2017 proved to be a stellar year for U.S. manufacturing with strong growth in 16 of the 18 manufacturing industries polled for ISM’s December 2017 survey. With machinery and computer and electronic products leading the way, U.S. manufacturing is expanding at a rate not seen in 13 years according to a BloombergMarkets article on the survey.
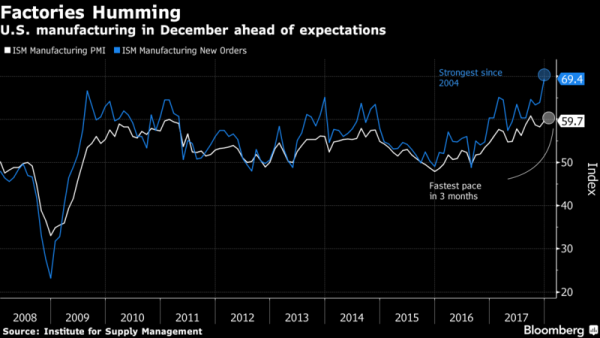
This growth trend is expected to continue into 2018 and will have a direct impact on the industrial automation sector. As explained in the IndustryWeek report on the Future of Manufacturing: 2020 and Beyond, manufacturing leaders are overwhelmingly positive about growth potential but face many challenges including market volatility, rising material costs, price reduction pressures and increasing labor costs.
Industrial automation can be utilized to tackle many of the top challenges these leaders face and is the reason many manufacturers are focusing on modernizing their operations. But what does it take to modernize or better yet what does it cost? Some manufacturers may tend to think big and wind up walking away once complexity and equipment costs begin to mount, but many times automation can be simple, affordable and extremely beneficial.
Keeping it Simple
Since their invention, PLCs have become the go-to control choice for automation projects worldwide. And although there are a multitude of PLC choices and technologies in today’s market, sometimes simple is better, especially when time and resources are limited and the application doesn’t call for the high-end bells and whistles. A simple, straightforward controller can be used to minimize production costs and ensure quality control of small, everyday processes for which you might not have thought of using automation.
For example, let’s say you run a package sorting facility and every holiday season you hire seasonal help for the holiday rush. Your loading dock operates using one outgoing package conveyor and a recirculating conveyor for instances when the outgoing conveyor is overloaded. One rare occasions, during the normal sort, packages are diverted to the recirculating belt using a manually positioned diverter arm. But with holiday sorts, and the extra volume, the diverter arm needs continuous extending and retracting to control the flow of packages to the outgoing conveyor line.
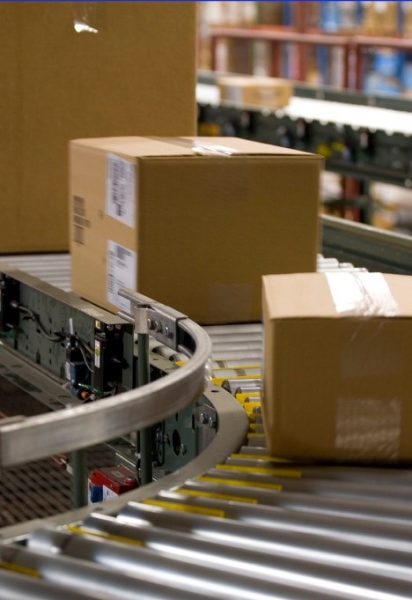
To bring in the additional seasonal help to manually divert packages, you pay $8/hr for the 4-hour sort, Monday through Friday. In terms of labor costs alone, that adds up to a yearly cost (2 months for holiday season) of about $1280 for the first year and over $6,000 after five years.
On the other hand, by simply installing a photoeye to detect the backed-up outgoing conveyor, some pneumatics to position the diverter properly and a low-cost CLICK CPU to control the process, you could save yourself yearly personnel headaches and staffing costs. Let’s look a little closer at the cost associated with this automation.
What it takes…
Here is the Bill of Materials for automating our diverter: (If you aren’t familiar with the convenient BOM feature on our store, you can find it here)
(1) Photoeye emitter (HEE-00-3A) – $38.50
(1) Photoeye receiver (HER-AP-3A) – $55.00
(1) CLICK CPU with power supply (and free software) – $137.00
(1) Pneumatic cylinder 6-inch stroke (A12060SN) – $28.50
(1) Pneumatic valve (AVP-31C1-24D) – $25.50
Total Equipment Cost = $284.50
For a control system with PLC, photoeye and pneumatics the upfront equipment cost would be around $220. Add in tubing, fittings, air preparation, and wiring, and the cost may jump up slightly but we’ll put it at $500. If compressed air isn’t readily available, then adding a small industrial compressor could make the upfront equipment cost bump up to $1300, give or take.
Compare the $1300 ($500 without compressor) first-year-only equipment cost of automating to the $1280 cost year after year of hiring seasonal help, and you can see the difference a simple control solution can make.
“But what about programming?” Well, CLICK PLCs make programming easy. With CLICK’s straightforward instruction set, you could code the sequence of operation in no time. For this example, it took only three rungs and two timers:
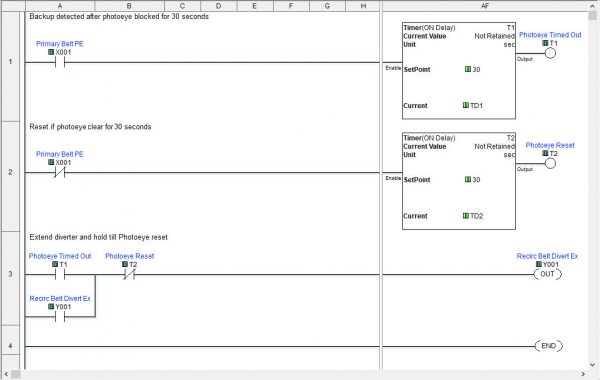
So, whether it’s a simple diverter, turning lights on and off in a stairwell or controlling tank level with pump switching, there are many small tasks all around us that are perfect for simple PLC control. If you’ve never considered automating or maybe you think it is out of your budget and/or expertise, now’s the time to consider what a low-cost, simple automated system can do for you.
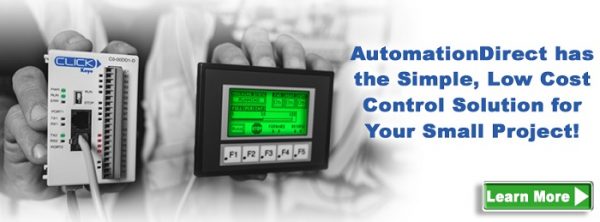
All AutomationDirect content and associated training supplies provided in connection therewith (the “Materials”), are supplied “as is”. These Materials are provided by our associates to assist others in learning the products we sell and service. We make no representation, warranty or guaranty, whether expressed, implied or statutory, regarding the Materials, including without limitation, implied warranties of merchantability or fitness for a particular purpose. We make no representation, warranty or guaranty that the Materials will be accurate, complete, uninterrupted, error free or non-infringing, or are suitable for your particular application, nor do we assume any responsibility for the use of this information in your application. Copyright © 2023 automationdirect.com