Everyone likes a smooth ride in their vehicle — unless you are off road in a 4-wheel drive vehicle. Most of us will avoid the bumps and potholes to drive on the smoothest pavement possible. Car manufacturers recognize this too. They spend lots of money on TV, print and digital advertising to promote that their vehicles have the smoothest ride on the market. It can be a major selling point when it comes to buying a car or truck.
Recently, creating the smoothest ride was the objective of a university student project where they worked together to determine what would provide a “smoother” ride. The team researched a way to keep the road smooth for auto manufacturers by using semi-active suspension rather than
passive suspension.
The Project
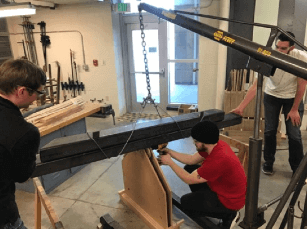
The Senior Capstone project is a curricular requirement for all mechanical engineering students who graduate from Eastern Washington University which is located in Cheney, Washington. The project spans approximately six months where every student works in teams to conceptualize, design, and fabricate a device and/or product. This particular team consisted of six mechanical engineering students: Joe Wagoner, Gordon Henry, Jack Egan, Eric Johnson, Chandler Johnson, and Mikel Danielson. They were assisted by two mentors Dr. Matthew Michaelis and Hessam Gharavi (both EWU professors).
Two of the students became interested in the topic when they heard Professor Gharavi give an extracurricular lecture on the subject. That interest eventually led to the idea to develop a Senior Capstone project to design and fabricate a semi-active suspension system to further analyze the dynamic response compared to passive suspension systems.
As explained in the students’ project report introduction: passengers of a vehicle do not directly experience the road profile itself but rather they feel the structural response of the suspension system that transmits a particular amplitude ratio of the road to the seat of the car. The vehicle’s suspension system does its best to try and diminish any bumpy movements for the passengers. Their theory was that the semi-active suspension would offer variable damping which would allow reduction in the amplitude ratio which would result in an effective increase in passenger ride comfort. The variable damping is accomplished by replacing the shock absorber with a magnetorheological (MR) damper. This variable damping from the semi-active suspension system would allow the vehicle suspension to better handle a changeable range of road excitations rather than a single frequency … meaning it would provide a smoother ride.
Given the project objective, the team developed workflows split up into subcategories to ensure all members had an active role. The team divided the work into the four phases of the engineering design process: problem scoping phase, concept generations phase, design and analysis phase, and solution implementation phase. To provide the best possible testing conditions, the team determined they should build a quarter-car test fixture frame which provided the structural support for the other assemblies and was fabricated from structural tube steel welded together. The suspension components consisted of a helical compression spring, magnetorheological (MR) damper, a secured concrete sprung mass, and sprung and unsprung mass plates. The road excitation was simulated utilizing a pneumatic cylinder actuator powered from a compressor. Finally, the electrical assembly consisted of all sensors, controllers, pneumatic valves and electrical fixtures. The control system utilized two different types of sensors to allow for different control theories to be tested and compared between the semi-active suspension system and the passive suspension model. AutomationDirect products were part of the project including NITRA cylinders (a 4-inch diameter cylinder was used), valves, and pneumatic accessories.
Both control theories developed for the project used a specific comfort index to determine whether or not to send power to the damper per the conditional statement; thus providing for testing at varying levels. Each control method was tested by actuating the pneumatic cylinder at different amplitudes and frequencies. Both the passive and semi-active systems were analyzed at each of these amplitude/ frequency pairs. Data from these tests provided numerical results.
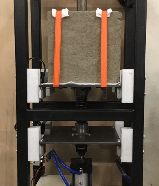
Results showed a measurable reduction in amplitude ratio between the semi-active and passive suspension systems. This reduction was measured using the same sensors used for the control system. Both visual and graphical results confirmed that the semi-active suspension system reduced the amplitude ratio by 5% to 20% compared to the
passive suspension.
Using the semi-active suspension system, the team was able to successfully reduce the amplitude ratio felt by the sprung mass of the system. The working principle of the MR damper alone was not enough to reduce the amplitude ratio alone. It needed to be coupled with the correct control system and electrical assembly to ensure that the damper turns on and off at the correct time. While it was confirmed that the semi-active suspension system was able to successfully reduce the amplitude ratio of the system, it is unclear to what degree exactly. Several more experiments would be necessary to examine various control theories and their effects with varying amplitudes and frequencies. Ultimately, the role of the damper should be examined as well to better understand how its response plays a role in the response of the system as a whole. This project served as a great foundation in the development of a semi-active suspension test fixture.
All the students involved in this project had a background and classes in mechanical engineering and have now each earned a Bachelor of Science degree in the subject. However, that made the electrical design aspects of the project challenging at times. Fortunately, the team saw this as an opportunity and, by the project’s end, had gained cross-disciplinary knowledge in the field of electrical engineering. In addition to the electrical design, the entire fabrication process was conducted by the team; therefore, all design aspects were carefully undertaken with design for manufacturability in mind. An important aspect of mechanical engineering is understanding the full product lifecycle which is critically reliant on those who fabricate the design. Manufacturing their own design gave the team insight on the difficulties of the fabrication process. Finally, during the manufacturing process, the team needed to learn new processes that they didn’t have any experience with before. An example of this involved learning how to use a CNC plasma cutter and CNC milling machine.
Everyone on the team plans to pursue a career in mechanical engineering with one teammate who is interested in specializing in the control systems industry. There were many aspects of this project related to mechanical design and manufacturing that will be beneficial to all members of this project as they develop their careers. The Senior Capstone project at Eastern Washington University is designed to put students through the entire engineering design process and act as a culmination of the coursework. This project helped all members grow as engineers and the interpersonal connections made as a team will be beneficial as many of them have stayed in touch after graduation.Sounds like a smooth road ahead for these graduates