DC motors provide a flexible and effective motive force for many machine and automation applications.
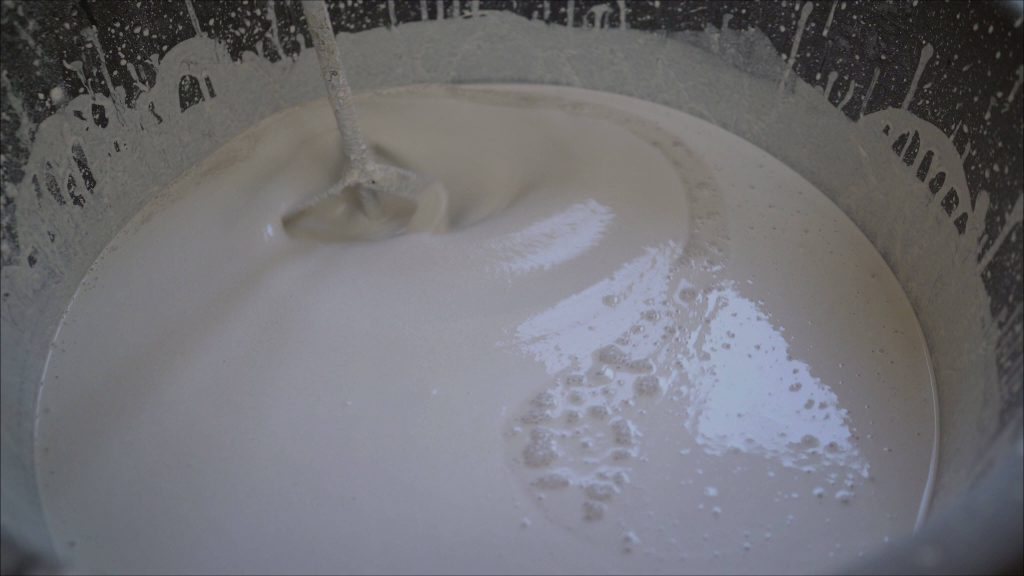
Although direct current (DC) motor technology dates from the early 1800s, and other motor types have been developed since then, DC motors remain the best option for many applications. DC motors can be obtained in tiny consumer-grade form factors suitable for toys, as well as large industrial-grade units for driving massive equipment like locomotives, and anything in between.
AutomationDirect offers DC motors ranging from 1/31 HP to 2 HP, in a variety of form factors, speeds, and voltage ratings suitable for many types of industrial applications. A full range of accessories, include DC drives, is also available. This article covers some useful basics regarding how to select and implement DC motors and associated drives.
DC Motor Basics
There are many types of motors, each of which turn electrical energy into physical motion, usually rotational. The four major motor types used for industrial applications are the alternating current (AC), servo, stepper, and the aforementioned DC motor. Servo and stepper motors are generally reserved for high-performance motion control applications. AC and DC motors share many similarities, but DC motors generally excel with respect to high startup power/torque, fast response times, and overall efficiency.
There are many DC motor technology variants—including shunt, separately excited, series, compound, and brushless—but the most common for industrial systems is the permanent magnet (PM) DC motor.

A basic PMDC motor consists of three elements:
- Stator: the fixed outside housing, which forms the main body of the motor.
- Rotor: made from armature electrical windings arranged to spin on a shaft within the stator, with the shaft protruding and delivering the rotational motion.
- Brushes: transfer electrical current from the fixed stator to the spinning rotor windings via a commutator.
The stator incorporates a strong permanent magnet within the housing and surrounding the rotor. When DC current is supplied to the rotor windings via the brushes, a magnetic field is produced by the rotor, which interacts with the magnetic field of the stator, causing it to spin. The speed of a DC motor is directly proportional to the supply voltage, and DC motors also exhibit a self-regulating characteristic where they adjust torque in response to varying loads.
DC motors are a robust method of generating and controlling rotational motion. One downside is that the brushes do wear out and are therefore a maintenance item, but they are easily replaced.
Applying DC Motors
Certainly, there are a lot more details and theory behind DC motor operation, but industrial equipment designers generally need to address the following details to specify a DC motor:
- Physical dimensions: DC motors are available in various frame sizes, and they can be flange-mounted or C-face mounted. Typical shaft diameters are 5/16, 1/2, and 5/8 inch.
