Improved performance, ease of use, and energy savings combined with IIoT capabilities make VFDs the right choice for many process industry motor applications.
Bryan Sisler, Product Manager for Drives and Motors at AutomationDirect, wrote an article for the May 2020 issue of Processing titled Beyond Process Control with VFDs. Here’s a summary, click on the link above for the full text.
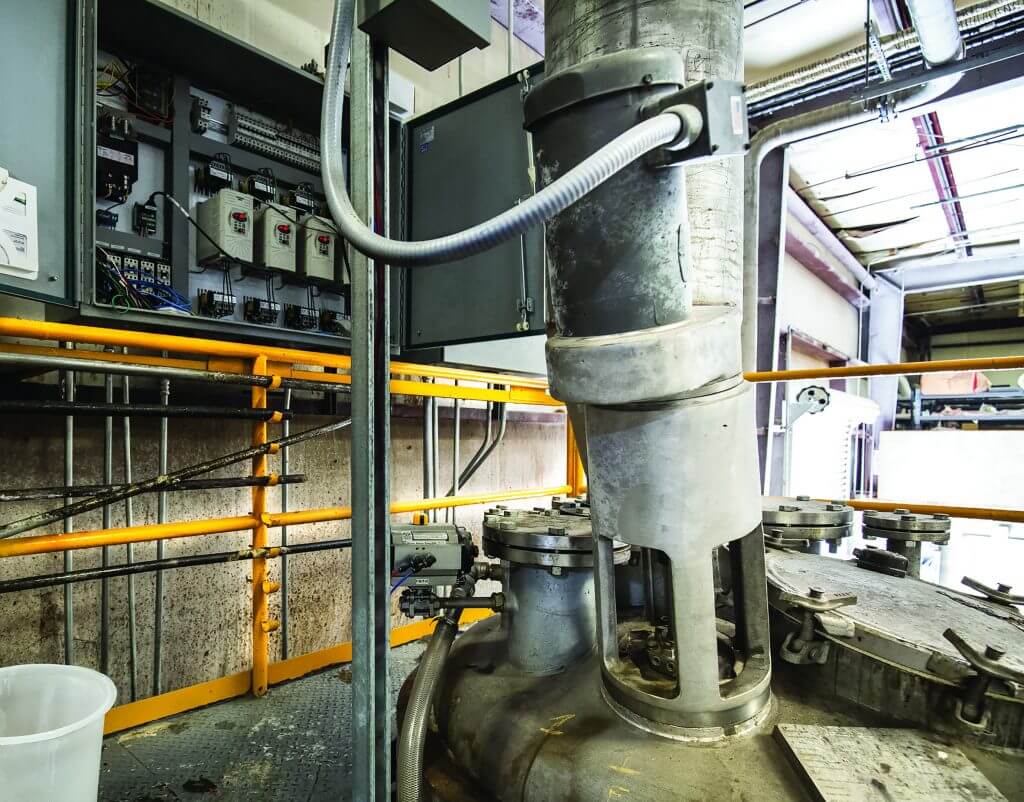
Industrial process plant workers involved with motor controls back in the 1980s may remember them as huge electrical apparatuses, with rudimentary control capabilities. Today’s AC motor drives, occasionally called inverters but most commonly known as variable frequency drives (VFDs), are far more advanced and suitable for almost any application. Beyond just speed control, AutomationDirect VFDs deliver advanced operation, are easy to interact with, and save energy.
VFDs Go Where Needed
One noticeable change over time has been the reduced footprint of modern VFDs, with some units 1HP and less literally fitting in one’s palm. Many VFDs are rated for extreme temperature operation (both hot and cold), so they can be conveniently installed where needed.
Smarter VFDs
Some of the most dramatic VFD advancements have been around improved human-machine interfaces (HMIs). These were first on-board, then they were the removable-type, and now PCs and mobile devices can connect via wired or wireless networks so users can configure, monitor, and command VFDs.
Users can readily integrate these VFDs with programmable logic controllers (PLCs). And taking things a step further, many VFDs include PLC-like programming capabilities right on board so they can operate locally in a standalone manner. This can be useful to make local operations more robust, or even to automate an entire small process.
