A manufacturing company teamed up with a systems integration firm to significantly accelerate an infrastructure project by integrating a robotic welder with precision motion control, intelligent safety systems, and other advanced automation components.
Tasked with producing over three miles of steel fencing in just 90 weeks, a leading steel fabrication company knew it needed to optimize its production methods. Partnering with systems integrator (SI) Properly Works, the combined team created fixtures and automation, and integrated them with a robotic welder, to achieve the necessary throughput with high-quality results. An article in The Robot Report June 2025 titled Welding Project Uses Robotics to Crunch 12 Workhours into 45 Minutes explains how the successful project was conducted.
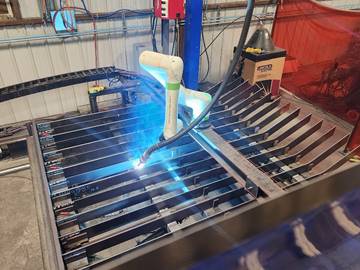
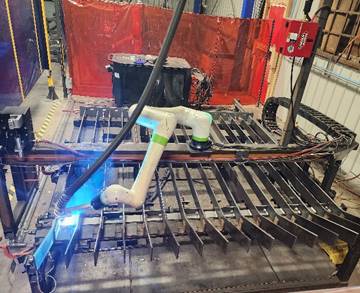
Welding Together a Solution
For this time-sensitive infrastructure project, each fence segment required over 140 welds and 10 hours of manual labor. The fabrication company, Seibel Modern, had performed large-scale projects before and knew that automation would be necessary to execute the work efficiently and within the time constraints. The team initially planned to implement tabletop-type robotic arms to make the welds, but they quickly determined that a fully integrated robotic welding cell was the best approach.
Seibel Modern could create the fixture and mechanisms, but they needed assistance with the automation aspects, so they partnered with Properly Works, an SI with specific experience in this type of work. As an independent SI, Properly Works is free to integrate various product brands for robotics, welding, motion-control, and general automation needs, but when there are no defined requirements driving the work, they prefer to use AutomationDirect products based on proven positive experiences.
The Spark of Modernization
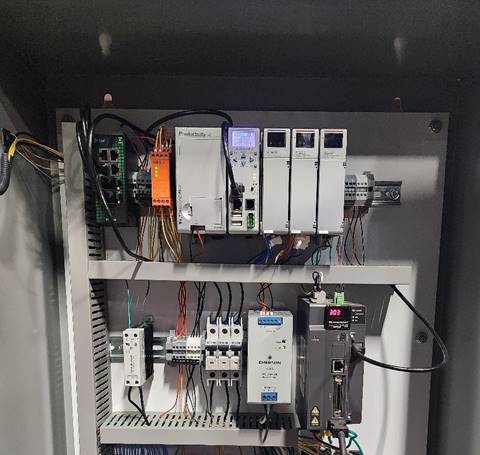
Due to the need for integrating several subsystems, Properly Works selected the AutomationDirect Productivity 3000 PLC for the project because it offers a multitude of features and functionality, combined with large storage capability and numerous communications options. The control architecture relied on hardwired I/O, IO-Link, and also EtherNet/IP and serial communications to exchange data with sensors and intelligent devices, such as the welder.
The PLC coordinates precision movements for the rack-and-pinion workpiece holder over a 9-foot travel axis using an AutomationDirect SureServo2 system. The PLC also manages the robotic arm’s six axes and other automation elements. For example, the PLC initiates the welding nozzle cleaning sequence at the most convenient times during operations to maximize efficiency, reduce weld defects, and conserve consumables.
An AutomationDirect C-more human-machine interface (HMI) provides complete system visualization, with intuitive control and monitoring via graphical weld displays and fault flagging. To handle non-standard segments, the PLC uses recipe-based logic, enabling easy configuration changes. Operators can include/exclude specific welds or posts, streamlining rework and customization.
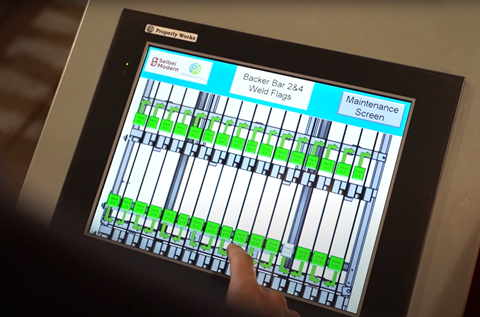
Safety is built into the work cell design using a variety of safety components, including Dold safety relays for monitoring the safety circuit, Datasensing safety light curtains (Category 4 Type 4) to detect intrusion into restricted areas, and both mushroom pushbutton and cable-pull safety switches emergency stop (e-stop) devices.
Measurable Results
Once commissioned, the system lowered production time per fence segment from 12 hours to just 45 minutes while reducing weld rework by 50%. The system’s modularity, flexibility, and ease of use facilitated rapid and reliable adoption by shop floor employees with minimal training.
Based on this project exceeding all goals, the client is now eager to pursue additional automation projects with Properly Works. With the right integration partner and smart technology, even the most daunting manufacturing challenges can be overcome with speed and precision. Due to its success, the automated solution was scaled to three cells, drastically increasing throughput. AutomationDirect’s comprehensive, easily sourced automation components proved integral to the project’s rapid development.