This electrical contractor relied on AutomationDirect PLC and HMI hardware and software to rapidly rip-and-replace the controls on a failing rock crusher.
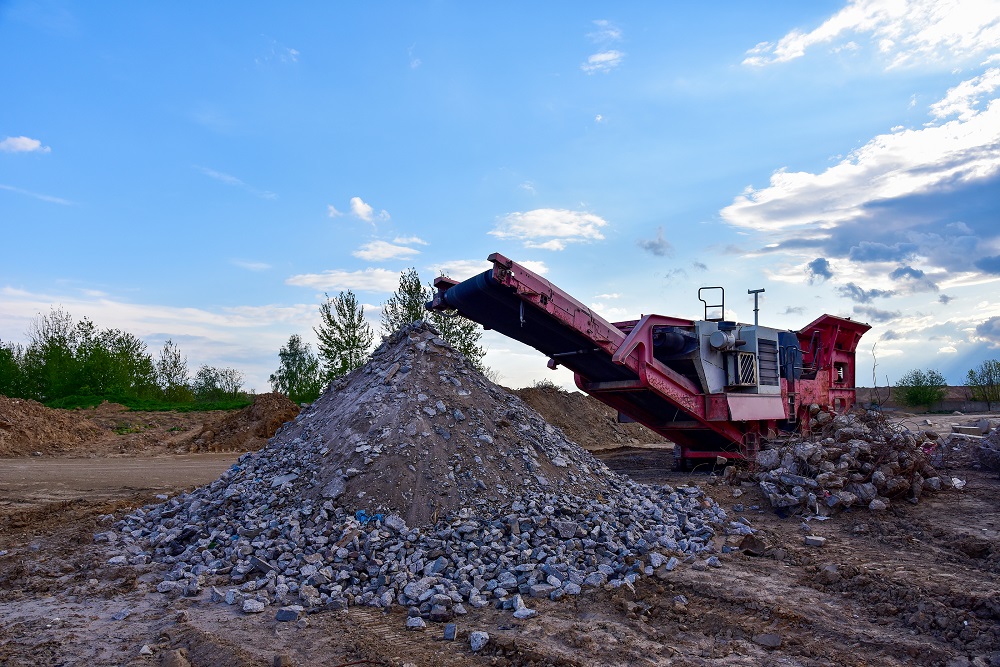
Equipment used in rock quarrying operations is subjected to extremes of dirt, vibration, heat, and more, pressing mechanical and electrical systems to the limit. When the crushing equipment legacy automation at one site experienced progressive failures, the operations team made patchwork repairs, but they knew that an automation retrofit would be necessary to move forward.
Theodore Thibeau at Fleming Controls and Power Specialties, Inc. (FCPS) recently wrote an article for Power & Motion May 2024 titled New Automation Solution Provides Quick Maintenance Fix for Quarry Operation, describing how his crew quickly assessed the client’s needs and promptly deployed a complete PLC/HMI retrofit.
A Crushing Failure
Rock quarries frequently use jaw crushers—machines with a funnel-shaped interior using fixed and motor-driven plates that create a compressive force—to break down material to the target size. In this case, the OEM had used a Modicon PLC, but the quarry did not have in-house personnel trained to support this legacy system. In fact, they did not even have access to the PLC program, which is a common reality with OEM equipment.
When the automation system exhibited failures, the operations team was forced to hardwire most functionality for basic manual operation, and their initial attempts at finding support to repair or replace the system were cost-prohibitive. Knowing that mill throughput would need to increase soon, they approached FCPS for help.
Choosing the Best-Fit Platform
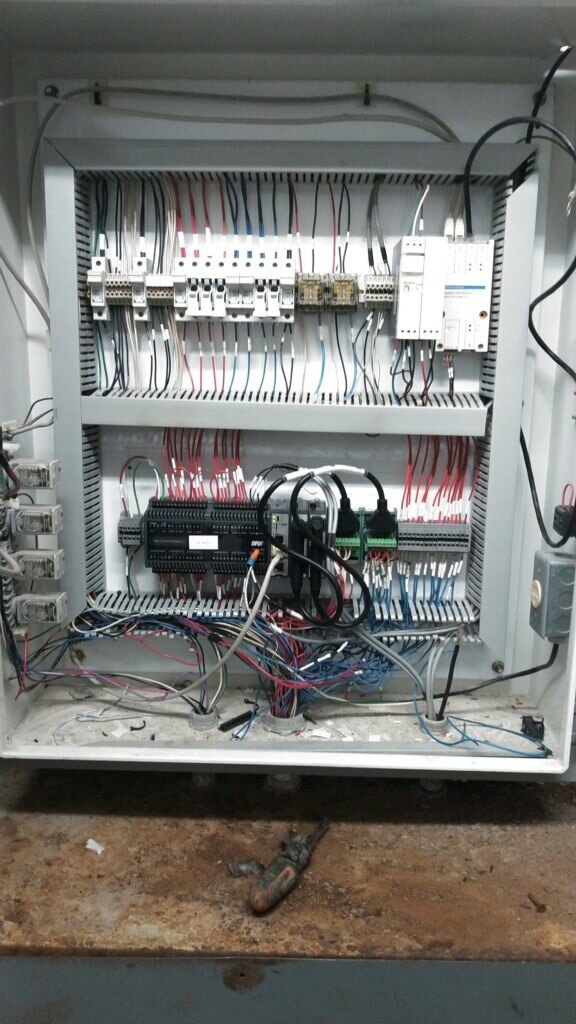
Although FCPS typically uses another automation brand, they quickly determined that AutomationDirect PLC and HMI products were the best solution to meet the client’s time and budget constraints, because all parts were readily available and priced reasonably. In short order, they selected a BRX stackable micro brick PLC, with I/O expansion modules. This versatile and compact PLC included the necessary functionality, processing power, and connectivity needed for the project, with plenty of room to grow—and it would retrofit nicely into the limited space, especially using the ZIPLink wiring solution. HMI duties would be carried out by two C-more CM5 series color touch screen devices.
