Smarter sensors and practical digital networking make premium automation capabilities accessible for discrete manufacturing applications.
Large food and chemical production plants are typically called “process” operations, while machinery and equipment are considered “discrete” manufacturing, but both categories need effective detection and measurement technologies. Some technologies, such as smart sensors and digital fieldbuses have largely been associated with process industries due to cost and complexity, but now versions are available to make advanced capabilities accessible for discrete manufacturing applications. Kevin Kakascik at AutomationDirect wrote an Automation World January/February 2024 article titled How Smart Process Sensors Benefit Discrete Manufacturing, addressing these improved connectivity methods and digital developments.
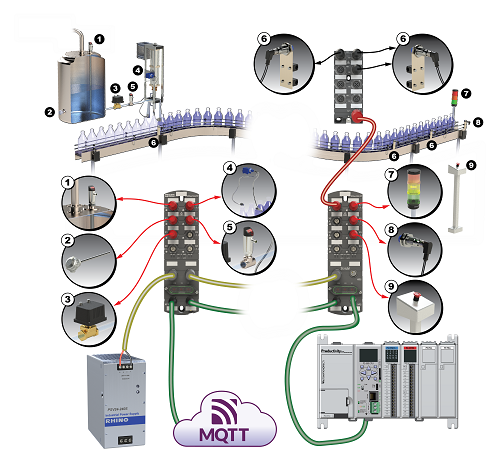
Getting Connected
Discrete manufacturing applications have traditionally used basic hardwired I/O for connecting with field devices, limiting them to communicating just one value, such as a switch status or analog variable. Industrial networks provide comprehensive process data, diagnostics, and configuration capabilities between a host and a field device, but usually involve specialized installation methods.
This has now changed, as many discrete and analog field sensors and devices—including photoeyes, proximity sensors, pushbuttons, beacons, flow/level/pressure/temperature instruments, and others—now are available with IO-Link.