- Environmental: The motor materials, finish, and seals must be rated to operate in the target environment. Totally enclosed fan cooled (TEFC) and totally enclosed non-ventilated (TENV) ratings are common.
- Supply voltage: Supply voltages classes are ordinarily 12/24, 90, or 180VDC.
- Power rating: Designers must determine the horsepower required to drive the load under all conditions.
- Speed: 1,800 rotations per minute (RPM) is perhaps the most common, but other full-rated synchronous speeds are available.
A suitable DC drive must be specified to operate each motor. Some drives are open frame circuit boards, which must be installed within a control panel or other enclosure for protection, while others are available in control panels rated up to NEMA 4/12, 4, and 4X.
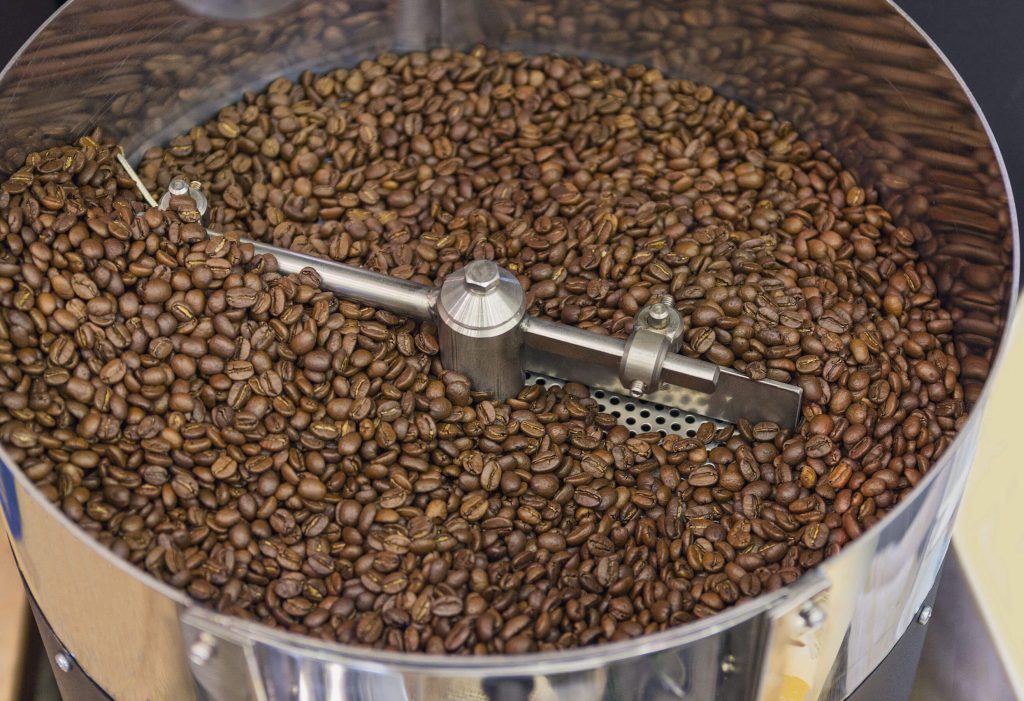
Electrically, the drive must be rated to provide the correct supply voltage, at an ampere rating sufficient for the horsepower. Basic DC drives typically use silicon controlled rectifier (SCR) technology, but pulse width modulation (PWM) using transistor switches produces a smoother output current.
Sometimes a user wants to manually control the motor operation. Basic DC drive designs are often analog, and they may include physical on/off switches and speed control potentiometers for this purpose. More advanced applications may need the DC drive to accept 4-20mA or pulse train signals from a remote PLC or other controller. Newer DC drive designs tend to be digital, and they may have advanced modules for multiple input signal types and communication modules.
There can be some more advanced considerations, such as whether an encoder should be integrated with the motor/drive, but in general a basic DC motor and associated drive are straightforward to specify and apply.
Selecting the Right DC Motors and Drives
The AutomationDirect website features entire sections devoted to DC motors and drives, as well as accessories. AutomationDirect maintains many resources—including specifications, documents/drawings, and videos—all accessible through their website, and support staff are ready to help designers identify the right solutions for their applications.