Automation of a tabletop coffee roaster demonstrates how home automation projects can help users explore new technologies and develop their skills.
Michael Hoffman, who works at Dragos and is a member of the SANS Technology Institute, wrote a success story for the October 2021 issue of Design World titled Brewing Up DIY Automation Solutions. Here’s a summary, click on the link above for the full text.
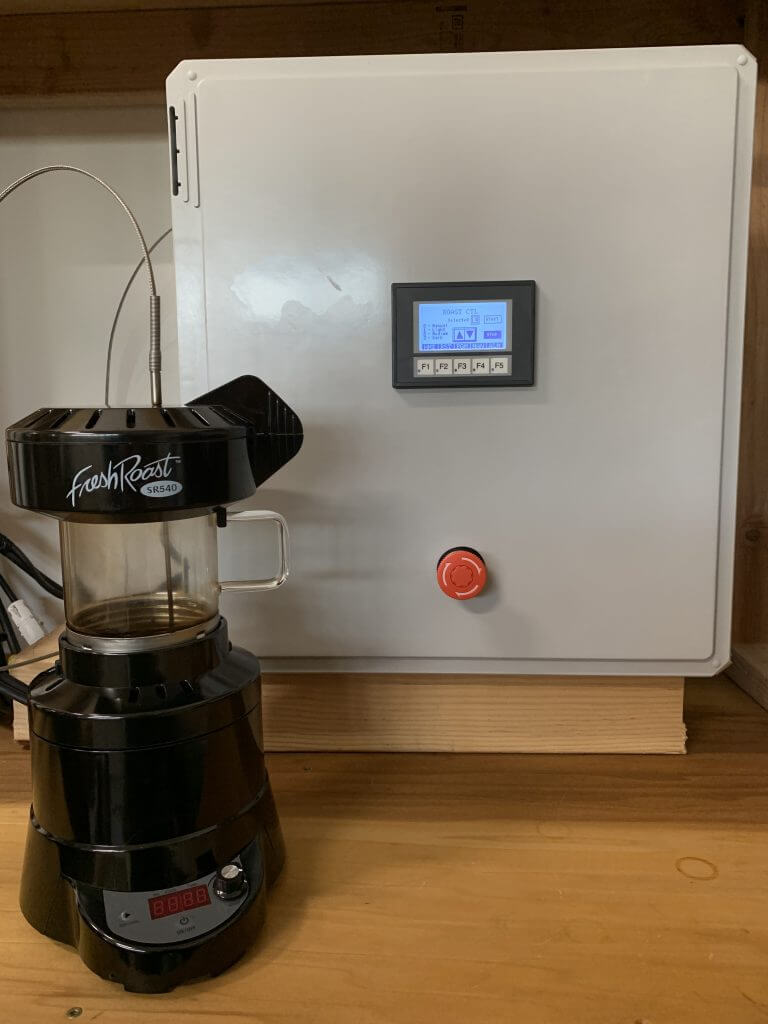
There are many control and communication technologies—ranging from consumer-to industrial-grade—for creating practical, robust, and secure automation solutions. With so many choices, it’s often difficult to pick the right path, but a good starting point is often a small do-it-yourself (DIY) project. Hoffman’s many years of industry experience and his involvement at SANS has convinced him that these types of DIY projects are a great way for users of all levels to learn and experiment with the design, building, programming, and protection of automation systems.
Starting small then scaling large
As a first step in the learning process, automation principles can be applied to almost any electro/mechanical system to provide remote visibility, better control, energy savings, and more.
At SANS, students use PLC kits consisting of an AutomationDirect CLICK PLC, I/O cards, and HMI, along with an associated virtual machine (VM) loaded with the free configuration software. This is a solid platform with many connectivity options, and it is well-suited for class projects and for industrial automation solutions ranging from simple to complex.
As an example, Hoffman chose to execute the design/build/program/secure process on a Fresh Roast SR540 appliance. This was done to prove a technical point, but also to obtain high-quality fresh roasted coffee for his use. The article steps through his approach.
Design
Some research yielded the stages and parameters for a typical medium roast, which includes drying, ‘first crack’ Maillard, ‘second crack’ caramelization, and cooling.
Build
Fortunately, it was possible to upgrade the appliance controls with a thermocouple, an AC solid-state relay for the heater, and a DC drive for the fan, all wired to the CLICK PLC I/O. Many other components were sourced from AutomationDirect, such as power supplies.
