Pneumatic components can incorporate analog electronic controls and sensors to improve operations.
Winn Paulk, automation controls group product manager at AutomationDirect, wrote an article for the November 2019 issue of Hydraulics & Pneumatics magazine, titled Integrating Analog Controls into Pneumatic Systems. See below for a summary or click on the link above for the full text.
Pneumatic technologies are clean, fast, and economical for achieving motion on machinery and industrial devices. This motion is often a discrete on-or-off type, as opposed to a continuously variable analog type, but not always. For instance, process control valves can use pneumatic positioners to perform analog control. There are other options for users to incorporate more advanced analog controls into pneumatic systems.
Discrete versus Analog
Automation is usually performed with smart relays, programmable logic controllers (PLCs), or programmable automation controllers (PACs). These computing devices connect to the outside world through input/output (I/O) points. Discrete outputs (DOs) command devices like solenoids, while discrete inputs (DIs) monitor on/off signals like limit switches.
Analog signals indicate a range of signals, like temperature level, weight, or speed. For pneumatic systems, common analog inputs (AIs) are pressure, position, and flow, while analog outputs (AOs) may command a valve position or a pressure controller via a current-to pressure (I/P) transducer.
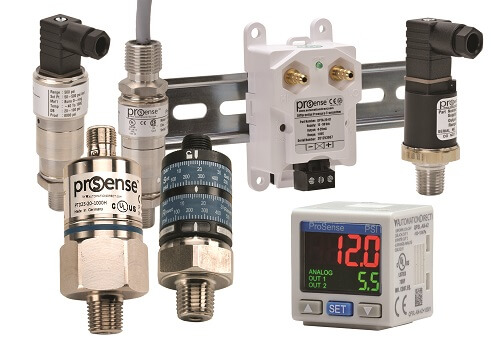
These AutomationDirect ProSense sensors monitor pressure in many process applications, providing discrete and analog output signals in wide measurement ranges for use in both pneumatic and hydraulic circuits.
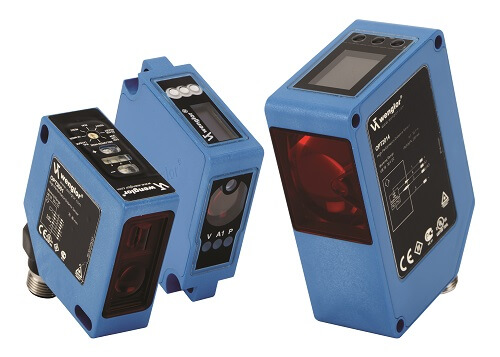
Laser distance sensors are a highly accurate way to sense equipment positions so control systems can command pneumatics as needed.
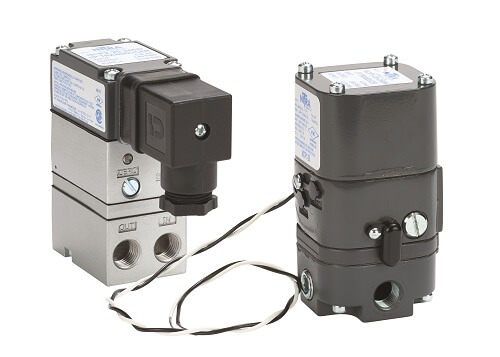
Current-to-pressure (I/P) transducers convert analog control system signals into varying pneumatic pressures.
Analog Signal Methods
Electrical signals for AI and AO connections require somewhat greater coordination than DI and DO I/O points. For analog signals:
Typical ranges are 4 to 20 mA, 0 to 10 V dc, or –10 to +10 V dc. For many industries, the 4- to 20-mA signal is the most popular, and it offers the additional benefit of positively identifying a failed instrument or wire connection if the signal ever goes below 4 mA.
Digital communication protocols like EtherNet/IP and IO-Link are more advanced options that can transmit more data in addition to the main process variable. In any case, analog signals must be scaled into proper engineering units within the controller.
Specification Details
Other details impacting analog signals are:
- Resolution
- Accuracy
- Stability
- Electrical isolation
Best accuracy is obtained when sizing an instrument for the range of interest and not over-sizing it. Analog signals are low voltage and susceptible to electrical noise, so the cabling must be carefully installed and protected.
Pneumatic Applications
One common analog pneumatic application is using a sensor to ensure a pneumatic line has the necessary pressure. A more advanced application could command and monitor a variable pressure to adjust the clamping force for handling different payloads.
Another common application uses laser sensors to monitor an actuator position so it can be commanded to a desired location.
Whenever analog controls are applied to pneumatic systems, a best practice is to include additional discrete sensors, like position limit switches or pressure switches, as a backup in case of primary sensor failure.
Analog Controls Provide More Options
Analog instruments and controls can add new functionality to pneumatically-operated applications. Following the guidelines in this article will help designers select the right signal range, field devices, and control elements to achieve reliable analog measurement and control.