IO-Link, as specified in IEC 61131-9, now provides a cost-effective and fit-for-purpose standard to support bi-directional communications of up to 32 bytes of data between a controller and a field device.
AutomationDirect offers a wide range of IO-Link field devices, master modules, hubs, and compatible PLCs, supporting seamless integration. Besides providing a wealth of data, the IO-Link digital bus solution supports automatic restoration of replaced devices, along with other user benefits.
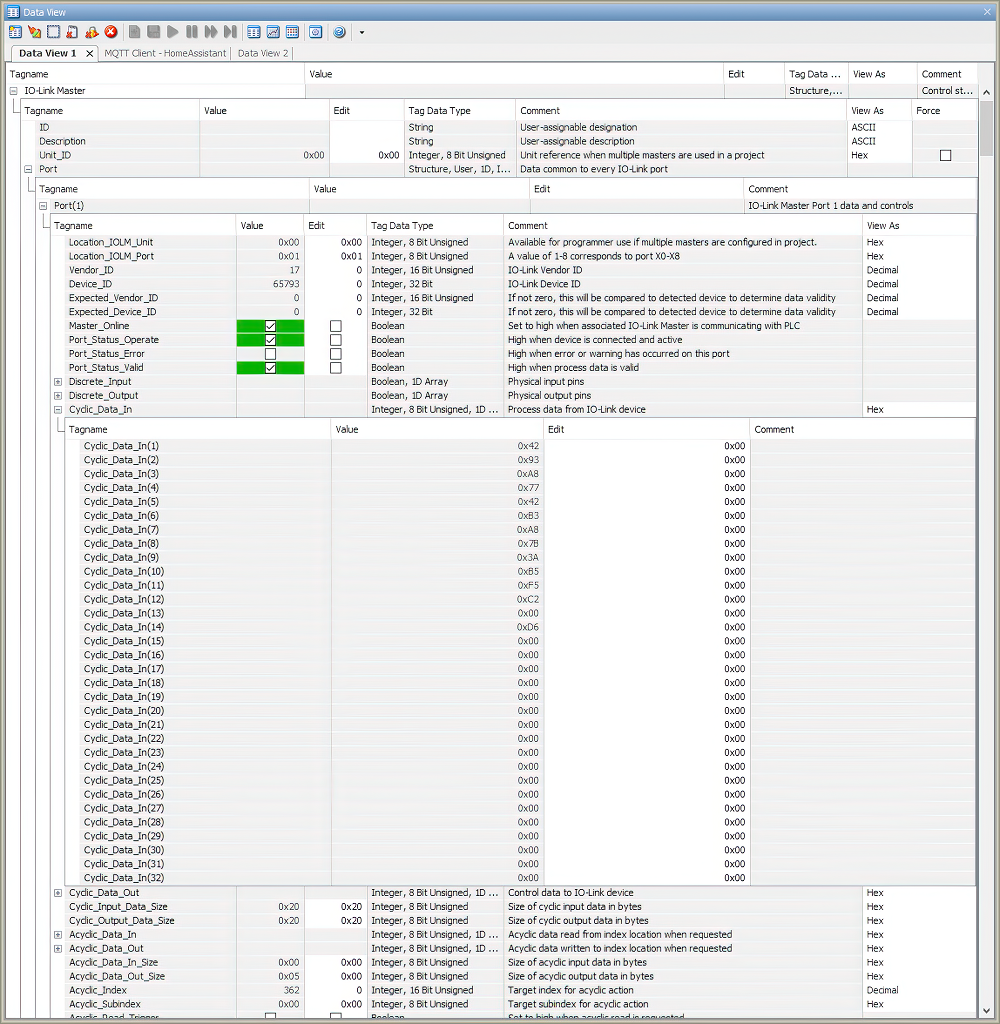
Convenient Commissioning
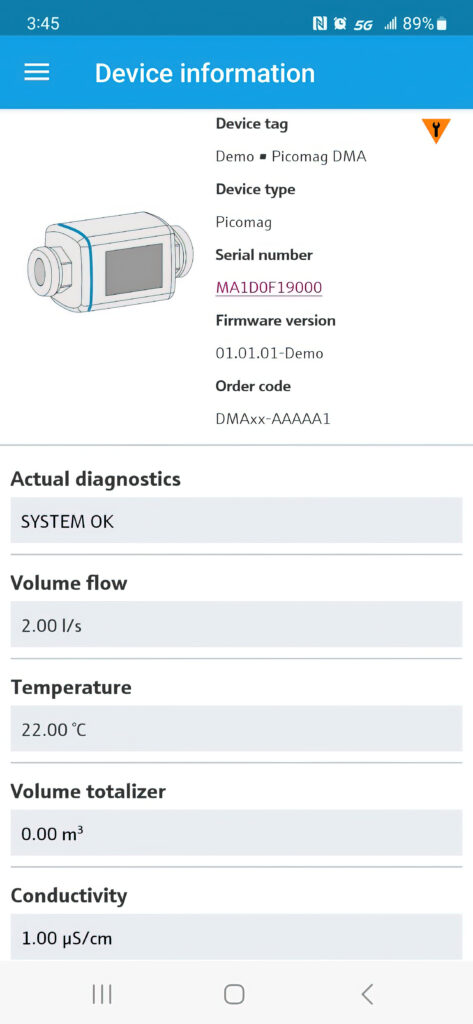
Intelligent field devices, by their nature, require configuration and calibration tasks that often needed to be performed right at the instrument itself. A better option is now available, as some modern instruments work with mobile applications and Bluetooth—for example, the Endress+Hauser SmartBlue app—so users can easily connect with field devices to commission, monitor, and diagnose them. These and other smart instruments are now available from AutomationDirect.
Only a handful of instruments support both IO-Link and Bluetooth at the moment, but more are coming.
Using one or both of these technologies provides discrete manufacturing designers and OEMs with better ways of automating equipment and systems while speeding and simplifying development and support efforts.
Designers benefit from flexible installation and commissioning options, along with the ability to access a wealth of data from each instrument, instead of just a single value.
Go to the AutomationDirect website to see the range of possibilities for IO-Link devices and automation integration.