When wandering the plant floor, keep an eye out for energy wasting machines. Those running conveyors, rattling pumps and hissing air lines on idle equipment not only raise the decibel level in the plant—they also waste energy. With proper monitoring and analysis, machine energy use can be optimized, and these energy saving measures will also improve equipment life and reduce repairs.
An initial energy efficient machine design is not enough as you also need to measure, monitor and optimize energy use on all installed machinery. Being aware of the running and idle state of each machine and its energy use can highlight inefficiencies and point the way to improvements.
A View into the Equipment
Measuring and monitoring energy use of machines and equipment at the main power feed is better than just using motor nameplate data that’s usually worst case at full load power. Go after the actual power draw of the machine or equipment as power usage varies in a cycling machine. Understanding if a machine is idle, running production or purging product can help identify where energy use is the highest. This data can highlight areas for improvements, both in machine design and operation.
For example, if measured data shows a machine is waiting for product 50% of the time, this might indicate problems with upstream equipment or with operators. It may also show that the downstream equipment could be run slower to save energy.
Start Measuring and Monitoring
There are a variety of measuring and monitoring devices such as power meters, current donuts and true RMS transducers available for connection to an existing networked control system.
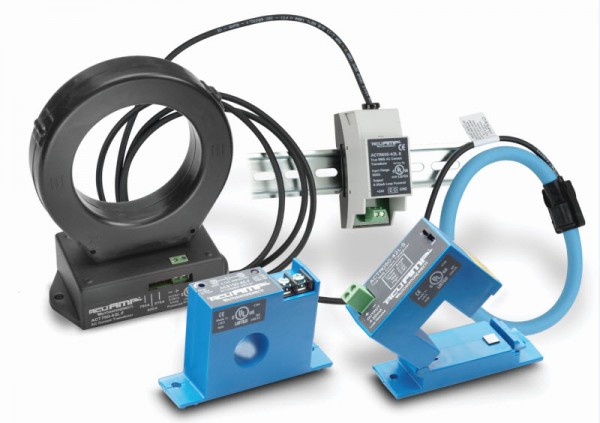
These same devices could also be connected to a plant-wide monitoring system using field I/O separate from the machine controllers. AutomationDirect’s Protos X I/O and Terminator I/O are good examples of field I/O for use in a plant wide, real-time power monitoring system.
The analog output of a machine mounted current transducer, which combines a current transformer and a true RMS signal conditioner, can easily connect to field-mounted analog I/O. As an added benefit, with this field I/O infrastructure in place, you can add OEE (Overall Equipment Effectiveness) monitoring capability such as machine running status and automatic part counting.
Maybe You Could Just Shut It Off?
Like many monitoring and data collection systems, the data is only as good as the input. As they say, garbage in equals garbage out. However, with good energy data in hand, efficient control of the machines can become a reality, while unused machines can be shut down or turned down wherever possible.
Turning off your lights at home saves energy, so turn them off when they are illuminating idle assembly cells or machines. There can be significant money savings from turning off the lights in large automated lines and production facilities.
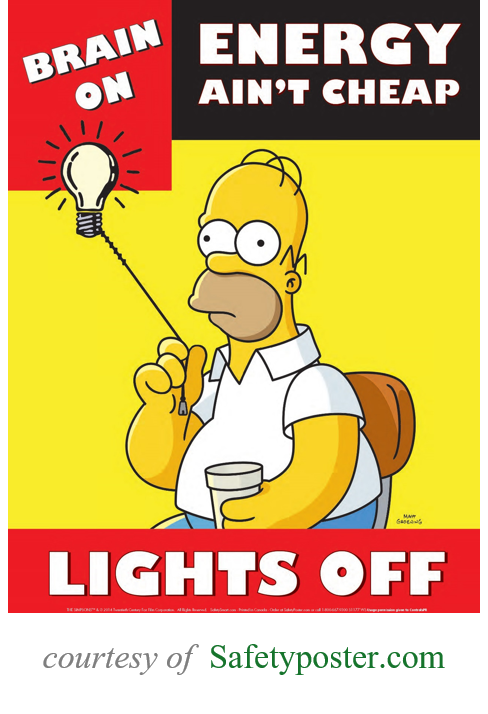
The same is true when powering down idle conveyors, auxiliary equipment and machines. Turn them off, either as a matter of procedure or as a programmed automatic function triggered by a machine idle timeout event.
Some applications can be slowed down to match the cycle rate of the line. While not all motors benefit from running at reduced speed, fan and pump applications in particular can save significant energy when run at a slower rate as dictated by a variable frequency drive (VFD).
Look at your plant through a green lens. Power down idle machines, turn off the lights and conveyors, and slow down the motors with VFDs where possible. Not running the machine or running it at a slower rate will save energy, reduce maintenance and save on repairs.
For more information, please see the article Best Practices for Energy-Efficient Machines in the June 2015 issue of Control Engineering magazine, authored by Cindy Green, an Industrial Engineer at AutomationDirect.
To read more articles about programmable control, click here.