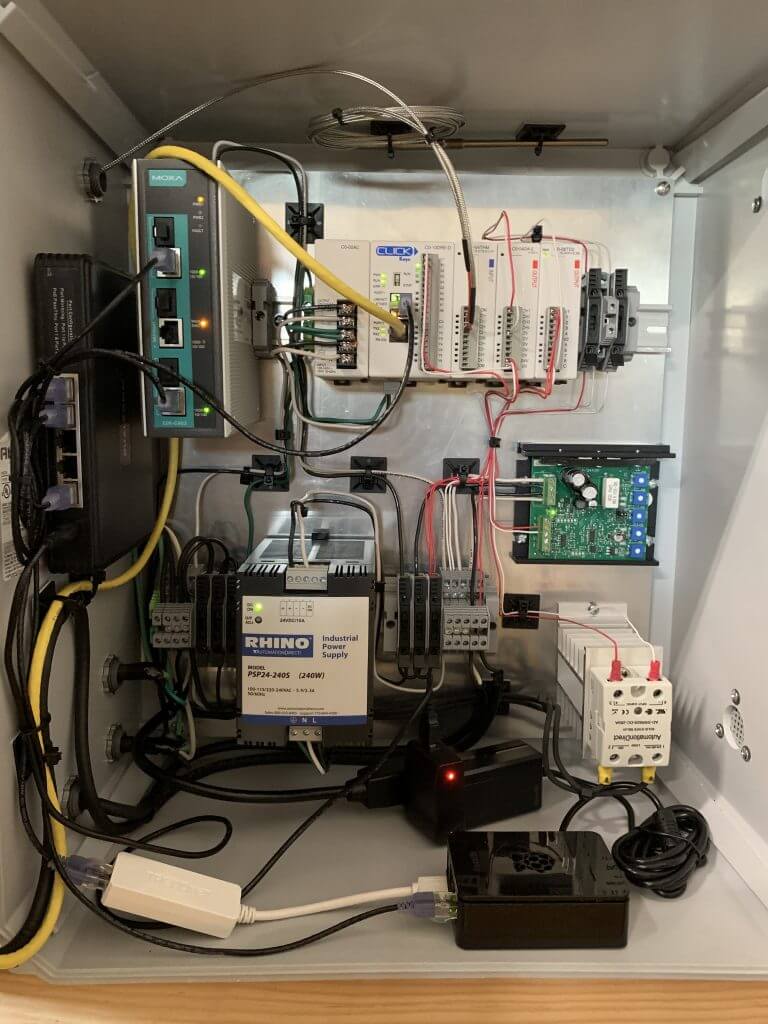
Program
A five-step program with user-adjustable parameters was developed. A PID loop handled the temperature control duties, and several C-more Micro HMI screens were developed for monitoring and control.
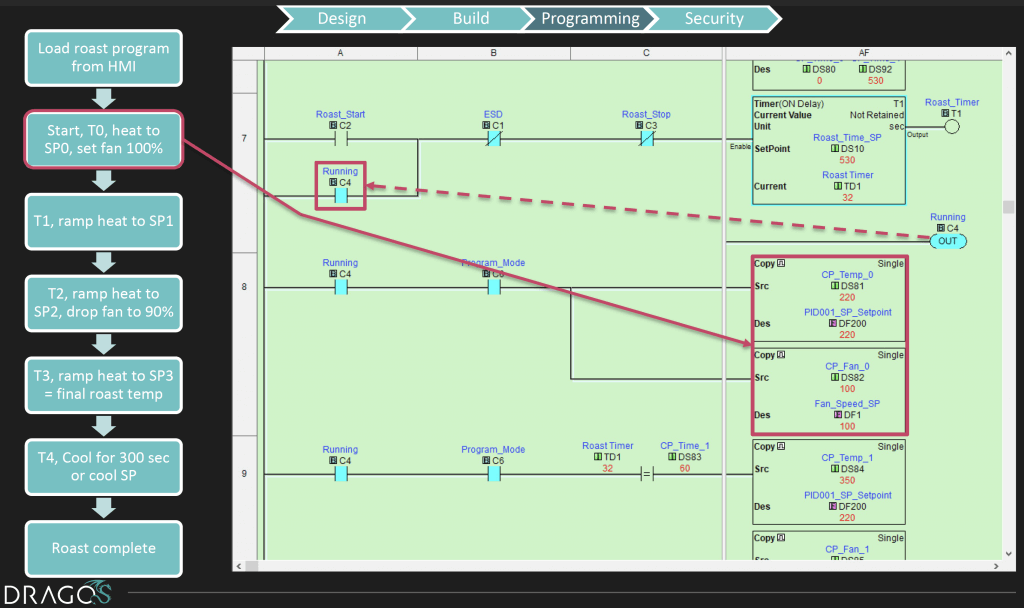
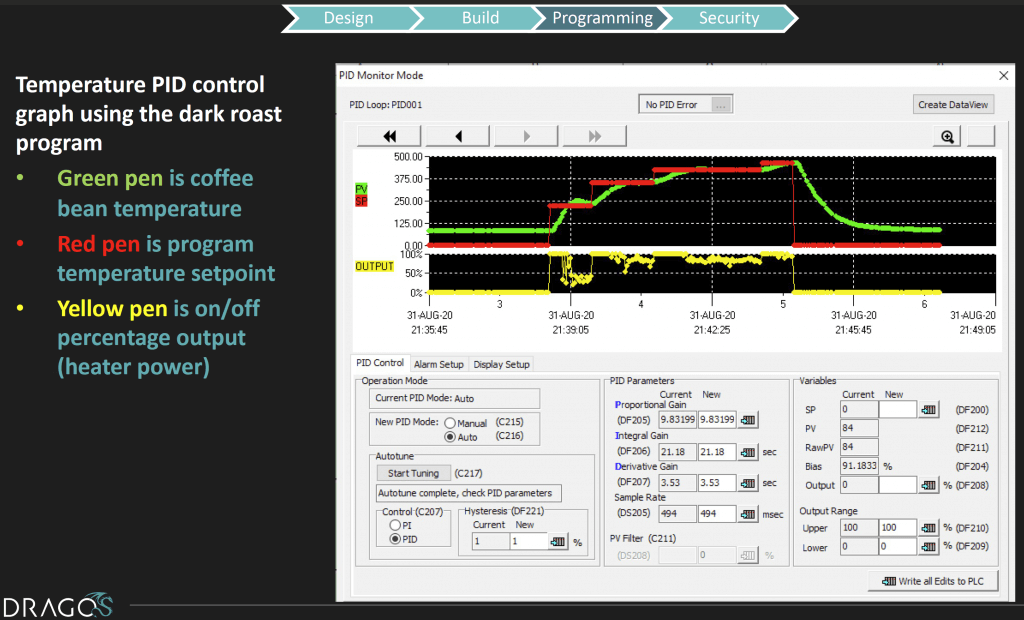
