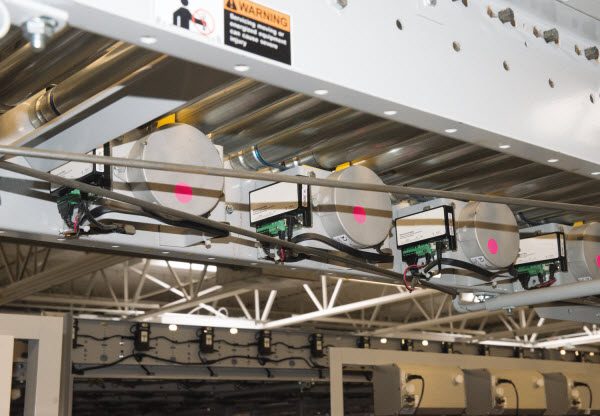
Variable Speed Applications
Precisely controlling the speed of fans, centrifugal pumps, mixers/agitators, conveyors and other loads can greatly increase energy efficiency. The ability to control acceleration and deceleration may also help handle product better, such as on a conveyor, and reduce mechanical issues by being gentler on the motor and drivetrain of the system. Coarse positioning of product can also be accomplished with variable speed control using slowdown and stop photoeyes.
DC and AC motors work well in most variable speed applications. DC drives have been around for over 100 years, and variable speed drives for AC motors have been in use for about 30 years.
DC motors are common used on conveyors and other fractional horsepower applications because they provide full torque at low speeds, with torque remaining constant throughout much of the speed range. Many DC motors use brushes which require maintenance, so keep that in mind or spend a little more money for brushless DC motors, or switch to AC motors and drives.
An AC induction motor with a VFD is the popular choice today. If it is a fan or pump application, this is often the best option, especially if motor loads are over 1 HP.
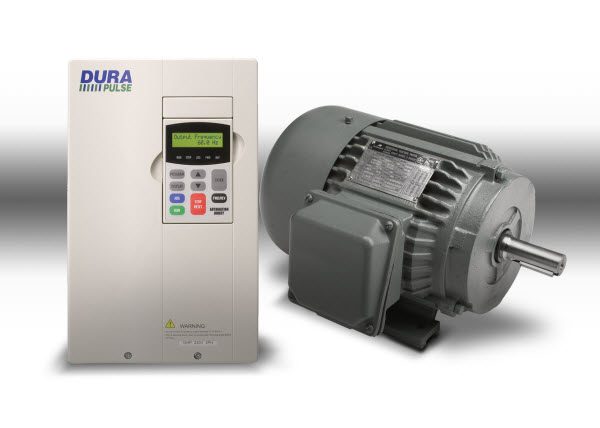
Position Control Applications
Beyond simple constant speed and variable speed applications is motion control. Executing precise position control, and implementing motion profiles with closed loop control, often requires a servo or stepper system. Dispensing applications and moving a linear slide or actuator are examples.
At the low speed end of the precision scale, a stepper system, open or closed loop, is a good choice, especially since the stepper has full torque at zero speed. As speeds and accuracy requirements increase, a servo system is a good choice because it handles dynamic loads and complex motion profiles better than a stepper.
There is a wide choice of AC, DC, stepper and servo motors available for your applications. Identify whether it is a constant speed, variable speed or position control application—and then size and select appropriately using online guidance from AutomationDirect.
For more information, please see the article How to select a motor for an industrial application in the February 2017 issue of Control Engineering.
To read more articles about motors, click here.