See how a water utility standardized around AutomationDirect products to improve operations while saving time and money.
A team of operations, maintenance, and engineering personnel at Helix Water District in San Diego, CA has retrofitted and constructed many sites using automation hardware and best practices based on AutomationDirect products. David Reagan wrote an article with the support of SCADA team members Henry Palechek, Bobby Fortuno, Gary Richardson, Kyle James, and Jeremy Boone. The January 2020 issue of Flow Control carries their article, Case Study: Standardization of Automation Practices Improves Operations at Water Utility, which captures their experiences. Here’s a summary, click on the link above for the full text.
Industrial automation may control small standalone machines, larger processes, or some combination of the two. Regardless of scale, it always makes sense to streamline design efforts, simplify support, and reduce costs by following good standardization practices. Automation projects include hardware, software, and networking which must be implemented for today’s challenges but upgradable over coming years due to changing needs and technologies.
While many end users may not have access to a large engineering group, this article shows how a moderately-sized staff at a water utility recognized the challenge of designing projects and took a few practical steps to implement standardization.
The Water District Takes Control of its Future
Helix supplies about 270,000 customers from a 106 million gallons per day treatment plant supported by about 25 geographically distributed pump stations.
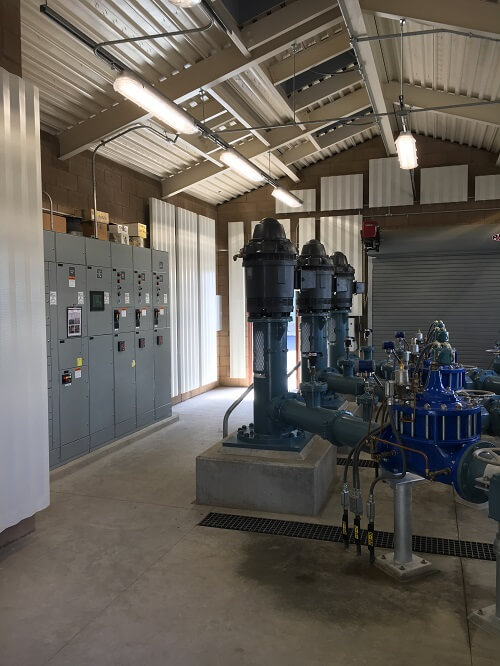
Some assets were over 40 years old, so the utility created a 10-year capital improvement plan to rebuild and replace various stations and motor control centers (MCCs). However, because each smaller project was typically performed by outside contractors, the results were a variety of products, each a little different, with designs that were difficult to support.
Building a Template for Success
Since pump station sites typically incorporated automation components within the MCCs, the team came up with a compact design suitable for retrofitting into existing MCCs, or built into new MCCs, and able to accommodate various motor sizes, pump quantities, and I/O counts. The team specified the core programmable logic controllers (PLCs) and human-machine interfaces (HMIs) as AutomationDirect, but allowed some substitutions for commodity-oriented parts.
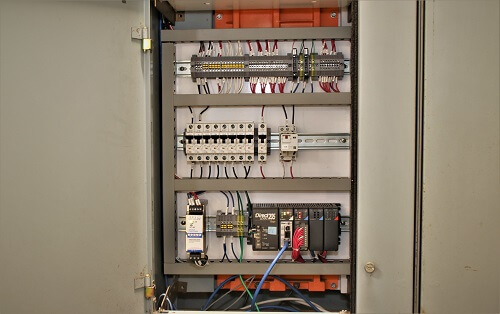
Codifying Code
Just as the team’s technicians standardized physical panel designs for good workability, they applied similar efforts to the software design. First, they architected the PLC logic to reliably handle the basic needs of any pump station, making the code usable for different pump quantities, signal ranges, and even communication technologies with only minor adjustments to customize for a given site.
Typical memory locations, I/O assignments, and a library of common HMI graphical objects, make it easier to implement and operate the systems.
Local Control, Centralized Visibility
Many utilities have distributed sites which must operate locally as isolated “automation islands,” but also interact with each other under a single SCADA umbrella. Critical field-located PLCs communicate peer-to-peer as needed while a centralized data collector PLC at the main plant provides the main monitoring HMI, handling of start/stop setpoints, data logging, and alarming. This multi-tiered approach was carefully tested on the benchtop before deployment.
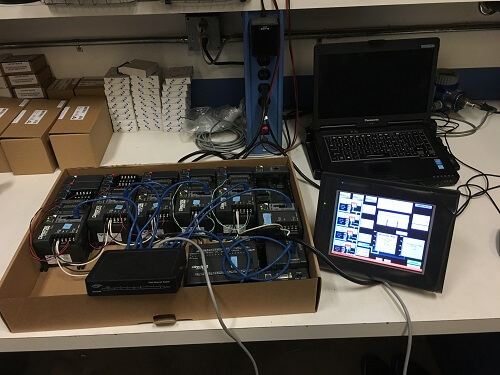
Proof in the Field
The team has successfully retrofitted and built many pump stations using this approach. They have experienced reliable functionality with added benefits like proactive system alerts and the ability to save time and money through remote connectivity.
Attainable Standard Automation Practices
Most end users understand the benefits of standardization but may be unsure how to proceed when developing actual projects. The Helix team’s efforts to improve the utility’s systems are a case study in how to approach the task methodically from the bottom up, starting small, and adding value at every level. Pre-testing and a staged deployment can help ensure the best results.
Click here to read more articles related to the water industry!