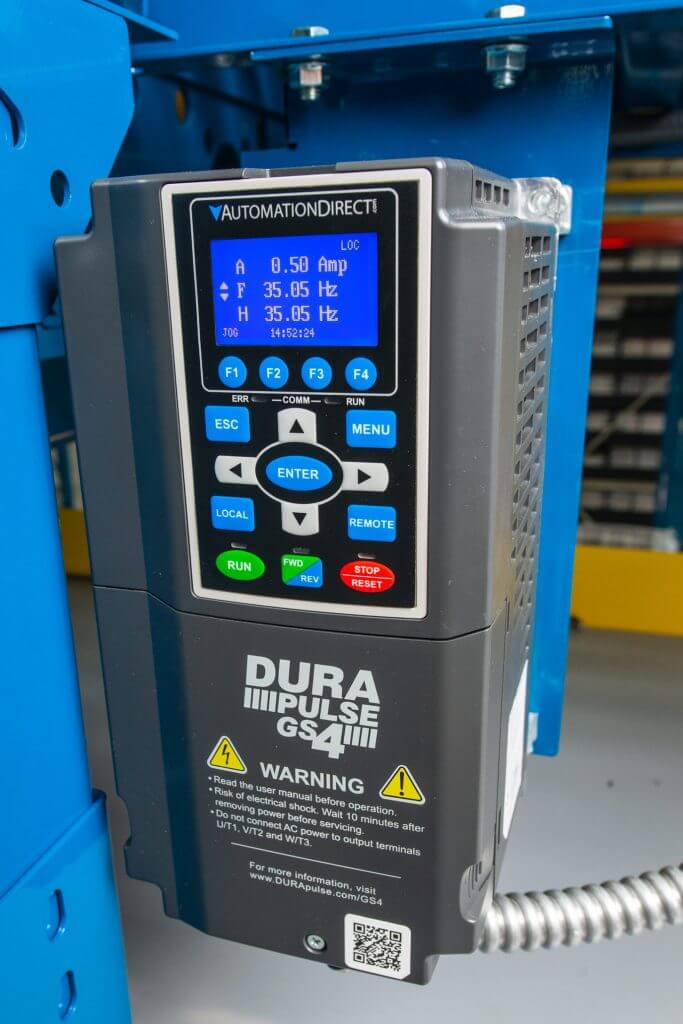
Safer Operation
Power handling advancements mean that VFDs can efficiently and accurately operate the many types of motors a machine designer may choose to use. Today’s VFDs also include built-in industry-standard safe control methods like safe torque off (STO), safety brake control (SBC), and more. STO and SBC make it easier for users to design new equipment or upgrade existing installations with the right level of safety.
Connected VFDs
Most VFDs now support various Ethernet or other industrial digital protocols, so users can take advantage of increased networking and industrial internet of things (IIoT) capabilities while minimizing field wiring. Fiber optics and various high-speed and redundant-capable communications options are ideal for the most demanding printing, paper, steel, pharmaceutical, food and beverage, and other processing applications.
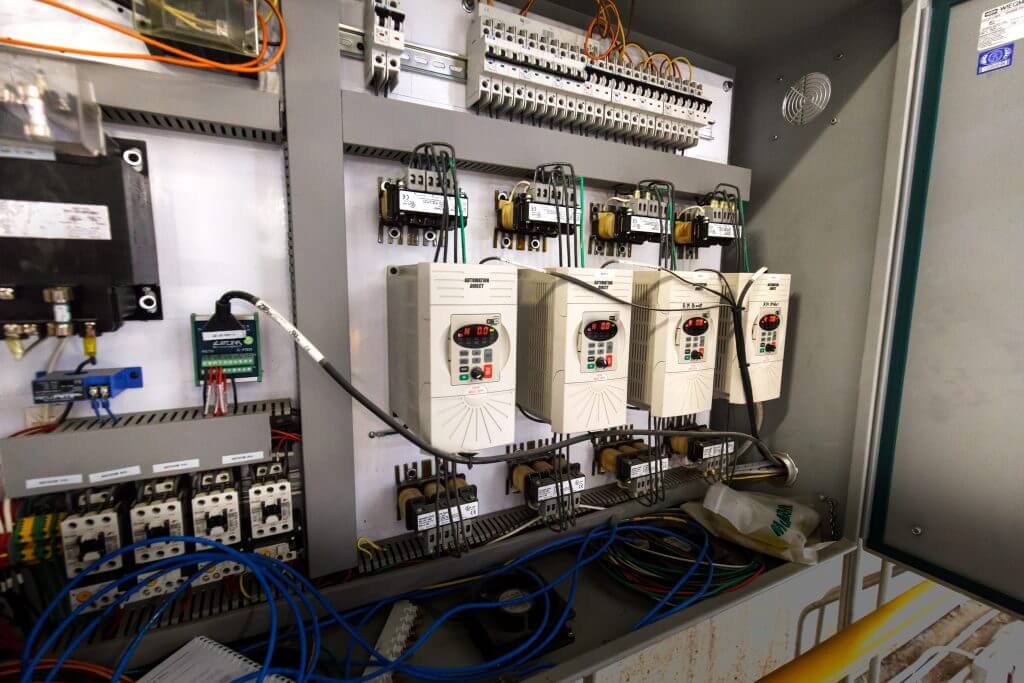
The Future of VFDs
To a great extent, VFDs have followed Moore’s Law, like many other solid-state technologies.
The confluence of processing, power and communications advancements are enabling reliable control and data accessibility like never before. Even if these added features are not used immediately, choosing a VFD with these capabilities when designing equipment is a form of futureproofing, or at least making the system upgrade-ready.
Although developments will continue, process industry users and designers will benefit from performance and digital transformation gains by implementing VFDs today in a wide variety of applications.