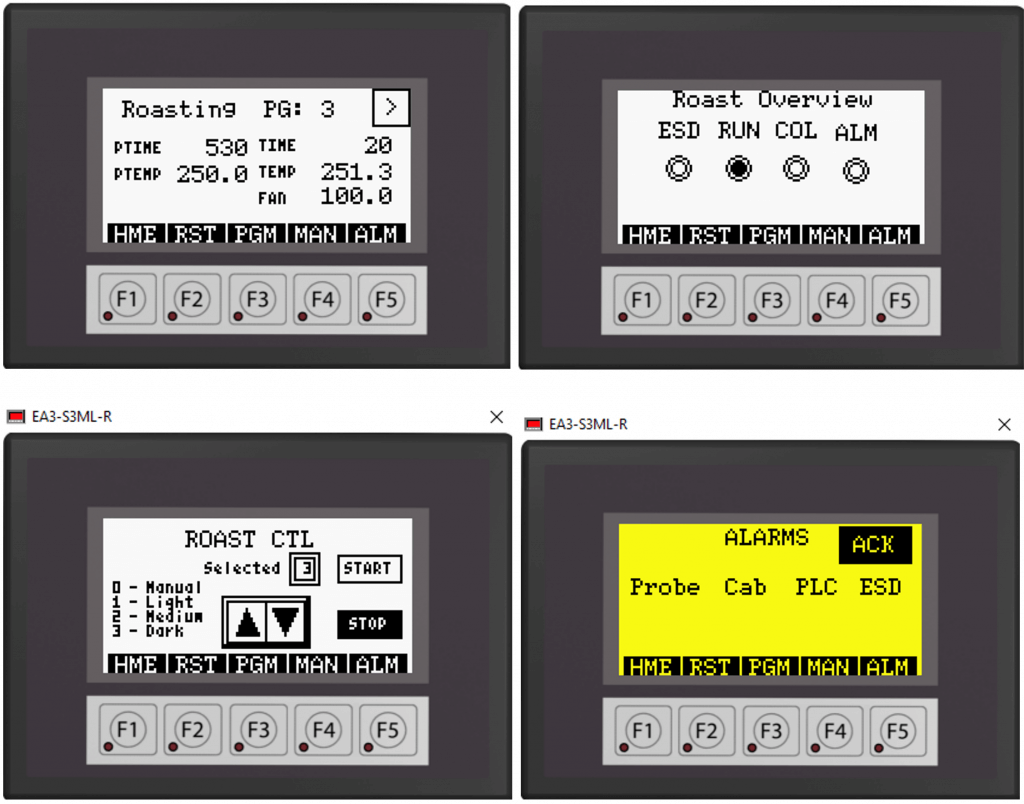
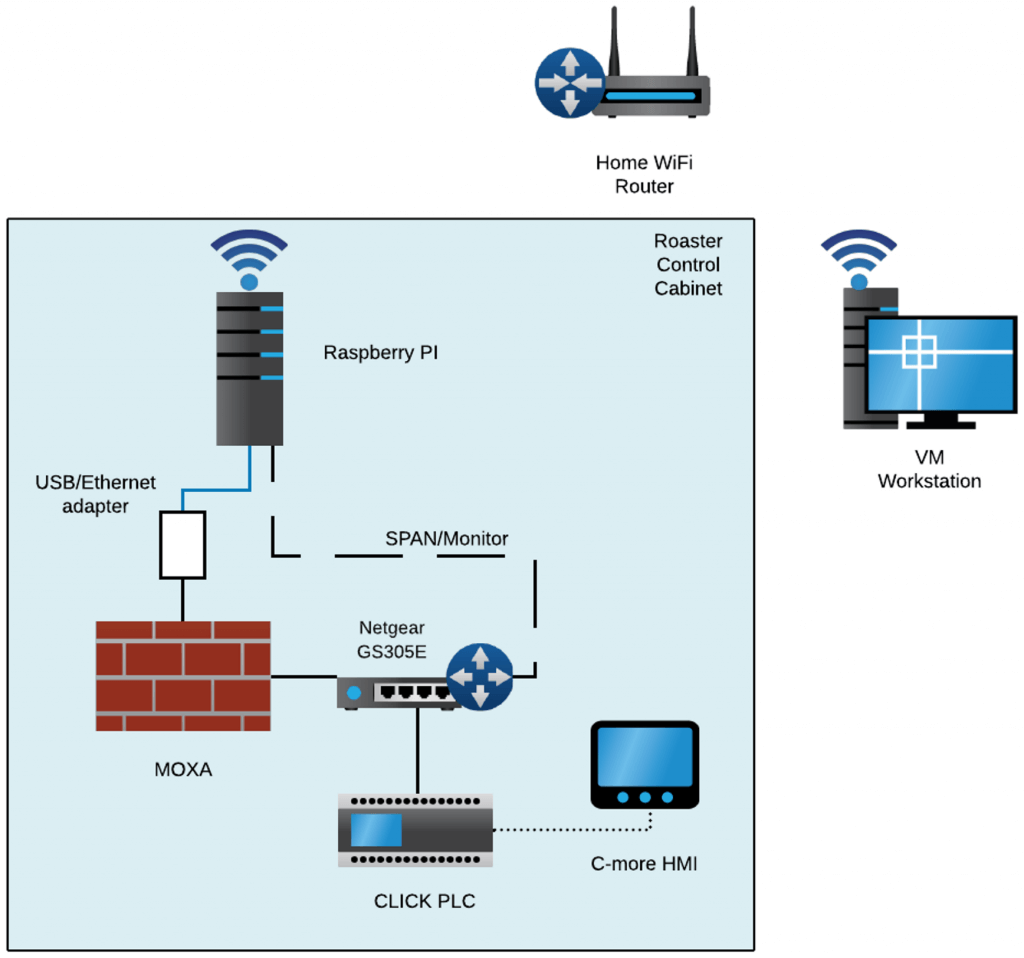
Protect
A standalone ‘island of automation’ system is less susceptible to outside cyberattacks, but most modern systems include network connectivity. In this case, a Raspberry Pi v4 was configured as a router and wireless network bridge, in conjunction with a Moxa firewall. These components provided secure remote connectivity.
This coffee roaster automation project, primarily based on AutomationDirect hardware and software, provides a solid example of how DIY projects and commercially available industrial-grade products provide a good foundation for advanced topics and larger projects.
Figures, all courtesy of Michael Hoffman