Initially, FCPS had some reservations about learning a new platform on a tight deadline, but ultimately, they found it to be an enjoyable challenge. Although there was a lot to learn, there was no shortage of support … from AutomationDirect.
The FCPS team was able to easily apply their industry automation experience to this new-to-them platform, and they appreciated the free and intuitive software. The discrete I/O was straightforward, but a question did arise in using a 4-20mA input to monitor the current draw for each of the two crusher motors. AutomationDirect support swiftly addressed the issue, bolstering FCPS’s confidence in vendor choice.
Rock-Solid Results
Automation design prioritized ease-of-use for both controls and visualization. The primary user interface is a 12” unit, offering plenty of space to display all crusher and feeder settings at a glance. Alarms and alerts are available on the main display, and also on a conveniently located remote 10” unit.
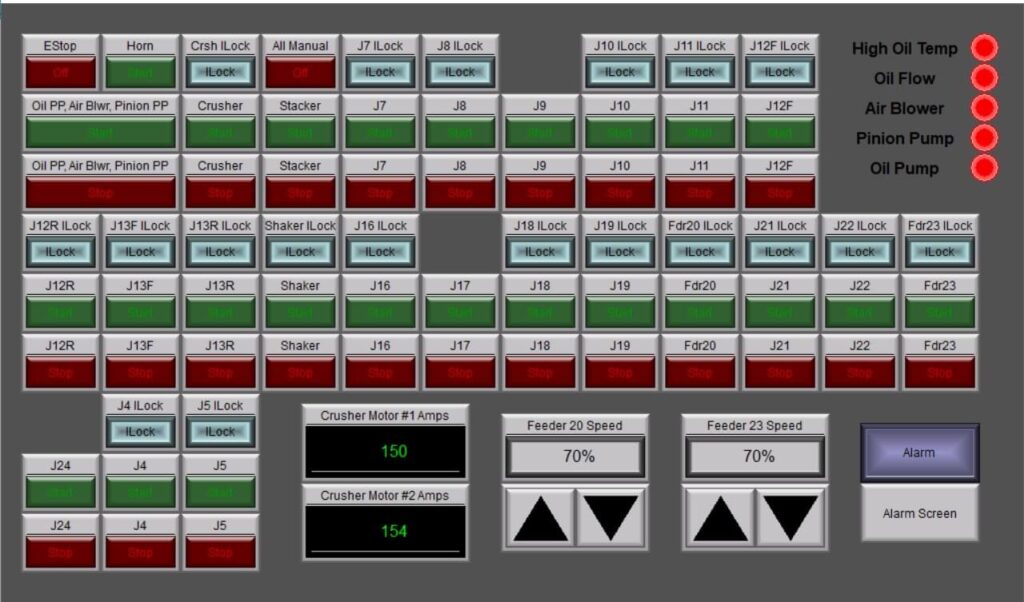
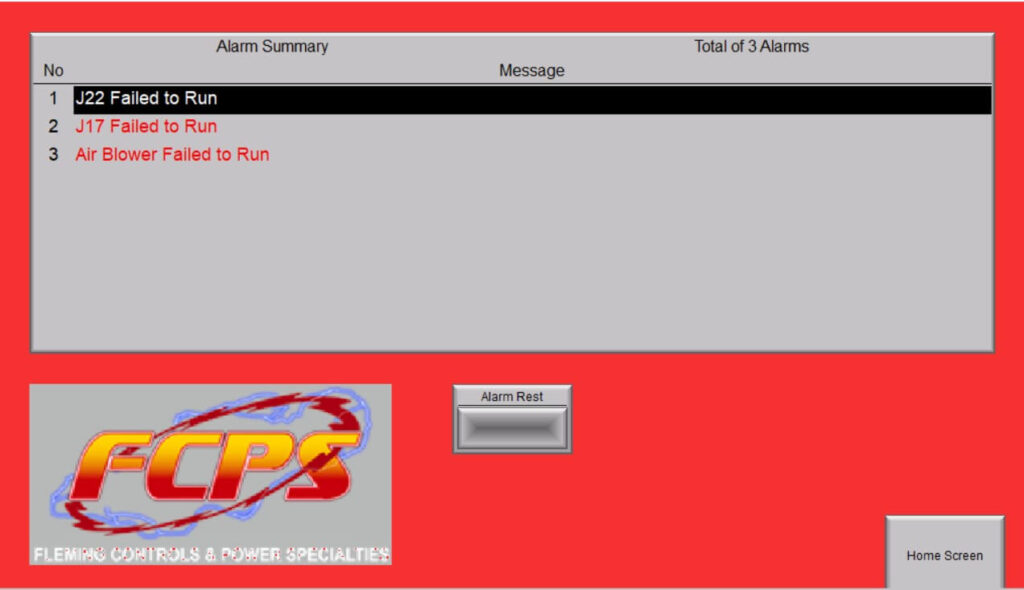
This project highlights the transformative power of innovative and fit-for-purpose automation solutions. Visit the AutomationDirect.com website today to learn more about how the portfolio of AutomationDirect products and support can help any end user, OEM, or systems integrator create practical automation solutions with exceptional value.
All figures courtesy of Fleming Controls and Power Specialties, Inc.