Beyond the standard sensor types used in machine automation—such as photo eyes, limit switches and DC proximity sensors—are a wide range of color, contrast, AC proximity and area sensors. All of these sensors, as well as optical rotary encoders, are used to enable sorting, detection, error checking and positioning for machine automation.
Andrew Waugh, Product Manager for Sensor and Safety Products at AutomationDirect, penned an article titled Moving Beyond Standard Sensors, showing how these types of sensors and encoders can help solve your toughest sensing applications. In addition to presenting several less common sensor types available, Andrew details some selection criteria and common uses.
Detect Colors
If color object detection is needed, consider color sensors instead of expensive and complex vision systems.
These color sensors, usually with small spot diameters, reliably detect colored objects at varying scanning distances in automated high-speed applications based on the previously defined (taught) reference colors. Integrated LED technology is often used to create the white light, with automatic adjustment of intensity.
Color sensors can typically provide detection of 3 to 12-colors. For example, an AutomationDirect Wenglor 30 color sensor can reliably and simultaneously detect up to 12 colors. These colors are taught with an “okay” and “not okay” sample, with separately adjustable tolerance thresholds for each color. Other configurations and options are also available.
Color sensors can be configured with single-lens optics or fiber optic cable extensions to provide flexible mounting options at a variety of sensing distances. Single-lens optics use a reflective (diffuse) method to detect color, bouncing the light off the object. When used with glass fiber-optic cables, a sensor can be operated in a reflective mode, as well as a through-beam mode to look through an object.
Andrew suggests using color sensors to measure and check color in painting processes, sort color parts, and detect color registration marks on packages and labels.
Contrast Detects Presence
Andrew describes contrast sensors as photoelectric sensors that evaluate contrast by sensing the red, green or blue (RGB) light reflected by the object when using a suitable light source. The sensor detects the difference in the light wavelength when reflected by an object, a mark or a background.
These sensors use either a white light or an adjustable color RGB light, and have a sensing distance or 6 to 40 mm. The white light sensor’s settings are taught using a target and background color. RGB lights are similarly taught, but can automatically select the optimal color light source for an application during the teach function.
These contrast sensors are used in a variety of industrial applications including paper and printing machinery, packaging lines, and beverage and bottling lines. For example, this AutomationDirect Datalogic contrast sensor with RGB light emission can be used in high-speed, cut-to-length web handling applications to detect the registration mark.
Andrew explains that, due to the detection speed and repeatability of the sensor, they can be used to confirm or adjust position in web cutting or printing equipment. These sensors can also be used to detect presence of shrink-wrap seals, tamper-proof seals, labels, inserts and bar codes.
Replacement AC Proximity Sensors
While DC proximity switches are far more popular than their AC counterparts, the technology used in the AC version is similar to the DC version, and the operation is nearly identical. On new designs, if DC voltage is not available, the use of AC proximity switches is a reliable choice.
Andrew points out that you don’t have to change from an AC to DC proximity switch when a failure occurs because there are still options for replacement AC proximity sensors.
Many low-cost, reliable AC proximity sensors are available in a variety of shapes and sizes for a wide range of applications. Popular sizes include M8 (8 mm), M12 (12 mm), M18 (18 mm), M30 (30 mm) metal barrel, all for flush and non-flush use. These AC sensors operate on a wide range of voltage from 20 to 253 VAC, and typically use a 2-wire electrical hookup.
Drop into Area Sensors
Andrew describes an area sensor as a multi-beam array of photoeyes. These sensors provide a simple method to detect different sized and shaped objects as they drop or pass through the two-dimensional target area.
The sensor’s photoelectric arrays use a linear series of lenses, usually with a 5-mm or 10-mm pitch. The sensor pitch, height and teach method affect the minimum detectable object size, as well as the maximum response time. The smallest detectable objects range from 1.5 mm to 10 mm.
These area sensors cover a wide area from 70 mm to almost 1000 mm height, and up to a 6-meter sensing distance between the emitter and receiver. Discrete outputs are available and an analog output, proportional to the unblocked detection height, is also available in the form of a 4-20 mA or 0-10 Vdc signal.
Some common applications include error-proofing the dropping of a part into a reject bin, poka-yoke mistake proofing and others.
Andrew also made it clear that area sensors must not be considered safety devices. While similar in appearance and function to a safety light curtain, they are not suitable for safety applications, such as protecting an operator for a machine hazard.
Encode a Position
A rotary encoder senses rotary position using an internal coded disc and a sensing head. Encoders are used to sense position, rotation and speed on machines, tooling and actuators.
Incremental encoders can connect to a high-speed PLC input or counter for accurate position monitoring and control. Some absolute encoders use a simple parallel connection to standard PLC DC input cards where position is provided using Gray code.
A variety of encoders are available in light-, medium- and heavy-duty configurations with various body diameters, shaft diameters and environmental ratings. Open collector, totem-pole or line driver outputs can be specified. Different pulses per revolution (PPR) can also be specified depending on application requirements.
Andrew also talked about some rules to follow to simplify encoder design and integration, so be sure to check out the complete article.
To read more articles about process sensing & control, click here.
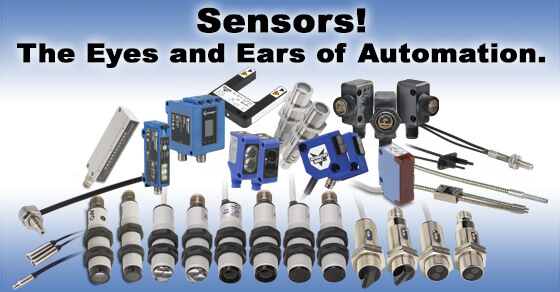